Pipelines are infrastructures subject to different types of threats that affect their integrity and, if not managed properly, can lead to leaks, spills or explosions with negative results.
unwanted. The pipeline integrity assessment makes it possible to identify the deterioration caused by threats, and determine its ability to continue in service, estimate its remaining life, and establish the need for measures such as repair or replacement.
These systems are a key element in many industrial processes and are the most widely used means of transporting hydrocarbons. They are subjected to a large amount of stress, generating failures and damage to the metallic structure, hence the importance of carrying out the tests of mechanical integrity to assess pipeline condition and prevent failure in order to maintain safety, efficiency, and profitability in pipeline systems.
In addition, pipeline integrity tests can provide valuable information about pipeline condition, helping engineers and technicians make informed pipeline maintenance and repair decisions in accordance with industry-accepted standards and practices. Data collected during pipeline integrity tests can be used to schedule preventative maintenance and reduce downtime.
In this article, a brief exposition is made on the importance of pipeline integrity tests; as well as the different types of pipeline integrity tests
Types of pipeline integrity tests
There are several types of pipeline integrity tests, each of which is used to assess different aspects of pipeline condition. Some of the more common types of pipeline integrity tests are described below:
Integrity Assessment
One of the stages to consider in a Piping Systems Integrity Management Program for the transport of dangerous fluids, is the evaluation of the sections that make up a pipeline, in order to identify the deterioration caused, know its status and determine its remaining useful life, to continue in service, and establish the need for measures such as repair or replacement (Figure 1).
It is important to subject the gas pipeline to preventive maintenance that allows avoiding or reducing problems that affect its integrity; One of the ways is using tools for cleaning and internal inspection of the pipeline. The correct selection of these tools allows to obtain an optimal solution to the possible problems that appear in the pipeline; thus achieving that the entire system works optimally and can meet the requirements and objectives set.
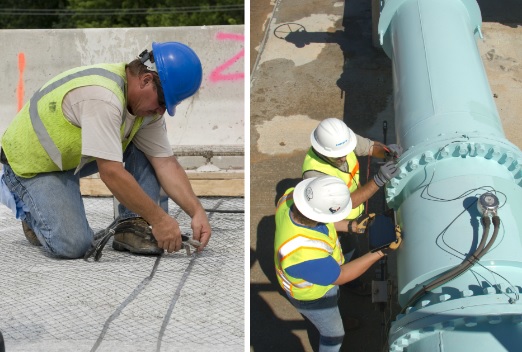
For this integrity evaluation, the Recommended Practice (PR) API 1160 [1] is available, where the techniques to be considered are suggested:
- Hydrostatic test: to carry out this test it is necessary to place the section of pipe to be evaluated out of service, fill it with water or another suitable fluid until reaching a pressure greater than the operating pressure for a certain time. If the section fails because it does not meet the conditions to maintain this pressure, it is necessary to locate, repair the fragment and carry out the test again before putting the pipeline back into operation. These types of tests are widely used when the pipeline cannot be inspected internally.
- Direct evaluation: This type of evaluation integrates specific information on a type of threat (external corrosion, Stress Corrosion Cracking (SCC), for example) to determine segments with a high probability of failure, which will later be directly examined with non-destructive techniques that allow for an estimated diagnosis. the condition of the pipeline. For which, you must have access to the identified sectors; however, on some occasions this entry is not feasible (for example, in jacketed pipes, river or road crossings, or dangerous excavations).
- Online Inspection (ILI): This method, also known as Online or In-Line (Smart Pigging) is one of the most used methodologies in the inspection of the real state of the pipe, it is executed through the use of tools, which are inserted inside the pipe, and they travel with the flow of the product, to carry out specific cleaning or inspection tasks. These are equipped with instruments capable of locating and characterizing anomalies associated with one or more of the identified threats, among which the most commonly used are magnetic flux leakage (MFL), ultrasound (UT), electromagnetic-acoustic transducers ( EMAT) and eddy currents (ET).
Gas pipeline inspection and maintenance tools
Hydrostatic test
Method applied with the purpose of guaranteeing the hermeticity and integrity of gas pipes, and locating possible fault weaknesses.
Hydrostatic testing is a proven method to verify the ability of a natural gas pipeline to operate at a safe level of pressure (known as the maximum allowable operating pressure, or MAOP), in order to ensure the reliability of the installation during its normal operation.
The design codes for equipment and piping systems Integrity according to API 1160 / ASME B31.8, among others, clearly establish the recommended practices on how to perform hydrostatic testing, in order to guarantee the physical integrity of people and equipment . Figure 2 shows the hydrostatic test equipment and the installation of the connections that will be used to raise the pressure.
