Table of Contents
- What is fusion welding?
- Importance of non-ferrous metal welding in industry
- What are the most common welding defects in non-ferrous metals?
- Main fusion welding methods for non-ferrous metals
- Best practices to improve the welding process
- Innovations and emerging technologies in fusion welding
- Conclusions
- References
Fusion welding is an essential primary technique in the manufacture of products in various industrial sectors, especially when working with non-ferrous materials. These materials, such as aluminum, copper, and their alloys, require a specialized approach to avoid problems and maximize efficiency.
This article explains methods, techniques, and best practices for optimizing welding on non-ferrous materials, including the use of TIG welding, MIG welding, and other key aspects to reduce weld defects and achieve high-quality joints.
What is fusion welding?
This welding consists of joining two or more pieces of material by applying heat, causing the materials to melt and form a solid joint. Regarding non-ferrous metals, they are those metals and alloys that do not contain iron in significant quantities. These materials are characterized primarily by their corrosion resistance, light weight and high thermal and electrical conductivity, making them essential in many industrial applications where iron is not suitable.
Common welding materials include aluminum, copper, magnesium, and titanium. Each has its own properties and challenges; therefore, it is essential to know the characteristics of each material before starting the welding process.
Importance of non-ferrous metal welding in industry
The use of these materials in industry has increased due to their corrosion-resistant and lightweight properties, making them ideal for applications in sectors such as aeronautics, automotive, and energy. The correct fusion welding of these materials guarantees the durability and safety of the final products.
However, these metals present particular challenges, such as the propensity to oxidize, which requires specific techniques and controls. Therefore, mastering this technique is key to ensuring quality and strength in the joints and guaranteeing their strength and quality. An incorrect process can result in defects that weaken the structure and compromise safety. Precision in the choice of appropriate techniques and equipment maximizes the strength of welds, especially in critical applications.
What are the most common welding defects in non-ferrous metals?
In non-ferrous materials, welding defects are usually divided into geometrical defects and metallurgical defects. These problems affect the quality of the weld and must be carefully controlled to ensure durable and strong joints.
Geometrical defects
These occur mainly due to problems in equipment handling and welding techniques, such as:
- Incorrect torch angle: May cause uneven joints.
- Inadequate speed: Too fast or too slow a feed rate affects the uniformity of the weld.
- Incorrect electrical parameters: Incorrect voltage or amperage settings can lead to weak or overwelded welds.
Metallurgical defects
These defects are related to material properties and temperature. Some factors that cause them include:
- Impurities in the base material: Unwanted elements can be trapped in the weld, weakening the joint.
- Inadequate temperature cycling: Poor temperature control can alter the structure of the metal, forming unwanted phases.
- Unsuitable filler metal: The use of a filler metal that is not compatible with the base material can lead to failures.
- Formation of undesirable compounds: In some metals, compounds, such as carbide, can form that weaken the weld.
- Imbalance in internal structures (ferrite/austenite): In sensitive materials, incorrect mixing can cause embrittlement.
Controlling these defects in non-ferrous materials requires careful management of techniques and proper selection of materials and temperatures to ensure high-quality welds.
Main fusion welding methods for non-ferrous metals
There are several fusion welding methods used for working with non-ferrous metals. Two of the most common and effective methods are described below: TIG welding and MIG welding.
TIG welding (Tungsten Inert Gas)
It is a technique that uses a tungsten electrode and an inert gas, usually argon, to protect the weld area from oxidation. This method is ideal for working with non-ferrous metal, especially aluminum and magnesium, which are highly reactive and prone to oxidation.
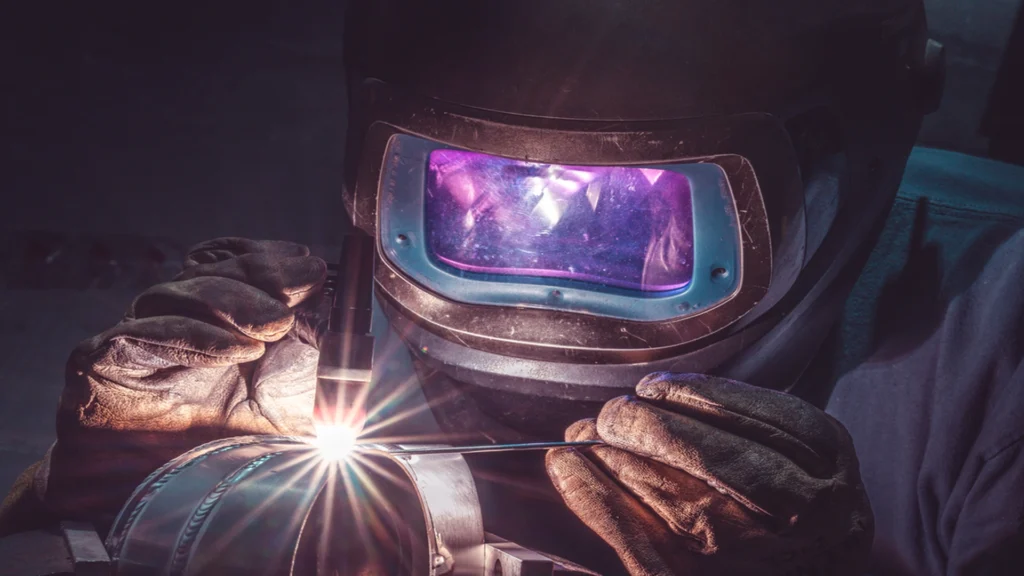
Advantages of TIG welding of non-ferrous metals
- Precise fusion control, ideal for precision work.
