Introduction
In the operation of industrial and energy facilities, control rooms are the core where monitoring, decision-making and management of critical processes converge. Personnel operating in these environments, commonly referred to as panelists or control room operators, are tasked with ensuring the continuity, safety, and efficiency of operations.
However, in many organizations, attention to the ergonomic design of these spaces has been underestimated. This ignores that the constant interaction between the operator and the control systems can be affected by factors such as fatigue, inadequate posture, information overload, or lack of environmental comfort. These aspects have an impact on the health and well-being of personnel, and on the ability to respond to abnormal situations, increasing the risk of operational errors and decreasing productivity.
The purpose of this article is to highlight the determining factors of ergonomics in control rooms, with a technical and practical approach aimed at professionals in the energy and industrial sector. By the end of the reading, you will understand how ergonomics can be a strategic factor to increase the efficiency, safety, and operational performance of your organization.
What is ergonomics?
Ergonomics is a scientific and technical discipline that studies the relationship between people, the elements of a system, and its environment, with the objective of optimizing human well-being and the overall performance of systems. Also known as human engineering or human factors, ergonomics seeks to adapt products, tasks, spaces, and processes to the physical, cognitive, and psychological characteristics, capabilities, and limitations of users.
The essential purpose of ergonomics is to design systems in which working conditions are safe, healthy, and efficient, reducing the risk of injury, fatigue, errors and increasing productivity and job satisfaction.
From a technical approach, ergonomics is classified into three main areas:
- Physical ergonomics: Studies the interaction between human beings and the physical elements of their work environment. It covers aspects such as posture, movement, tool design, workstation layout, load handling, and prevention of musculoskeletal disorders.
- Cognitive ergonomics: focuses on the mental processes of individuals, such as perception, memory, attention, mental workload and decision-making. This area seeks to make information systems and operating procedures intuitive, clear and avoid cognitive overload.
- Organizational Ergonomics: Analyzes organizational structure, communication, company culture, work shifts, time management and social interaction. It aims to optimize organizational processes to improve performance and staff well-being.
In addition to these areas, ergonomics integrates knowledge from various disciplines such as physiology, biomechanics, psychology, engineering, anthropometry, and occupational medicine, which allows a comprehensive approach to the factors that affect human performance in the work context.
Today, the application of ergonomics is essential in sectors such as industry, energy, construction, health and services, improving the safety and health of workers, as well as optimizing the efficiency, quality, and sustainability of production processes.
Importance of ergonomics in control rooms
In industrial and energy facilities, control rooms are spaces where operators supervise and manage processes that directly impact safety, continuity and operational efficiency; therefore, ergonomics applied to control rooms is not a secondary aspect, but a key factor to ensure the correct performance of personnel and minimize operational risks.
The work of panelists or control room operators involves continuous exposure to multiple sources of information, alarm monitoring, real-time decision-making, and, in many cases, long working hours under high levels of pressure. Without proper ergonomic design, these factors can lead to physical and mental fatigue, loss of concentration, increased human error, and even health problems for operators.
Aspects supporting the importance of ergonomics in control rooms
- Improves responsiveness to critical situations: An ergonomically optimized environment enables operators to quickly, clearly, and easily access key information, facilitating timely and accurate decision-making.
- Reduces fatigue and operational stress: A design that considers posture, lighting, temperature, noise, and distribution of work elements reduces physical and mental overload, favoring sustained concentration.
- Minimizes human error: Adequate location of screens, controls, alarms, and appropriate presentation of information reduces the risk of omission or misinterpretation of critical data.
- Contributes to operational safety: Ergonomics helps to anticipate and mitigate incidents derived from distractions, fatigue or communication failures, significant elements in high-risk industries such as energy, petrochemical or continuous processes.
- Increases productivity and efficiency: When operators work in an environment adapted to their physiological and cognitive needs, overall performance improves, positively impacting the organization’s efficiency indicators.
- Promotes well-being and job satisfaction: An adequate ergonomic environment favors motivation, reduces absenteeism due to health problems, and improves the perception of quality of work life.
Key ergonomic factors in control room design
The ergonomic design of a control room should consider variables that together ensure an efficient, safe, and comfortable operating environment for personnel. These factors must consider the physical appearance of the space, and the cognitive and organizational needs of the panelists overseeing critical processes.
The following are the key ergonomic factors that should be considered in the planning and layout of a control room:
1. Workstation design and layout.
The physical configuration of the space should allow comfortable and safe access to all monitoring and control elements. The most important of these include :
- Proper height, depth, and orientation of consoles and tables.
- Optimal reach and visibility of screens, keyboards, and control devices.
- Sufficient space to allow freedom of movement and postural changes.
2. Anthropometry and ergonomic furnishings
Furniture should fit the average body dimensions of operators, allowing adaptability for different users. Key aspects include:
- Ergonomic chairs with lumbar support, height adjustment and armrests.
- Work surfaces that allow a neutral posture to be maintained.
- Adjustable elements to minimize postural fatigue.
