Introduction
One of the most critical problems in industries is corrosion in buried pipelines used in industrial processes, especially those used to transport substances. The implementation of subway pipelines is an efficient method to transport products such as oil, gas, and water over long distances. However, these pipelines are exposed to an increased risk of failure due to corrosion, especially in urban areas with highly corrosive wastes.
Corrosion affects pipelines, tanks, equipment, and mechanical parts, compromising safety and operational efficiency. Over the years, numerous studies have developed and applied various methods to mitigate or reduce the corrosion rate in subway environments. Among these methods are high electrical resistance coatings and cathodic protection techniques, which protect metallic structures from environmental degradation.
The purpose of this article is to explore how corrosion impacts subway pipelines, and to evaluate the various mitigation and protection techniques used to combat this problem. Through a comprehensive review, the most effective methods to ensure the integrity and service life of these infrastructures in aggressive environments will be identified.
Causes of corrosion in buried pipelines
What is external corrosion?
Corrosion in buried structures such as pipelines and other structures is often the result of different electrochemical cells formed by: Soil aggressiveness, differential aeration, bonding of dissimilar metals or the same metal with different potentials, presence of anaerobic bacteria.
Soil aggressiveness: Buried pipelines pass through soils with varying compositions, including physical (roughness, grain size) and chemical (chemical constituents, pH) differences. These variations generate different galvanic potentials along the pipeline, which can occur on a macro scale (over kilometers) or on a microscale (within a few centimeters). These differences in galvanic potential can cause localized and accelerated corrosion in certain areas of the pipeline.
Differential aeration: Pipelines in soils with different oxygen concentrations undergo corrosion cell activity. In these cells, the portion of the pipeline in the area with the lowest oxygen concentration acts as the anode, while the area with the highest oxygen concentration acts as the cathode. This condition, known as a concentration stack, generates differential corrosion in the pipe, increasing deterioration in specific areas.
Dissimilar metals: Pipes constructed of different materials (e.g., carbon steel with brass valves) in contact with a common electrolyte and without electrical insulation can experience galvanic corrosion. The metal higher in the galvanic series becomes the anode and corrodes more rapidly, while the metal lower in the series acts as the cathode, exacerbating corrosion at the anode.
Bacteriological corrosion: Microorganisms in pipeline trenches can affect corrosion directly or indirectly. Sulfate-reducing anaerobic bacteria, which thrive in the absence of oxygen, consume hydrogen and cause a loss of polarization on the surface of the steel pipe. This depolarization hinders the effectiveness of cathodic protection, increasing susceptibility to corrosion.
Current interference effects: Also known as stray currents, they occur when direct currents from an external metallic system (not directly associated with the pipe) use the steel pipe as a conductor. These currents pass into the pipe from the soil and flow longitudinally in the steel, discharging into the adjacent soil to complete their circuit, causing localized corrosion.
Steady state: In this condition, the magnitude of the interfering current is constant and generally comes from a nearby cathodic protection system. Since the systems involved are stationary, the eddy current flow patterns are constant. This state allows relatively simple analysis by field testing, although steady currents can cause sustained corrosion in specific areas of the pipeline.
These causes of corrosion must be evaluated and mitigated to ensure the integrity and service life of buried pipelines by applying solutions such as protective coatings and cathodic protection systems, which are discussed below.
Types of external corrosion in buried pipelines
The following are the most common types of corrosion that occur in buried pipelines:
Differential aeration corrosion
It is due to the formation of piles by the union of two metals of different electronegatives, both in the same electrolyte. This mainly occurs because of the potential difference of both metals, by the nature and concentration of the corrosive medium, the polarization of the metal, and the geometric relation of the metals.
Microbiological corrosion
It is a type of corrosion generated by organisms such as: bacteria, fungi, among others, existing in the soil. Which is aerobic or anaerobic depending on the oxygen content present in the type of soil, the following figure shows this type of corrosion formed by colonies of bacteria: black gelatinous protrusions in the area in contact with the metal surface of a pipe (sulfate-reducing bacteria) and reddish brown color on this (iron bacteria).
