Table of Contents
- Introduction
- Cast iron and its welding challenges
- Types of cast iron
- Weldability comparison between cast iron types
- Welding methods for cast iron
- Comparison between methods
- Process for welding cast iron
- Cast iron welding standards
- Practical recommendations for welding cast iron
- Most common applications of cast iron welding
- Success stories and industrial applications
- Conclusion
- References
Introduction
Cast iron welding represents a remarkable technical challenge due to the properties of this material, characterized by its high brittleness and tendency to develop internal stresses under the application of heat. Despite these limitations, cast iron is still widely used in various industries due to its compressive strength, durability and machinability.
This article offers a comprehensive guide to how to weld cast iron, exploring the most effective methods, recommended electrode types and steps necessary to achieve high quality work, minimizing the risk of defects and maximizing joint durability.
Cast iron and its welding challenges
Cast iron is a material with high compressive strength, but also very brittle due to its high-carbon granular structure. These properties complicate welding processes, as the heat applied can cause cracks, internal stresses and joint defects.
It is characterized by the fact that it is not malleable or suitable for plastic deformation, which limits its versatility in certain manufacturing processes. However, it is machinable, relatively hard and offers good resistance to both corrosion and wear, characteristics that make it a valuable option in specific applications despite its limited weldability.
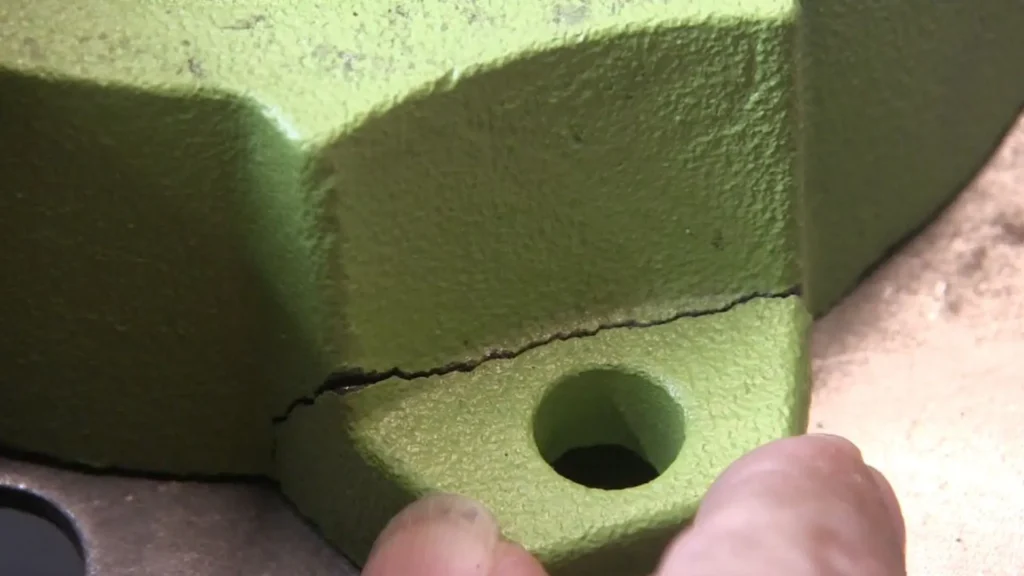
Characteristic cracks in cast iron.
Types of cast iron
There are four main types of cast iron, each with properties and characteristics that affect its weldability. Each type and its level of weldability is detailed below:
Gray cast iron
It is the most common, with a high carbon content (2.5%-4%) and graphite in the form of flakes. Its structure makes it resistant to compression but brittle under tensile stresses.
- Weldability: Its high brittleness and the risk of thermal cracking make it difficult to weld.
- Recommendations: Slow preheating and cooling to minimize stresses. Use pure nickel or nickel-ferrous electrodes for better adhesion and ductility.
Nodular (or ductile) cast iron
This type contains graphite in the form of nodules or spheres, which improves its ductility and strength compared to gray cast iron.
- Weldability: Less risk of cracking than gray iron, but still more susceptible to thermal stresses.
- Recommendations: Use moderate preheating (150-250 °C) and nickel-iron or bronze electrodes. It is ideal for structural repairs or critical parts.
White cast iron
In this type, carbon is present as cementite (iron carbide), forming a hard and brittle structure. It is extremely wear resistant, but very difficult to machine.
