Table of Contents
- Introduction
- Stone: The origins of monumental sculpture
- Iron: Forging new possibilities
- Marble: The quest for classical perfection
- Bronze: The metal of gods and heroes
- Stainless steel: The modernist revolution
- Modern coatings: A revolution in preservation
- Ethical and technical challenges in modern conservation
- Conclusions
- References
Introduction
The historical evolution of materials used in artistic sculpture and how modern coating technologies have preserved the artistic legacy of different eras, allows us to analyze the development of sculptural materials from primitive stone to contemporary metals, as well as to study how advances in protective coatings have revolutionized the conservation of cultural heritage against the destructive effects of time and the environment.
Likewise, investment in the heritage care of towns may be irrelevant to some, however, as part of a productive process in the smokeless industry such as tourism, works of art end up being an emblematic and representative symbol of a country, for example, like the Eiffel Tower or the Statue of Liberty.
Throughout history, artists have used a variety of materials to express their creativity, communicate ideas and leave a cultural legacy. From the first sculptures carved in stone to modern installations in stainless steel, the evolution of artistic materials reflects the technological development of each era and also the aesthetic and conceptual aspirations of different societies (Winckelmann, 1764/2006). However, the passage of time, exposure to natural atmospheric elements and environmental pollution represent constant threats to the integrity and preservation of these heritage works.
The conservation of artistic heritage is a fundamental challenge for our society, as these works not only have an aesthetic value, but also represent the cultural identity of past and present civilizations. As Appelbaum (2007) points out, “the preservation of cultural objects is not simply a technical issue, but a commitment to safeguarding our collective memory materialized in the form of art” (p. 3). In this context, the development of modern coatings has emerged as a promising solution to protect the artistic legacy without compromising its authenticity and historical value.
If we analyze the historical trajectory of sculptural materials, the characteristics and limitations of each one, and delve into how contemporary coating technologies are transforming the paradigms of artistic conservation, we will understand why there is a special focus on emblematic cases such as, for example, the restoration of historic monuments in New York and current strategies to protect bronze sculptures and other materials that are exposed to the elements in different cities around the world.
Stone: The origins of monumental sculpture
The first sculptural manifestations of humanity were created in stone, a material that has defined numerous artistic epochs from the Paleolithic to the present day. Let’s take a look at The Venus de Milo, which, although not a work for the ornamentation of a city, is the representation of a moment of inspiration to testify to the ingenuity and talent of an era. The choice of stone as a primary material responded to its abundance in nature, its relative ease to be worked with simple tools and, mainly, its durability (Schädler-Saub & Weyer, 2010). Mesopotamian, Egyptian, Greek and Roman cultures developed sophisticated techniques for carving stones such as granite, limestone and marble, creating monumental works destined to last.
Stone offered a promise of eternity that was attractive to civilizations concerned with transcendence. As Wittkower (1977) explains in his analysis of sculpture: “Stone was chosen for its physical qualities, and for its symbolism of permanence and ability to convey messages through time” (p. 14). This characteristic explains why the Egyptian pharaohs commissioned their sculptures in granite and why the Greeks preferred marble to represent their deities.
However, despite its apparent indestructibility, stone is susceptible to erosion processes caused by climatological factors. On the other hand, acid rain, sudden temperature changes and the biological action of lichens and microorganisms cause the progressive degradation of stone surfaces (Doehne & Price, 2010). Today, the conservation of historic stone sculptures depends on the application of modern hydrophobic coatings, such as silane coatings, nano-coatings, and hydrophobic polymers, which create invisible barriers against moisture and pollutants, allowing the stone to “breathe” while protecting it from aggressive elements.
Iron: Forging new possibilities
With the mastery of metallurgy, ancient civilizations began to experiment with iron as a sculptural material. Although initially limited by the technical difficulties of casting (requiring temperatures close to 1500°C), wrought iron made it possible to create more dynamic and resistant forms than stone. During the Middle Ages, iron was mainly used in decorative architectural elements such as railings, gates and balconies, which combined functionality and artistic expression.
The choice of iron responded to its versatility and ability to withstand stress, allowing for the creation of thinner and more elaborate structures than with stone. As Eitoku (2015) argues, “iron introduced the possibility of creating sculptures where linear elements and negative space became as important as the solid mass that characterized stone sculpture” (p. 87).
The main disadvantage of iron is its high susceptibility to corrosion, especially in humid or saline environments. Rust not only aesthetically disfigures parts, but also compromises their structural integrity (Corrosionpedia, 2023c). Traditional coatings for iron included lead-based paints and natural oils, which offered temporary protection, but required constant maintenance.
