Table of Contents
Introduction
Subsea welding is a process used to join metal parts in different industrial sectors, especially in the oil and gas industry, marine construction and underwater infrastructure maintenance. This welding method plays a key role in ensuring the integrity and functionality of submerged structures in water. As industries continue to expand and innovate, understanding the current trends and future challenges is becoming increasingly important to maintain safety, efficiency and economic viability.
What is subsea welding?
Subsea welding, also known as hyperbaric welding, refers to the process of welding at elevated pressures, typically underwater. There are two main types of underwater welding: wet welding, which is performed directly in the water, and dry welding, which is performed in a dry environment created by a hyperbaric chamber.
Dry welding involves creating a temporary dry enclosure around the welding area using a specially designed habitat or hyperbaric chamber to balance the external water pressure, preventing water from flooding the workspace. This method allows welders to work in conditions similar to conventional onshore welding. However, the complexity and cost of installing the dry enclosure limit its practical application to large-scale projects or critical repairs.
In contrast, wet welding is a more widely used and accessible method. It involves welding directly in the water without any dry enclosure. Underwater welders use specialized diving equipment, such as wet welding electrodes and an electric welding machine designed for underwater use1.
Risks of subsea welding
Subsea welding is an essential technique in a variety of industries, especially in the oil and gas sector, but it carries significant risks for welders. These professionals face unique challenges due to the extreme conditions of the subsea environment. Below are some of the most critical risks associated with this profession.
Physical and environmental hazards
- High pressures and decompression; Working underwater involves dealing with high pressures, which causes health problems such as decompression sickness, also known as “the bends”. This condition occurs when welders ascend too quickly, causing dissolved gases in the blood to form bubbles that can block blood vessels.
- Hypothermia: Low water temperatures pose another significant risk. Despite specialized wetsuits, welders can experience hypothermia, a condition in which body temperature drops dangerously low, affecting cognitive and physical function.
Security risks
- Electrocution: The combination of electricity and water creates an inherent risk of electrocution. Despite advanced safety measures, there is always the possibility that equipment failure or human error could lead to a fatal accident.
- Limited visibility and accessibility: Low visibility conditions and difficulties in accessing certain areas complicate welding operations, increasing the risk of errors and accidents, as welders must often work by feel and with limited visibility.
Long-term health risks
Exposure to Toxic Substances: Underwater welders are exposed to a variety of toxic chemicals and gases, both in the water and in the materials they weld. Inhalation of these gases can lead to respiratory problems and other long-term health conditions.
Physical and mental stress: Strenuous work and long hours underwater can cause significant physical and mental stress. The need to concentrate intensely for long periods and the pressure to perform tasks under extreme conditions can lead to exhaustion and psychological disorders.
The following video shows the critical role of subsea welding in the repair of marine infrastructure such as oil rigs and pipelines, as well as, the myriad hazards faced by subsea welders. Source: Interesting Engineering.
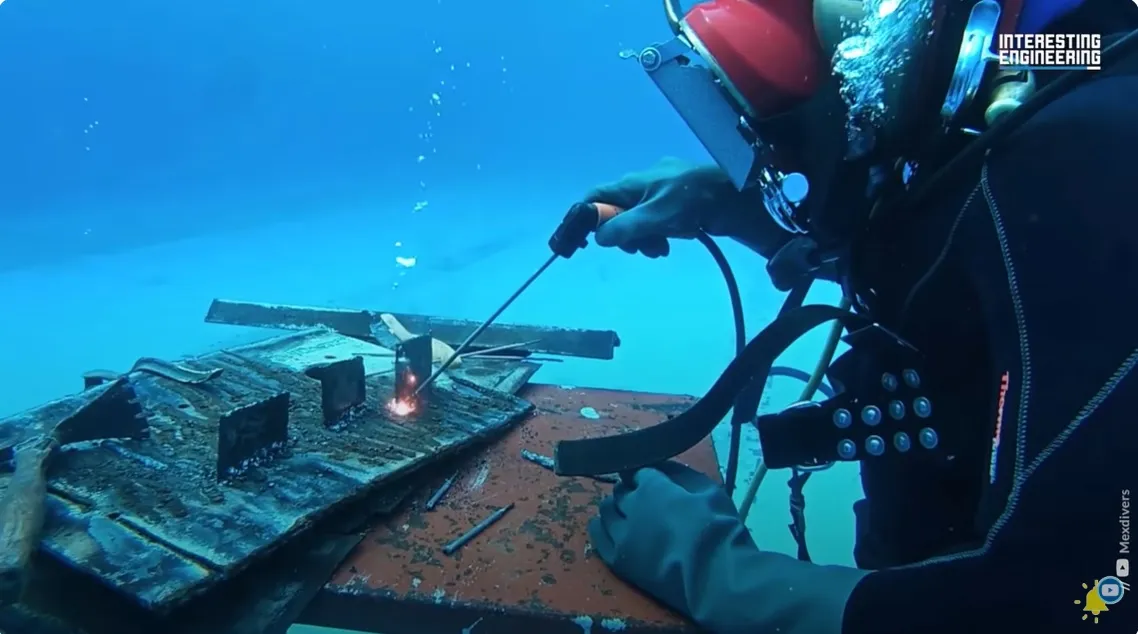
The most dangerous Job EVER: Underwater welding.
