Introduction
In the oil and gas sector, maintaining aging infrastructure poses an increasingly significant challenge. These installations, essential for global operations, must function under extreme conditions and comply with stricter regulations, which require appropriate workforce training for maintenance and operation teams.
Retrofit, defined as the process of reconditioning, upgrading, refurbishing, or adapting existing infrastructure, aims to extend the lifespan of critical assets, optimize their performance, and ensure sustainability. This approach updates installations to meet modern safety, energy efficiency, and sustainability standards without resorting to costly demolitions or new construction projects that could significantly impact the environment.
Unlike new construction, retrofitting maximizes the use of existing resources, making it a more economical and environmentally friendly solution. Additionally, it offers the flexibility to adapt innovative technologies and materials to address specific challenges for each facility.
This article explores how advancements in materials, including smart materials (embedded sensors, self-cleaning coatings, shape-memory materials, wear-resistant nanocomposites, advanced insulating panels with integrated sensors, and more), and technologies are transforming reconditioning projects in oil and gas. It examines everything from material selection to the integration of intelligent monitoring systems, demonstrating how these solutions ensure safety, energy efficiency, and operational sustainability.
Objectives of retrofit (reconditioning) in oil and gas
Reconditioning projects in the oil and gas industry aim to modernize critical infrastructure, maximizing performance, safety, and sustainability. This approach allows for optimizing existing assets, adapting them to current operational demands, and prolonging their lifespan.
Extending lifespan
Retrofitting reinforces pipelines, offshore platforms, and refineries exposed to extreme conditions such as high pressures, elevated temperatures, and corrosive agents. The incorporation of advanced materials, such as specialized alloys and polymer coatings, minimizes deterioration, ensuring functionality for additional decades.
Enhancing operational safety
Safety is paramount in the oil and gas sector. Reconditioning reduces risks of structural failures and leaks by implementing reinforcement technologies such as carbon fiber composites for tanks and advanced elastomers for seals. However, their effective implementation depends on adequate workforce training. These solutions strengthen critical components, mitigating potential accidents and ensuring operational integrity.
Optimizing energy efficiency
Efficient thermal insulation, advanced coatings, and smart materials are essential to reducing energy losses in processing and storage systems. Materials such as aerogel panels and reflective coatings not only improve thermal performance but also lower operating costs associated with energy consumption.
Regulatory compliance
In a highly regulated sector, reconditioning ensures compliance with environmental and safety standards such as API, OSHA, and international sustainability protocols. Solutions like low-VOC coatings and wear-resistant materials align with these requirements, protecting both the environment and workers.
Economic impact
Retrofit presents a more economical and sustainable alternative to building new assets. By modernizing existing infrastructure, it significantly reduces initial investment costs, downtime, and the environmental impact associated with demolitions and construction projects.
Together, these objectives demonstrate how retrofit or reconditioning projects in oil and gas improve the operation of critical assets while delivering economic and environmental value to this vital industry.
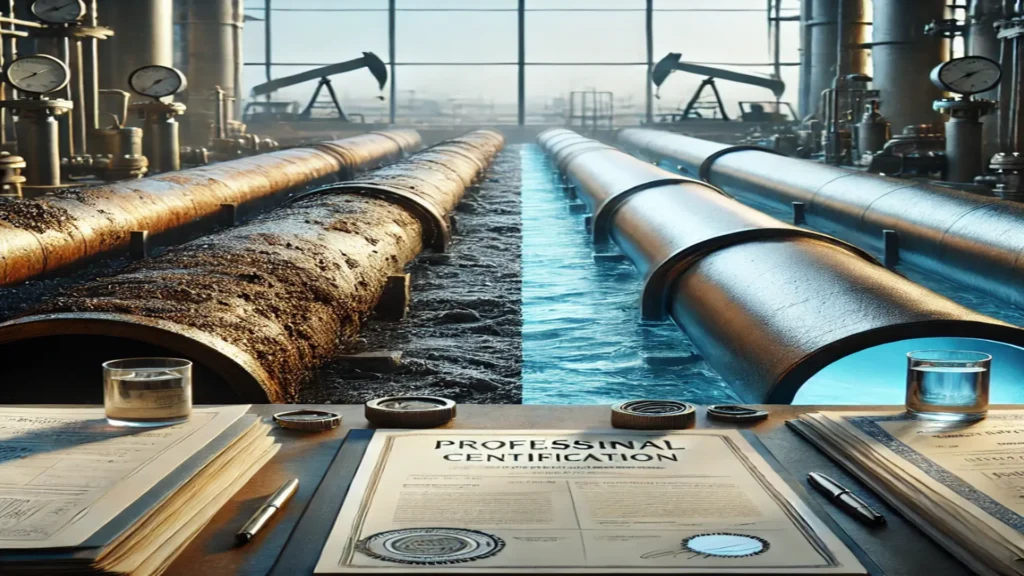
Essential materials for retrofit (reconditioning) in oil and gas
In the oil and gas industry, materials used in retrofit projects must meet rigorous technical requirements due to the extreme conditions in which they operate.