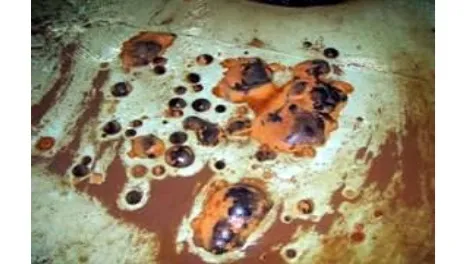
Pitting corrosion
It is a form of localized corrosion and is the most risky type of corrosion that can occur. It is generally found arbitrarily along the passive surface of the metal and slowly spreads toward the inner zone causing serious structural failures as shown in the following image.
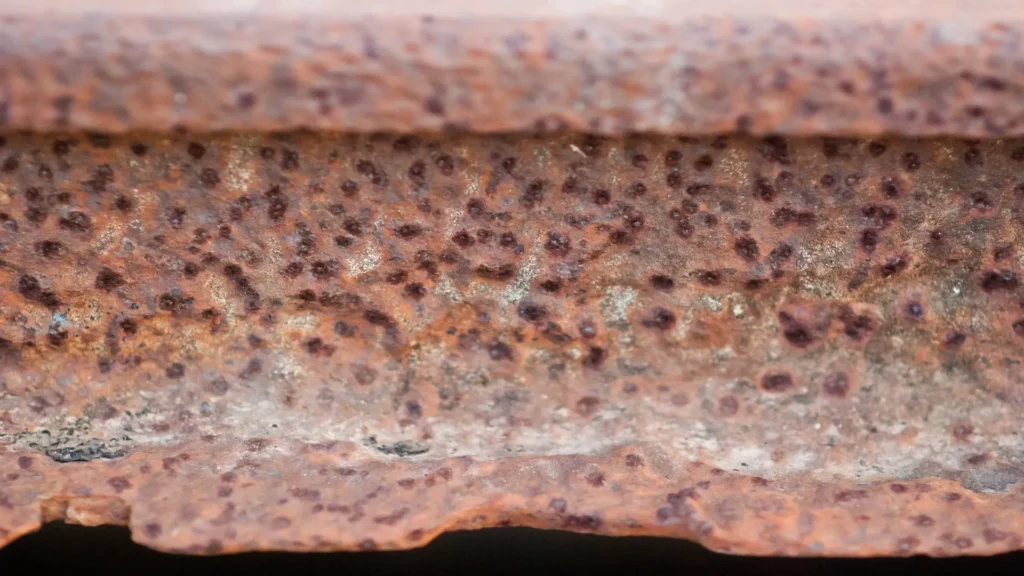
Protection in buried pipelines
Buried pipelines, unlike surface pipelines, are completely submerged in an electrolytic medium. Each soil has specific resistivity and conductivity characteristics that vary along the length of the pipeline. To ensure protection against corrosion, a simple paint coating is not enough. It is important to apply coatings that isolate the pipeline from the environment in which it is located.
Coatings
Coatings may include polyethylene, polypropylene, epoxy resin, epoxy pitch, primer, and adhesive plastic tape. Polyethylene, polypropylene, and epoxy resins require industrial application in specialized plants, while tar and the combination of primer and adhesive tape can be applied on-site. However, no coating guarantees 100% protection. Impurities in the material or errors in the application process of the protective coating, as well as shocks or scratches during transportation or installation, can compromise the insulation.
For this reason, to prolong the service life of a coated pipe, it is complemented with a cathodic protection system. This system ensures that even if the coating is compromised, the pipe will still be protected against corrosion, thus guaranteeing greater durability and reliability in its operation.
Cathodic Protection (CP)
Cathodic protection (CP) is one of the most effective methods for controlling corrosion on metal surfaces. The method consists of connecting the metal to be protected (cathode) with another metal that is more easily corroded than the first and thus acts as the anode of the electrochemical cell. As a result, the metal that is more easily corroded protects the noble metal.
Types of Cathodic Protection (CP)
- Galvanic Cathodic Protection: Galvanic cathodic protection protects the metal surface by means of a more reactive metal, known as a galvanic or sacrificial anode. This anode, with a less negative electrochemical potential, oxidizes instead of the protected structure. An example of this is the protection of steel pipes in buried pipelines with aluminum anodes. Steels can also be galvanized, i.e. coated with a layer of zinc. This zinc layer acts as a sacrificial anode, protecting the steel in subway and marine environments.
- Impressed Current Cathodic Protection (ICCP): ICCP is a more economical technique for protecting long subway pipelines or large offshore equipment. In ICCP, electrons are supplied to the structure by a DC power supply (rectifier). The steel component is connected to the negative terminal and the impressed current anodes to the positive terminal of the power supply. This method allows the protection of large and complex structures by connecting multiple anodes to the positive terminal of the power supply.