- Weldability: The hard structure and the absence of graphite make welding difficult, with a high probability of crack formation.
- Recommendations: It is considered practically non-weldable. Methods such as brazing or the use of bronze filler materials for minor repairs are used to join this material.
Malleable cast iron
This type is manufactured by heat treatment of white iron, transforming the carbide into graphite in nodular form (annealed carbon). It is more ductile and malleable than other types of cast iron.
- Weldability: Better weldability compared to white and gray iron, but still requires thermal precautions.
- Recommendations: Use arc welding methods (SMAW) and nickel-iron electrodes. It is common in automotive parts and piping.
Weldability comparison between cast iron types
Cast iron type | Ductility | Welding ease | Recommended electrode | Alternative method |
Gray | Low | Moderate | Pure Nickel or Nickel-iron | Controlled preheating and cooling |
Nodular | Moderate | Good | Nickel – iron or bronze | Brazing |
White | Very low | Very difficult | Not applicable | Brazing or repair methods |
Moldable | High | Good | Nickel-iron | Cold repair |
Welding methods for cast iron
There are several effective methods for welding cast iron, each with advantages and limitations. The following are the most commonly used:
Shielded metal arc welding (SMAW)
It is widely used thanks to its adaptability and efficiency in the repair of cast iron parts.
Recommended electrodes
- Pure Nickel Electrode (ENi-CI): Excellent ductility, minimizes cracks. Ideal for cold repairs and subsequent machining.
- Nickel-Iron (ENiFe-CI): Increased mechanical strength and compatibility with stressed structures.
- Bronze electrodes: Useful in less critical parts, they provide high resistance to corrosion.
TIG Welding (Gas Tungsten Arc Welding)
It allows precise arc control and is ideal for delicate work in cast iron.
Recommended consumables
- Pure nickel rods (AWS A5.15 ERNi-CI): Ensure a ductile joint and minimize internal stresses.
- Brass or bronze rods: Suitable for minor or decorative repairs.
MIG Welding (Gas Metal Arc Welding)
It is a faster option for joining cast iron parts, especially in large repairs.
Recommended electrodes
- Solid nickel wire (AWS A5.15 ERNi-CI): Ideal for structural applications.
- Bronze wires (CuSn6 or CuSn8): Provide good corrosion resistance and smooth welds.
Oxyacetylene welding
This traditional welding method is useful for repairing old parts or making bimetallic soft welds.
Recommended consumables
- Nickel rods: Provide good adhesion and ductility in the joints.
- Bronze rods with built-in flux: Ideal for minor repairs and decorative joints.
Brazing
It is an unconventional but effective technique for joining cast iron parts.
Recommended consumables
- Bronze or brass alloys: They are used with flux to improve fluidity and adhere to the base metal surface (wetting).
- Silver rods (AWS A5.8 BAg): Suitable for high quality, low structural load joints.
Comparison between methods
Method | Accuracy | Cost | Cracking risks | Major repairs | Fine repairs |
SMAW | Medium | Moderate | Moderate | Yes | Partially |
TIG | High | Low | Low | No | Yes |
MIG | Medium | Moderate | Moderate | Yes | No |
Oxyacetylene | Low | Moderate | Moderate | No | Yes |
Brazing | Medium | Low | Low | No | Yes |
Process for welding cast iron
Before starting, a good surface preparation is performed and then continue with the process, as indicated below:
- Surface cleaning: Remove rust, grease, paint or any other contaminant.
