Table of Contents
- Purpose of explosion welding
- How explosion welding works
- How explosive energy is applied in explosion welding
- Common explosives used in explosion welding
- Properties of metal cladding by explosive welding
- Common dissimilar metal combinations in explosion welding
- Industrial applications of explosion welded cladding
- Design considerations in explosion welding
- Quality control in explosion welding
- Conclusions
- References
In industries facing aggressive environments, high pressures and elevated temperatures, protecting structural materials from corrosion and erosion is a priority challenge. One of the most effective and reliable solutions is explosion welding, a solid-state joining technique widely used in cladding processes. This method combines dissimilar metals while maintaining the structural integrity and original thermal properties of the materials involved.
Purpose of explosion welding
The primary goal is to create a strong metallurgical bond between different metals using controlled explosive energy. This technique applies a corrosion- and erosion-resistant metal cladding layer without melting the materials. It minimizes thermal defects, retains the original properties of the metals, and offers an economical solution by applying only a thin noble metal layer over a cheaper structural base.
How explosion welding works
Explosion welding is a solid-state joining process that uses the energy from a controlled explosive charge to force two different metals into high-speed collision. Unlike fusion welding, this method does not melt the materials, thereby eliminating heat-affected zones (HAZ) and significantly reducing thermal defects.
The process involves placing two metal plates, one thicker and lower-cost base plate (e.g., carbon steel) and one thinner cladding plate made of corrosion-resistant material (e.g., stainless steel, titanium, copper, or nickel alloy).
An explosive charge is carefully distributed on top of the cladding plate. Upon detonation, a shock wave drives the cladding plate toward the base plate at a precise angular velocity, producing a firm metallurgical bond without melting. The result is a characteristic wavy interface, which confirms the solid-state nature of the bond and enhances mechanical anchoring between both materials.
For more information on the subject, I invite you to watch the following video. Source: ReP Facts Operational Facts.
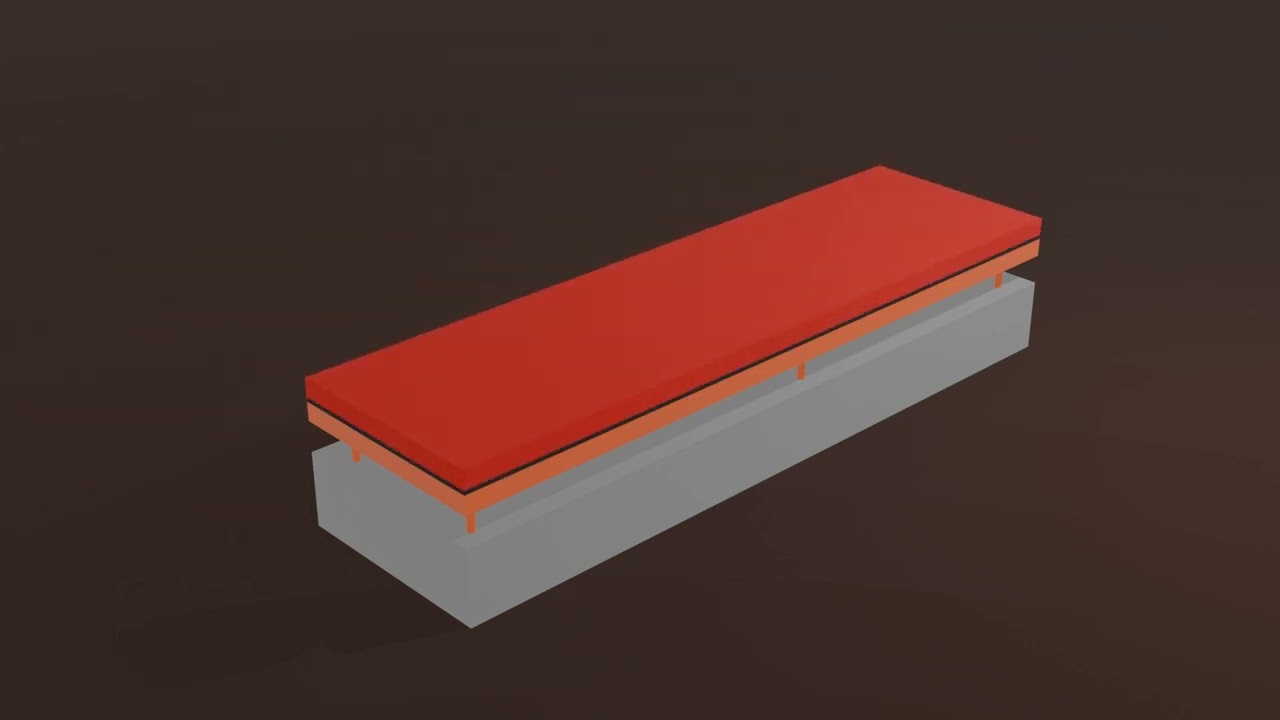
Explosive welding.
Importance of the wavy interface
The undulated interface formed during explosion welding acts as a mechanical buffer:
- It improves stress distribution caused by differences in thermal expansion.
- It increases the contact surface area, improving adhesion.
- It absorbs differential movement, delaying delamination or separation failure.
How explosive energy is applied in explosion welding
Applying explosive energy is a critical stage. It’s not a simple detonation, but a precisely engineered event designed to achieve a clean bond without damaging the metals.
Key design considerations include:
- Type and thickness of metals: These determine the energy required to induce proper deformation and bonding.
- Explosive type and detonation velocity: These affect collision speed and pressure; must be tuned to the specific metal pair.
