Table of Contents
- Introduction
- What is CWI certification?
- Why is CWI certification important?
- What does it mean to be a CWI?
- How to obtain CWI certification?
- Benefits of CWI certification for professionals
- Benefits for companies
- Welding standards: The safety guide
- The future of CWI certification
- What does this mean for CWI inspectors?
- Conclusions
- References
Introduction
The CWI (Certified Welding Inspector) certification granted by the American Welding Society is the seal of guarantee that ensures that each welded joint has been made under the strictest standards. In the industrial and energy world, where quality and safety in welding is non-negotiable, this certification becomes an essential pillar. The bridges we cross, the power plants that drive our cities, and the oil rigs that supply essential resources depend on safe and durable welds.
This article focuses on CWI certification, why it is important to the industry, how it is obtained, and what the advantages are for both professionals and organizations that benefit from this certification. We will also highlight how welding standards define the quality and safety of the most critical industrial processes.
What is CWI certification?
An internationally recognized accreditation, awarded by the American Welding Society (AWS), that demonstrates that an individual possesses the knowledge and skills necessary to perform welding inspections competently and reliably.
The AWS Certified Welding Inspector (CWI) credential is a leading recognition in the welding industry, validating a thorough knowledge of the field’s processes and standards. This certification boosts careers by offering greater recognition, better salary opportunities, and brings value to companies by ensuring that their projects meet the highest quality standards.
To accommodate different needs, AWS offers flexible training options, such as customized seminars tailored to each organization’s requirements, as well as classroom and online courses. This makes it easy for professionals to effectively prepare for and obtain certification.
Why is CWI certification important?
- International recognition: The certification is highly valued in the industry worldwide.
- Quality assurance: Companies that hire CWI inspectors ensure a high level of quality in their welding processes. Certified inspectors are responsible for reviewing every aspect of the welding job, from preparation to final inspection.
- Professional development: Obtaining certification opens doors to better job opportunities and further professional development.
- Responsibility: A CWI inspector assumes a great responsibility in ensuring the integrity and safety of welded structures. He ensures that all procedures comply with the specifications established by the American Welding Society.
What does it mean to be a CWI?
A CWI inspector must:
- To have a thorough knowledge of welding codes and standards: AWS, ASME, API, among others.
- Master the welding processes: TIG, MIG, SMAW, etc.
- Perform non-destructive testing: X-ray, ultrasound, liquid penetrant, magnetic particles.
- Interpret blueprints and technical specifications.
- Evaluate the quality of welds.
- Prepare detailed inspection reports.
How to obtain CWI certification?
Generally required:
- Work experience: Depending on the candidate’s educational level, two to five years of welding, fabrication or inspection experience is required.
- Education: A minimum level of education, often a technical or college degree related to engineering or welding.
- CWI Certification Examination: The CWI test is known for its rigorousness and consists of three parts: theory, practical and regulatory.
- Process for becoming a CWI inspector
The path to becoming a Certified Welding Inspector involves several stages of preparation, training and evaluation. Below, we break down this process to give you a better understanding of what is involved.
Training and preparation
The Certified Welding Inspector (CWI) Certification is a prestigious accreditation in the welding industry. To earn it, candidates must pass three exams, which test a variety of knowledge and skill areas
A minimum score of 72% on each part of the exam is required to earn the CWI credential. Consolidated results for Parts 1, 2 and 3 are emailed to candidates approximately two weeks after completing Parts 1 and 3.
Below is the following video courtesy of Weld.com, on how to prepare to take the CWI exam. Courtesy of: Weld.com.
