Table of Contents
- Introduction
- History of the American Welding Society
- Growth, transformation, and future of the American Welding Society
- Innovation and technical leadership
- Case studies and statistics
- Economic impact of AWS standards
- Global impact
- Challenges faced
- Programs: Training, preparation and certification
- Conclusions
- References
Introduction
The American Welding Society (AWS), founded in 1919, has been a cornerstone in the advancement of welding science and technology for more than a century. Throughout its 106 years of existence, the AWS has demonstrated an unwavering commitment to innovation, leadership and standard-setting that has transformed the industry worldwide. The history of the AWS is, like any successful organization, an example of constancy and unwavering faith in making a place for itself in the world, through its outstanding achievements, the challenges it has faced and its global impact on the welding industry.
The purpose of this article is to highlight the history of the American Welding Society (AWS), its impact on the industry and its leadership in welding.
History of the American Welding Society
On March 28, 1919, at a critical time for the manufacturing industry after World War I, the American Welding Society was born in response to a critical need during a period of industrial transformation in the United States, when welding emerged as a fundamental and necessary technology for the manufacturing industry. During the war, the requirements to build ships and armaments quickly and efficiently had demonstrated the importance of welding as an alternative to traditional riveting. However, the lack of standards, unified procedures and adequate training resulted in quality inconsistencies and significant safety problems.
President Woodrow Wilson, recognizing this problem, called upon Comfort A. Adams, a respected Harvard professor of electrical engineering, to chair the Emergency Fleet Corp.’s Welding Committee. This committee’s initial mission was to standardize welding processes for shipbuilding. Subsequently, this governmental committee merged with the National Welding Council, an existing industry organization, to form the American Welding Society, with Adams as its first president.
The fundamental purpose of the AWS at the time of its creation was: To develop uniform standards for welding processes. To promote the training and certification of qualified welders. To advance scientific research on welding technologies, and, to establish a forum for the exchange of technical knowledge in the industry.
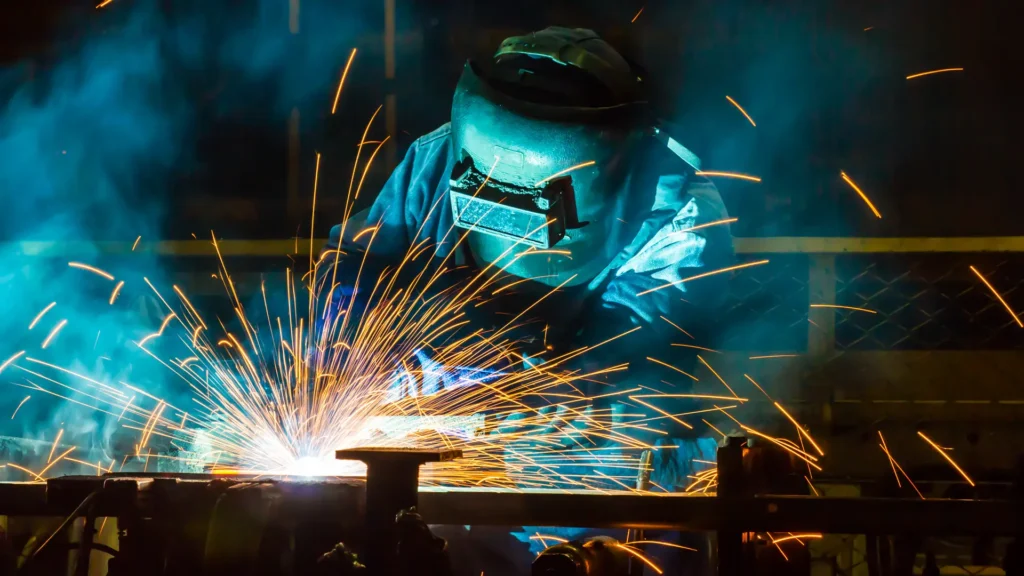
Extensive work was done to standardize and improve welding practices that had proven vital during the war effort. What began as a modest initiative would become one of the most influential technical organizations. In this way the AWS was responding to the practical need to ensure the quality, safety and efficiency of welding at a time when this technology was becoming an everyday practice and essential to the industrial development of the United States and, later, the world.