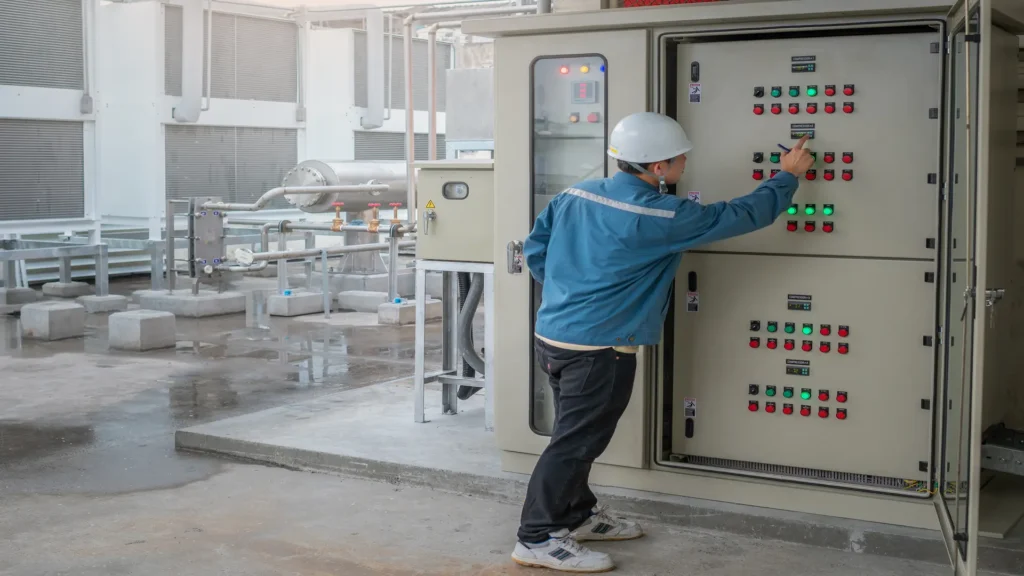
3. Distribution and display of information
The presentation of information on screens and panels should be clear, hierarchical, and easy to interpret. It is recommended:
- Logical organization of screens and process graphics.
- Adequate size, contrast, and color of visual elements.
- Minimization of irrelevant information that may generate cognitive overload.
4. Lighting
It is important to have adequate lighting to avoid reflections, glare, or low visibility areas. Natural and artificial light levels should be balanced, considering:
- Use of indirect and adjustable lighting.
- Elimination of reflections on screens and consoles.
- Adequate color temperature for prolonged monitoring environments.
5. Environmental conditions
Factors such as temperature, humidity, and noise level directly influence the comfort and concentration of operators. It is advisable to:
- Keep the temperature in a comfortable range (generally between 22 °C and 25 °C).
- Control ambient noise levels below 50 dB to avoid distractions.
- Ensure adequate ventilation and air quality.
6. Location and accessibility of controls and alarms
Control devices and alarm systems should be located within the operators’ field of vision and manual reach. It is important:
- Prioritization of alarms by criticality and frequency.
- Easy access to emergency buttons and communication systems.
- Intuitive and standardized interface design.
7. Shift and break management
Ergonomic design should be complemented with organizational practices that minimize fatigue and stress derived from prolonged work, including:
- Shift rotation that allows for physical and mental recovery.
- Incorporation of active breaks and adequate rest areas.
- Continuous training on good ergonomic practices.
A design that takes these factors into account will not only improve operational efficiency and reduce human error, but will also contribute to the overall well-being of personnel, strengthening the culture of safety and productivity in industrial operations.
Standards and best practices in control room ergonomics
The ergonomic design of control rooms should not only be based on technical and functional criteria, but also on compliance with international standards and the application of industry-recognized best practices. These guidelines ensure that supervisory environments meet standards that promote safety, health, and operational efficiency.
Technical standards for ergonomic control room design
There are several regulations that guide the ergonomic design of workstations and, specifically, of control rooms. Some of the most relevant are:
1. ISO 11064 – Ergonomic design of control centers. This series of international standards is the main reference for the design of control rooms. It is composed of seven parts that address aspects such as:
- General design principles.
- Analysis and specification of requirements.
- Design of workspace layout.
- Workstation layout design.
- Design of man-machine interfaces.
- Environmental design (lighting, noise, air conditioning).
- Ergonomic compliance assessment.
2. ISO 9241 – Ergonomics of Human-System Interaction Provides guidelines for user interface, including presentation of information, ease of use, and reduction of cognitive load.
3. ANSI/HFES 100 – Human Factors Engineering of Computer Workstations Provides detailed criteria for ergonomic configuration of workstations, also applicable to control rooms.
4. OSHA – Occupational Safety and Health Regulations Although not specific to control rooms, the Occupational Safety and Health Administration (OSHA) guidelines include recommendations for minimizing ergonomic hazards in the work environment.
Best practices in control room ergonomics
In addition to regulatory compliance, the application of best practices helps to optimize the operating environment. Some of the recommended practices are:
- Operator participation in the design process: Including end-user input ensures that the design meets the real needs of those working in the control room.