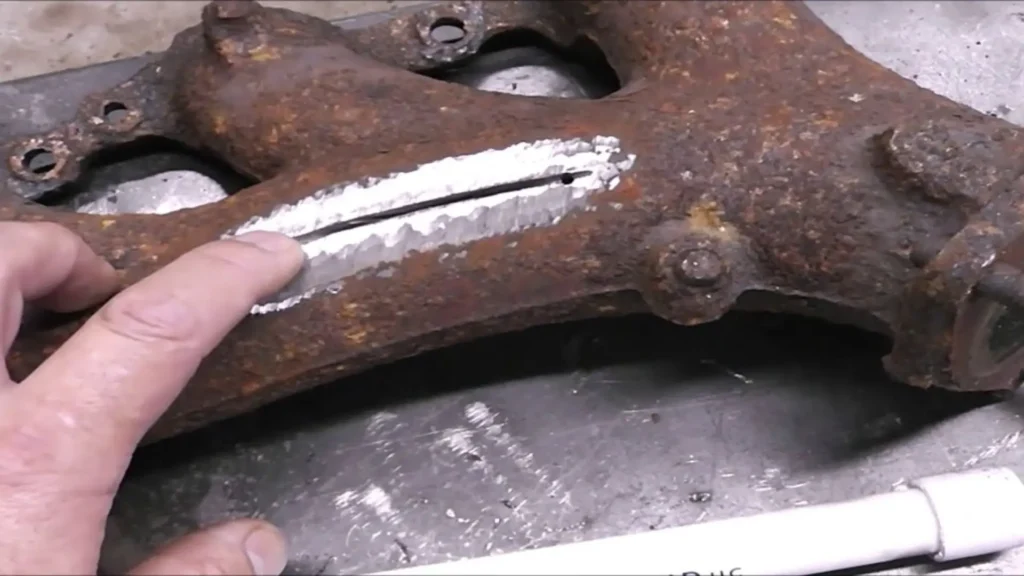
- Crack inspection: Identify structural defects and eliminate cracks with mechanical tools, before welding, ensuring that the roughing is in a U-shape without sharp areas.
- Method and electrode choice: This depends on the application and will be selected from the available options.
- Preheating: To reduce thermal shock, the material should be preheated slowly and uniformly between 260 °C and 648°C, depending on the thickness and welding method.
- Weld without preheating: The size of the workpiece may require that the weld be made without preheating. In this case, the surface temperature should be approximately 38 °C and short weld beads of approximately 2.50 cm should be made.
- Peening: In peening, the surface of the weld, while still hot, is struck with a ball peen hammer, thus allowing the surface layer to expand, forming beneficial compressive residual stress in those areas.
- Slow cooling: Cooling is significant in the process of soldering cast iron. The slower the cooling, the better the results. When the weld is finished, it is advisable to wrap it with thermal insulation blankets to prolong the cooling as long as possible, which is a good practice.
Cast iron welding standards
AWS D11.2/D11.2M:2023 – Guide for Welding Iron Castings
Provides guidelines for welding different types of cast iron, such as gray, nodular and white iron. It helps to select the proper procedures, consumables and preheating and cooling techniques, reducing the risk of cracking.
ISO 1071 – Welding Consumables for Cast Iron
Specifies requirements for filler materials used in cast iron welding, such as electrodes and rods. Ensures that the consumables selected are compatible with the type of cast iron and the application.
Practical recommendations for welding cast iron
- Pre-testing: Perform tests on similar materials before welding the final part.
- Controlled cooling: Cool slowly to avoid internal stresses.
- Thin layers: Apply solder in multiple thin layers instead of thick passes to reduce the risk of cracking.
Most common applications of cast iron welding
- Automotive industry: Repair of engine blocks, cylinder heads and transmission casings.
- Industrial machinery: Recovery of parts such as gears, shafts and machinery bases.
- Infrastructure: Restoration of historic architectural and structural components.
- Power generation: Repair of turbine casings, valves and thermal plant equipment.
- Mining industry: Repair of pump casings and heavy equipment components.
- Artistic and decorative ironwork: Restoration of railings, sculptures and other design elements in cast iron.
Success stories and industrial applications
In the automotive industry
In engine repair shops, cracked cast iron engine blocks are restored using nickel electrode welding. This process allows parts to be recovered that would otherwise be discarded, saving significant costs.
Historical pieces
In the restoration of cast iron structures and decorative elements, such as lampposts, railings or old bridges, oxyacetylene welding is used to maintain the original aesthetics.
In the mining industry
In mines, cast iron gears and pump casings have been welded using the SMAW method with ENiFe-CI electrodes. This has reduced downtime by avoiding the need to fabricate new components.
Oil and gas industry
Cast iron valves and pump casings used in refineries have been repaired with MIG welding, avoiding the replacement of critical equipment.
Conclusion
Mastering cast iron welding requires understanding its properties, choosing the right method and applying best practices. Techniques such as the use of nickel electrodes or brazing must be adapted to the specific challenges of each project. Complying with welding standards not only ensures optimal results, but also durability and quality in repairs or construction.
References
- https://www.weldingtipsandtricks.com/tig-welding-cast-iron-vise.html
- https://xpressmobilewelding.com/metal-fabrication/how-to-fix-cast-iron-without-welding/