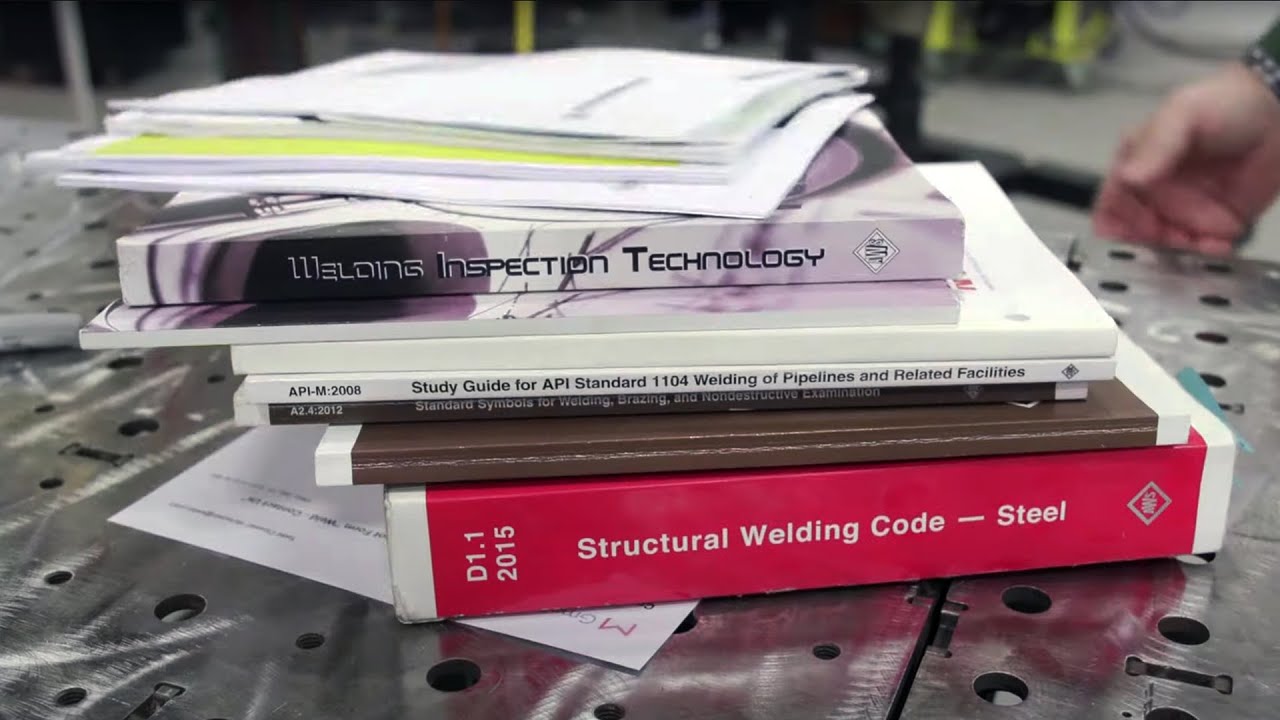
Prep before the CWI Exam.
The CWI exam
The CWI exam consists of three parts:
- Part 1: Fundamentals examination. Evaluates general understanding of welding processes and concepts. Includes 150 questions on destructive testing, fabrication mathematics, safety, metallurgy, nondestructive testing, welding symbols, WPS/PQR and welding fundamentals.
- Part 2: Practical CWI exam. Here, candidates must identify defects in real or simulated welds. It also consists of practical activities using equipment provided by AWS and 46 questions related to those activities. The activities include:
- Application of WPS and PQR.
- Use of inspection tools, methods, and techniques.
- Execution of the required welds.
- Part 3: Codebook examination. This part of the CWI examination is an open-book test that establishes the participant’s ability to locate and understand the information in the codebook. The 50 to 65 questions on the exam are based on the editions of the codebook listed in the Welding Standards section of this content.
Responsibilities of a certified welding inspector
A Certified Welding Inspector plays an important role in ensuring the quality and safety of welded structures. Their responsibilities cover a wide variety of tasks, including:
- Interpretation of codes and standards:
- Proficient in codes such as AWS, ASME, API, and others relevant to the industry.
- Ensure that all welding activities comply with the requirements set forth in these codes.
- Verification of welding procedures:
- Evaluate and approve qualified welding procedures (WPS).
- Verify that welders are qualified to perform the work according to approved procedures.
- Monitor compliance with procedures during the execution of welds.
- Evaluation of materials:
- Ensure that the materials used comply with the project specifications.
- Visual and dimensional inspection:
- Perform thorough visual inspections of welds for defects such as cracks, pores, undercuts, etc.
- Verify weld dimensions according to design requirements.
