Table of Contents
- Introduction
- Technical description
- Dissimilar metals and their weldability
- Materials involved
- Jointing mechanisms
- Technique selection
- Technical challenges
- Evaluation of mechanical and metallurgical properties
- Quality tests
- Factors affecting quality
- Specific applications and uses
- Advantages and disadvantages of bimetallic welding
- Real examples
- Results analysis
- New developments
- Conclusions
- References
Introduction
Welding is a fundamental technique in the fabrication and repair of metal structures, piping, and equipment, widely used in industries such as automotive, shipbuilding, energy, and aerospace, among many others. However, not all welding processes involve joining identical metals. In many cases, it is necessary to join different materials to take advantage of each other’s unique properties, which has led to the development of bimetallic or dissimilar welds.
Bimetallic welds involve the joining of two or more dissimilar metals, each with its own physical, chemical, and mechanical properties. This ability to combine the best of both worlds makes bimetallic welds, although complex, essential in applications where special characteristics such as corrosion resistance, thermal conductivity, or wear resistance are required.
Technical description
Bimetallic or dissimilar welds refer to the joining of two metallic materials that are not identical in composition. This can include joining different steel alloys, steel to aluminum, copper to steel, among others. The main objective is to take advantage of the complementary properties of the materials involved to create a bond that is more suitable for a specific application than if only one material were used.
Dissimilar metals and their weldability
One of the main challenges of bimetallic welding is the weldability of dissimilar metals. The difference in physical and chemical properties between metals, such as thermal conductivity and coefficient of thermal expansion, makes it difficult to join dissimilar metals, which results in undesirable metallurgical phenomena. These phenomena include the formation of brittle intermetallic phases, residual stresses, and weld and heat-affected zone (HAZ) stresses.
Successful weldability of bimetallic materials depends largely on good design with proper choice of materials, compliance with welding procedure specifications (WPS), and control of the welding process to minimize these effects. Bimetallic welds should only be used when they are absolutely necessary and provide real benefit.
The following video shows in practice how to describe some of the actions to take into account when welding dissimilar metals, but it is important to remember that each case is unique and requires a detailed analysis to select the most appropriate welding procedure.
Materials involved
The most common materials in dissimilar welds include:
- Steel with copper: Used in applications where high thermal conductivity is required along with the mechanical strength of steel.
- Stainless steel with aluminum: Used in the automotive industry to combine the corrosion resistance of stainless steel with the lightness of aluminum.
- Titanium with steel: Applied in the aerospace industry due to the high strength-to-weight ratio of titanium.
- Inconel with nickel alloys: Used in the aerospace and gas turbine industries, this combination enables the manufacture of components that can operate at high temperatures and in highly corrosive environments. The compatibility between Inconel and other nickel alloys facilitates welding and provides an effective transition in critical components such as turbine blades and engine components.
- Inconel with titanium: Although less common and a very complicated dissimilar weld, this combination is used in applications where high mechanical and corrosion resistance is required, such as in the aerospace industry. Inconel provides an oxidation and corrosion-resistant barrier, while titanium provides lightweight and structural strength.
- Aluminum and Inconel: For rocket transition points, leak-proof joints are used between two different materials. Instead of using a mechanical joint, friction welding offers a simpler and more reliable alternative.
Jointing mechanisms
Joining dissimilar metals is not trivial due to differences in material properties. The main difficulty lies in the formation of brittle intermetallic compounds at the interface of the materials, which can compromise the integrity of the weld. The most common joining mechanisms include fusion welding, friction stir welding, and laser welding, each with its own technical challenges.
Common techniques
- TIG Welding (Tungsten Inert Gas) welding: Suitable for joining dissimilar materials that require high-temperature control and a clean welding environment. It is very useful for joining pipes of different characteristics such as carbon and low alloy steel with stainless steels.
- MIG Welding (Metal Inert Gas) welding: Used for fast and efficient joining, especially in the automotive industry. It is also widely used in the weld overlay of carbon steels with stainless steels, offering protection against corrosion and erosion.