Specialized metal alloys
1. Inconel (Ni-Cr):
- Exceptional resistance to corrosion and high temperatures.
- Applications: Pipelines, valves, and turbines exposed to acidic gases.
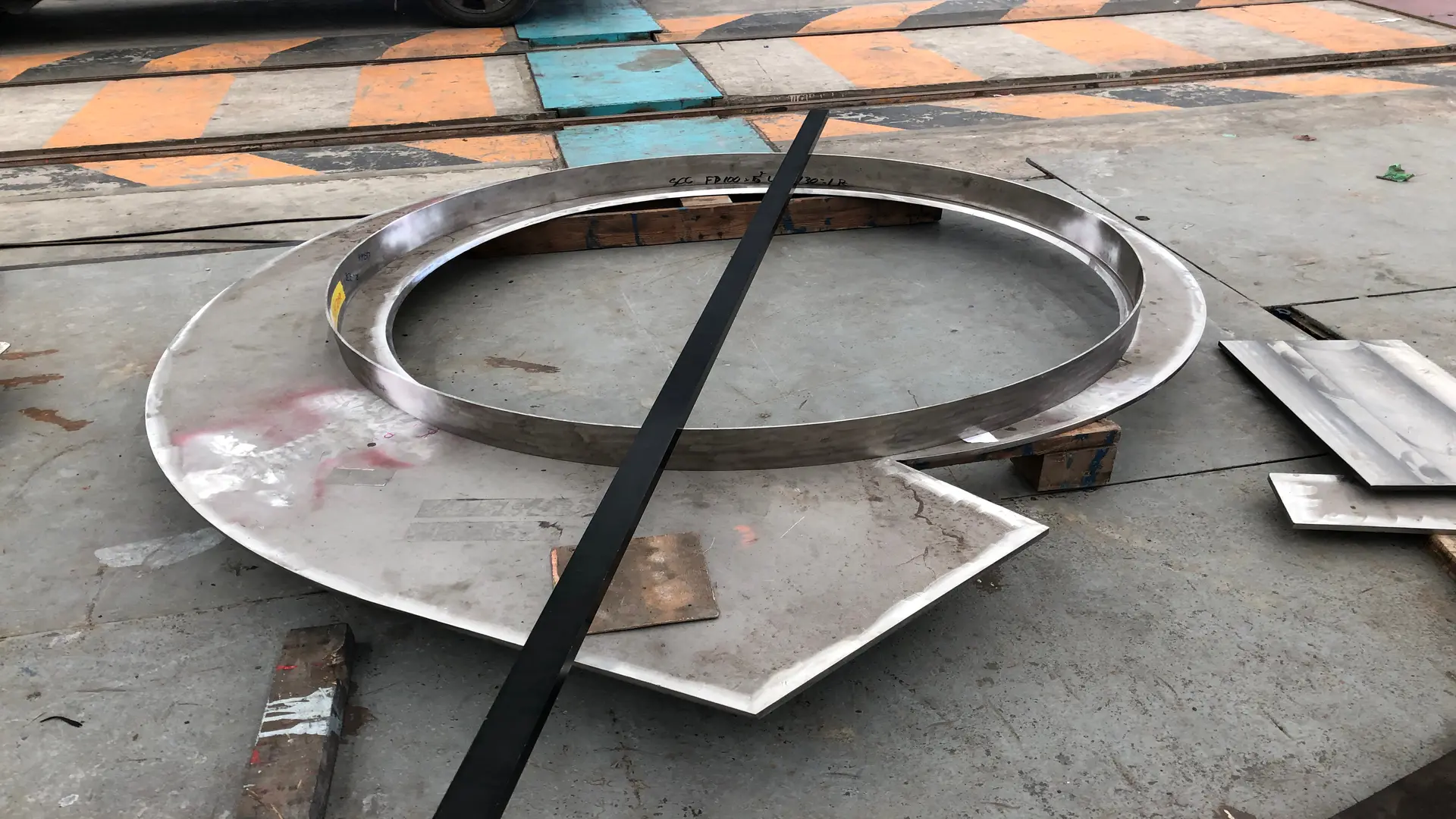
2. Duplex and superduplex stainless steel:
- High resistance to stress corrosion, ideal for chloride environments.