Growth, transformation, and future of the American Welding Society
Since its founding, the American Welding Society (AWS) has experienced impressive growth, establishing itself as a significant institution in the development of the welding industry. In its first year of operation, the AWS had only 217 members and published the first issue of the prestigious Journal of the American Welding Society. This modest beginning contrasts greatly with its current status, as the organization now serves more than 73,000 members worldwide, demonstrating its adaptability and leadership in the industry.
One of the most recent milestones in AWS’s transformation has been the renewal of its visual and digital identity. In this regard, the updated logo reflects a modern interpretation of the iconic AWS diamond, incorporating beveled metallic elements and contemporary typography. This change symbolizes the evolution of the organization and its commitment to modernizing the industry and reflects a new era for the Society as it represents a more contemporary style. This renewal is part of a comprehensive renovation project that also includes updating its website, improving the user experience and facilitating access to technical information and resources for industry professionals.
The global expansion of the AWS has been another key factor in its growth. Today, the organization is structured into 22 districts encompassing 250 sections and student chapters, allowing it to maintain a significant presence in more than 50 countries. This international network has been instrumental in unifying and raising welding standards worldwide, ensuring that best practices and technologies are available to professionals on different continents.
The following video provides a brief overview of how, for nearly 106 years, AWS has been driving the future of welding, elevating standards, inspiring leaders and uniting communities around the world. Source: American Welding Society.

Future of the American Welding Society.
The American Welding Society has grown in membership and geographic scope, and has evolved in its identity and strategic approach to the future. With a combination of tradition and innovation, the AWS continues to play an important role in the development and modernization of welding as a high-tech, high-skill industry globally.
Innovation and technical leadership
AWS has been a pioneer in promoting welding innovation through the development of numerous standards and codes used globally. Among the most prominent are:
- AWS D1.1 (Structural Welding Code – Steel): Considered the cornerstone of structural welding, this code is a must-have reference in infrastructure projects around the world.
- AWS D1.2 (Structural Welding Code – Aluminum): Establishes standards for welded aluminum structures.
- AWS D1.6 (Structural Welding Code – Stainless Steel): Defines practices for the welding of stainless steels.
But AWS’s technical influence extends beyond the publication of codes. Since 1970, it has published more than 2,200 research articles that have contributed significantly to the advancement of welding knowledge, addressing topics ranging from advanced metallurgy to innovative welding techniques.
Case studies and statistics
Golden Gate Bridge
One of the most iconic case studies demonstrating the importance of AWS standards is the construction of the Golden Gate Bridge in San Francisco. AWS provided the standards and training necessary to ensure the structural integrity of this engineering marvel. The welding methods employed, which conformed to the AWS standards of the time, have stood the test of time, allowing this iconic structure to continue in service after more than 88 years. The following image shows this great engineering work.
