Table of Contents
- Introduction
- What is PMI?
- PMI's importance in the reception of components and raw materials
- Common portable technologies used for PMI
- Emerging technologies and alternatives for PMI
- PMI assisted by artificial intelligence (AI)
- PMI Procedure: Step-by-Step Guide
- PMI test acceptance criteria
- Acceptance requirements
- Off-specification material disposition
- Applicable references
- Conclusions
- References
Introduction
Accurately verifying the chemical composition of materials is a critical aspect of industrial processes, particularly in sectors such as energy, petrochemicals, aerospace and construction, where material quality and compliance directly impact safety, operational performance and asset life.
Positive material identification (PMI) ensures that the components used meet the design requirements and engineering specifications necessary to preserve structural integrity and in-service performance. Given the need to perform efficient inspections without compromising quality, portable elemental analysis methods are presented as a strategic solution, allowing immediate material validation in the field, optimizing batch traceability and significantly reducing the risk associated with the use of non-conforming materials.
What is PMI?
Positive Material Identification (PMI) is a non-destructive inspection technique that allows highly accurate verification of the chemical composition of materials, ensuring their compliance with technical and regulatory specifications. Its application is essential in industries such as energy, petrochemical, construction and aerospace, among others, where an error in the selection of materials can cause structural failures, safety risks and high operating costs.
During the receipt of components and raw materials, PMI prevents the use of incorrect materials and helps avoid failures, costly repairs or unplanned downtime. Today, portable PMI technologies enable fast and reliable identifications directly at the job site.
To complement the information, the following video provides an explanation of this analytical technique that has been used for many years to determine the elemental composition of a wide variety of materials. Source: Hitachi High-Tech Corporation official YouTube site.

What is XRF? -X-ray fluorescence explained
PMI’s importance in the reception of components and raw materials
The implementation of Positive Material Identification (PMI) in the reception of components and raw materials is a decisive process to ensure integrity, quality and safety in industrial operations. Its correct application allows:
- Avoid the use of incorrect alloy materials or components, which may compromise the performance and safety of the systems.
- Prevent accidents resulting from material failures, such as fractures, leaks or failures in operation.
- Reduce costs associated with rework, unplanned repairs and production losses due to out-of-specification materials.
- Verify that materials comply with technical and contractual regulations, avoiding legal penalties and reputational damage.
- Ensure that welds comply with correct filler material.
Through a rigorous control with PMI, the compliance of materials and components with design requirements is verified, which helps to prevent structural or functional failures, reduce operating costs and mitigate legal risks. In addition, it contributes to maintaining and strengthening the organization’s reputation for quality with its customers and regulators.
For example, in the energy industry, the use of an incorrect alloy in a high-pressure pipeline could lead to catastrophic failures during operation, with serious consequences for the safety of personnel and the environment. Source: Fuente: Mister MHW.
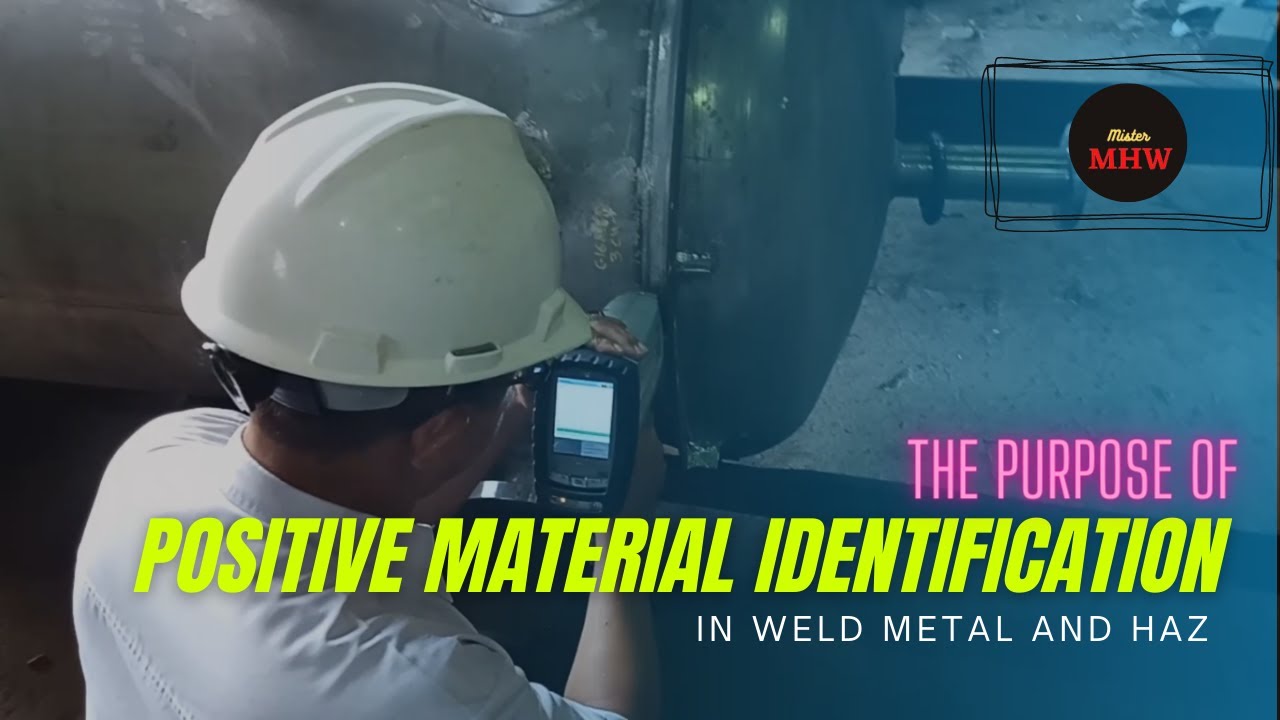
The purpose of Positive Material Identification in weld areas.