- Production of a clean and aesthetically pleasing weld bead.
- Reduced risk of welding defects due to arc stability.
Disadvantages
- It is a slow process compared to other welding methods.
- It requires a high level of skill and experience from the operator.
MIG Welding (Metal Inert Gas)
MIG welding is another popular common method for fusion welding of non-ferrous metals. This process uses a consumable wire as the electrode, which is continuously fed, allowing for faster welds. As with TIG welding, inert gas (argon or a mixture of argon and helium) protects the weld from oxidation.
Advantages of MIG welding
- It is a faster and more efficient technique in terms of working time.
- Ideal for large-scale welding projects where speed is crucial.
- Greater tolerance to the presence of impurities in the base material.
Disadvantages
- Lower accuracy compared to TIG welding, which can be problematic in fine or detailed work.
- Higher risk of spatter and other defects in welds.
Best practices to improve the welding process
Material preparation
Preparation is vital to achieve a sound and flawless bond. The most important steps are described below:
- Surface cleaning: Non-ferrous material usually have a layer of surface oxide that must be removed prior to welding. In the case of aluminum, for example, aluminum oxide is commonly removed by mechanical brushing or with a specific cleaning solution.
- Material preheating: Materials such as copper and its alloys may require preheating to reduce thermal deformation and improve the flowability of the filler material.
- Filler material selection: It is essential to choose a filler material compatible with the base metal to avoid weld defects. For aluminum, aluminum-silicon or aluminum-magnesium filler alloys are commonly used, while for copper, copper-zinc alloys are commonly used.
- Adjustment of welding parameters: Proper setting of current, voltage, and electrode feed rate is essential to avoid weld defects and achieve uniform fusion.
Main defects in welding and how to avoid them
During fusion welding of non-ferrous metal, certain welding defects are common if proper parameters and techniques are not applied. Here are some of the most common defects and strategies to avoid them.
Porosity
Porosity is a common defect in non-ferrous metal welding, especially in aluminum. This defect occurs when gas is trapped in the molten material and forms small bubbles that weaken the weld structure.
Solution: Use high-purity inert gas and ensure that the surface is completely clean. It may also be useful to increase the gas flow to improve the protective coverage.
Hot cracking
Hot cracking occurs when the material cools too quickly after melting, causing cracks in the solidified metal.
Solution: Preheat the material before welding to reduce the cooling rate and avoid crack formation.
Thermal deformation
The high thermal conductivity of some non-ferrous metals, such as copper, can cause deformations during this welding process.
Solution: Control the temperature by preheating and apply controlled cooling after welding.
Oxide inclusions
In TIG and MIG welding, oxides can become trapped in the weld, weakening it and causing joint failure.
Solution: Properly clean and brush the material before starting, in addition to maintaining a constant inert gas atmosphere during the process.
Welding quality control
Carrying out quality controls in the different stages is the most advisable to comply with the quality of the product and the codes, norms, and standards such as API, ASME, ANSI, among others, thus complying with the engineering design.
Visual inspection
Visual inspection is one of the most common and effective methods to evaluate the quality of fusion welds. This process consists of examining the welds with the naked eye or with basic weld measuring tools (gauges, vernier, squares), magnifying glasses, looking for visible defects and features that ensure the structural integrity of the joint.