Main applications of subsea welding
Its main applications include the repair and maintenance of oil platforms, subsea pipelines, ships and other marine structures. This welding technique is indispensable for carrying out repairs without the need to bring the structures to the surface, saving time and resources. Figure 1 shows typical structures whose underwater maintenance requires subsea welding.
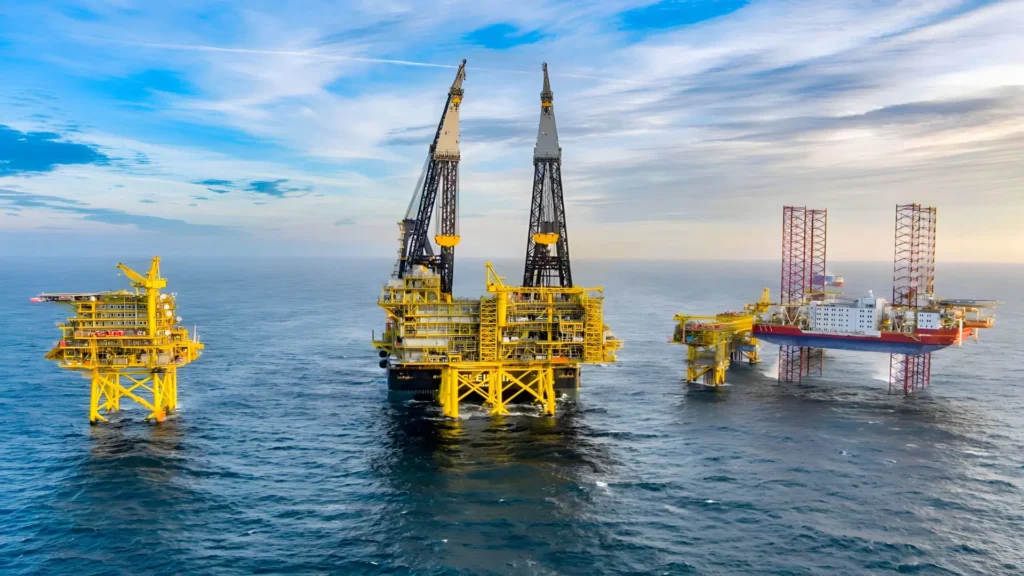
Economic and operational relevance of subsea welding
Economic importance in the oil and gas industry
In the oil and gas industry, subsea welding is crucial for the maintenance and repair of offshore drilling platforms and subsea pipelines, ensuring continuous operation and minimizing downtime, which can result in significant economic losses. By enabling in-situ repairs, subsea welding helps maintain the steady flow of oil and gas, supporting the global energy supply chain.
Operational benefits
Subsea welding facilitates the construction and maintenance of subsea infrastructure such as bridges, dams and tunnels. It enables fast and efficient repairs, reducing the need to retrieve structures to the surface, which is costly and time-consuming. This method also supports the life extension of subsea facilities, improving their safety and reliability.