- Friction Welding (FW): This process does not require filler material and is the most commonly used for bimetallic welds. It is ideal for materials that have a high difference in their melting points, since it does not involve the complete melting of the materials, reducing the risk of deformations and residual stresses and forming stronger and more durable joints, especially in applications where structural integrity is critical. Widely used in the manufacture of rotating equipment parts such as pumps, turbines, and parts of automotive transmissions, among others.
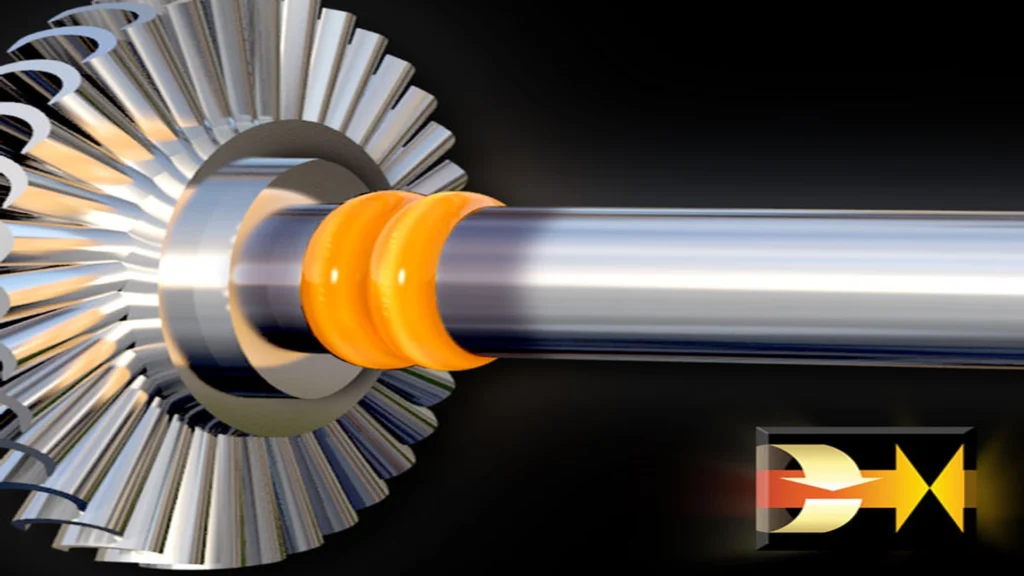
(Source: American Friction Welding)
- Laser Beam Welding (LBM): Provides high precision and precise thermal control, which is crucial to avoid the formation of unwanted intermetallic compounds.
- Explosion Welding (EXW): This technique is especially effective for joining metals with large differences in their melting points and physical properties. In this process, one of the metals is accelerated by an explosive charge towards the other metal, which causes a controlled collision resulting in the bonding of the materials at the molecular level. This method is widely used for cladding carbon steels with stainless steels, aluminum, copper, bronze, titanium, monel, and other materials that are difficult to weld by conventional methods.
Technique selection
The choice of welding technique depends on several factors, including:
- Compatibility of materials: The difference in melting points and the propensity to form intermetallic compounds.
- Final application: It is essential to consider the operating environment, paying special attention to factors such as exposure to corrosion and high temperatures. Also, the difference in electrical potentials of the dissimilar materials that will make up the bimetallic joint must be evaluated to prevent electrochemical corrosion.
- Cost and efficiency: The economic viability of the technique in relation to the scale of production.
Technical challenges
One of the main challenges in welding dissimilar materials is the difference in thermal expansion coefficients, which can cause residual stresses and cracks in the weld. In addition, the formation of brittle intermetallic compounds can weaken the joint, requiring precise control of the temperature and welding technique used.
Evaluation of mechanical and metallurgical properties
The mechanical and metallurgical properties of bimetallic welds are critical to their performance in industrial applications. These properties include:
- Resistencia a la tracción: La capacidad de la unión soldada para soportar cargas de tensión sin fallar.
