In the field of materials engineering and structural integrity, the topic of corrosion vs. rust is important in distinguishing the two mechanisms. Generally, these concepts are often used interchangeably, both in technical and common parlance. However, from a rigorous electrochemical perspective, they represent distinct, yet closely related phenomena with specific implications on the durability, strength and functional performance of metallic materials.
This distinction is especially relevant in critical sectors such as the petrochemical industry, maritime infrastructure, energy, and civil construction, where premature deterioration of materials can have catastrophic consequences in terms of safety, operability, and maintenance costs.
Oxidation is, in general terms, a surface chemical reaction in which a metal loses electrons, usually by reacting with oxygen in the presence or absence of moisture. Although it does not always compromise the structure of the material, it can form passivating layers or, on the contrary, initiate more complex deterioration mechanisms. Corrosion is defined as a destructive electrochemical process involving the interaction between the metal, an electrolyte, and an oxidizing agent, resulting in the transformation of the metal into its most thermodynamically stable form. That is, its corresponding oxide, hydroxide, or salt.
The purpose of this article is to discuss corrosion vs. rust, addressing its underlying mechanisms, conditions of occurrence, typical manifestations and structural consequences on metallic materials. In addition, the importance of its correct identification for the application of effective preventive techniques, the selection of suitable materials and the design of predictive maintenance strategies will be highlighted.
Oxidation vs. Corrosion
In the field of materials engineering, and particularly in corrosion engineering, it is essential to distinguish precisely between the concepts of oxidation and corrosion, since their technical implications, physicochemical mechanisms and structural consequences are substantially different.
Oxidation: Surface reaction
Oxidation is a surface chemical reaction where a metal, in contact with oxygen, forms oxides. This phenomenon, although visible (Fe₂O₂O₃, reddish layer), does not severely compromise the structural integrity of the metal substrate if controlled. For example, this process involves electronic transfer, but does not necessarily involve an electrolytic medium1.
This reaction typically occurs on the surface of the metal when it comes into contact with an oxidizing agent, such as atmospheric oxygen. Under dry ambient conditions, the oxidation of iron, for example, results in the formation of ferric oxide (Fe₂O₃), a brown or reddish surface layer. This phenomenon occurs without the need for an electrolyte and, in many metals, can form a passivating patina that slows down subsequent deterioration processes (as shown in the following image). However, in other materials such as iron, this layer is porous and non-protective, allowing progressive exposure of the underlying metal.
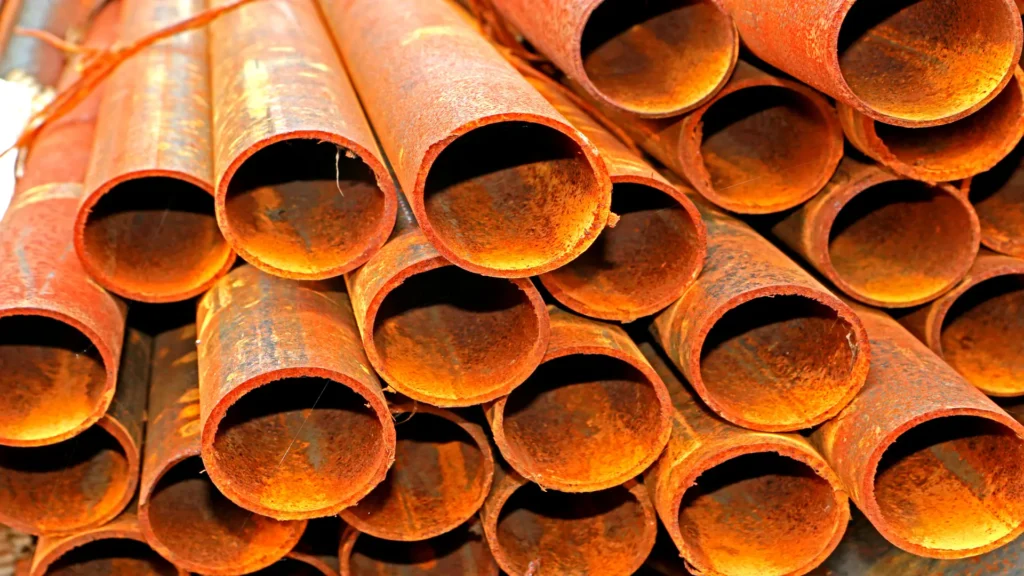
From a thermodynamic point of view, oxidation simply involves the loss of electrons by the metal, which may or may not be associated with structural deterioration. In industrial practice, this type of surface oxidation can be easily reversed by mechanical processes such as sandblasting, shot blasting or sanding, and rarely significantly affects the mechanical strength of the substrate if detected and treated in time.