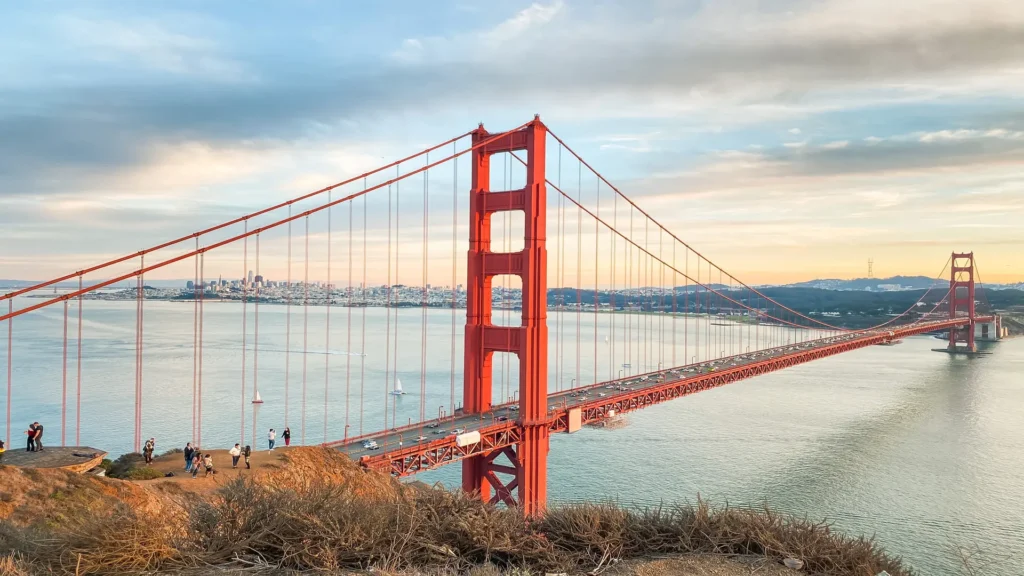
For the Golden Gate Bridge, which was built between 1933 and 1937, it is estimated that approximately 200 to 250 skilled welders worked on the project. This bridge was particularly significant because it represented a historic transition from rivet construction to welded construction for large structures. The welders faced extremely challenging conditions, including high winds and fog while working at great heights.
Burj Khalifa Project
The Burj Khalifa in Dubai, the world’s tallest building, represents another emblematic case where AWS standards proved their critical value. During its construction (2004-2010), welding techniques played a key role in the structural integrity of this 828-meter colossus. Engineers rigorously applied AWS D1.1 and D1.6 codes for the critical joints of the steel structure.
The tower required more than 330,000 cubic meters of concrete and 39,000 tons of steel, with thousands of welded joints that had to withstand extreme conditions, including wind speeds of up to 45 m/s. Certification of welders to AWS standards and inspection based on AWS criteria ensured that each joint met strength and durability requirements. After more than a decade in operation, the structure maintains its integrity with no weld-related structural failures, validating the effectiveness of the standards implemented.
In the case of the Burj Khalifa, the project employed approximately 300 to 350 welders certified specifically for critical structural work. The total project involved more than 12,000 workers at its peak, but the specialized welders comprised a select group that had to meet AWS certifications to perform critical joints in the steel structure. These professionals worked in continuous shifts to maintain the ambitious construction schedule for the world’s tallest building.
Undoubtedly, these estimates reflect the importance of having highly qualified personnel certified to AWS standards for large-scale infrastructure projects.
Economic impact of AWS standards
The economic impact of AWS on the global economy is considerable, although difficult to quantify precisely. According to recent studies by the International Institute of Welding, the implementation of AWS standards has generated an estimated savings of $12.5 billion between 2022 and 2023 in the global construction industry. These savings come mainly from:
- Reduced failure rates and repair costs: approximately $5.3 billion saved by reducing defective welds requiring correction.
- Process optimization: close to $4.1 billion in savings derived from more efficient procedures that reduce production times and material consumption.
- Accident prevention: about $3.1 billion in avoided costs related to accidents, production stoppages and litigation for structural failures.
In the energy infrastructure sector alone, the application of AWS standards has reduced maintenance costs by approximately 17% in the last two years, representing a savings of $2.8 billion globally. These figures demonstrate the role of AWS not only in safety and quality, but also as a catalyst for significant economic efficiencies across multiple industry sectors.
Global impact
The impact of AWS transcends U.S. borders. Its standards are adopted or referenced in more than 50 countries, demonstrating its international influence. The organization has established chapters in numerous countries and actively collaborates with institutions such as:
- International Institute of Welding (IIW).
- International Organization for Standardization (ISO).
- National welding associations in Europe, Asia and Latin America.
This international collaboration has harmonized standards and practices, facilitating global trade and raising the quality of welded constructions worldwide.
Challenges faced
Throughout its history, AWS has faced and overcome numerous challenges:
- Global standardization: The homogenization of standards worldwide has been particularly complex due to different regulations and industry practices between countries. AWS has addressed this challenge through persistent technical diplomacy, establishing strategic alliances with international bodies and adapting its standards to make them compatible with various regulatory frameworks.
