Table of Contents
- Introduction
- What is a centrifugal pump?
- Basic operating principles of a centrifugal pump
- Types of centrifugal pumps
- Technological advances in centrifugal pump design
- Geometry impellers
- Examples of specific industrial applications for each type of pump
- What is cavitation in pumps?
- Types of flow in centrifugal pumps and their impact on efficiency
- Conclusions
- References
Introduction
Centrifugal pumps are essential equipment in various industries due to their ability to transport liquids efficiently. Their operating principle is based on the conversion of mechanical energy into hydraulic energy by means of the centrifugal force generated by a rotating impeller.
These pumps stand out for their versatile design and wide range of applications in sectors such as water supply, chemical industry, wastewater treatment and power generation.
Over the years, centrifugal pumps have evolved in terms of their construction, shaft arrangement, number of impellers and hydraulic characteristics. They can be classified into different types according to their suction, impeller shape and casing, thus allowing their adaptation to different operating conditions.
However, with technological advances and increasing demands for energy efficiency, sustainability and reliability, the industry has developed innovations in the design and materials of these pumps. The most outstanding distinctive features are presented below.
What is a centrifugal pump?
A centrifugal pump is a type of hydraulic pump that uses the principle of centrifugal force to move liquids. Its design consists of an impeller that rotates inside a casing, creating a flow of liquid. These pumps are widely used in a variety of industrial applications, from water supply to chemical processes.
Basic operating principles of a centrifugal pump
- Impeller: The heart of the centrifugal pump is the impeller, which is a rotating component with blades or vanes. When the impeller rotates, it provides energy to the liquid, accelerating it outward.
- Centrifugal force: As the impeller rotates, the liquid is thrown outward due to centrifugal force. This force pushes the liquid from the center of the impeller toward the periphery.
- Energy conversion: The impeller converts mechanical (rotational) energy into kinetic (liquid movement) energy. As the liquid leaves the impeller, its velocity increases.
- Volute or diffuser: After leaving the impeller, the liquid enters a volute or diffuser, which is a section of the pump designed to convert the kinetic energy of the liquid into pressure. In this phase, the velocity of the liquid decreases, while its pressure increases.
- Liquid outlet: Finally, the pressurized liquid is directed to the pump outlet, where it can be used for various applications, such as irrigation, heating or fluid transport in industrial systems.
Types of centrifugal pumps
Centrifugal volute pumps
These pumps have a design that includes a volute (spiral casing) that converts the kinetic energy of the liquid into pressure. The most outstanding distinctive features are presented below.
Distinguishing features
- Efficiency: High efficiency over a wide range of flow rates.
- Simplicity: Simple design for easy maintenance.
- Applications: Suitable for clean, clear liquids such as water and non-viscous chemicals.
Centrifugal diffuser pumps
Diffuser pumps use a series of fixed vanes (diffusers) that convert fluid velocity into pressure.
Distinguishing features
- High pressure: Capable of generating higher pressures than volute pumps.
- Efficiency: More efficient in applications where high pressure is required.
- Applications: Used in irrigation systems and industrial applications where high pressure liquids are handled.
Multistage centrifugal pumps
With multiple impellers (stages) in series, these pumps can significantly increase the liquid pressure.
Distinguishing features
- High pressure: Ideal for applications requiring very high pressures.
- Compact design: They take up less space due to their vertical or horizontal design.
- Applications: Commonly used in water supply systems, heating systems and in the petrochemical industry.