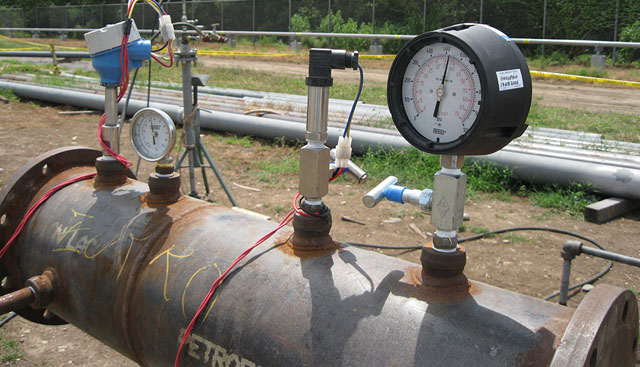
This integrity assessment method may be appropriate for the threats being assessed. The operator must consider the results of the risk assessment and the types of abnormalities expected to determine when to perform inspections using the pressure test.
The pressure test is appropriate when dealing with time-dependent threats. Time-dependent threats are external corrosion, internal corrosion, stress corrosion cracking, and other environmental mechanisms that influence corrosion. Suitable when treating the pipe seam as a manufacturing defect threat.
The pressure test shall meet the requirements of ASME B31.8 . This will define whether air or water is used.
When the Maximum Allowable Operating Pressure or MAOP (Maximum Allowable Operating Pressure) of a steel pipe is increased, or the operating pressure is increased above the historical operating pressure (for example: the highest pressure recorded in the 5 years prior to the effective date of this Standard), pressure testing is performed to address the seam issue.
The pressure test shall comply with ASME B31.8, at least 1.25 times the MAOP. ASME B31.8 defines how to perform piping tests for both post-construction and in-service (23). Pressure testing is typically an inappropriate inspection method to use for all other threats.
Internal inspections of lines or pipes (ILI)
Internal Line Inspection or Inline Inspection (ILI) devices are available, devices called “Smart Pigs” can be equipped with robotic cameras and sensors to check pipe thickness and welds, also detect flaws by corrosion (Figure 3). The main disadvantage of these devices is that the line must be designed to accommodate these devices (i.e. Smart Pig insertion and extraction points, smooth transitions between pipe segments, minimum radius turns, same diameter pipe segments, valves without stopper, etc.). The vast majority of pipelines in gas industries were designed and built before the Smart Pigs technology was developed. These lines would require significant reconstruction to accommodate line inspections.
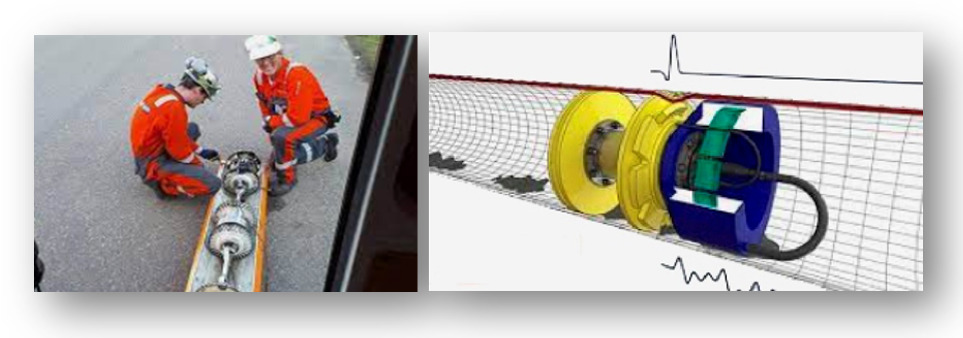
The Smart Pigs can detect blockages, corrosion and other problems inside the pipeline.
In summary, pipeline integrity testing is essential to ensure the safety and efficiency of pipeline systems. The methods used to perform these tests can vary depending on the type of integrity testing being performed, but it is important to have asset integrity experts in place to select the appropriate method and carry out the test safely and accurately.
Importantly, they are not only necessary to comply with regulatory requirements, but also to ensure business continuity and prevent serious incidents. Investment in pipeline integrity testing is essential to ensure the safety and efficiency of the pipeline system and to avoid potential negative consequences for people and the environment.
Corrpro: a company that makes a difference in the sector
Corrpro Companies Inc. is an international provider of technical and engineering services that offers an integrated asset protection and preservation capability, primarily focused on corrosion and cathodic protection processes. It has specialized technical personnel to resolve complex situations that involve the operational and mechanical integrity of assets.
Work with the best and insure your assets.