- Technological innovation: Staying at the forefront of rapid technological evolution has required constant updating of standards and codes. To this end, a periodic review system has been implemented to ensure that its normative documents incorporate the latest advances in materials, equipment and welding techniques.
- Education and training: The chronic shortage of qualified welding personnel has been a persistent problem. To combat this, AWS has developed innovative educational programs, from professional certifications to online resources, ensuring the training of new generations of competent welders.
- Safety and quality: Ensuring safety and quality in welding processes remains a priority. The organization has established rigorous certification systems and inspection programs that have significantly raised safety standards in the industry.
- Adoption of new standards: One of the existing conditions in the industry is to get out of the comfort zone. Implementing new standards can be costly for companies. AWS has addressed this resistance through educational programs, technical assistance and transition periods that facilitate the adoption of new standards without compromising business competitiveness.
- Environmental sustainability: In response to growing environmental concerns, the AWS has incorporated sustainability considerations into its standards, promoting practices that minimize the environmental impact of welding processes.
Programs: Training, preparation and certification
Training programs
AWS develops a wide range of training programs to meet the needs of industry professionals:
- AWS Academy: This program offers a comprehensive, up-to-date welding technology curriculum designed for educational institutions. It prepares students to obtain industry-recognized certifications and develop practical skills highly valued by employers.
- AWS Skills Centers: These are face-to-face training centers where participants can explore career opportunities in welding through classes taught by certified instructors, interactive exhibits and professional networking events.
- Digital Technical Training: AWS has adapted its training offerings to the digital environment, offering more than 600 online courses on various aspects of welding and related technologies. These resources are complemented by hands-on labs and simulations that reinforce theoretical learning.
Preparation for certifications
The organization periodically provides materials specifically designed to help professionals prepare for certification exams, including study guides, specialized courses and educational videos.
AWS Educate: This is a program aimed at young people aged 13 and older, offering introductory welding content and access to a network of emerging talent. The program represents AWS’s commitment to cultivating early vocations in the welding field.
Certification program
Statistically speaking, the AWS has certified more than 100,000 welders worldwide. This certification program has contributed significantly to the improvement of quality and safety in the welding industry. AWS-certified welders are recognized globally for their technical competence and adherence to the highest quality standards.
Conclusions
Throughout its 106 years of existence, the American Welding Society has established itself as a transformational force in the welding industry. Its commitment to innovation, leadership and quality standards has significantly improved the safety and efficiency of welding processes worldwide.
The data presented confirms the profound impact of AWS: more than 73,000 active members, standards adopted in more than 50 countries, more than 100,000 certified welders and more than 2,200 published research articles. These numbers reflect a dynamic organization that has been able to adapt to technological and societal changes while holding firm to its core mission.
The legacy of the AWS transcends statistics; it represents an unwavering commitment to technical excellence and safety that has saved countless lives and enabled the construction of infrastructure that defines the modern world. As the AWS continues its second century of existence, its relevance as a global benchmark and invaluable resource for welding professionals remains undisputed.
References
- AcademiaLab. (s.f.). Sociedad Americana de Soldadura. https://academia-lab.com/enciclopedia/sociedad-americana-de-soldadura/
- Aggressive Tube Bending. (2023, enero 13). ¿Qué es la AWS? Conoce más sobre la Sociedad Estadounidense de Soldadura. https://blog.es.aggressivetube.com/2023/01/13/que-es-la-aws-conoce-mas-sobre-la-sociedad-estadounidense-de-soldadura/
- American Welding Society. (s.f.). Mission, Vision, Core Values. https://www.aws.org/About/Mission-Vision-Core-Values/
- Inspenet. (s.f.). Normas AWS en la integridad de soldaduras. https://inspenet.com/articulo/normas-aws-en-la-integridad-de-soldaduras/
- Inspenet. (s.f.). Importancia de la certificación CWI. https://inspenet.com/articulo/importancia-de-la-certificacion-cwi/
- Welding Research Supplement. (s.f.). https://www.aws.org/magazines-and-media/welding-research-supplement