Introduction
The Atomium, located in Brussels, Belgium, is an architectural landmark symbolising innovation in materials engineering, designed by engineer André Waterkeyn and architect Jean Polak and built for the 1958 World Exposition in Brussels. This iconic 102-metre-high structure represents an iron crystal magnified 165 billion times and is made up of nine steel spheres 18 metres in diameter, interconnected by tubes that reflect the forces operating inside an atom.
Despite the advanced technology in resistant materials used in the design and construction of this iconic structure. A symbol of innovation in materials engineering, it is not exempt from facing problems of deterioration and corrosion damage caused by the weather and the environment. Therefore, it is essential to carry out regular inspections and maintenance to ensure its structural integrity, thus preserving this iconic construction as a symbol of progress and sustainability in modern engineering.
This article aims to highlight the Atomium as a symbol of innovation in materials engineering and to analyse the challenges of its conservation over time, due to deterioration and corrosion factors. It explores the relevance of the structure as an architectural heritage and the importance of periodic maintenance to ensure its integrity.
Crystalline structure and materials of the Atomium
The Atomium is a faithful reproduction of the crystal lattice of pure atomic iron, with a Body Centered Cube (BCC) structure at room temperature. The nine spheres represent the nine constituent atoms of the iron crystal, as shown in figure 1.
The structure was designed with an unnatural orientation: a cube resting on one of its spheres, with a vertical diagonal, more for aesthetic than functional reasons. This approach, however, demanded high precision in structural calculations to avoid collapse during and after construction1.
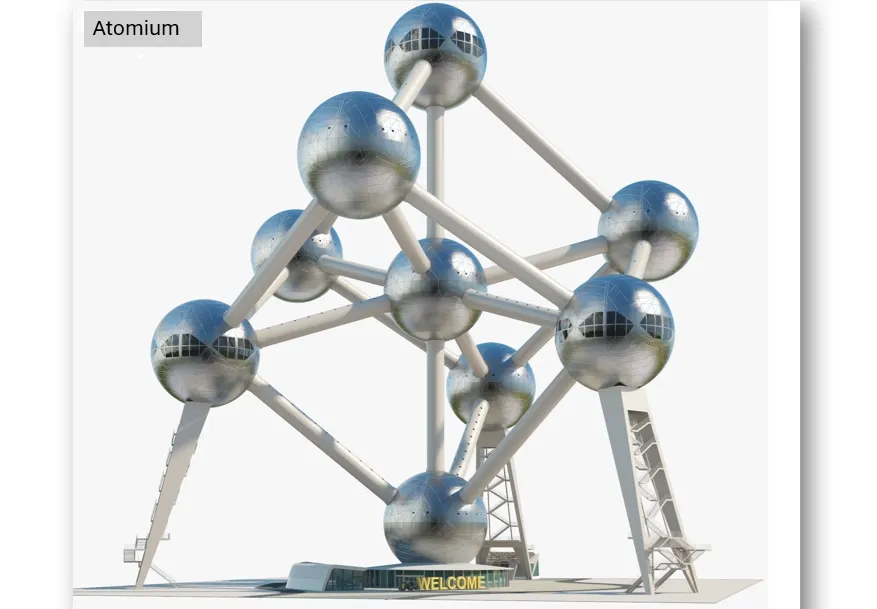
The base of the structure sits on a steel frame that has been designed with the body-centred cubic (BCC) crystal lattice in mind. This type of lattice is significant for understanding the arrangement of atoms in iron, which exhibits superior mechanical properties at room temperature and up to 911°C.
According to the above, the design of this structure was inspired by the iron crystal, which has a cubic structure centred on the body in a unit cell (figure 2). At room temperature and up to 911 °C, it is an allotropic metal, so it changes its crystalline structure depending on the temperature at which it is found. This characteristic makes it possible to carry out heat treatments and modify the mechanical properties of steels. Iron has a cubic structure centred on the body in a unit cell at room temperature.