Corrosion: Electrochemical degradation
Unlike oxidation, corrosion is not merely superficial. It manifests itself with different modes of attack (uniform, localized, intergranular, pitting, crevice, stress corrosion, etc.), depending on the type of alloy, media conditions and structural design. Moreover, its cumulative effect is often invisible until the integrity of the component is compromised, as is often the case in submerged structures, storage tanks, buried pipelines or equipment subjected to thermal cycling and aggressive environments.
Corrosion represents a more complex and irreversible electrochemical process, in which the metal acts as an anode in a spontaneous galvanic cell, losing electrons to a cathode through a closed circuit in the presence of an electrolyte, generally water with dissolved salts. This leads to the progressive dissolution of the base metal, causing loss of mass, reduction of useful area, and, in advanced stages, formation of cracks, pitting, or structural collapse, as shown in the following picture.
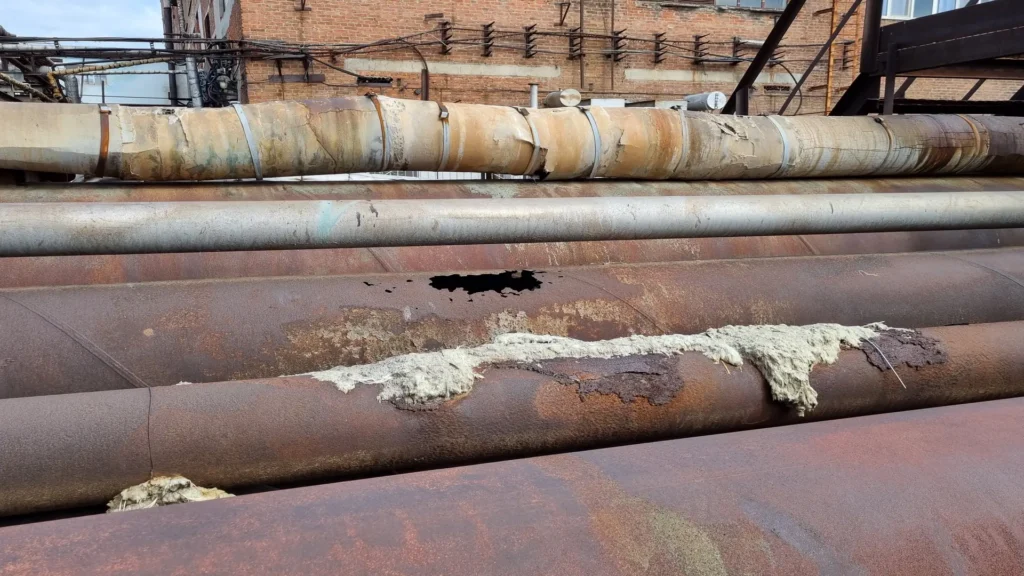
In this mechanism, the metal acts as an anode and undergoes dissolution: Fe → Fe²⁺ + 2e- (anodic reaction), accompanied by a cathodic reaction, such as oxygen reduction: O₂ + 4H⁺ + 4e- → 2H₂O.
This distributed galvanic cell system generates progressive mass loss, cracking or perforation2.
Therefore, although both processes involve the interaction of metals with the environment, oxidation can be considered an initial and superficial chemical phenomenon, while corrosion involves a complete electrochemical cell that functionally and irreversibly deteriorates the material.
The following table shows a summary of the most important differences between the concepts of oxidation and corrosion.
Comparison between oxidation and corrosion
Characteristic | Oxidation | Corrosion |
---|---|---|
Nature of the process | Surface chemical reaction | Electrochemical process |
Agents involved | Oxygen | Oxygen, moisture, electrolytes |
Damage depth | Superficial | Penetrative and structural |
Reversibility | Reversible through mechanical cleaning | Irreversible; requires repair or replacement |
Effect on mechanical properties | Minimal | Significant; may lead to structural failures |
Watch the following video, a very interesting way to explain this topic. Source: Youtube.

Rust and corrosion.
Causes and critical environments
The oxidation of metals is a process that intensifies mainly in humid environments with the presence of atmospheric oxygen. This reaction, fundamentally chemical in nature, does not require a liquid electrolyte to develop, as it can occur even under conditions of exposure to air.
A classic example is the formation of ferric oxide (Fe₂O₃) on iron or steel surfaces exposed to air and moderate levels of ambient humidity. Although oxidation is usually limited to a surface layer, this oxide film can act as a protective barrier or, conversely, as a precursor to more aggressive mechanisms, if localized microenvironments develop beneath the film.
In contrast to the above, corrosion is a process with a more complex mechanism that requires an electrochemically active medium, where the metal acts as an anode and oxidizes, releasing electrons that will be consumed by a cathodic reduction reaction. Both cathodic and anodic reactions must occur at the same time. This process requires the presence of a conductive electrolyte, such as water with dissolved salts, to produce the ionic flow that completes the corrosion cell.
