Table of Contents
The phenomenon of corrosion is one of the main causes of failures in the industrial sector; generating great economic impacts, when performing both preventive and corrective maintenance and sometimes, in a short term, it is necessary to replace materials due to irreparable deterioration, further affecting the economy of the industry. This article presents a summary of the importance of the application of paints on welds (Field Weld), complying with the specifications of the standards, procedures and additionally represents information of interest to professionals and technicians associated with the industry.
There are multiple protection systems that have been developed in order to prevent and control corrosion failures in the industry. Some of the main organizations that are responsible for generating norms and standards are the NACE (National Association of Corrosion Engineers) and the SSPC (Steel Structures Painting Council). which indicate the various procedures, specifications, conditions and acceptance or rejection criteria that must be met when applying any protection system to equipment, pipes and structures, among other assets.
Protection system application procedure.
In the industrial sector, small, medium or large plants are continually being built; which require having all their engineering approved to start the construction phase and subsequent start-up. Regarding the metal-mechanic area, when the manufacturing of equipment and pre-manufacturing of pipes and accessories in general begins, these are made in factories or specialized workshops, in compliance with all the standards and specifications indicated by the design. All these assets go through their different stages of review, control and release, so that they can then be transferred to the site where they will be installed. Emphasis is placed on the subject of welding in the field, of the new plants because it is where a greater quantity of them is generated; but this condition is also continually found in plant maintenance.
In general, the specifications of the coating protection systems indicate that, during the prefabrication of the metallic elements, the sections or ends to be welded in the field (with its acronym in English: Field Weld / FW) should not be painted. An area of 100 millimeters will be left free of paint, which will be measured from the edge to be welded, in order to facilitate and guarantee the welding process in the field; then these areas must be protected with their respective coatings, as indicated by each system or element.
When starting the construction and installation in the field of the different systems or circuits that make up the metalworking area of a plant, continuous welding is carried out in the field; which are distributed throughout the plant. In the event that these welds are not properly cleaned and protected, according to the indications of the standards and design, these points would be exposed to corrosive atmospheres, causing early failures in these areas.
When applying paint protection systems on welds; it is frequent. that these areas are not adequately treated. Usually the guidelines indicated by the quality controls are not followed, the maintainers or executors do not meet the specifications and conditions requested in the procedures and sometimes the lack of time, interest or ignorance of the specification that must be applied in these areas. they also affect the final quality of the works. Additionally, when the treatment of the surface in the FW area begins, it is deficient, the desired anchoring profile is not reached because the cleaning is not effective, not all contaminating agents are removed from the substrate, such as smoke. metal, slag and spatter, which are detrimental and affect the adhesion of the first coating layer to be applied (wetting layer). In the same way, it happens in the phase or process of the application of the coating where certain premises are not met, such as temperature controls (environmental, dew and substrate), the selection of the appropriate paint for each layer, the time intervals of drying between coats and the number of coats of paint needed to achieve the ideal dry film thickness. All these deviations cause these areas to be sensitive and start corrosion in a short time, later showing an accelerated development of said corrosive process, which is detrimental when guaranteeing the mechanical integrity of the plant’s assets.
To control or minimize premature failures due to corrosion in welded joints made in the field (figure 1), it is necessary to emphasize the control, monitoring and compliance with all the guidelines and criteria that indicate the protective paint systems. Careful and effective surface preparation must be carried out before and during the application of the protective system. It is important to treat the surface of the substrate efficiently, leaving it in optimal conditions, free of any impurity that may affect the adhesion and subsequent performance of the coating; Regarding the process for the application of the paint coating, it must comply step by step and the specifications indicated in the procedures, all layers of paint must be applied, respecting the temperature ranges, the drying times between layers and achieving the adequate dry film thickness, so that each area of FW is released under the design specifications, and with this guarantee the extension of the useful life of the element.
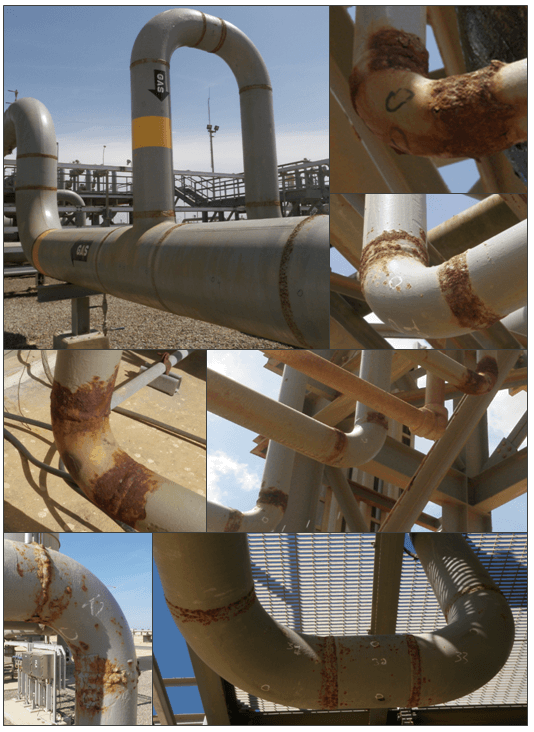
Conclution
Adequate compliance with the rules and procedures that govern the application of paint protection systems will allow the metal surfaces to be kept in optimal conditions, extending the useful life of the assets and their reliability; which will translate into operational security and significant economic benefits for the company.
References
Own source
For more articles visit https://inspenet.com/en/articles/