How does a cathodic protection system work?
This method achieves the protection of structures by supplying electrons to the metal from an external source, converting it into a cathode and thus preventing corrosion.
Below is a video that provides information on the operation of a cathodic protection system. Source: MOBILTEX – CorTalk.
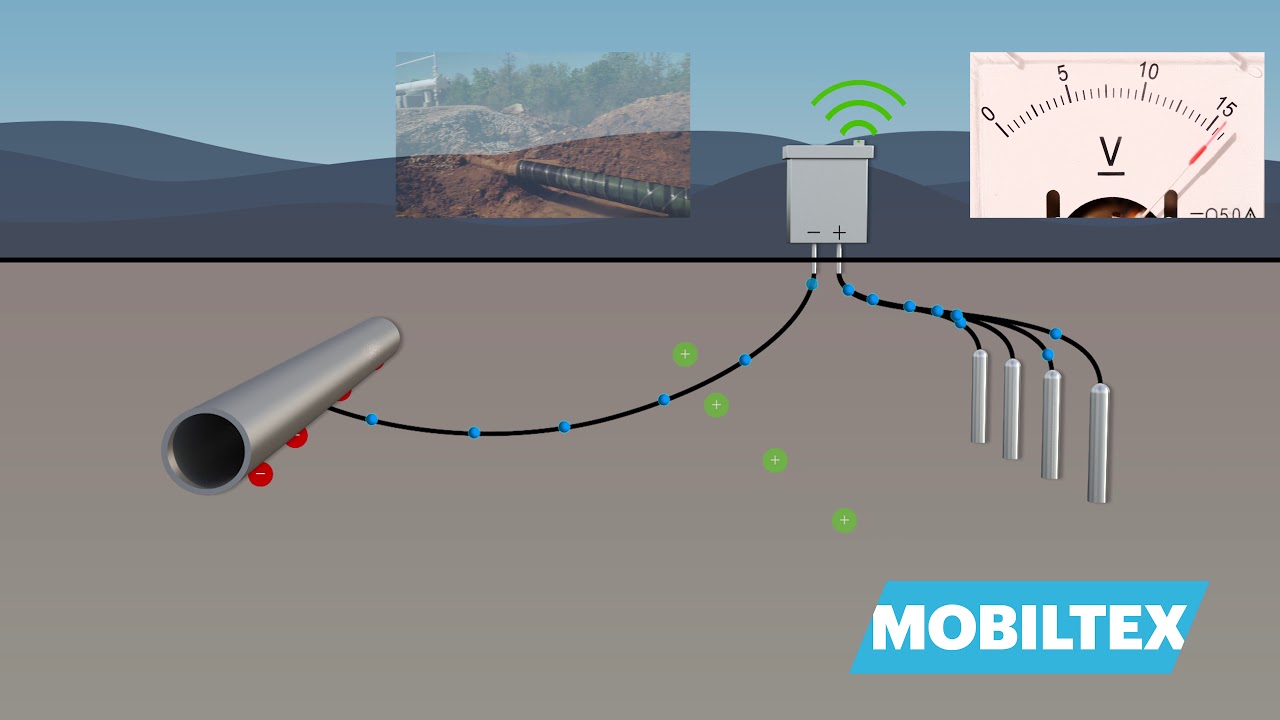
What is cathodic protection and how to monitor efficiency?
Conclusions
Controlling corrosion in buried pipelines is important to maintain the safety and efficiency of industrial processes. Lack of control can lead to unexpected failures, operational interruptions, and high repair and replacement costs.
Integrating cathodic protection into coating control methods is the safest way to prevent corrosion in subway pipelines. Coating failure is compensated by using electrical currents to counteract the corrosive processes, thus prolonging the life and operability of the pipelines. The selection of the appropriate method depends on factors such as the size and location of the structure to be protected and the conditions of the environment surrounding the pipelines.
Corrosion in subway pipelines has a significant impact on the environment and industry, causing leaks of hazardous substances, soil, and water contamination, and risks to public safety, as well as considerable economic losses for companies.
References
- Mars G. Fontana; Ingeniería de la corrosión. 3ª Edición.
- Charles Nehme; Ingeniería de tuberías: From Concept to Construction; Primera edición.