Critical environments for corrosion include:
- Marine or coastal environments, rich in chlorides, which accelerate the formation of galvanic cells and pitting.
- Humid soils with high electrical conductivity, especially those containing sulfates, chlorides or degradable organic compounds, which favor both uniform and microbiologically influenced corrosion (MIC).
- Industrial environments with acid or base vapors, where aggressive condensations are generated that attack the metal directly.
- Interfacial areas or under deposits, such as welded joints or flanged connections, where localized corrosion is favored.
Additionally, in heterogeneous metallic systems or where there are electrochemical potential imbalances, galvanic couples are generated between materials with different nobilities, intensifying the corrosion of the less noble component. These conditions require specific protective measures, such as the use of coatings, cathodic protection or corrosion inhibitors, depending on the operating context.
Consequences of oxidation and corrosion
It is important to clearly distinguish the differences and mechanisms between oxidation and corrosion, since this differentiation not only has conceptual value, but also profound implications in the design, operation, and maintenance of industrial equipment. Generating technical, economic, safety and environmental consequences.
Technical consequences: Oxidation usually manifests itself as a surface film of oxides (such as Fe₂O₃) which, although it may alter the appearance of the material, does not affect the mechanical properties of the component. Corrosion seriously compromises the structural integrity of the material. Loss of thickness, localized pitting, internal lamination pitting and induced stress cracking are typical consequences of corrosive action. This degradation can jeopardize operational safety, especially in pressurized systems, support structures, process lines or storage tanks.
Economic and productive: Corrosion represents one of the most costly challenges for industry. Losses associated with corrosion can range from 3% to 5% of Gross Domestic Product (GDP) in developed countries3. This figure includes equipment replacement, unexpected failures, corrective maintenance costs, unplanned shutdowns and loss of production efficiency. It also raises the costs associated with industrial insurance, litigation for regulatory non-compliance and environmental mitigation expenses.
In terms of safety: Corrosion has been the root cause of numerous industrial accidents, from hazardous substance spills to fatal structural collapses. Deterioration hidden under coatings or in hard-to-reach areas is a latent risk if proper monitoring and protection techniques are not applied.
Environmental impact: Leaks of hydrocarbons, chemical contaminants or industrial effluents released from corroded line failures can result in severe environmental damage, regulatory sanctions and loss of operating license.
Importance of prevention and control
It is important to clearly distinguish the differences and mechanisms between oxidation and corrosion to understand why their control is not an option, but a fundamental necessity in any industrial context. Both processes, although different in nature, converge in a common consequence: the progressive loss of functionality and reliability of metals exposed to aggressive environments.
Properly controlling them implies safeguarding not only the structural integrity of metal assets, but also the safety of people, the sustainability of processes and the economic viability of operations.
Every metal system exposed to an environmental setting is engaged, to a greater or lesser extent, in a constant battle against thermodynamics: metals tend to return to their most stable state, i.e. their oxidized forms. Not intervening in this process by means of control strategies means accepting progressive degradation as an inevitable consequence, but modern engineering is based on anticipation and action. That is why corrosion control represents an extension of the principle of operational responsibility.
Economic analyses in industrialized nations have shown that the damage caused represents a major capital drain. This impact is not limited to the replacement of rusted or corroded components; it also includes losses due to process interruptions, emergency repairs, penalties for environmental incidents and, in the most serious cases, accidents with irreparable human and ecological consequences.
Controlling rust and corrosion is, in short, an act of foresight. It is investing today in stability, safety, and efficiency for tomorrow. It is to protect technical, human and environmental capital against a silent but constant threat. And it is also to assume, from the engineering point of view, the ethical responsibility of designing more durable, safe and sustainable systems.
Conclusions
Economic analyses of industrialized nations have shown that the damage caused represents a major capital drain. This impact is not limited to the replacement of rusted or corroded components; it also includes losses due to process interruptions, emergency repairs, penalties for environmental incidents and, in the most serious cases, accidents with irreparable human and ecological consequences.
Controlling rust and corrosion is ultimately an act of foresight. It is investing today in stability, safety and efficiency for tomorrow. It is to protect technical, human and environmental capital against a silent but constant threat. And it is also to assume, from the engineering point of view, the ethical responsibility of designing more durable, safer and sustainable systems.
The distinction between both phenomena allows the application of the most appropriate control method such as coatings, cathodic protection or selection of resistant materials and the establishment of effective predictive maintenance programs. Correctly managing the risks associated with corrosion and oxidation is fundamental to extend the useful life of equipment, ensure operational continuity and comply with sustainability and industrial integrity standards.
References
- Bockris, J.O’M., Reddy, A.K.N. (1998). Modern Electrochemistry. Springer.
- Uhlig, H.H. (1985). Corrosion and Corrosion Control. Wiley.
- Fontana, M.G. (1987). Corrosion Engineering. McGraw-Hill.