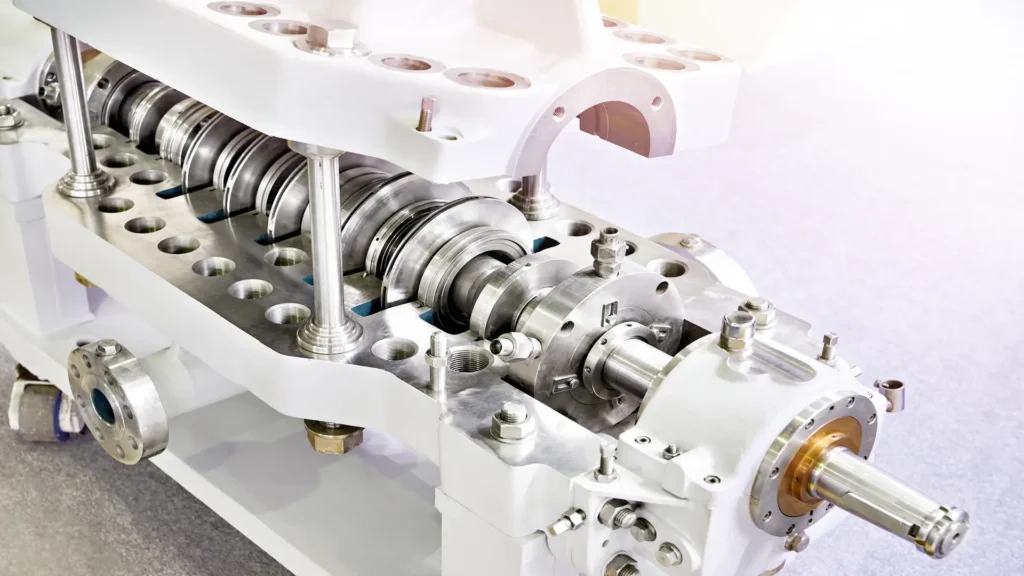
Open impeller centrifugal pumps
These pumps have an impeller with open blades, which allows solids and particles to pass through.
Distinguishing features
- Solids handling: Capable of pumping liquids with solids in suspension.
- Lower efficiency: Generally less efficient than closed impellers.
- Applications: Used in wastewater handling and in applications where sludge needs to be pumped.
Closed impeller centrifugal pumps
These pumps have an impeller with closed blades, which improves efficiency and performance.
Distinguishing features
- Efficiency: Higher efficiency compared to open impellers.
- Low maintenance: Less wear due to reduced fluid turbulence.
- Applications: Suitable for clean liquids and in general industrial applications.
Self-adhesive centrifugal pumps
Designed to prevent the liquid from draining completely from the impeller, these pumps are ideal for applications where cavitation is a problem.
Distinguishing features
- Self-adhesion: Ability to keep the liquid in the impeller, avoiding cavitation problems.
- Ease of operation: No manual priming required at start-up.
- Applications: Commonly used in heating and cooling systems.
Technological advances in centrifugal pump design
Technological advances have improved the efficiency, durability and versatility of centrifugal pumps. The following are some of the most significant developments in this field:
Computational modeling and simulation
- CFD (Computational Fluid Dynamics): Used to simulate fluid flow inside the pump, optimizing impeller and casing design to improve efficiency and reduce cavitation.
- Virtual prototypes: They allow testing in a digital environment before manufacturing, which reduces costs and development time.
Advanced materials
- Specialty alloys: More corrosion- and wear-resistant materials have been developed, such as stainless steel alloys and ceramic composites.
- Coatings: Protective coatings are applied that increase the durability of internal components, especially in applications with abrasive or corrosive liquids.
Optimized impeller designs
- High efficiency impellers: New designs allow better performance over a wider range of flow rates and pressures.
- Variable geometry impellers: They adapt their shape according to the operating conditions, thus improving efficiency in different situations.
Intelligent control technologies
- Sensors and monitoring: Integration of sensors that allow real-time monitoring of parameters such as pressure, temperature and flow.
- Advanced controllers: Control systems that automatically adjust pump operation to optimize efficiency and reduce energy consumption.
Improved coupling and transmission systems
- Non-contact couplings: Technologies such as magnetic couplings are used to eliminate friction and wear, increasing pump life.
- Frequency inverters: They allow adjusting the motor speed to optimize the performance according to the system demand.
Modular design
- Interchangeable components: Modular design allows easy replacement of parts, facilitating maintenance and repair.
- Configuration flexibility: Ability to easily adapt the pump to different applications and operational requirements.
Energy efficiency
- Regulatory compliance: Development of pumps that comply with energy efficiency regulations, contributing to sustainability and reduced operating costs.
- Energy recovery technology: Systems that allow the recovery of part of the energy from the fluid, improving the overall efficiency of the system.