Today, epoxy, polyurethane and galvanized coatings provide more durable and effective solutions for the preservation of historic railway sculptures. When talking about the Eiffel Tower, few people can imagine the logistics implemented for the preservation of the work.
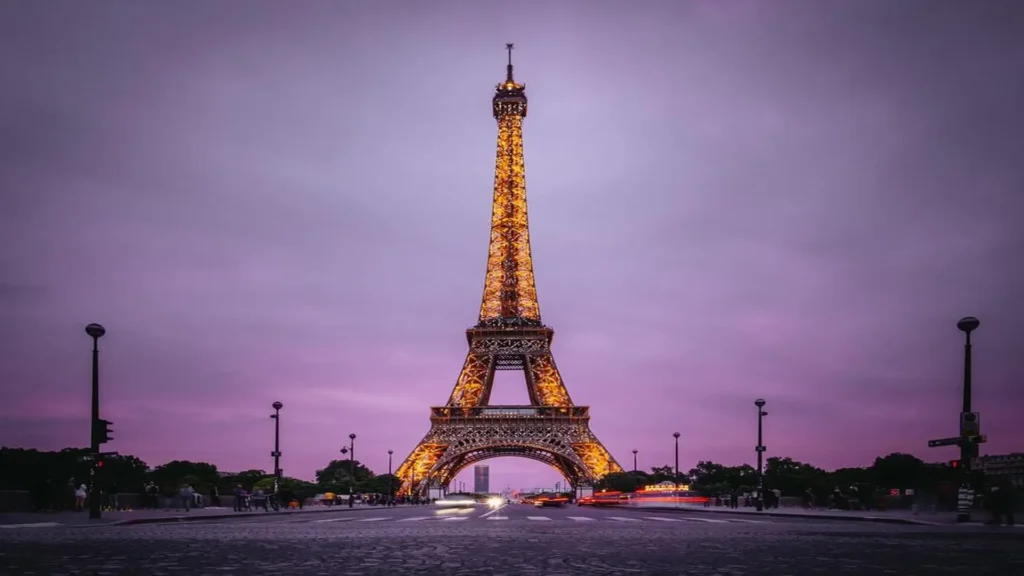
To prevent rusting, the iron lady has to be repainted every seven years, but after receiving 19 coats of paint for more than 130 years, a new way of preserving its youth must be found. The more coats are added, the more likely they are to peel off. In fact, that structure is a bit flaky and they are going to have to cover up the tower and repaint it.
It will be a titanic project to do this repainting work, considering that a routine repainting campaign takes two years and requires at least 30 painters on the layered structure. Repainting takes at least 3 to 4 years, and because of environmental rules and regulations, there will be areas that will be completely closed to avoid fumes and not pollute the Paris sky.
Marble: The quest for classical perfection
Marble reached its peak as a sculptural material during the classical Greek period and later in the Italian Renaissance. Its choice was not accidental: this type of metamorphic stone offers an exceptionally homogeneous surface, allows for a brilliant polish and, crucially, possesses a translucency that mimics the visual quality of human skin (Penny, 1993). Great masters such as Phidias, Michelangelo and Bernini exploited these qualities to create works that seemed to come to life.
The predilection for marble also had practical underpinnings. As Rockwell (1993) explains, “Marble, especially the Carrara varieties, combines a hardness sufficient to maintain precise detail with a workmanship that allows the sculptor to move relatively quickly” (p. 13). This combination of aesthetic and practical qualities explains its continued use for centuries.
However, marble has significant vulnerabilities to modern atmospheric pollution. The sulfur compounds present in the pollution react with the calcium carbonate of the marble, forming gypsum on the surface and causing what is known as “stone disease” (Siegesmund et al., 2002). This process disfigures the surface and progressively weakens the structure. Modern coatings for marble include consolidants based on silicates and nanoparticles that penetrate the crystalline structure without altering the visual appearance of the work, strengthening the material from within.
Bronze: The metal of gods and heroes
Bronze, an alloy mainly of copper and tin, revolutionized sculpture by allowing the creation of forms through the lost wax casting method. Used since ancient times in civilizations as diverse as the Chinese, Greek and Mesopotamian, bronze became the material of choice for representing deities and heroic figures (Scott, 2002). Its popularity was due to multiple factors: the ability to create hollow (lighter) works, the ability to record fine detail, and the natural formation of a protective patina.