- Applications: Heat exchangers and subsea pipelines.
3. Titanium alloys:
- Lightweight and resistant to corrosion in acidic and marine environments.
- Applications: Natural gas production systems and subsea equipment.
Advanced non-metallic materials
- Structural reinforcements for tanks and pipelines, designed with nanotechnology to optimize resistance and reduce wear.
- Benefits: Lightweight, high-pressure resistance, and easy installation.
2. Polymer coatings:
- Protection against internal and external corrosion in tanks and ducts. Polymeric coatings offer significant benefits in complex operational environments but require skilled personnel through specialized workforce training programs.
The implementation of materials such as carbon fiber composites and polymer coatings offers significant benefits in complex operational environments but requires trained personnel through specialized workforce training programs.
Refractory and insulating materials
3. Refractory ceramics:
- Thermal resistance exceeding 1,500 °C, used in furnaces and reactors.
4. Aerogel panels:
- Efficient thermal insulation for cryogenic systems.
Critical applications and case studies
1. Offshore platforms:
- Structural reinforcement with high-performance concrete and carbon fiber.
- Use of metallic coatings to combat corrosion in marine environments.
2. Refineries:
- Installation of refractory ceramics in catalytic cracking units.
- Use of self-cleaning coatings developed with nanotechnology to reduce maintenance costs and maximize durability in marine environments.
3. Pipelines and ducts:
- Application of polymer coatings to protect against corrosive agents.
- Use of high-resistance elastomers in critical seals and joints.
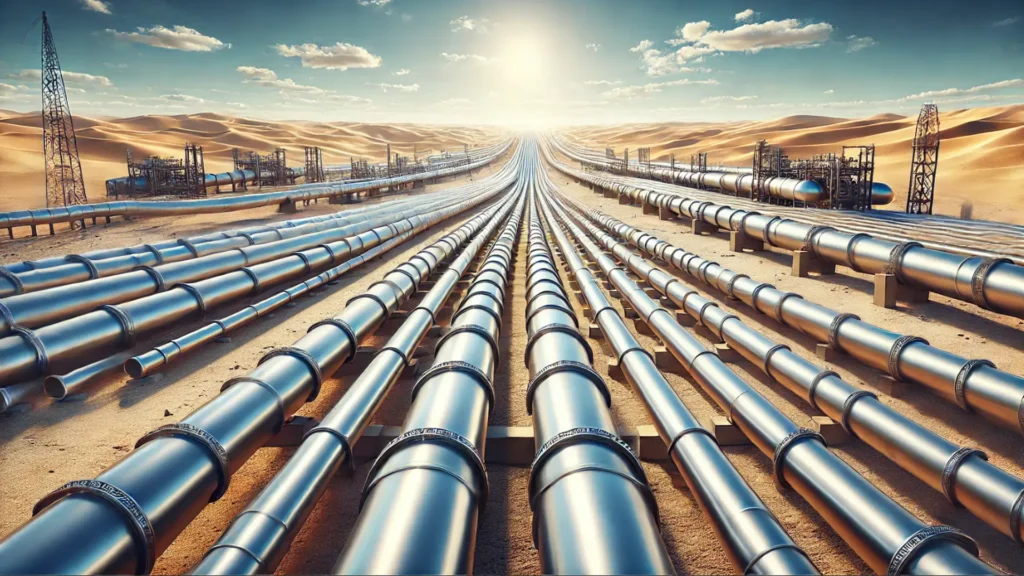
Case studies
The implementation of reconditioning projects in the oil and gas industry has proven to be an effective strategy for optimizing operations and ensuring the longevity of critical infrastructure. Below are two verifiable case studies highlighting the effectiveness of these solutions.
Refinery in the Gulf of Mexico: Extending service life with Ni-Cr coatings
Initial situation:
A refinery located in the Gulf of Mexico faced accelerated wear in high-temperature reactors used for catalytic cracking processes. Continuous exposure to temperatures exceeding 1,000°C, coupled with highly corrosive environments due to the presence of sulfides, resulted in high maintenance costs and a significant risk of failures.
Implemented solution:
Ni-Cr (nickel-chromium) coatings were applied using thermal spray technology. These coatings, known for their resistance to wear and corrosion, created a protective barrier on critical reactor surfaces, mitigating thermal and chemical degradation.
Results:
- Extended service life: The coatings enhanced the reactors’ resistance, extending their service life by 30%. This reduced the frequency of replacements, optimizing operating costs.
