Are you fighting against flash rust? This fast-appearing surface rust phenomenon, with repercussions on the durability and functionality of metal structures, is a common problem in metal protection, especially after wet surface cleaning and preparation processes such as water blasting or pressure washing.
Flash rust, also known as flash rust, can compromise the adhesion and performance of protective coatings, directly affecting the service life of metal structures.
Understanding the underlying causes of flash rust formation and implementing effective rust prevention strategies is critical to rust treatment and metal finishing performance, particularly in the corrosion protection industry. This article discusses the mechanisms of flash rust formation, the factors that contribute to its occurrence and key strategies for its prevention.
What is flash rust?
Flash rust is a surface corrosive process that occurs rapidly on metal substrates exposed to moisture, triggering an immediate reaction with oxygen and compromising the quality of the metal treatment and finish. Unlike generalized corrosion, this phenomenon manifests itself as a reddish or orange-colored surface rust layer that can appear in a matter of minutes or hours.
Although it is a surface phenomenon, its presence is problematic, interfering significantly at the interface between the metal substrate and the applied protective systems. This surface oxide layer modifies the surface energy of the metal and creates a physical barrier that hinders the correct wetting and mechanical anchoring of paints, protective coatings and other finishes.
The resulting reduction in adhesion compromises the long-term durability and effectiveness of metal protection, exposing industrial assets to premature corrosion and potential non-compliance with their operational specifications.
How is flash rust formed?
Its formation is an electrochemical process that occurs when the metal surface treated by cleaning or cutting is exposed to air, coming into contact with moisture and oxygen, resulting in instantaneous oxidation, which is mainly composed of iron hydroxide. Under these conditions, corrosion microcells are established, where anodic and cathodic reactions develop simultaneously.
In anodic areas, metallic iron (Fe) is oxidized, releasing iron ions (Fe²⁺) to surface water:
- Anodic reaction (iron oxidation): Fe → Fe2+ + 2e– These dissolved Fe²⁺ ions migrate to the cathodic areas, where they react with the oxygen dissolved in the water and the electrons generated in the anodic reaction, forming hydroxide ions (OH-).
- Cathodic reaction (oxygen reduction): O2 + 2H2O + 4e- → 4OH– Next, Fe²⁺ ions react with hydroxide ions (OH-) to form ferrous hydroxide [Fe(OH)₂], which is unstable and, in the presence of oxygen and water, further oxidizes to form ferric hydroxide [Fe(OH)₃], the main component of the oxide.
- Surface rust formation: 4Fe(OH)2 + O2 + 2H2O → 4Fe(OH)3 (Yellow, bright orange or reddish-brown are the characteristic colors of flash rust). This process occurs rapidly due to the high reactivity of the freshly cleaned metal surface, together with the presence of a thin layer of water, which facilitates ion transport and electrochemical reactions.
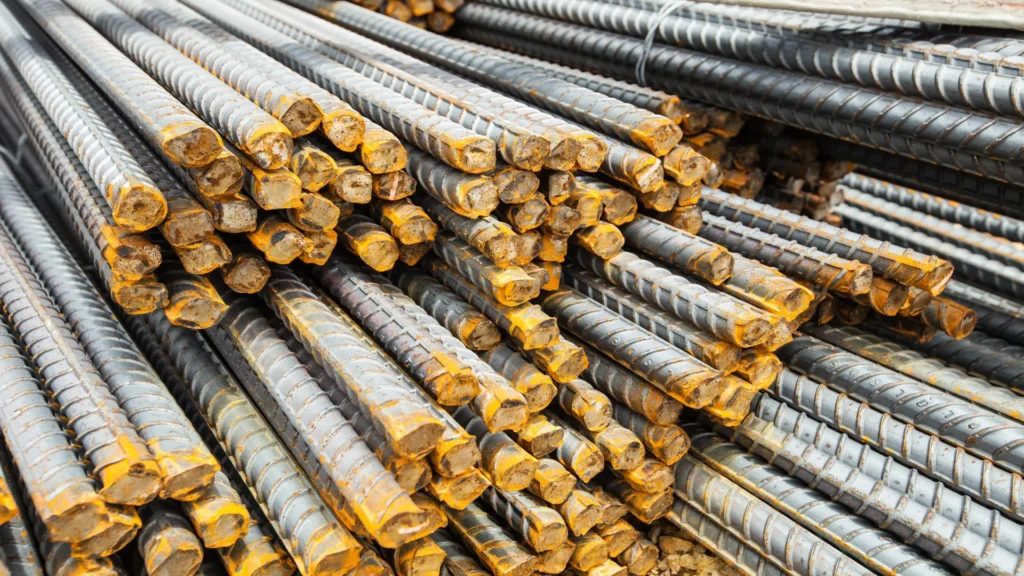
Factors contributing to flash rust formation
Among the most important factors that accelerate the flash rusting process are:
- Relative humidity: To prevent flash rusting it is important to control humidity. A humid environment elevates and accelerates the electrochemical process, favoring the formation of surface oxides.