Geometry impellers
Variable geometry impellers are innovative designs that allow the shape or angle of the impeller blades to be adjusted according to operating conditions, thus optimizing pump performance in different situations. Some specific examples of variable geometry impellers are presented below:
- Adjustable blade impellers
- Example: Pumps for marine applications.
- Description: In these pumps, the impeller blades can be angle-adjusted to optimize performance according to water depth and flow variation, thus improving system efficiency.
- 2-stage impellers with variable geometry
- Example: Centrifugal pumps in power plants.
- Description: These pumps use a two-stage design where the geometry of the vanes is adjusted to handle different loads and operating conditions, optimizing flow and pressure.
- Radial impeller pumps with movable vanes
- Example: Pumps for the oil and gas industry
- Description: Some designs allow the impeller blades to move or change position according to variations in fluid viscosity or inlet pressure, which improves efficiency in pumping viscous fluids.
- Flexible blade impellers
- Example: Pumps in wastewater treatment applications.
- Description: In these pumps, the vanes are flexible and can adapt to different flow conditions, allowing the pump to handle solids in suspension without compromising efficiency.
- Adjustable impeller systems for head pumps
- Example: High pressure pumps in irrigation systems.
- Description: These pumps allow the impeller geometry to be adjusted to optimize pressure and flow rate according to demand, which is crucial in applications where head varies.
The following image shows the cross section of an industrial pump.
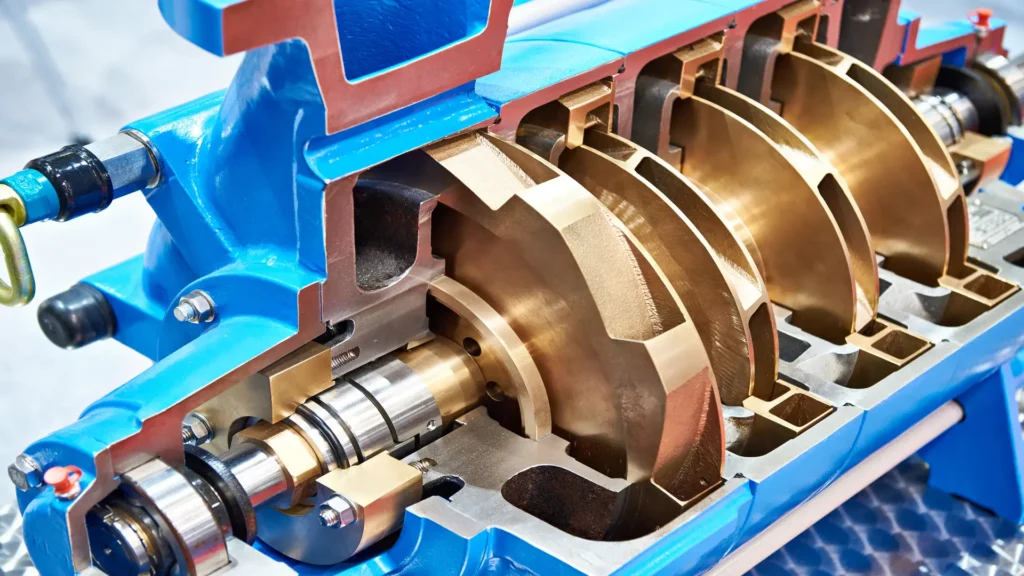
Examples of specific industrial applications for each type of pump
Centrifugal volute pumps
- Applications:
- Water supply systems: For pumping drinking water in treatment plants.
- Chemical processes: Handling of non-viscous liquids in the chemical industry.
Centrifugal diffuser pumps
- Applications:
- Agricultural irrigation systems: To increase water pressure in sprinkler irrigation systems.
- Power plants: In cooling systems where high pressures are required.
Multistage centrifugal pumps
- Applications:
- Municipal water supply systems: To lift water to great heights in distribution networks.
- Heating systems: In boilers requiring high pressures for return water.
Open impeller centrifugal pumps
- Applications:
- Wastewater treatment: For pumping sludge and liquids with suspended solids.
- Mining: In extraction processes where fluids with particles are handled.
Closed impeller centrifugal pumps
- Applications:
- Food industries: For pumping liquids such as juices or sauces without solids.