As Corrosionpedia (2023b) notes, “bronze alloy was historically chosen for its excellent castability, allowing intricate detail to be reproduced, and for naturally developing a greenish patina (basic copper carbonate) that many considered aesthetically appealing and offered some degree of additional corrosion protection.”
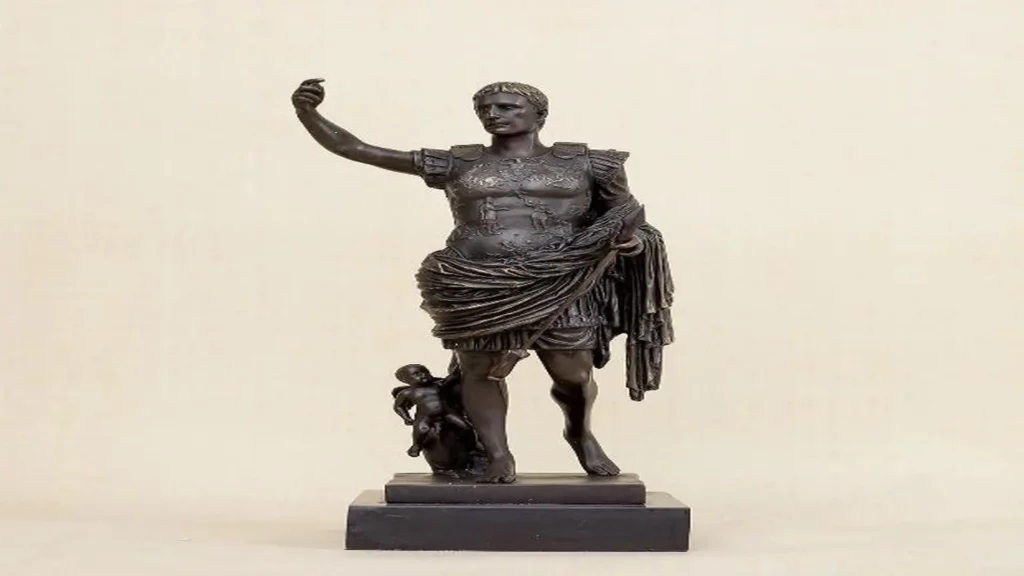
However, exposed bronze sculptures undergo accelerated corrosion processes in contemporary urban environments. Acid rain, bird droppings, and atmospheric pollution cause unstable patinas to form that can lead to loss of surface detail and structural problems (Corrosionpedia, 2023b). Modern conservators use bronze-specific corrosion inhibitors and clear acrylic coatings that preserve the historic patina while providing a barrier against corrosive agents. Sealers such as elastomeric, siliconized acrylic and polyurethane sealers are also used.
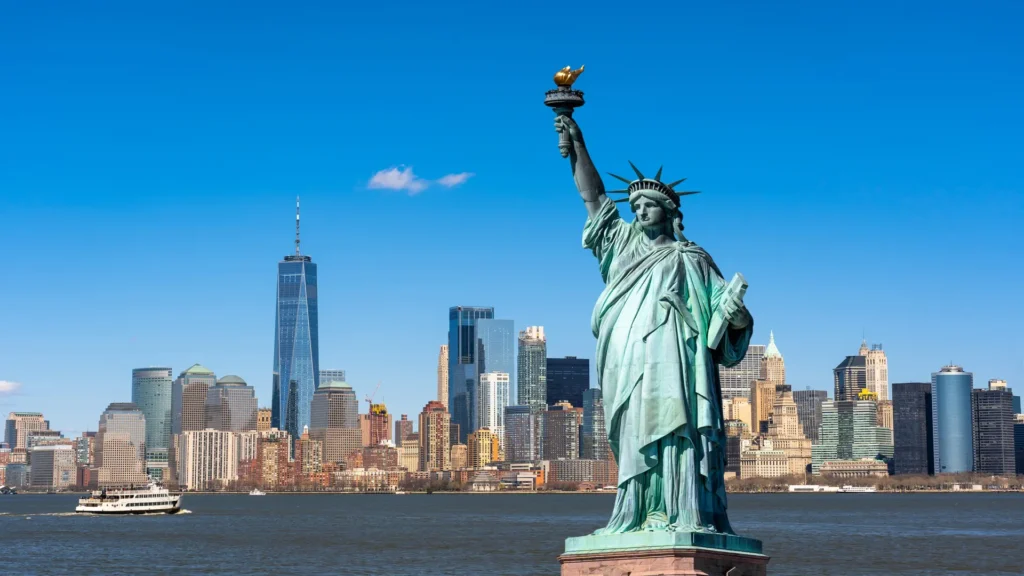
In the case of the Statue of Liberty, although it is not bronze, but copper, its exposure to the salty air of New York Harbor requires regular inspections for signs of deterioration. The Statue of Liberty’s green patina is a protective layer that forms naturally on copper due to oxidation and exposure to the elements. Rather than being removed, it is preserved and controlled because it protects the underlying metal from corrosion.