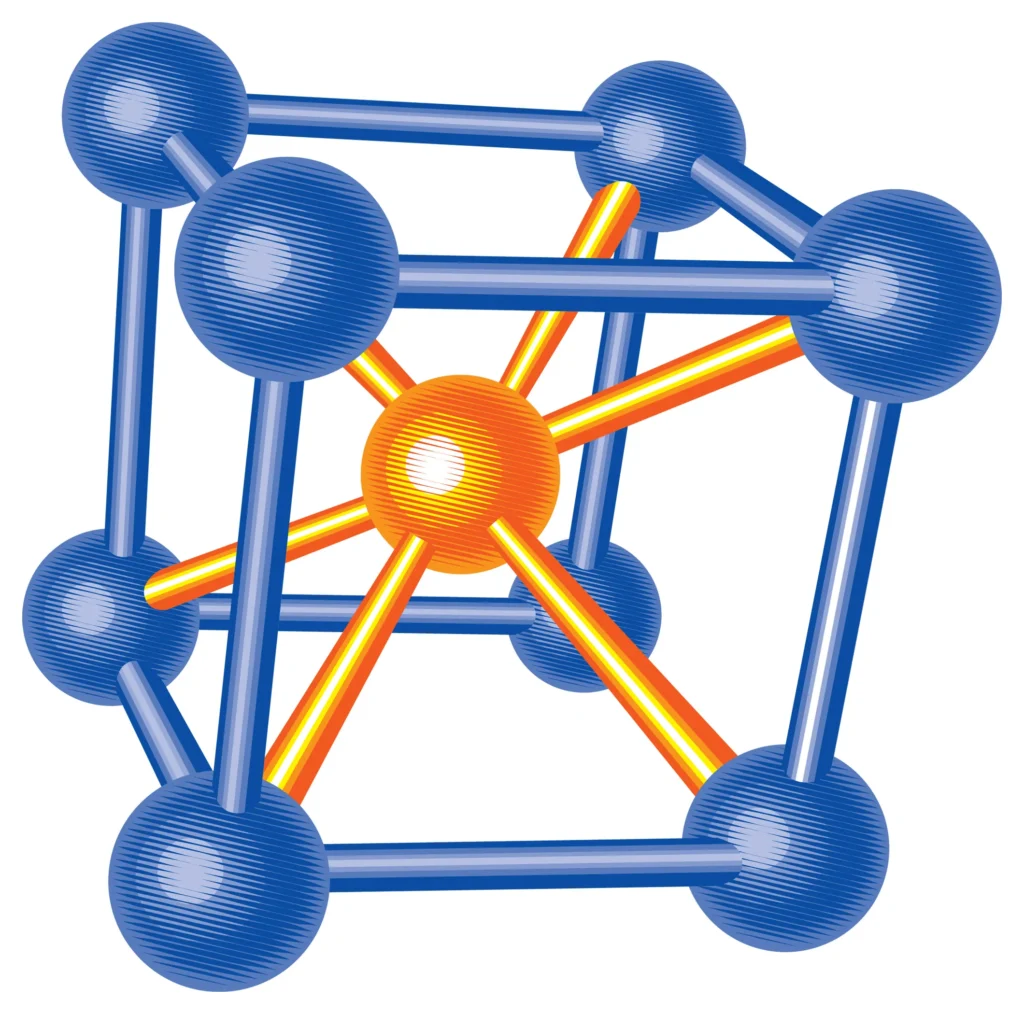
The choice of appropriate materials is considerable in the construction of structures of this scale, and this is no exception. The implementation of grade 1.4404 stainless steel, known for its high corrosion resistance and formability, has enabled the structure to maintain its integrity and aesthetics over time.
Grade 1.4404 or 316L is an austenitic stainless steel of type AISI 316 which has very good corrosion resistance due to its high chromium and molybdenum content combined with a low carbon content. Its hardened strength is about 600 MPa for large diameters, but can be increased by cold working for small sections.