- Periodic ergonomic evaluations: Conduct internal audits to identify opportunities for improvement in layout, lighting, furniture, and environmental conditions.
- Continuous training in ergonomics: Train personnel in healthy habits, postural techniques and proper use of work elements.
- Operational fatigue management: Establish protocols that include rest times, task rotation and workload monitoring.
- Application of a holistic approach to ergonomics: Consider not only physical aspects, but also cognitive, organizational, and psychosocial factors that affect the operator’s performance.
The following video presents the purpose of ISO 11064, which is to establish a generic framework for the application of ergonomic principles and recommendations to the design and evaluation of control centers. This is done in order to eliminate or minimize the risk of human error. Source: HF Specialist in human factors.

ISO 11064 and the control room solution.
Benefits of implementing ergonomics in control rooms
Implementing ergonomic principles in the design of control rooms not only improves the comfort and well-being of operators but also has a direct impact on the productivity, safety, and operational efficiency of the organization. The benefits of proper ergonomics in these environments are vast and encompass both the human and organizational levels.
1. Improved physical and mental well-being of operators
One of the most important benefits of ergonomics is the reduction of physical fatigue and mental stress in control room operators. Prolonged work in poorly designed environments can result in musculoskeletal disorders, eye fatigue, and stress-related problems. However, by applying ergonomic principles, such as the correct arrangement of furniture and improved environmental conditions, the risk of these concerns is significantly reduced. This contributes to the overall well-being of staff and their long-term health.
- Reduced musculoskeletal injuries: Adapting chairs, tables, and screens to the physical needs of the operator minimizes the risk of low back pain, muscle strains, or posture-related injuries.
- Improved concentration: Improved working conditions, such as proper lighting and noise reduction, promote the ability to concentrate and reduce mental fatigue.
2. Increased operational efficiency
Ergonomics helps operators work more efficiently and with less effort. When systems and tools are designed according to human needs, reaction times are reduced and productivity improves. Operators can perform their tasks faster and more accurately, without having to make constant adjustments or unnecessary movements.
- Optimized response time: Properly designed screens and controls allow operators to quickly and clearly access critical information, facilitating immediate decision making in emergency situations.
- Reduced errors: Well-organized information, with intuitive interfaces and clear visibility of data, reduces the possibility of operational errors.
3. Increased operational safety
Ergonomics improves safety in control rooms, minimizing the risk of accidents and human error. Properly designed spaces allow safer interaction with systems, and operators are less likely to make critical errors under adverse conditions.
- Reduced accidents: The design of visible and easily accessible controls and alarms allows operators to respond quickly to emergency situations, reducing the likelihood of incidents.
- Improved responsiveness: In ergonomically designed environments, operators will respond efficiently in high-pressure situations, increasing the likelihood of mitigating risks and preventing accidents.
4. Increased job satisfaction and motivation
The physical and e motional well-being of operators not only affects their health, but also their level of motivation and commitment to work. Ergonomic improvements demonstrate that the company cares about the comfort and safety of its personnel, which can increase job satisfaction and reduce employee turnover.
- Improved morale: Ergonomically designed control rooms create a pleasant work environment that promotes operator satisfaction and engagement.
- Reduced job stress: By eliminating stressors such as discomfort or fatigue, operators experience less stress, which improves their overall performance and well-being.
5. Long-term cost reduction
Although implementing ergonomics in control rooms may require an initial investment, the long-term benefits are significant. Improved operator health reduces costs associated with medical care, sick days, and staff turnover, resulting in financial savings for the organization.
- Reduced sick leave: Prevention of musculoskeletal injuries and other health problems leads to lower incidence of medical absenteeism.
- Longer equipment life: An ergonomic environment also protects the equipment and tools used, extending their useful life and reducing maintenance costs.
Conclusions
The implementation of ergonomic principles in control rooms transcends the improvement of operator comfort, constituting an integral strategy that optimizes operational efficiency, safety and labor welfare. It also facilitates compliance with regulatory standards and promotes organizational sustainability. Consequently, any entity that aspires to maximize its performance and ensure a safe and healthy work environment must consider ergonomics as a critical factor in the design of its operational spaces.
Proper planning and the implementation of ergonomic best practices will enable companies to have more efficient, safe, and productive control rooms, generating a significant competitive advantage in the energy and industrial sectors. The integration of ergonomics in operating spaces not only preserves the health and well-being of operators but also constitutes a fundamental element in maximizing operational efficiency, reinforcing industrial safety, and optimizing real-time decision making.
References
- International Ergonomics Association. (2019). What is ergonomics? International Ergonomics Association. Recuperado de https://www.iea.cc/what-is-ergonomics
- International Organization for Standardization. (2018). ISO 11064: Ergonomic design of control centres. ISO.
- McAtamney, L., & Nigel, C. (2017). Workplace ergonomics: A practical guide. Routledge.
- Robertson, M. M., & Lee, S. M. (2018). Ergonomics and human factors: Theories and applications.
- Van der Molen, H. F., & Huitema, G. L. (2016). Ergonomics and productivity in control rooms: A review of the literature. Applied Ergonomics.