Impact on safety
How does subsea welding contribute to the safety of subsea operations?
Safety is a primary concern in subsea operations. Subsea welding ensures the structural integrity of offshore installations, preventing catastrophic failures that could lead to environmental disasters and loss of life. By maintaining robust and reliable infrastructures, subsea welding contributes significantly to operational safety.
Examples of projects where subsea welding has been crucial to safety
One notable example was the maintenance of the Trans-Alaska Pipeline, where subsea welding ensured that the pipeline remained intact and operational despite harsh subsea conditions.
Another case example was the repair of the Deepwater Horizon oil rig, where subsea welding played a key role in stabilizing the structure after the disaster. Images of this accident can be seen in the following video. Source: Santa Barbara Society of the United States.

Deepwater Horizon blowout animation.
Underwater welder training
Is a highly specialized field that requires rigorous training and exceptional skills. The training process to become an underwater welder is extensive and demanding, combining traditional welding techniques with advanced diving skills.
Underwater welders begin by training to become professional welders before learning to dive commercially. You should be sure to enroll in high-quality training schools to learn the welding and diving aspects of the job before seeking additional training at an accredited institution to gather skills as an underwater welder2.
Technological trends and advances in subsea welding
Automation and robotics
Automation and robotics are becoming increasingly prevalent in subsea welding. ROVs and automated welding systems can perform complex welding tasks with high precision, reducing the need for human divers in hazardous conditions. Welding robots are available for standard welding applications and can weld with higher efficiency and quality than human welders1.
Automated systems offer unmatched accuracy and consistency, which are critical to the structural integrity of subsea welds. They also improve efficiency by performing tasks faster and more reliably than human welders.
New materials and techniques
Innovations in materials science have led to the development of new welding consumables that offer improved performance and durability in subsea conditions. These materials are designed to withstand the harsh marine environment, reducing the frequency of repairs and maintenance.
Advanced techniques to improve subsea welding quality and durability
In recent years, there have been significant advances in subsea welding technology. Innovations such as improved hyperbaric chambers and more durable welding equipment have improved the quality and efficiency of operations.
Techniques such as friction-stir welding, which generates less heat and therefore reduces the risk of material distortion, and laser welding, which allows for deeper and more accurate welds, are improving the quality and longevity of subsea welds. These techniques help ensure that subsea structures remain safe and operational for longer periods.
challenges and opportunities for subsea welding
Current challenges
Subsea welding presents several challenges, including high pressure, low temperatures and poor visibility. These conditions can make it difficult to obtain high-quality welds and ensure safe welding operations.
Technical problems such as equipment failures and difficulty in making accurate welds underwater are common. Logistically, coordinating subsea welding operations can be complex and costly, requiring specialized equipment and highly trained personnel.
Future opportunities
The future of subsea welding is promising, with numerous growth opportunities on the horizon. Increasing demand for offshore oil and gas exploration, expanding renewable energy projects and the need to maintain aging infrastructure are driving demand for advanced subsea welding techniques.
Promising areas of research include the development of new welding materials that offer improved performance in subsea conditions, the use of artificial intelligence to improve the accuracy and efficiency of welding operations, and the exploration of new welding techniques that can further improve the quality and durability of subsea welds.
Conclusions
Subsea welding is an important process that supports a wide range of industrial applications, particularly in the oil and gas sector. Despite the challenges it faces, the field is experiencing significant technological advances that are improving the quality and efficiency of welding operations. Automation, robotics and new materials are revolutionizing the industry, while innovative solutions are addressing current challenges.
The future of subsea welding is bright, with numerous opportunities for growth and development, driven by the continued need for safe and reliable subsea infrastructures. As research and technology continue to advance, subsea welding will continue to be a cornerstone of the industry.
References
- Igus Engineer’s Toolbox. Making underwater welding safer with roboticsIGUS ENGINEER´S TOOLBOX. Making underwater welding safer with robotics; Consulted on June 17, 2024. https://toolbox.igus.com/143/underwater-welding-robotics.
- TWI. What is underwater welding and how does it work?; Consulted on June 17, 2024. https://www.twi-global.com/technical-knowledge/faqs/what-is-underwater-welding