The Internet of Things (IoT) is based on the interconnection of devices equipped with sensors, software and technologies that enable communication and data exchange. In the field of smart industrial instrumentation, Industrial IoT (IIoT) is transforming process monitoring and control through advanced sensor networks, real-time analytics and smart automation.
This transformation, often referred to as “industrial process intelligence” encompasses a wide range of technologies that improve operational visibility, predictive maintenance and overall system efficiency. Effective quality management involves monitoring a wide range of process and machine parameters that influence product quality.
In the past, quality control in manufacturing was a manual process that was often prone to errors. With the advent of the IoT, manufacturers can now track quality parameters such as moisture, temperature, pressure and particulates with greater accuracy.
IoT sensors help collect data that can determine which products meet quality standards and should be inspected more closely. This is especially important for industrial instrumentation manufacturers that comply with quality standards such as ISO and GMP.
Industrial instrumentation in industrial process control
Industrial instrumentation is fundamental in the automation and control of processes in sectors such as manufacturing, energy and petrochemicals. It consists of a set of devices, such as sensors, transmitters and controllers, that allow monitoring and adjustment of critical variables such as pressure, temperature, level and flow.
An instrumentation system is composed of a set of interconnected instruments that work together to ensure accurate and consistent measurements. These systems include sensors, transducers, physical connections and automation software that ensure repeatability and reliability of measurements.
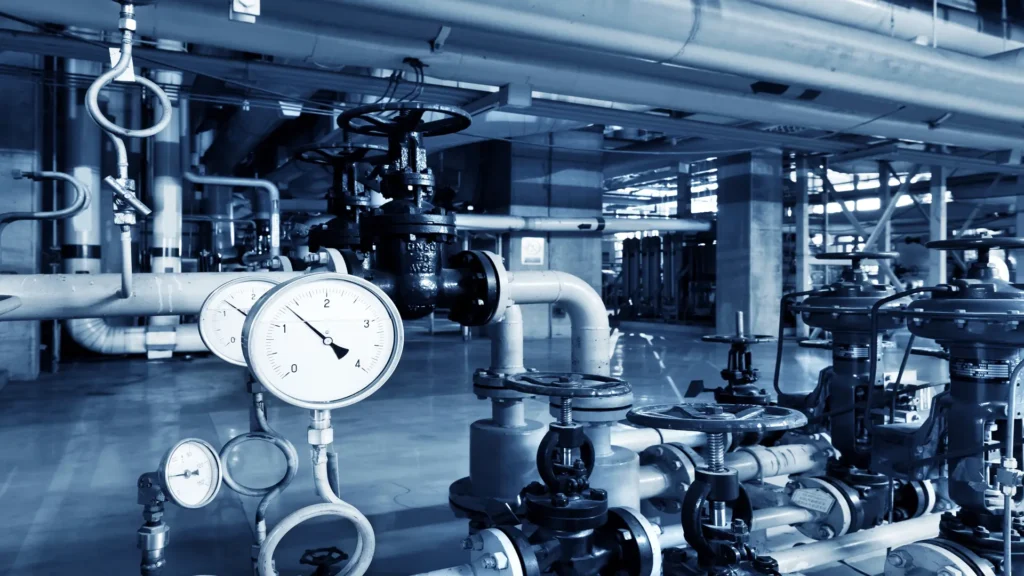
Industrial instrumentation system.
In industrial plants, the control and measurement of variables are fundamental to guarantee the efficiency, safety and quality of the processes. Among the main physical variables monitored are flow rate (mass and volumetric), pressure, temperature, level (of liquids and solids), velocity, weight, humidity and dew point.
As for chemical variables, pH, electrical conductivity and redox potential are essential to maintain chemical equilibrium and avoid problems such as corrosion or contamination. Precise instrumentation of these variables allows effective control, optimizing resources and ensuring reliable operations.
Efficiency in production processes depends on these instruments because they encompass the use of elements designed to measure, convert, transmit and control key variables, ensure quality and safety in the operation, and optimize the resources used, reducing costs and improving sustainability.
The sensor is the essential component of this system, responsible for sensing a physical variable, such as temperature or pressure, and transforming it into an interpretable signal. Transducers, in turn, convert these signals into useful forms for recording or control, such as electrical or mechanical signals.