Stainless steel: The modernist revolution
With the advent of the industrial age and the artistic avant-garde of the 20th century, sculptors began to explore new materials that reflected the aesthetics and values of modernity. Stainless steel, developed commercially in the early decades of the 20th century, became an emblematic material for artists such as David Smith, Richard Serra and Jeff Koons (Krauss, 1977). It was chosen for both practical and conceptual qualities: exceptional resistance to corrosion, the ability to withstand high structural stresses and reflective surfaces that established a dialogue with the environment.
Stainless steel owes its resistance to corrosion to the presence of chromium in the alloy (minimum 10.5%), which forms a passive layer of chromium oxide on the surface, self-healing when damaged (Sedriks, 1996). This characteristic makes it ideal for sculptures exposed to adverse environmental conditions, minimizing maintenance needs. (Work in stainless steel: Fragment of rain for Caracas, by Carlos Medina).
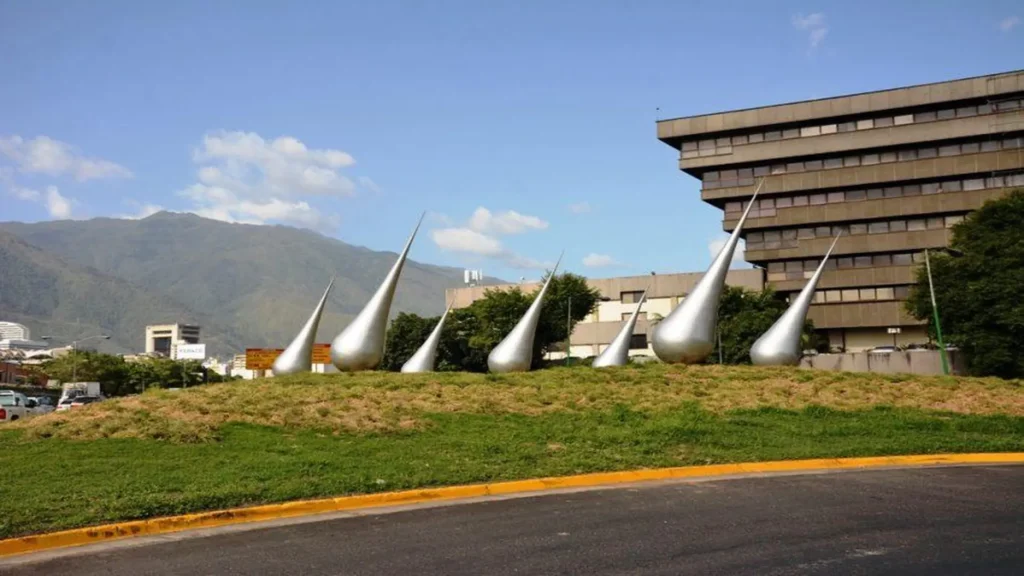
Among the most famous iconic works include the Pyramid of the Louvre Museum in Paris, constructed of steel and aluminum, has a special coating to protect it from corrosion. The steel, which forms part of the pyramid’s structure, is coated with a type of paint specially designed to resist corrosion and the effects of time.
A special paint is used that contains components that prevent rust and corrosion of the steel. This paint is usually of the epoxy or polyurethane type, which offer excellent resistance to weathering and chemicals. Another iconic structure is the Atomium, located in Brussels, Belgium. It is an architectural landmark symbolizing innovation in materials engineering, constructed of steel with a special coating containing chromium, nickel and molybdenum for high corrosion resistance.
Despite its superior durability, stainless steel is not completely free of preservation problems. In particularly aggressive marine or industrial environments, it can develop pitting from localized corrosion and staining from surface contamination (Corrosionpedia, 2023c). Contemporary coatings for stainless steel include nanostructured hydrophobic and oleophobic films that repel contaminants and facilitate cleaning, while maintaining the material’s characteristic luster.
