Tailor-made NDT calibration for industry: the ECUTEC approach
As part of the PANNDT trade show, the Inspenet team met with Todd Lorich, senior engineer at ECUTEC, to learn more about the company's approach to NDT calibration solutions. Based in the United States and with a strong Pan-American presence, ECUTEC specializes in the manufacture of calibrated blocks, tubes and parts, developed to each customer's unique specifications.
A tailor-made solution at the heart of NDT
Unlike many suppliers in the industry, ECUTEC does not base its model on standardized catalogs, but rather each request is manufactured from scratch, meeting the specific requirements of depth, location and type of defect that the customer needs to simulate.
This flexibility enables companies in different industries to have NDT calibration tools that more closely reflect the actual service conditions of their assets. In addition, turnaround time is fast, thanks to an in-house design and manufacturing system that allows for quick modification or generation of customized drawings.
Continental presence and strategic links
Although ECUTEC is headquartered in South Carolina, the company has strong ties to Canada, the country where its founder was born and raised, which has generated a relationship of trust with Canadian clients over the years. In addition, the owner's trajectory includes 15 years of residence and work in Brazil, consolidating ECUTEC's presence throughout the Americas.
This geographic reach has allowed it to adapt to the regulatory and operational requirements of different markets, making it a reliable option for inspection, manufacturing, maintenance and quality assurance companies throughout the region.
Industrial sectors that depend on ECUTEC
Although its offer can be adapted to any field where non-destructive testing is applied, ECUTEC has a particularly strong presence in the heat exchangers industry. Most of the parts produced are intended for this application, where accuracy in the simulation of defects is crucial to avoid failures during service.
Other sectors using its solutions include the aerospace industry, structural component manufacturers, energy companies and even amusement parks, with the manufacture of parts for inspection of roller coaster parts. This variety of customers is evidence of the versatility and confidence that ECUTEC has achieved in the field of NDT calibration.
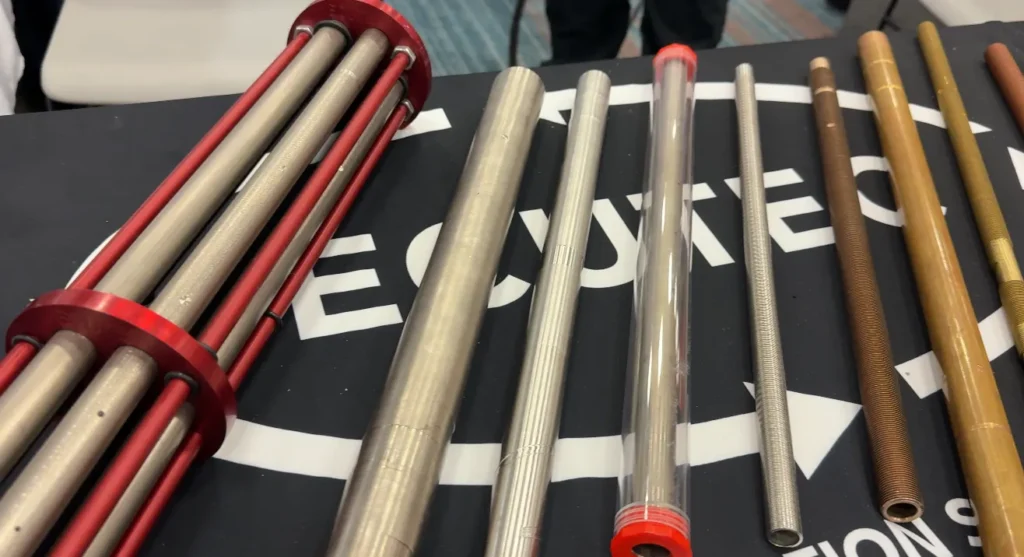
Accuracy, traceability and reliability
Each part manufactured by the company undergoes an inspection process after machining, in order to ensure that the defects introduced comply with the requested parameters, such as depth, position and shape. All this information is documented in a traceability system that includes serial number assignment, allowing any standard to be traced even years after delivery.
This commitment to traceability is key in industrial environments where audit and reliability of the inspection process are critical. In addition, the use of NIST (National Institute of Standards and Technology) certified tools guarantees the metrological quality of the components.
Constant innovation and rapid response
Far from remaining in a comfort zone, the company's team is constantly in contact with its customers to explore new manufacturing possibilities.
We have manufactured grooves up to 2000 and 3000 microns wide, and we are always looking to push the limits on new machining ideas, depending on the customer's needs.
Todd Lorich.
With more than three decades of experience, ECUTEC has built a reputation based on customization, traceability and closeness to its customers. The interview with Todd Lorich confirms that the company combines technical excellence with a philosophy of agile service focused on the real value the customer needs. In an industry where accuracy and reliability are imperative, its NDT calibration approach makes a tangible difference in the industry.
For more content on PANNDT 2025, visit our YouTube channel and our LinkedIn profile.
Source: Inspenet.