- Hardness: The resistance of the weld to wear and plastic deformation.
- Toughness: The ability of the weld to absorb energy without fracturing.
Quality tests
To ensure the quality of dissimilar welds, several non-destructive and destructive tests are performed such as:
- Ultrasound: To detect internal defects such as porosity or cracks.
- Radiography: To inspect the internal integrity of the weld.
- Tensile tests: To evaluate the strength and ductility of the weld.
- Impact test: Used to determine the toughness of the weld, i.e. its ability to absorb energy before fracturing under shock or impact conditions.
- Bend test: Used to verify the ductility and quality of the weld by subjecting it to plastic deformation.
- Electron microscopy: To analyze the microstructure of the welded interface and detect the presence of intermetallic compounds.
Factors affecting quality
The quality of a bimetallic weld depends on several factors, such as surface preparation, choice of welding parameters (current, voltage, welding speed), and controlled cooling. Too fast or too slow cooling can lead to residual stresses or the formation of unwanted phases in the heat-affected zone (HAZ).
Specific applications and uses
- Automotive industry: Bimetallic welds are used to manufacture lighter and more fuel-efficient vehicles. A typical example is the joining of aluminum and steel, where the aluminum reduces the overall weight of the vehicle, while the steel provides the necessary structural strength.
- Energy industry: Dissimilar welds are essential in the manufacture of components for the energy industry, such as metallic coatings on pipelines and process towers, drill pipes, oil and gas extraction pipelines, and heat exchanger components in nuclear power plants, among many others.
- Aerospace industry: Dissimilar welding combined strength and lightness enables the construction of complex components that must withstand extreme conditions, such as high temperatures and intense vibrations. It also facilitates the integration of highly corrosion-resistant metals into critical structures, such as airframes and engines, improving the durability and performance of aircraft.
Advantages and disadvantages of bimetallic welding
Advantages
- Optimization of properties: Bimetallic welds make it possible to combine the best properties of two different materials, such as corrosion resistance and high mechanical strength.
- Cost reduction: By using an economical material in most of the structure and a more expensive material only in critical areas, costs can be significantly reduced.
- Improved performance in extreme conditions: These welds can be designed to withstand extreme environments, such as high temperatures, corrosion, or heavy wear.
Disadvantages
- Technical complexity: Requires precise control of welding parameters and a thorough understanding of material properties.
- Risk of failure: The formation of brittle intermetallic compounds can weaken the bond, increasing the risk of failure.
- Electrochemical corrosion: By difference in the electrical potential of the materials.
- High initial cost: The research, development, and implementation of bimetallic welding techniques require a higher cost than ordinary welding, especially in the initial stages.
Real examples
One of the most illustrative cases of the application of bimetallic welds is the fabrication of bimetallic pipes in the oil industry, where carbon steel is joined with stainless steel to take advantage of the corrosion resistance of stainless steel on the inner surface, while carbon steel is used on the outside to reduce costs.
Results analysis
In this case, tests have shown that the bimetallic joint significantly improves pipeline life, reducing maintenance and repair costs. In addition, an improvement in operational efficiency has been observed due to the reduced need for corrosion outages and a substantial increase in the reliability of the facilities by reducing the chances of unwanted fire events.
New developments
Current research in bimetallic welding is focused on the use of advanced technologies such as high-precision laser welding and the addition of nanoparticles to improve joint strength. In addition, non-fusion welding methods, such as solid-state welding, are being explored to reduce the formation of intermetallic compounds.
Conclusions
Dissimilar material welding is an advanced technology that allows the combination of materials with complementary properties for critical industrial applications. Although it presents significant technical challenges, its advantages in terms of performance, durability, and cost optimization make it an attractive option for various industries.
With continued research and development in welding techniques such as blast welding and the integration of new technologies, bimetallic welds are expected to play an increasingly important role in the fabrication and maintenance of metal structures in the future.
References
- https://www.sciencedirect.com/science/article/abs/pii/S0925838819348054
- https://spinweld.com/welding-dissimilar-metals/