Measurement, which consists of assigning a specific value to a physical variable, is the basis for making informed decisions in real time. Industrial instrumentation systems allow these measurements to be made with high precision, thus improving the regulation, supervision and safety of production processes.
Key factors of intelligent industrial instrumentation
Smart instrumentation in Industry 4.0 leverages advanced data analytics and connectivity to transform process control and monitoring. This paradigm shift encompasses five key factors:
Smart instruments transcend traditional measurement functions by generating ancillary data, including diagnostic information
These devices use advanced communication protocols such as Ethernet/IP or OPC-UA, allowing direct integration into site networks, bypassing conventional control system intermediaries.
This architecture allows control systems to focus on core functions, while maintenance, calibration and commissioning data are accessible at higher hierarchical levels such as SCADA.
Advanced diagnostic capabilities
Modern smart devices, such as flowmeters, employ sophisticated diagnostics in both sensors and transmitters to detect physical anomalies or calibration deviations. Analytical sensors, including pH and conductivity probes, have evolved to primarily digital outputs with advanced protocol support.
These digital sensors provide critical metrics such as duty cycles, calibration drift and overall sensor health, facilitating data-driven decisions for calibration and component replacement.
Benefits of enhanced protocol
Ethernet-connected instruments offer superior data throughput compared to traditional 4-20 mA signals, with reduced wiring complexity.
For example, a magnetic flowmeter can now transmit temperature, conductivity and flow rate data over a single Ethernet connection, eliminating the need for multiple analog outputs and potentially reducing both costs and space requirements.
Ubiquitous access to data in connected facilities
In a fully connected Industry 4.0 facility, instrumentation data is easily accessible via mobile interfaces, enabling on-demand process monitoring and equipment localization.
Direct connection of instruments to SCADA systems or historical systems via open protocols facilitates proactive maintenance scheduling and work order generation, mitigating unplanned downtime and rendering traditional PLC-based calibration alarms obsolete.
Data utilization and analysis
The voluminous data generated by smart instruments require sophisticated data management strategies. Customized dashboards for data cleansing, organization and visualization provide valuable information for decision-making processes.
By leveraging this data, manufacturers can implement predictive maintenance algorithms, optimize production processes and improve overall operational efficiency.
Proper planning of control system integration
Control systems integration is not a functional layer that sits on top of a facility design; it is the design of the facility, or a component of it. Your control systems integration team must work together with process and facility engineers to align initial design decisions with the overall plant controls philosophy.
Input from individuals representing operations, maintenance, quality and other teams throughout the plant is key. Incorporating this multidisciplinary perspective into the initial process design and planning activities will lay the foundation for a resilient and meaningful control system integration strategy.
What is Industrial IoT (IoT)?
IoT technologies exist all around us: all those interconnected devices we use, such as wearable technologies and virtual assistants, are made possible by IoT.
Industrial IoT, then, is taking the digital interconnectivity we have come to depend on and applying it to massive manufacturing operations, where the risks are greater, but the rewards are greater. As manufacturing moves from the automated functions and connected systems of Industry 4.0 to the enhanced personalization and cognitive computing of Industry 5.0, IIoT can be thought of as a more human-centric approach to manufacturing.
IoT sensors and wireless networks connectivity and real-time data
Wireless Sensor Networks (WSNs) play an essential role in the Internet of Things (IoT) ecosystem. These networks enable seamless connectivity and real-time data collection from sensors distributed in different locations. By taking advantage of WSNs, IoT technology is making significant advances in efficiency, monitoring and automation.
A wireless sensor network is a system composed of small, low-cost, energy-efficient sensor nodes that communicate with each other wirelessly over short distances. Each node is equipped with transducers, microcomputers, transceivers and a power source, allowing them to measure physical or chemical variables in the environment and transmit this data to a base station or gateway.
This approach not only enhances real-time monitoring capabilities, but also facilitates advanced data analysis, opening up new possibilities in sectors such as industry, agriculture, smart cities and healthcare. In an increasingly connected world, WSNs are the backbone that enables IoT sensors to transform the way we interact with our environment.
Below is a tutorial, courtesy of Sentec®, introducing the different types of IoT sensors, temperature, pressure and level sensors. In this video you will understand the capabilities and functionalities of the different IoT sensors.