Modern coatings: A revolution in preservation
The development of advanced coatings represents one of the major advances in the conservation of historic sculptures in recent decades. These protective systems have evolved from simple physical barriers to complex formulations that interact at the molecular level with the substrates they protect. As explained in Corrosionpedia (2023a), “modern coatings not only protect the surface of sculptures, but in many cases can stabilize already initiated degradation processes and significantly prolong the life span of heritage works”.
Among the most promising technologies are:
Sol-gel coatings: Based on hybrid organic-inorganic chemistry, these coatings form three-dimensional networks at the nanometer level that provide excellent adhesion and corrosion protection. Their transparency makes them ideal for cultural heritage applications where the original appearance must be preserved (Brinker & Scherer, 1990).
Green corrosion inhibitors: Derived from plant extracts and other biocompatible compounds, these inhibitors replace traditional inhibitors based on toxic heavy metals. They work by forming stable complexes with metal ions on the surface of the sculpture, preventing electrochemical reactions that would cause corrosion (Corrosionpedia, 2023b).
Applied nanotechnology: silica, titanium and silver nanoparticles incorporated in coatings provide additional functionalities such as superhydrophobicity, photocatalytic effect for self-cleaning and antimicrobial properties that prevent biodeterioration (Baglioni et al., 2015).
Let’s return to an outstanding example of the application of these technologies and specifically found in the restoration of historic monuments in New York. According to Corrosionpedia (2023a), “the Statue of Liberty, built with an iron frame and copper cladding, has been protected with specialized coatings that address the specific challenges of galvanic corrosion between dissimilar metals and exposure to the salty atmosphere of the bay.”
Ethical and technical challenges in modern conservation
The application of modern coatings on historic heritage raises important ethical and technical issues that conservators must carefully consider. The fundamental principle of reversibility, which states that any intervention on a heritage work should be removable without damaging the original, may conflict with the need for effective long-term protection (Muñoz Viñas, 2005).
The most efficient coatings are often those that interact most intimately with the substrate, which can compromise their reversibility. In that sense, as Ashley-Smith (2018) notes, “there is an inherent tension between protective effectiveness and full reversibility; conservators must navigate this dilemma by seeking the optimal balance for each specific case” (p. 143).
Another significant challenge is the compatibility between historic materials and modern coatings. Differences in coefficients of thermal expansion, water vapor permeability and mechanical properties can lead to stresses that accelerate deterioration rather than prevent it (Corrosionpedia, 2023c). Here, interdisciplinary research between chemists, physicists, materials engineers and conservators is essential to develop solutions adapted to each type of work and environmental condition.
Conclusions
From stone to stainless steel, each material has brought distinct aesthetic and technical possibilities, but has also presented specific vulnerabilities to the passage of time and atmospheric agents. Modern coatings represent the current culmination of this quest, making it possible to preserve the artistic legacy of the past while developing new expressive languages.
As demonstrated in the cases analyzed, effective conservation of sculptural heritage requires a multidisciplinary approach that combines advanced scientific knowledge with historical and artistic sensitivity. Coating technologies not only extend the useful life of the works, but also make it possible for future generations to enjoy them in conditions similar to the original ones.
The future of sculptural conservation points towards increasingly specific coatings, molecularly designed for each type of material and environmental condition. Nanotechnology and biomimetics offer promising prospects for developing protective systems that mimic natural self-protection and repair mechanisms (Giorgi et al., 2010). These innovations will allow history materialized in sculptures to continue to communicate its messages through time, bridging past, present and future.
References
- Appelbaum, B. (2007). Conservation treatment methodology. Butterworth-Heinemann.
- Ashley-Smith, J. (2018). The ethics of conservation. Getty Conservation Institute.
- Baglioni, P., Carretti, E., & Chelazzi, D. (2015). Nanomaterials in art conservation. Nature Nanotechnology, 10(4), 287-290. https://doi.org/10.1038/nnano.2015.38
- Brinker, C. J., & Scherer, G. W. (1990). Sol-gel science: The physics and chemistry of sol-gel processing. Academic Press.
- Corrosionpedia. (2023a). Using Modern Coatings to Restore Historical New York Landmarks. Corrosionpedia. https://www.corrosionpedia.com/using-modern-coatings-to-restore-historical-new-york-landmarks/2/6607
- Corrosionpedia. (2023b). Corrosion and Protection of Outdoor Bronze Sculptures. Corrosionpedia. https://www.corrosionpedia.com/corrosion-and-protection-of-outdoor-bronze-sculptures/2/6579