- HVAC systems: In heating, ventilation and air conditioning systems for water transport.
Self-adhesive centrifugal pumps
- Applications:
- Heating and cooling systems: To maintain liquid circulation without priming.
- Pharmaceutical industries: In processes where it is required to avoid the entry of air into the system.
These examples illustrate the versatility of centrifugal pumps and their importance in various industrial applications.
What is cavitation in pumps?
Cavitation is a phenomenon that occurs in pumps when the liquid pressure at the pump inlet drops below the vapor pressure of the liquid, causing vapor bubbles to form. When these bubbles move into areas of higher pressure within the pump, they collapse violently, generating shock waves that can cause significant damage to pump components.
Causes of cavitation
- Low suction pressure: If the pressure at the pump inlet is too low, it can cause cavitation.
- High flow rates: Operating the pump at flow rates above its capacity can lead to cavitation conditions.
- Elevated temperature: At higher temperatures, the vapor pressure of the liquid increases, which increases the risk of cavitation.
- Improper design: Improperly sized or selected pumps can be prone to cavitation.
Effects of cavitation
- Damage to components: Bubble collapse can erode the impeller and other internal components, reducing pump life.
- Noises and vibrations: Cavitation generates characteristic noises and vibrations that can affect pump operation and stability.
- Loss of efficiency: Cavitation can decrease pump efficiency, affecting overall pump performance.
Cavitation prevention
- Maintain proper suction pressure: Make sure that the pressure at the pump inlet is always above the vapor pressure of the liquid.
- Sizing the pump correctly: Choose a pump that fits the needs of the system and does not operate outside its specifications.
- Temperature control: Maintain the temperature of the liquid within a suitable range to prevent it from approaching its boiling point.
- Proper installation: Ensure that suction piping is properly installed, without unnecessary bends or restrictions.
Types of flow in centrifugal pumps and their impact on efficiency
Influence of flow type on cavitation
Cavitation is a phenomenon that occurs when the pressure on the suction side of the pump drops below the vapor pressure of the liquid, generating vapor bubbles that collapse violently inside the pump, causing damage to the impellers and reducing the efficiency of the system.
- Radial flow pumps are the most prone to cavitation due to the high pressure generated and the low suction pressure. If the available NPSH is lower than that required by the pump, the risk of cavitation increases significantly. The fluid is deflected 90° towards the periphery of the impeller.
- Axial flow pumps, working with lower pressures, have a lower risk of cavitation, although they can still be affected if they operate at inadequate speeds. The fluid moves parallel to the axis of rotation.
- Mixed flow pumps may exhibit cavitation if they are not properly designed to maintain adequate suction pressure, especially at high speed and flow conditions. The fluid outlet occurs at an intermediate angle between axial and radial.
To minimize cavitation in any type of flow, it is recommended:
- Ensure an available NPSH greater than that required by the pump.
- Correctly design suction piping to avoid excessive head losses.
- Use impellers made of materials resistant to erosion caused by cavitation.
- Implement variable speed control systems to operate in optimal ranges.
Conclusions
Centrifugal pumps are essential in industry because of their ability to move liquids efficiently. Each type of centrifugal pump has distinctive characteristics that make them suitable for specific applications.
The selection of the correct pump depends on factors such as the type of liquid, the required pressure and the ambient conditions. A clear understanding of these types and their characteristics is essential to optimize pumping systems and improve operational efficiency.
Cavitation is a critical problem in pump operation that can lead to significant damage and decreased operating efficiency. Understanding its causes, effects and prevention methods is essential to ensure optimum performance and prolong the life of pumps in industrial systems.
Technological advances are transforming the centrifugal pump industry, enabling greater efficiency, reliability and adaptability to new industrial applications. The trend towards digitalization, the use of advanced materials and the optimization of energy consumption are leading the way to a more sustainable future in fluid pumping.
References
- Computational Fluid Dynamics: Principles and Applications. J. Blazek
- Alstom Power Ltd., Baden-Daettwil, Switzerland
- https://www.simscale.com/blog/what-is-centrifugal-pump/
- https://www.csidesigns.com/blog/articles/what-is-pump-cavitation-and-how-to-prevent-it