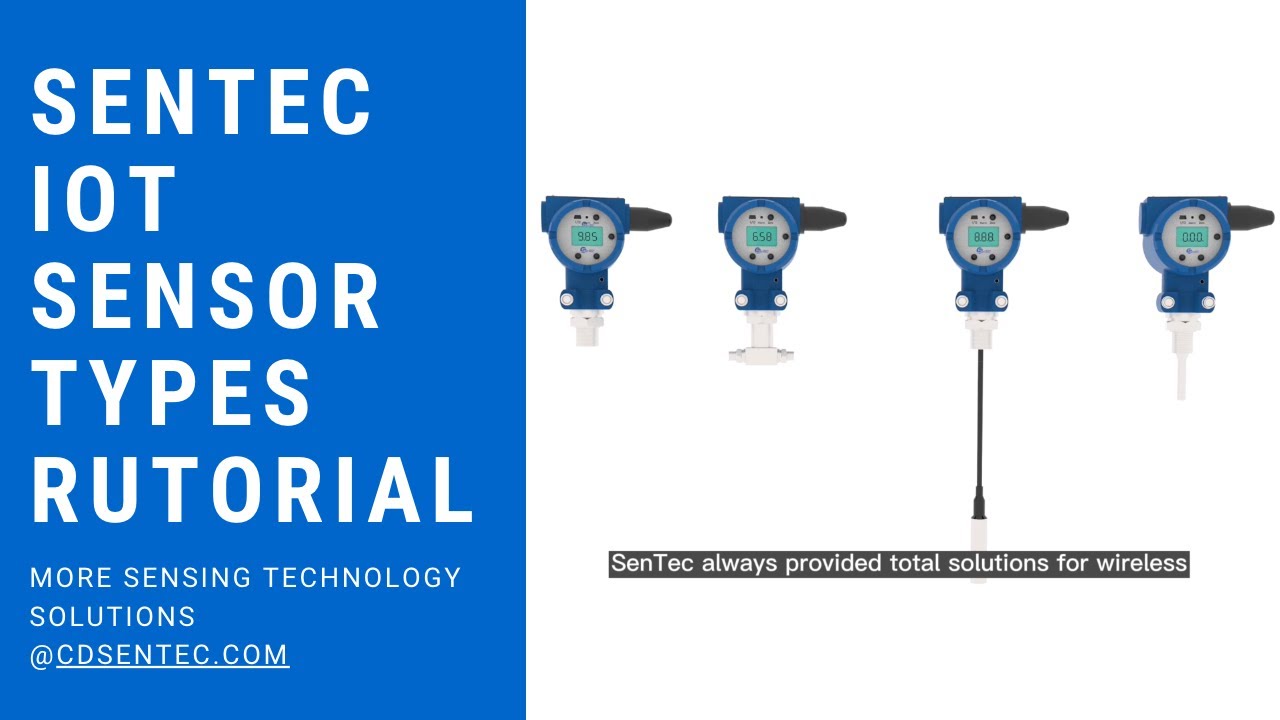
Types and applications of IoT sensors.
The digital transformation in manufacturing, called Smart Manufacturing, enables operators to optimize decision making by analyzing massive data generated by the Industrial Internet of Things (IIoT). This strategy requires a comprehensive investment in operational digitization, founded on four critical technology components:
- Smart sensor infrastructure: Devices and machines enabled with digital monitoring systems that capture, record and transmit operational data in real time. Smart sensor technology refers to sensors that have embedded microprocessors to process the data they collect.
- Cloud computing architecture: Scalable computing platforms with distributed storage and processing capabilities that ensure the integrity and availability of industrial data.
- Analytical smart systems: Advanced data processing tools that transform raw information into strategic insights, enabling predictive optimization of manufacturing processes.
- Specialized human capital: Qualified technical resources, trained in the interpretation and application of data analysis, capable of implementing operational improvements and maintaining the efficiency of the technological ecosystem.
IoT adoption in manufacturing
Integrated industrial IoT is understood to be an essential part of the future of manufacturing, driving revenue-generating strategies such as data monetization and new business models as both equipment and service.
Predictive maintenance in manufacturing
Nothing affects a manufacturing operation more negatively than machine downtime. Experts estimate that the average manufacturer experiences 800 hours of equipment downtime per year, which adds up to a cost of $50 billion per year in unplanned expenses for the entire industry.
When maintenance in the manufacturing world is reactive instead of proactive, manufacturers get stuck trying to identify what the problem is, how it can be fixed and how much it will cost. With predictive maintenance powered by industrial IoT solutions, all of those problems are relieved.