Common portable technologies used for PMI
Currently, the two most common portable PMI technologies are:
- X-ray fluorescence (portable XRF): Uses X-rays to excite the atoms of the material, causing the emission of characteristic secondary radiation. X-ray fluorescence makes it possible to determine the elements present quickly and non-destructively.
- Optical emission spectroscopy (portable OES): By means of a spark or electric discharge, the sample is ionized, causing the emission of light. This light is analyzed to identify the composition of the material.
XRF is ideal for rapid chemical analysis of metals and alloys, while OES is best used to measure light elements such as carbon, crucial in steels. The following image shows some portable devices with both technologies:
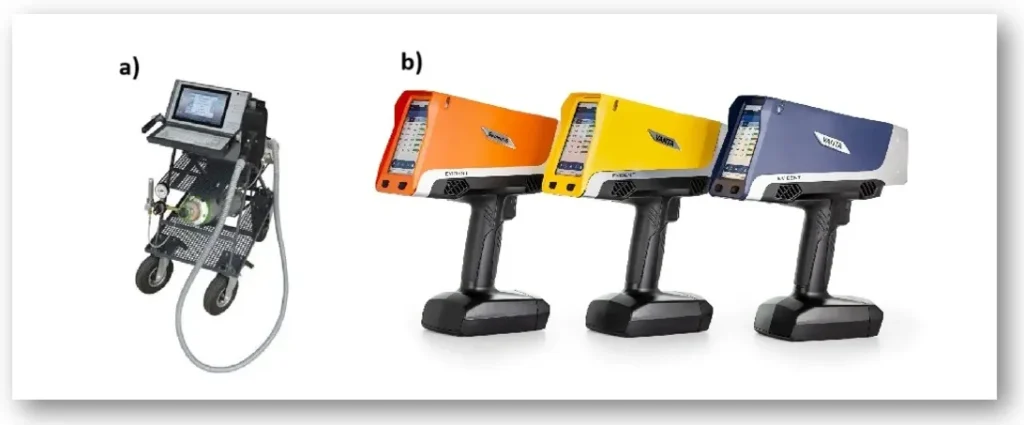
Emerging technologies and alternatives for PMI
In addition to XRF and OES, there are other emerging technologies for the positive identification of materials:
- Raman spectroscopy: Uses a low intensity laser to cause a Raman effect, where the light changes energy according to specific molecular vibrations. This spectrum allows precise identification of organic materials, polymers and contaminants, without contact or special preparation. It is ideal in sectors such as pharmaceuticals, petrochemicals and polymers, where fast, non-destructive and reliable identification is required.
- FTIR (Fourier-Transform Infrared Spectroscopy): Analyzes how chemical bonds absorb infrared light at different wavelengths. Each compound has a unique absorption pattern, which facilitates accurate molecular identification. FTIR is key in the analysis of chemical compounds, plastics, polymers, resins and adhesives, especially in quality control and characterization of organic materials in industry.
- Portable LIBS (Laser-Induced Breakdown Spectroscopy): Applies a high-energy laser pulse to create a microplasma that emits light representative of the elements present. LIBS offers fast and accurate identification of light and heavy elements in seconds, making it ideal for mining, metallurgy, archaeology and industrial field inspections.
