Table of Contents
- Introduction
- What is welding safety equipment?
- Main safety equipment for welders
- Additional implements for increased safety
- Benefits of using safety equipment in welding
- Criteria to select the best safety equipment
- Common errors in the use of safety equipment
- The future of welder's safety equipment
- Conclusion
- References
Introduction
Welding is one of the most demanding activities in the industrial sector. Although welding represents a great contribution to productivity, it also involves certain risks for those who perform it with exposure to high temperatures, UV radiation and fume inhalation. In this context, adequate personal protective equipment is essential to ensure the safety and well-being of the welder. In this article, we will examine the main safety implements for welders, highlighting their importance and offering guidelines for proper selection.
What is welding safety equipment?
Welding safety equipment includes a set of tools and equipment designed to minimize occupational hazards. These are part of personal protective equipment (PPE) and range from specialized clothing and footwear to devices for eye, respiratory and hearing protection.
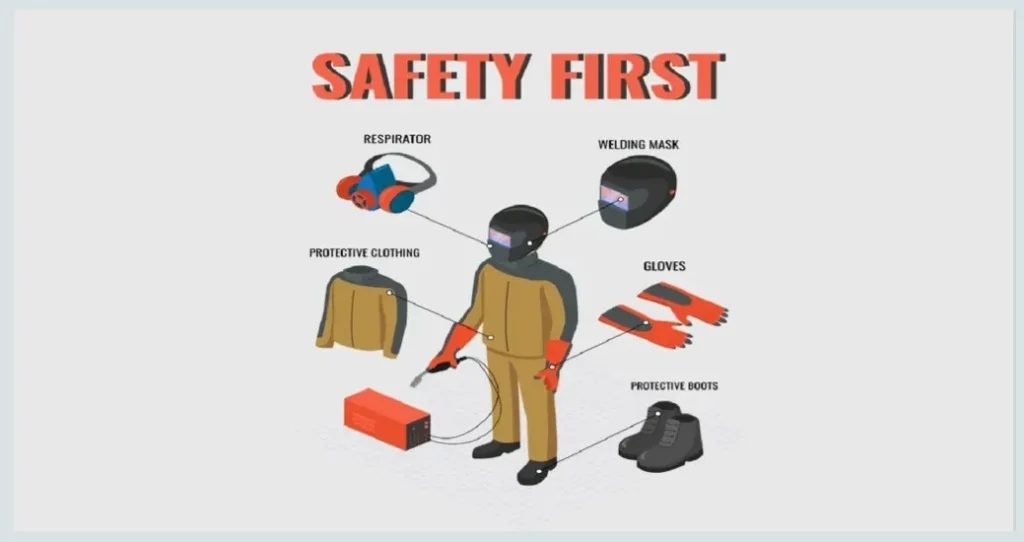
Main safety equipment for welders
The following is a description of the implements that every welder should consider:
Welding helmet
The welding helmet, mask or welding helmet is probably the most important element of the welder’s protective gear. Their function is to protect the eyes, face and neck from ultraviolet light, welding spatter, infrared light, and heat.
The types of welding helmets or masks are as follows:
Passive welding helmet
They use a fixed shade lens that does not change shade, providing constant protection against glare and sparks. Disadvantages include the following: Need to be lifted before each arc to align with the part, lenses break easily, impractical for continuous welds or in complex positions.
Welding helmet with automatic darkening
They include LCD display with sensors that detect the electric arc and automatically darken the lens according to the light level. One of its major advantages is that the welder does not need to remove the helmet for each arc and has customizable settings for different shade levels. The most notable disadvantages include: They are more expensive than passive ones and require batteries.
Solar-powered helmet with lenses
They use solar energy to power the auto-darkening lenses, when not in use the lens shuts off automatically, battery replacement is less frequent. However, they have disadvantages such as: They can present problems in low light areas and some models have a slightly slower response time.
Battery-powered helmet
They run on replaceable or rechargeable batteries to operate sensors and automatic lenses. They are more versatile even in low light conditions and fast and reliable response. They have the following disadvantages: Batteries need periodic maintenance and replacement, they are usually a bit heavier due to the battery compartment.
Welding helmet with fixed lenses
They have lenses with a fixed tint that does not adapt to different light intensities, have no electronic components, are reliable and durable, especially for uniform tasks and do-it-yourself workers who are inexperienced welders. Disadvantages include: limited to a specific range of welding applications, need a different lens for each welding process, less efficient to switch between welding processes with different light intensities.
Welding helmet with variable shade lenses
Equipped with adjustable lenses that allow the user to select the appropriate shade for the type of welding (MIG, TIG, MMA, etc.). They offer great flexibility for welders working with different processes, reducing eye fatigue by allowing precise adjustments. They have the following disadvantages: They are generally the most expensive. They require more maintenance than fixed shade models.
Underwater welding helmet
Specially designed to perform this activity. They allow the welder to breathe and basically it is a common diving helmet, but with a lens for automatic darkening welding. It presents the following disadvantages: They are expensive, of exclusive use, it has a much greater weight than the rest of the welding helmets.
