Researchers at the University of Tartu’s Institute of Technology have developed an innovative method that allows robots to generate their own structures in real time. Inspired by the way spiders create their silk webs, this system uses extruded polymer fibers to form structural components on the fly.
Spider-inspired method
This approach represents a step forward in bio-inspired robotics , allowing robots to adjust their structure to the needs of their environment . Instead of relying on pre-assembled parts, the robot can weave its own body and tools from flexible, durable materials.
The material used is an extruded thermal polymer, which solidifies rapidly after application. This mechanism allows it to create paths, bridges, or even artificial limbs according to the requirements of the task at hand. This capability gives robots unprecedented adaptability in dynamic and challenging environments.
Applications in exploration and rescue work
The potential uses for this technology are broad. From rescue missions in disaster zones to exploration in uneven terrain, robots with in-situ spinning capabilities can build temporary structures to navigate obstacles. This could transform the way autonomous devices are deployed in extreme situations.
According to the researchers, one of the key experiments involved creating a makeshift bridge in a rubble environment. The robot wove fibers over an unstable surface, generating a structure strong enough to support its own weight and allow it to move forward safely.
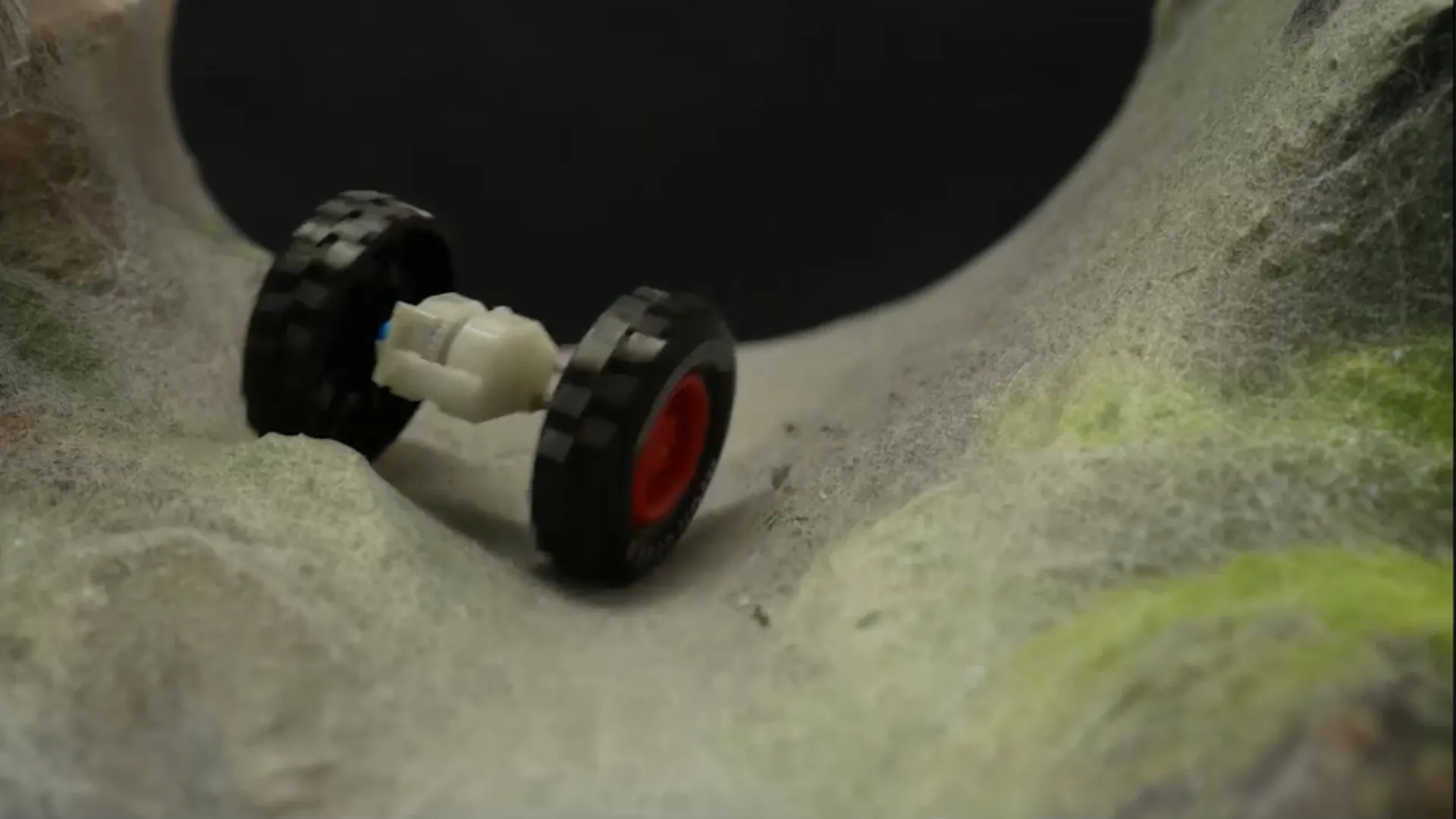
This in-situ spinning method allows robots to adjust their structure to the needs of the environment. Source: npj Robotics
The development of robots capable of self-construction and adapting their morphology marks a turning point in robotics engineering. Applications of this approach could extend to the construction sector, planetary exploration , and the creation of temporary infrastructure in extreme environments.
Follow us on social media and don’t miss any of our posts!
YouTube LinkedIn Facebook Instagram X (Twitter) TikTok
Source and photo: npj Robotics Magazine