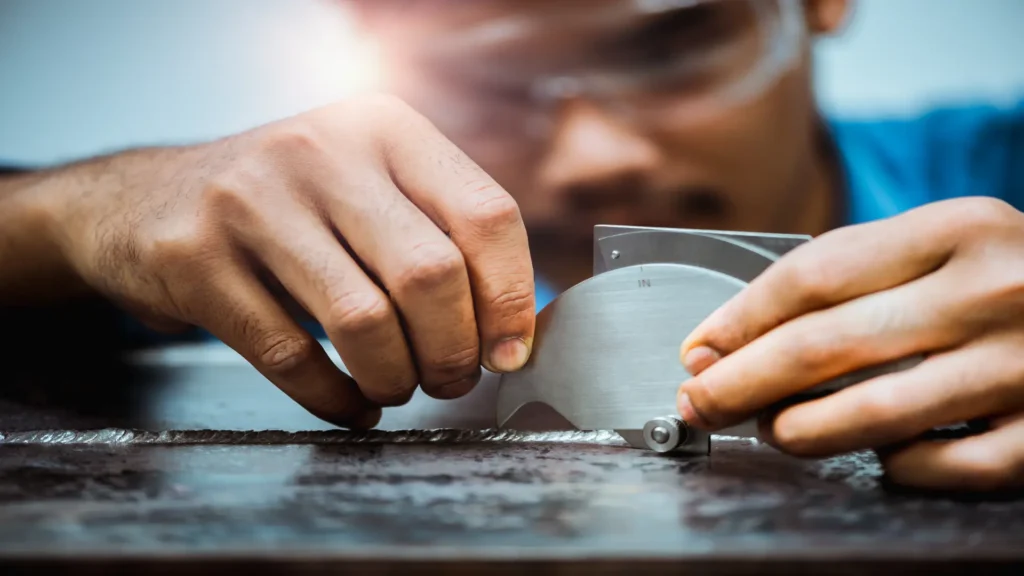
- Non-Destructive Testing (NDT):
- Perform or supervise NDT tests such as radiography, ultrasound, liquid penetrant, and magnetic particle.
- Interpret test results and take necessary corrective actions.
- Qualify procedures and welders by destructive testing if required.
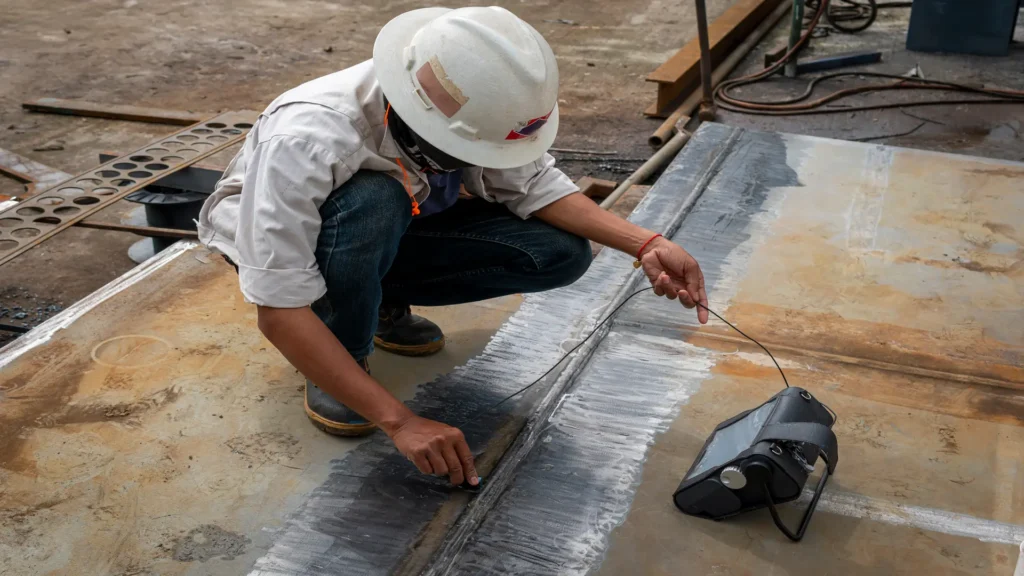
- Documentation and reporting:
- Maintain detailed records of all inspections performed.
- Produce clear and concise reports on the results of inspections, including any deviations from requirements.
- Recommend corrective actions for identified problems.
- Coordination with other teams:
- Work closely with engineers, welders, quality inspectors, and other project team members.
- Training and development:
- Keep up to date on the latest developments in welding codes, standards, and technologies.
- Participate in ongoing training programs to improve their knowledge and skills.
Benefits of CWI certification for professionals
- Increased employability: CWI inspectors are in high demand in various industry sectors.