- Temperature: High temperatures accelerate chemical reactions, increasing the rate of oxide formation.
- Contaminants in the substrate: Soluble salts such as chlorides and sulfates act as electrolytes, intensifying corrosion. These contaminants may remain after inadequate cleaning processes.
- Quality of water used for cleaning: If it contains corrosive ions, it accelerates oxidation.
- Metal surface finish: Rough or porous surfaces retain more moisture and contaminants.
- Steel type: Carbon steels are more susceptible to flash rust compared to stainless or alloy steels.
- Environmental humidity control: By eliminating humidity, the corrosion process is controlled, eliminating a basic element for the development of rust.
- Fast drying: Use of dry compressed air or controlled heat after wet cleaning.
- Adjustment in surface cleaning: Modifying cleaning techniques, by using deionized water to avoid the accumulation of soluble salts or reducing the exposure time, avoids flash rusting.
- Rust inhibitor application: During surface cleaning it is recommended to apply additives and chemical barrier builders.
- Use of primers with corrosion inhibitors: A high quality primer and corrosion inhibitor can prevent bare metal from being exposed to moisture and oxygen.
- Rapid application of protective coatings: Once the metal surface is clean and dry, the application of the primary protective coating should be done immediately to isolate the metal from the corrosive environment.
- Exposed surface care: Avoid contamination of the clean surface with salts, dust or fingerprints, as these act as starting points for oxidation.
- Special protection in cut areas: Areas where steel has been cut, either by mechanical or thermal means, present susceptibility and reactive spots. These areas require immediate cleaning and application of rust inhibitors to prevent the rapid appearance of flash rust due to exposure of the base metal without the original protective coating.
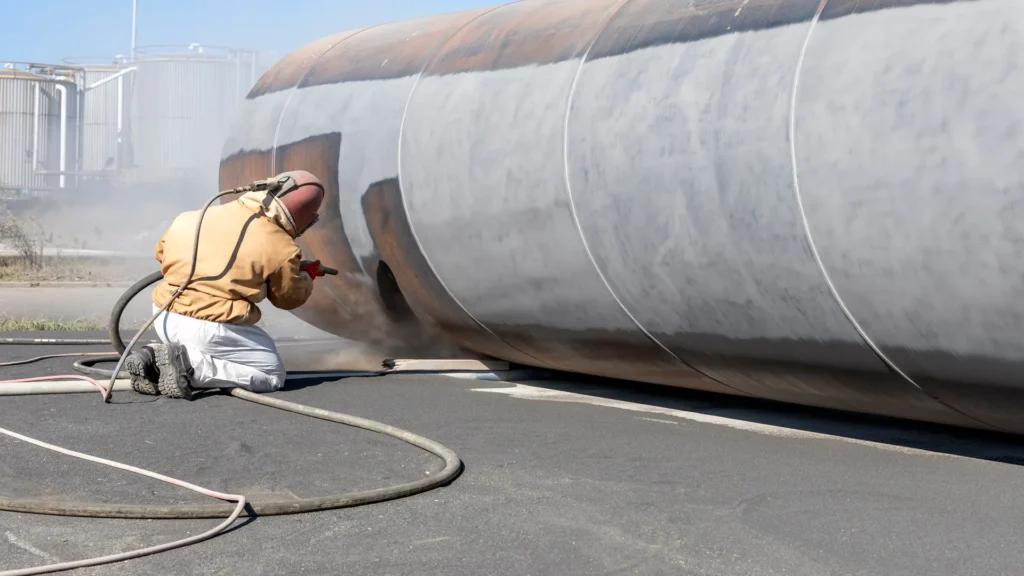
Strategies for flash rust prevention
To keep metal surfaces in optimum condition, it is necessary to implement surface rust prevention measures, paying special attention to parts made of iron, cast iron or carbon steel. The more sensitive the metal, the more oxidative phenomena will occur.
- Control of ambient humidity: By eliminating humidity, the corrosion process is controlled, eliminating a basic element for the development of rust.
- Rapid drying: Use of dry compressed air or controlled heat after wet cleaning.
- Adjustment in surface cleaning: Modifying cleaning techniques, by using deionized water to avoid the accumulation of soluble salts or reducing exposure time, prevents flash rusting.
- Application of rust inhibitors: During surface cleaning it is recommended to apply additives and chemical barrier builders.
- Use of primers with corrosion inhibitors: A high quality primer and corrosion inhibitor can prevent bare metal from being exposed to moisture and oxygen.