- Hybrid LIBS + Raman / LIBS + OES technologies: Combine two techniques in a single instrument, extending the range of analysis and improving accuracy. LIBS + Raman allows to know the elemental and molecular composition simultaneously, ideal for materials research and pharmacology. LIBS + OES combines the speed of LIBS with the sensitivity of OES, detecting critical light elements such as carbon, phosphorus and sulfur in steels and alloys. These solutions optimize inspection times and reduce the need for multiple equipment in complex industrial applications.
Comparative table of portable technologies for PMI
Technology | Advantages | Limitations |
Portable XRF | Fast, non-destructive, accurate for heavy metals. | Lower precision in light elements. |
Portable OES | High precision, detects carbon. | Requires prepared surface. |
Portable LIBS | Ultra-fast analysis, detects light elements. | May slightly damage the surface. |
Portable FTIR | Ideal for plastics and organic compounds. | Not suitable for metals. |
Portable Raman | Useful in plastics, contaminants and liquids. | Sensitive to fluorescence in certain samples. |
The choice depends on the type of material, the required portability and the expected sensitivity.
PMI assisted by artificial intelligence (AI)
The future of positive material identification is transformed by the assistance of artificial intelligence. Through the use of this technique, AI-enabled systems are able to analyze multiple spectra simultaneously, automatically optimize measurement parameters, detect error patterns, prevent misidentifications and accelerate response times with greater accuracy.
The combination of artificial intelligence with technologies such as X-ray fluorescence, FTIR and Raman spectroscopy greatly improves the reliability of rapid material identification.
PMI Procedure: Step-by-Step Guide
A typical positive material identification process includes:
- Selection of the appropriate technology (XRF, OES, Raman, FTIR, LIBS): According to the type of material and critical elements.
- Equipment configuration and calibration: Adjust parameters for the specific material.
- Surface preparation: Clean the area to be analyzed to avoid contamination.
- Measurement: Apply the selected technique on the sample.
- Result interpretation: Compare the data obtained with the required specifications.
- Documentation and certification: Record results for traceability and compliance.
PMI test acceptance criteria
Acceptance of Positive Material Identification (PMI) testing is based on verification that the chemical composition measured on the material is within the limits established in standards such as ASTM, ASME or purchasing specifications. According to API Recommended Practice 578, PMI results must match the material specification, allowing a typical tolerance of ±10% for major alloying elements, unless customer or critical service requirements demand tighter limits (±5%).
For critical materials (e.g. high pressure or severe corrosion applications), the measured values must strictly conform to nominal chemical tolerances. Out-of-specification results require corrective actions such as segregation, re-inspection or rejection of the component.
Acceptance requirements
- The chemical composition determined must match the reference material specification (ASTM, ASME standards or internal project specifications).
- A variation of up to ±10% with respect to the nominal value of the main alloying elements is allowed, unless a more restrictive provision is established by the customer or applicable standards.
- In materials critical for structural integrity, corrosive service or high temperature, the accepted tolerance is reduced to ±5%.
- The presence of prohibited elements (e.g. lead in stainless steels) implies immediate rejection.
Off-specification material disposition
- Immediate segregation of the affected lot or component.
- Confirmation by laboratory analysis if applicable.
- Rejection or rework according to the severity of the deviation and customer’s instructions.
Applicable references
- API Recommended Practice 578 – Material Verification Program for New and Existing Alloy Piping Systems.
- ASME B31.3 – Process Piping.
- ASTM Metallic Material Specification Standards.
Conclusions
Positive material identification is essential to ensure safety, quality and compliance in any modern industry. Thanks to portable technologies and advances in artificial intelligence, fast, accurate and reliable inspections are now possible in any work environment. The right choice of PMI technology not only improves operational efficiency, but also protects assets, people and the environment.
Mastering the step-by-step of positive material identification, properly selecting rapid material identification technology and understanding the chemical analysis involved is essential to maximize the benefits of these advances and ensure operational excellence in any industry sector.
References
- API Recommended Practice 578 (3rd Edition), 2018. “Material Verification Program for New and Existing Alloy Piping Systems”; Editorial: American Petroleum Institute (API).
- ASTM E1476-01(2014); “Standard Guide for Metals Identification, Grade Verification, and Sorting” ; ASTM Guide for Metals Identification, Grade Verification, and Sorting, including methods such as PMI and interpretation criteria; Publisher: ASTM International.
- Kaiser, J. (2012); “Principles and Applications of X-Ray Fluorescence (XRF) in Materials Analysis”; In Encyclopedia of Analytical Chemistry.