- Competitive salaries: Obtaining CWI certification is directly related to higher salary opportunities. For example, a qualified equipment inspector without CWI certification typically earns a lower salary compared to a certified inspector, whose accreditation ensures greater professional recognition and remuneration commensurate with their level of expertise and responsibility.
- Professional prestige: Being a CWI brings great recognition in the industry.
- Continuous development: Certification requires keeping knowledge up to date.
Benefits for companies
Companies that employ certified welding inspectors have significant competitive advantages, such as:
- Regulatory compliance: Ensure that projects comply with international laws and standards.
- Operational efficiency: Detect and correct welding problems before they become costly failures.
- Reputation and trust: Organizations that value safety and quality are more respected in the industry.
Welding standards: The safety guide
Welding standards are detailed guidelines that govern how welding operations should be performed. These standards, defined by the American Welding Society, cover everything from material properties to inspection techniques, and are important to ensure welding quality and safety.
Main AWS standards and other applicable standards
- AWS D1.1: Structural Steel Code: 2020 Edition.
- API 1104: 22nd edition: Welding of pipelines and related installations.
- AWS D1.2: Structural aluminum code: 2014 edition.
- AWS D1.5: Bridge Welding Code: 2015 edition (including clause 12).
- AWS D15.1: Rail: 2012 Edition.
- AWS D17.1: Aerospace: 2017 with amendment 2.
- Section IX of ASME BPVC (2019 edition), B31.1 (2018) and B31.3 (2018).
- ISO standard.
Certified welding inspectors must be well-versed in these standards in order to perform their work effectively.
The future of CWI certification
This certification, awarded by the American Welding Society (AWS), has been an industry benchmark for decades. However, the current and future landscape presents some trends and challenges that will shape the role of the certified welding inspector:
- Technology integration:
- Digitization: Digitization of inspection processes, including the use of drones, robots, and image analysis software, will enable more accurate and efficient inspections.
- Virtual and augmented reality: These technologies will facilitate the training of new inspectors and will make it possible to visualize and analyze welds in greater detail.
- Big data and analytics: The analysis of large volumes of data will make it possible to identify patterns, predict failures, and optimize inspection processes.
- Focus on prevention:
- Predictive maintenance: CWI inspectors will play a key role in implementing data-driven predictive maintenance programs to avoid catastrophic failures.
- Simulation and modeling: The use of simulation tools will allow the performance of welds to be evaluated prior to fabrication, reducing costs and improving quality.
- Globalization and standards:
- Harmonization of standards: The increasing globalization of the industry will require greater harmonization of welding norms and standards internationally.
- Mutual recognition of certifications: It is expected that there will be greater cooperation between the different certifying organizations to facilitate mutual recognition of certifications.
- New materials and processes:
- Advanced materials: The emergence of new materials, such as composites and 3D-printed metals, will require CWI inspectors to acquire expertise in these materials and associated welding processes.
- Innovative welding processes: Advances in welding processes, such as laser welding and friction stir welding, will require new inspection and certification techniques.
- Sustainability:
- Green welding: CWI inspectors will play an important role in promoting more sustainable welding practices, reducing energy consumption, and minimizing environmental impact.
What does this mean for CWI inspectors?
- Continuous training: CWI inspectors must be willing to constantly update themselves to keep up with the latest technologies and trends.
- Adaptability: The ability to adapt to new environments and technologies will be critical to the success of CWI inspectors.
- Critical thinking: Problem-solving and data-driven decision-making will be increasingly valued skills.
- Collaboration: Teamwork and collaboration with other professionals will be essential to address industry challenges.
In summary, the future of CWI certification is promising and full of opportunities. Certified welding inspectors who adapt to these changes and acquire the necessary skills will be able to play a key role in building a safer and more sustainable future.
Conclusions
CWI (Certified Welding Inspector) certification is an essential pillar of quality and safety in the welding industry. Both Certified Welding Inspectors and the companies that employ them play a critical role in preventing structural failure and complying with international welding standards. In a world where safety cannot be compromised, having highly trained and certified professionals is imperative.
Investing in this certification is ultimately an investment in the safety, quality, and success of industrial and energy projects. As we can see, this certification not only raises the level of professionals but also strengthens organizations by ensuring that welding practices are carried out under the most rigorous standards.
Get your CWI Certification and take your career or project to the next level – invest in quality and safety today!
References
- AWS.org: American Welding Society
- ISTUC: Instituto de soldadura y tecnología y de unión.