Below are representative images of the helmets mentioned above:
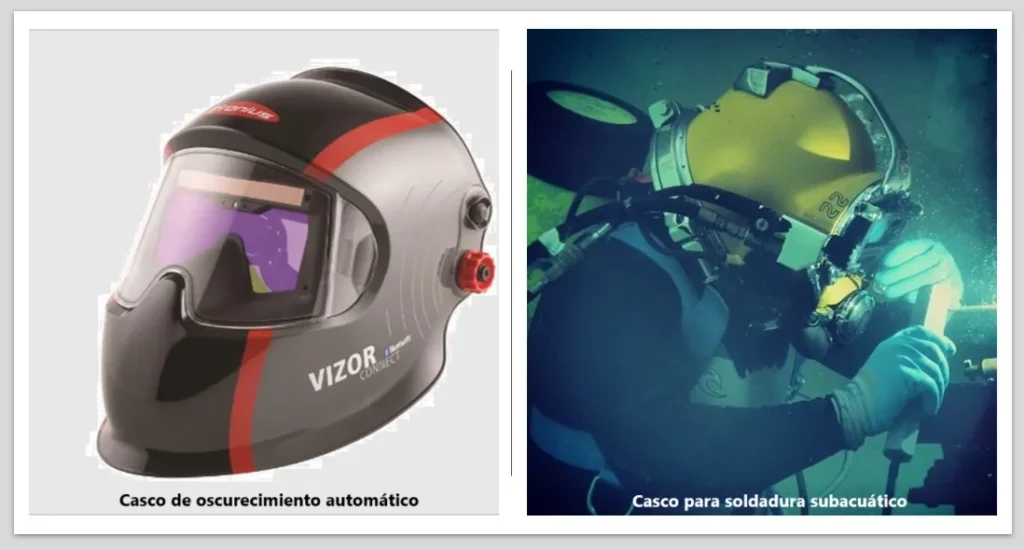
Safety masks
“Pancake” welding mask
It is lightweight and designed specifically for pipeline welding and outdoor work. Its structure is circular, with a flat front face where the welding lens is located, and a support made of wood or similar material to fit the face. It is extremely lightweight and comfortable for prolonged use in awkward positions.
Among the disadvantages, the following are the most important: Not practical for indoor welding, limited to specific applications such as pipe welding, does not provide full protection like standard helmets in industrial environments.
Leather welding mask
They are made entirely of heat and spark resistant leather, with a fixed or removable welding lens. They are flexible and cover the face easily. They are excellent for confined spaces where a rigid helmet would be uncomfortable. Disadvantages: Less impact and radiation protection compared to more advanced helmets, less durability, especially in harsh industrial environments, not the best choice for prolonged work.
Welding safety jackets
These are garments made of flame retardant materials, designed to protect the wearer from molten metal splashes, sparks and extreme heat. It not only protects against burns, but also prevents accidental fires when working in confined spaces or near flammable materials. Some of the most outstanding features include: Treated cotton or leather construction, high temperature and abrasion resistance, full arm and torso coverage.
Welding goggles
They are essential to protect the eyes against radiation, projected particles and dust. They must be used together with other implements such as masks or face shields for comprehensive protection. They have the following characteristics: Dark lenses with UV and infrared filters, impact resistance, adaptability to different types of welding (oxyacetylene, TIG, MIG).
Welding respirator
Protects the user from inhaling toxic fumes, gases and fine particles generated during the process. The most common are: Disposable respirators, reusable respirators with interchangeable filters, powered air supply systems.
Welding safety shoes
It is designed to protect the feet from heat, sparks and impact with heavy objects, to ensure adequate protection must have the following features: steel toe caps, heat-resistant and slip resistant soles, flame retardant construction for safety.
Hearing protection for welders
Protects against noise generated by welding processes, especially in enclosed workshops with noisy machinery, such as grinding, cutting tools, electric arc or plasma cutting, which can exceed 85 dB, causing hearing damage. Available options include: moldable foam earplugs, noise-reducing earmuffs, electronic systems that filter out harmful sounds but allow communication.
Additional implements for increased safety
In addition to the above equipment, welders should consider:
Heat-resistant gloves: To protect hands and wrists. Welder’s jacket: To protect torso and arms from heat and sparks, be made of flame-resistant material, such as leather or wool. Leather aprons: Provide additional coverage to torso and legs. Portable fire extinguishers: In case of emergency. Ventilation systems: Especially in enclosed spaces.
Benefits of using safety equipment in welding
Reduction of accidents: A properly equipped welder faces fewer occupational hazards. Regulatory compliance: Many industrial regulations require the use of certified PPE. Increased productivity: Feeling protected, the worker concentrates better on his tasks. Long-term care: Prevention of occupational diseases and chronic injuries.
Criteria to select the best safety equipment
Evaluate the type of welding: Each process (MIG, TIG, oxyacetylene) requires specific protection. Look for certifications: Make sure products meet international standards. Prioritize comfort: Comfortable and adjustable equipment increases the likelihood of continuous use. Regular maintenance: Inspect and replace damaged attachments to ensure efficiency.
Common errors in the use of safety equipment
Underestimating eye protection: Wearing only goggles or inadequate face shields. Not using flame-retardant clothing: Opting for synthetic clothing can increase the risk of burns. Ignoring respiratory protection: Especially when welding materials such as aluminum or stainless steel.
The future of welder’s safety equipment
With advances in technology, safety implements are evolving to be more effective and convenient. Examples include: Smart masks integrated with sensors and digital displays, innovative materials, nanofiber clothing for greater thermal resistance, advanced hearing protection through noise-canceling systems without compromising communication.
Conclusion
Welding safety is an investment that protects the health and life of the worker, as well as improving efficiency and regulatory compliance. From welding jackets to welding respirators, each piece of equipment plays an essential role in the overall protection of the welder. Proper equipment is not only a must, but a step toward a safer and more professional work environment.
References
- https://www.thefabricator.com/thefabricatorenespanol/article/arcwelding/introduccion-a-los-cascos-para-soldar-con-oscurecimiento-automatico
- https://mascaradesoldar.com/proceso-de-la-soldadura-subacuatica/