Preservation: Structural and maintenance challenges
The original structure of the Atomium included a steel frame clad with aluminium panels. Over time, environmental factors such as air pollution deteriorated these materials, leading to rusting of the steel and surface damage to the aluminium, which necessitated the restoration of this work, including the following challenges:
- Corrosion susceptibility of aluminium and exposed steel: The initial choice of aluminium for the cladding posed a challenge, as its corrosion resistance was not sufficient for the environmental conditions to which it was exposed. Over time, the aluminium showed signs of wear and deterioration. In the 2001 refurbishment, the aluminium was replaced with grade 1.4404 stainless steel, which contains chromium, nickel, and molybdenum to provide high corrosion resistance.
- Surface finish: An electrolytic polish was applied to the stainless steel to produce a smooth, reflective surface, making it easier to clean and reducing particle build-up. This not only prolongs the life of the coating, but also reduces maintenance requirements.
Technical aspects of the restoration
The restoration process of the Atomium required technical innovations in the design of the new stainless steel panels. The renovated structure had to meet modern standards of thermal, acoustic and fire insulation, while maintaining the original aesthetics of the 1958 structure. The following considerations were taken into account in this process:
- Panel design: Triangular stainless steel panels with an insulating core were prefabricated and carefully segmented to respect the geometry, maintaining the space between the cladding and the structural frame.
- Panel fixing and insulation: To avoid galvanic corrosion between the metals of the panels (stainless steel and galvanised steel), elastomer profiles were used as spacers. Fixing the panels was a challenge due to the curved shape and the need for precise alignment, achieved with adjustable mounting discs.
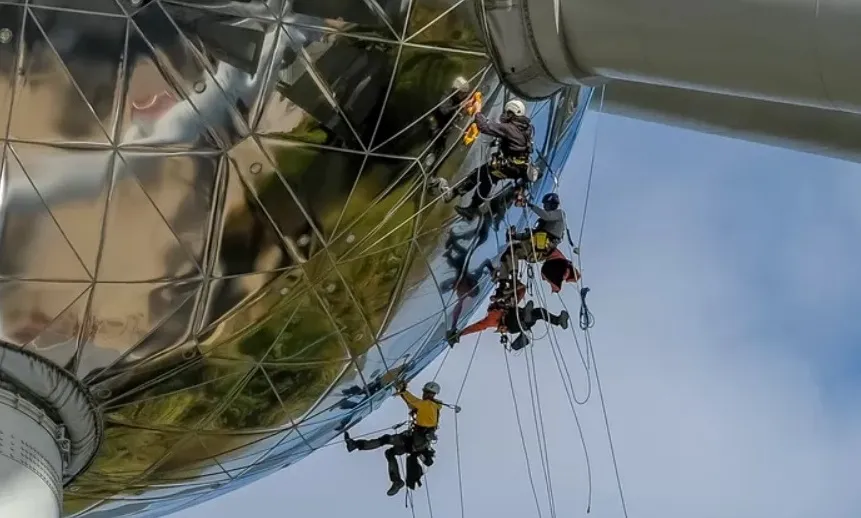
- Installation and cladding process: During the installation of the panels, cranes, and cables were used to position the parts without the need for extensive scaffolding. The panels were attached to the steel frame by means of clamps and H-shaped steel profiles, ensuring a stable and watertight structure. This process allowed to be restored while minimising disruption to its historic structure.
Safety and modernisation considerations
In the preservation process, the original structure was kept largely intact to preserve the historic design. However, today’s safety and sustainability requirements led to a series of strategic interventions to bring it up to modern standards. Advanced fire protection systems were incorporated to ensure a rapid response in the event of an emergency, as well as thermal insulation, improved ventilation and redesigned electrical networks. In addition, the lighting system was upgraded, installing LED lights in the meridians of the spheres, which highlight the design of the unique structure, striking a balance between heritage conservation and modern technology.
Conclusion
The Atomium is an example of how materials engineering and structural maintenance can preserve a landmark building in the face of adverse environmental factors and material obsolescence. The innovations applied to the cladding and structure reflect advances in materials engineering and maintenance techniques for metal structures that ensure greater durability and functionality.
References
- Great icons of architecture and engineering as you’ve never seen them before.
- https://www.hln.be/brussel/aha-dus-zo-blijft-het-atomium-blinken~a9a2d6b9/