- Operational efficiency: The coatings improved thermal performance, ensuring uniform heat distribution during processes, which increased the refinery’s productivity.
Subsea platform in the North Sea: Reducing thermal losses with aerogel panels
Initial situation:
A subsea platform in the North Sea experienced significant thermal losses in its cryogenic systems, used for storing and transporting liquefied natural gas (LNG). The low required temperatures (approximately -162°C) and the region’s extreme climatic conditions increased energy consumption and associated costs.
Implemented solution:
Aerogel insulation panels were installed in the cryogenic systems. This material, renowned for its exceptional insulating capacity and lightweight properties, was applied to pipelines and storage tanks to minimize thermal transfer.
Results:
- Reduced thermal losses: The panels reduced heat loss by 20%, optimizing the system’s energy efficiency.
- Sustainability: Lower energy demand reduced the carbon footprint of operations, aligning with international sustainability goals.
- Durability: The aerogel provided more robust and long-lasting insulation, reducing the frequency of maintenance interventions.
Challenges and future trends
The retrofit sector in oil and gas faces a series of technical, economic, and operational challenges that limit its widespread implementation. However, emerging trends promise to shift the focus toward more efficient, sustainable, and advanced solutions.
Challenges
1. Material compatibility
Integrating modern materials, such as smart materials, with existing infrastructure presents significant technical complexities that require innovative solutions and solid workforce training for the execution teams:
- Differential wear: Advanced materials, such as specialized alloys or reinforced polymers, may have different thermal expansion coefficients compared to original components, leading to structural stress.
- Chemical interaction: In corrosive environments like offshore platforms or refineries, new materials must be compatible with the chemical conditions to avoid adverse reactions.
- Tailored solutions: Each project requires a detailed evaluation of existing conditions to select compatible materials that ensure integration without compromising structural integrity.
2. Initial costs
- Implementing advanced technologies and high-performance materials, such as aerogel panels or Ni-Cr coatings, represents a significant investment.
- Although these materials offer long-term returns in the form of reduced operating costs, energy efficiency, and durability, high initial costs may deter operators with limited budgets.
- The need for specialized equipment for coating applications or insulation panel installation also increases overall project costs.
3. Workforce training
- The lack of skilled personnel to implement advanced solutions is a critical challenge, highlighting the importance of investing in workforce training programs focused on emerging technologies.
- Technologies such as embedded sensors or nanotechnology-based coatings require specialized skills that are not always available in local teams.
- Intensive training and specific certifications increase costs and may delay projects.
Future trends
1. Nanotechnology
The application of nanotechnology in retrofitting materials is revolutionizing the sector, particularly in solutions like smart coatings and advanced sensors:
- Self-cleaning coatings: Incorporating hydrophobic or photocatalytic properties, these coatings repel dirt and minimize hydrocarbon buildup, improving maintenance in underwater or industrial environments.
- Wear resistance: Nanocomposites offer superior durability in extreme conditions, such as erosion and abrasion in transportation ducts.
If you want to learn about nanotechnology I invite you to watch the following video, courtesy of Aperture.

Nanotechnology: a new frontier.
2. Smart materials
Smart materials are transforming operational management through integrated technologies:
- Embedded sensors: Incorporated into pipes, valves, and tanks, often enhanced by nanotechnology to improve real-time monitoring accuracy, tracking key parameters such as pressure, temperature, and corrosion.
- Adaptive response: Materials with shape memory or self-adjusting properties improve safety and extend the lifespan of critical assets.
3. Sustainability strategies
Sustainability has become a central focus in the reconditioning industry:
- Recyclable materials: Advanced metallic alloys and polymers with recycling capabilities are being adopted to reduce environmental impact.
- Carbon-neutral: Manufacturers are developing production processes with reduced carbon footprints, aligning with global environmental regulations and corporate sustainability goals.
Conclusions
Retrofit or reconditioning in the oil and gas industry is an indispensable solution to extend the lifespan of critical infrastructure, optimize performance, and ensure regulatory compliance in an increasingly demanding environment.
Through advanced materials such as specialized metallic alloys, carbon fiber composites, and refractory ceramics, enhanced by nanotechnology for maximum effectiveness, it is possible to address the technical and environmental challenges associated with operations in extreme conditions.
With the integration of innovative technologies and sustainable practices, reconditioning not only modernizes existing assets but also promotes operational efficiency, supported by proper workforce training, and reinforces environmental responsibility.
The future of the sector relies on the ability of professionals to integrate innovative solutions, such as smart materials, and transform challenges into opportunities for a safer, more efficient, and sustainable industry.
References
Own source