- Impact angle: Influences the formation of the wavy interface and bonding quality.
- Standoff distance: Controls the cladding plate’s acceleration before impact to ensure a clean, uniform bond.
A detonator initiates a controlled reaction that generates transient pressures of several gigapascals for a few microseconds. This drives the cladding plate into angular collision with the base metal, stripping surface impurities and creating a solid metallurgical bond without altering the materials’ microstructure. The outcome is a high-quality industrial metal cladding with no melted zones or thermal degradation.
Common explosives used in explosion welding
Explosives are selected based on their power, safety, and compatibility with the metals being bonded:
- RDX (Cyclotrimethylenetrinitramine): High detonation velocity (~8,750 m/s); ideal for producing clean joints with defined wavy interfaces. Common in high-quality bimetallic plates.
- ANFO (Ammonium Nitrate-Fuel Oil): Cost-effective and easy to handle, with a moderate detonation velocity (~3,200–4,500 m/s). Used in large-scale applications where extreme explosive force isn’t necessary.
- PETN (Pentaerythritol Tetranitrate): Highly energetic and sensitive. Detonation velocity ~8,400 m/s. Suitable for bonding thin cladding layers.
- C4 (RDX-based with plasticizers): Moldable, water-resistant, and stable. Detonation velocity ~8,040 m/s. Useful for irregular geometries.
Properties of metal cladding by explosive welding
Explosion welding produces unique, high-performance joints with advantages such as:
- High bond strength: Far exceeds conventional welding.
- No fusion zone: Prevents solidification cracking and preserves original grain structure.
- Wavy metallurgical interface: Enhances mechanical interlocking, reducing delamination risk.
- Material compatibility: Enables bonding of challenging combinations like titanium-to-steel, copper-to-steel, and stainless-to-aluminum.
These properties make explosion-welded cladding suitable for demanding industrial environments.
Common dissimilar metal combinations in explosion welding
Base metal | Cladding metal |
Carbon Steel | Stainless Steel |
Carbon Steel | Titanium |
Carbon Steel | Copper or Brass |
Carbon Steel | Nickel or Nickel Alloys |
Stainless Steel | Aluminum |
Industrial applications of explosion welded cladding
Explosion welding is a strategic technology for industries requiring robust bonds between dissimilar metals. Common applications include:
- Pressure vessels: As per ASME VIII Div 1, explosion-welded bimetallic plates provide corrosion-resistant liners with a strong structural base.
- Heat exchangers: Require high thermal conductivity and resistance to aggressive fluids.
- Bimetallic plates: Used in distillation columns, reactors, and processing equipment.
- Naval and aerospace components: Where weight reduction and corrosion resistance are critical.
Design considerations in explosion welding
Proper design demands careful assessment of multiple variables:
- Metallurgical compatibility: Avoid combinations that form brittle or reactive phases. Keep thermal expansion mismatch ideally below 5–7 x 10⁻⁶ K⁻¹. Intermediate layers (e.g., nickel) may be used between incompatible metals like steel and copper.
- Explosive energy: The charge and detonation velocity must be adjusted to avoid damaging the plates.
- Joint geometry: Initial plate spacing, collision angle, and thickness influence interface quality.
- Surface preparation: Clean, flat surfaces are essential for optimal bonding.
- FEM simulation (Finite Element Method): Predicts thermal stresses, deformations, and validates parameters pre-detonation.
- Standards: Must comply with specifications like ASTM B898 and ASME VIII.
Quality control in explosion welding
Ensuring a reliable explosion-welded joint requires rigorous controls across three stages:
Before the process:
- Material verification: Confirm specs, certificates, and compatibility.
- Surface preparation: Visual inspection and mechanical/chemical cleaning.
- Geometry configuration: Measure spacing, alignment, and impact angle.
During the process:
- Environmental monitoring: Weather, safety perimeter, and explosive containment.
- Explosive control: Type, mass, detonation speed, and distribution.
- Detonation log: Chronology, pressure generated, and material response.
After the process:
- Visual and dimensional inspection: Check bond continuity and flatness.
- Non-destructive testing (NDT): Phased Array Ultrasonic Testing (PAUT) to verify adhesion and absence of defects.
- Mechanical testing: Shear, tensile, and hardness testing to validate bond strength.
- Hot shear tests: Evaluate high-temperature adhesion performance.
Conclusions
Explosion welding for metal cladding of dissimilar metals is an advanced technique that produces durable, high-performance joints. It preserves thermal conductivity, avoids heat-affected zones, and withstands extreme conditions—making it ideal for the fabrication of industrial cladding systems.
From bimetallic plates to ASME VIII-regulated equipment, this technology is expanding its reach, supported by FEM simulation and standards such as ASTM B898. Modern engineering continues to balance performance, durability, and cost-effectiveness in designing critical components.
References
- Zhou, Q., Lu, H., Lan, X., Guo, Y., Liu, K., Huang, G., Jia, B., & Chen, P. (2023). Anisotropy in microstructure and shear properties of TA2/Q235 explosive welding interfaces. Journal of Materials Research and Technology, 25, 6472–6491. https://doi.org/10.1016/j.jmrt.2023.06.129
- https://thetech.com.vn/en/what-is-explosion-welding-advantages-disadvantages-and-applications/
- Inspenet. (2025). Detaclad: Soldadura por explosión – AMPP 2025 [Video]. Inspenet. https://inspenet.com/video-tv/detaclad-soldadura-por-explosion-ampp-2025/
- Inspenet. (n.d.). Finite element analysis applications. Inspenet. https://inspenet.com/en/articulo/finite-element-analysis-applications/