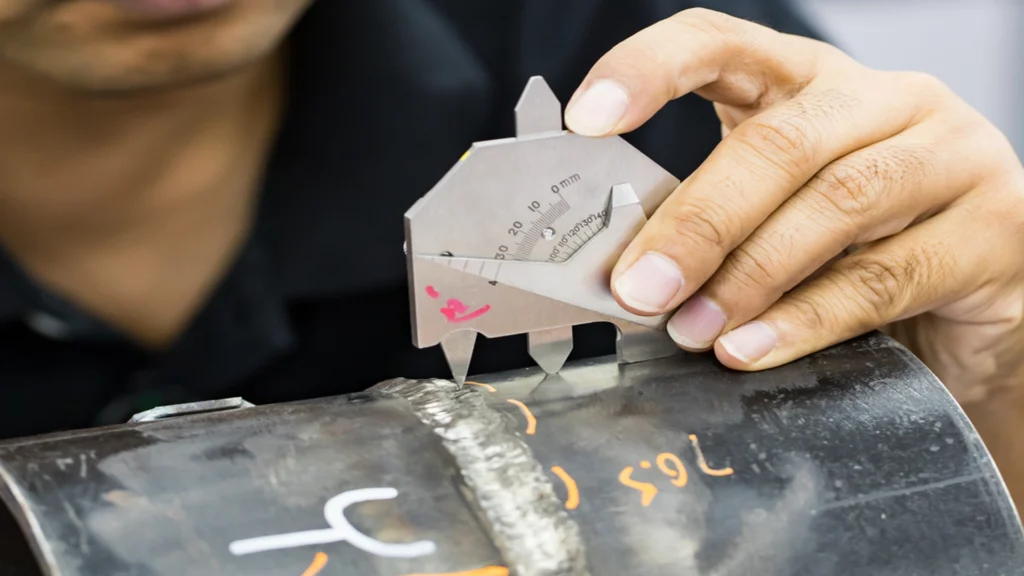
Positive Material Identification (PMI)
Positive Material Identification (PMI) is a key technique to ensure that the non-ferrous metals selected for fusion welding meet the specifications and properties required for the application. In welding, especially in industries where structural integrity and corrosion resistance are critical, such as petrochemical, energy, and aerospace, the use of the correct material is critical to avoid failure and maximize joint life.
Non-Destructive Testing (NDT) Application
Non-destructive testing (NDT) is essential to verify the integrity of welds. Methods such as ultrasound and radiography can be used to identify internal defects in non-ferrous metals, while liquid penetrant tests are useful to detect surface cracks in aluminum and copper. The choice of test depends on the properties of the material and the type of welding performed.
Other recommendations
To obtain the best results in this type of welding, it is important to take into account some practical tips:
- Maintaining high-quality welding equipment: Accuracy in TIG and MIG welding depends to a large extent on the quality of the equipment and its components.
- Train personnel properly: The welder’s skill and experience are critical to minimize welding defects and ensure proper fusion.
- Adjust the working environment: Non-ferrous metals are sensitive to oxidation and other contaminants. Working in a controlled environment helps reduce the risk of defects.
- Perform quality tests: A visual inspection and, if possible, verification tests of the joints before starting the welding, will guarantee the results.
Innovations and emerging technologies in fusion welding
Advances in automatic and robotic welding for non-ferrous materials
Automated and robotic welding offers precision and repeatability in industrial processes, especially in non-ferrous metal fusion welding. Welding robots, integrated with vision systems, enable precise heat application and improve the quality of welds in high production runs.
New alloys and their impact on melting processes
The development of new alloys, such as aluminum-lithium and nickel alloys with improved melting properties, has made it easier to work with non-ferrous metals under extreme conditions. These innovations allow improved weldability and durability, broadening the industrial applications of these materials.
Conclusions
Fusion welding on non-ferrous materials can be performed successfully when precise and appropriate techniques, equipment, and trained personnel are applied. The choice between TIG and MIG welding methods should be based on material properties and project requirements, ensuring optimum adaptation to the context of each application. This approach reduces defects and improves weld integrity, thus contributing to process efficiency and final product quality.
Fusion welding of non-ferrous materials is a challenging process that requires precision, knowledge, and proper technique. The choice between TIG and MIG welding will depend on the characteristics of the material and the specific requirements of the project. With proper preparation, the use of quality equipment, and continuous training of personnel, it is possible to achieve solid, defect-free welds, thus maximizing efficiency and product quality.
Improve your welding techniques now and raise the quality of your industrial projects!
References
- Air Liquide: ¿Cuáles son los defectos de soldadura más comunes?https://es.airliquide.com/soluciones/soldadura-industrial/cuales-son-los-defectos-de-soldadura-mas-comunes
- Arccaptain: ¿Qué es la soldadura por fusión? Su proceso y aplicaciones (Apr 17, 2024) https://www.arccaptain.com/es/blogs/article/what-is-fusion-welding?s
- Codam: Soldadura en metales no ferrosos (Ago 16, 2024) https://codam.com.ar/2024/08/16/soldadura-en-metales-no-ferrosos/