Dimensions of IIoT impact
Around production:
- Real-time predictive monitoring of manufacturing conditions.
- Enabling data-driven decision making for preventive maintenance.
- Occupational safety monitoring through geolocation and telemetry systems.
- Productive capacity analysis with dynamic scenario modeling.
Field operations:
- Fleet telemetry for comprehensive performance evaluation.
- Implementation of predictive maintenance through wear pattern analysis.
- Virtual supervision of equipment with geolocation and remote diagnostics.
- Reduction of response times through proactive service management.
Supply chain management:
- Integral monitoring of logistic flows with distributed sensors.
- Control of environmental conditions during transportation and storage.
- Early detection of potential disruptions through predictive analytics.
- End-to-end traceability of inventory movements.
Coordination of distributed operations:
- Centralized outsourced process management platform.
- Digital audit of compliance with standards.
- Standardization of quality and performance protocols.
The implementation of IIoT represents a systemic transformation that transcends mere digitization, becoming an organizational optimization strategy based on data intelligence.
IoT components
An IoT solution architecture comprises several critical components:
Connected devices
These encompass a variety of interconnected elements, including:
- Sensors and actuators for data acquisition and control.
- Embedded systems and microcontrollers (MCUs) for local processing.
- Communication modules for data transmission.
Key considerations include:
- Sensor types and specifications (e.g., temperature, pressure, flow).
- Data collection parameters and sampling rates.
- Edge computing capabilities for local execution of AI/ML algorithms.
Connectivity infrastructure
Data transmission is facilitated through:
- Wired protocols (e.g. Ethernet, RS-485).
- Wireless technologies (e.g., Wi-Fi, Bluetooth, LPWAN, 5G).
Critical factors:
- Network topology and architecture.
- Quality of Service (QoS) parameters.
- Real-time data transmission capabilities.
- Security protocols (e.g., TLS, DTLS).
Data processing and analysis platform
Scalable software infrastructure for data management and analysis:
- Cloud or edge computing platforms.
- Big Data storage solutions (e.g., data lakes, time series databases).
- Analytics engines to obtain descriptive, predictive and prescriptive information.
- Machine learning pipelines for model training and implementation.
This architecture ensures a robust, scalable and smart IoT ecosystem capable of delivering actionable information and driving operational efficiencies.
To ensure enterprise-wide acceptance, there must be an understanding of the value that industrial IoT provides. Too often, companies get bogged down in solving technical problems and focus exclusively on investing in hardware (sensors, gateways, etc.), connectivity, cloud storage, administrative labor, technical support and more.
Conclusions
Smart instrumentation, driven by the Industrial Internet of Things (IIoT), has transformed the way industries manage their operations. Thanks to advanced sensors and real-time data analysis, it is possible to achieve continuous process optimization. In addition, predictive maintenance significantly reduces downtime by anticipating failures and enabling more efficient planning of interventions.
The integration of technologies such as advanced sensors, cloud analytics and edge computing enables the creation of smart factories. These factories not only automate repetitive tasks, but also use autonomous systems to continuously improve processes and dynamically adapt to changing market demands. This results in a more agile, resilient and efficient industrial ecosystem aligned with the challenges of modern manufacturing.
The adoption of smart industrial instrumentation is revolutionizing the control and monitoring of production processes, turning them into highly sophisticated, data-driven disciplines. With the integration of technologies such as cloud computing and predictive analytics, industries are achieving unprecedented levels of operational intelligence, improving decision making, increasing productivity and ensuring more precise quality control in their operations.
Industrial instrumentation is a vital tool for the efficient transformation of physical data into actionable information, ensuring the stability and competitiveness of industrial operations. In a competitive and sustainability-oriented environment, industrial instrumentation not only improves control, but also drives innovation and adaptation to emerging technologies, consolidating itself as an essential resource for the future of industrial processes.
References
- https://netilion.endress.com/blog/6-examples-industrial-iot-monitoring-solutions/
- https://www.globalxetfs.com/connectivity-internet-of-things-digital-infrastructure/
- https://1nce.com/en-us/resources/news/blog/iot-hardware-and-ecosystem
- https://www.techtarget.com/iotagenda/tip/A-comprehensive-view-of-the-4-IoT-architecture-layers