- Quick application of protective coatings: Once the metal surface is clean and dry, application of the primary protective coating should be done immediately to isolate the metal from the corrosive environment.
- Care of the exposed surface: Avoid contamination of the clean surface with salts, dust or fingerprints, as these act as starting points for oxidation.
- Special protection in cut areas: Areas where steel has been cut, either by mechanical or thermal means, present susceptibility and reactive spots. These areas require immediate cleaning and the application of rust inhibitors to prevent rapid rusting.
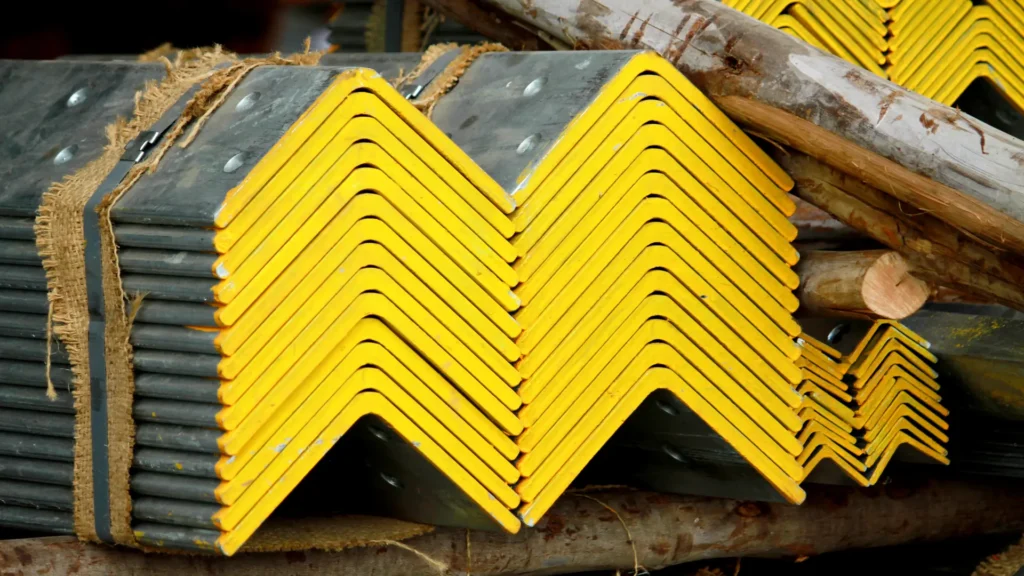
Rust inhibitors and their role in flash rust prevention
Rust inhibitors are chemical compounds that are added to cleaning water or applied directly to metal surfaces to retard rusting. Their use is essential and they act through several mechanisms:
- Protective barrier formation: These compounds create a thin film on the surface of the metal, preventing direct contact with moisture and oxygen, basic factors for corrosion.
- Metal surface passivation: Inhibitors form a passive layer that reduces its reactivity, hindering the occurrence of corrosive processes.
- Corrosive ion sequestration: Some inhibitors neutralize or immobilize corrosive ions present in the environment or in the cleaning water, preventing their interaction with the base metal.
- Electrochemical reaction inhibition: These compounds interfere in the anodic or cathodic reactions that facilitate corrosion, slowing down the process.
The choice of the appropriate inhibitor depends on factors such as the type of metal, environmental conditions and compatibility with subsequent coatings.
Rust inhibitor solutions
Cortec Corporation, a green chemistry company noted for its R&D capabilities and focus on creating innovative solutions for corrosion protection, has developed VpCI®-377, a concentrated water-based rust inhibitor. This additive meets stringent anti-pollution requirements and offers a wide range of dilutions with water (0.5-20%), allowing customization of protection duration and applied cost per unit area.
VpCI®-377 forms a solution in water and is applied to metal surfaces by spraying or dipping. It is not necessary to remove it, but, it can be removed with conventional alkaline cleaners; it is especially effective in preventing flash rust, because rust appears long after cleaning with water; because it forms a protective barrier that insulates the metal from water and air, and calms the surface so that it does not rust as quickly.
Surface rust treatment
If flash rust has already formed, the following actions are recommended prior to coating:
- Mechanical or abrasive brushing to remove surface rust.
- Use of chemical removers designed to dissolve rust without damaging the metal.
- Application of rust-converting primers that transform corrosion into a stable and coatable layer.
Conclusion
Flash rust is a recurring problem in the metal treatment and finishing industry, affecting the quality and durability of protective coatings. The implementation of adequate rust prevention strategies, such as moisture control, application of rust inhibitors and high performance protective coatings, is required to avoid premature failures in metal protection.
With this knowledge, professionals can optimize corrosion protection processes and ensure a longer service life of metallic materials in various industrial applications.
References
- https://www.corrosionpedia.com/definition/519/flash-corrosion