Table of Contents
- Introduction
- Overview of Non-Destructive Testing (NDT)
- Typical defects and properties evaluated in castings
- Ultrasonic testing (UT) in foundries
- Radiographic Testing (RT) in foundries
- Magnetic particle testing (MT) in foundries
- Liquid Penetrant Testing (PT) in foundries
- Eddy Current Testing (ECT) in foundries
- Selection of appropriate NDT techniques in the foundry industry
- Training and certification of NDT personnel
- Impact of NDT on quality assurance and production efficiency
- Conclusion
- References
Introduction
In the foundry industry, ensuring the integrity and quality of cast components is crucial. Non-destructive testing (NDT) methods play a vital role in this process, offering a way to evaluate the properties of materials and components without causing damage. This article delves into the application of NDT in the foundry industry, exploring various techniques, the types of defects they detect, the properties they evaluate, the selection of appropriate techniques, and the importance of personnel training and certification.
Overview of Non-Destructive Testing (NDT)
Non-Destructive Testing encompasses a variety of methods and techniques within each used to inspect and evaluate materials and components without affecting their future serviceability. NDT is essential in industries where safety and reliability are critical, including aerospace, automotive, and, notably, the foundry industry. Key NDT methods include:
- Ultrasonic Testing (UT)
- Radiographic Testing (RT)
- Magnetic Particle Testing (MT)
- Penetrant Liquid Test (PT)
- Eddy Current Testing (ECT)
Each of these methods has specific applications, advantages and limitations, making them suitable for different types of inspections in the foundry industry.
Typical defects and properties evaluated in castings
Foundry defects in a finished product can occur due to faulty pattern design, improper melting of the metal, defective molding material or improper venting. Defects can also occur due to control limitations or human interference1.
Foundries commonly encounter various types of defects and need to evaluate various properties to ensure product quality. Typical defects include:
- Shrinkage: Shrinkage is an internal volume change that occurs in the casting mold during a phase change in the transition of a metal from a liquid to a solid state. This phenomenon occurs in all types of metal casting processes2.
- Cracks: Surface or internal fractures in the casting.
- Porosity: Small holes or voids within the casting.
- Inclusions: Foreign material trapped inside the casting.
- Cold seals: Lack of fusion where two metal streams meet, but do not join.
- Casting failures: Incomplete filling of the mold, resulting in missing sections.
- Core shift: A core shift is a defect due to the buoyancy of the molten metal that causes the core of the model to move from its correct position, resulting in a disparity between the thicknesses of the part with respect to the original design. Figure 1 shows an example of core deflection.
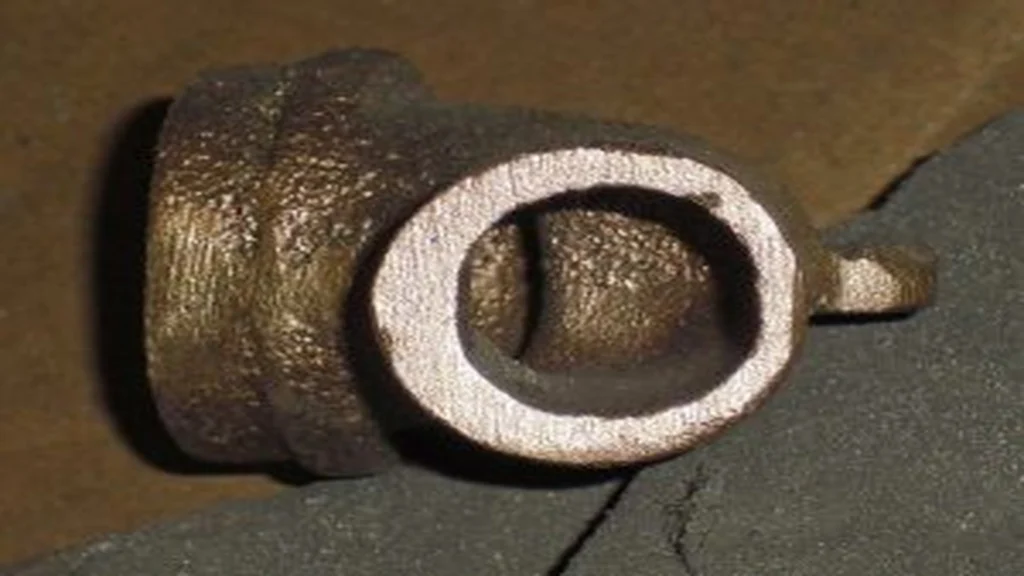
Properties evaluated include:
- Material thickness: Ensuring that the component meets design specifications.
- Surface finish: Evaluating surface quality for further processing.
- Internal structure: Verifying the homogeneity and integrity of the casting.
Ultrasonic testing (UT) in foundries
Principle of the test
Ultrasonic testing uses high-frequency sound waves to detect internal defects or characterize materials. In foundries, UT is mainly used to identify internal discontinuities such as voids, cracks and inclusions in castings.
Applications
- Internal defect detection: UT is highly effective in detecting internal defects that are not visible to the naked eye. This is crucial to ensure the structural integrity of critical components. Typical images of the internal condition of a casting are shown in Figure 2.
- Thickness measurement: Ultrasonic thickness gauges are used to measure the wall thickness of cast components, ensuring that they meet the required specifications.
- Foundry quality: By measuring the attenuation of the material, the size and distribution of the grains and thus the quality of the casting can be evaluated.

Benefits
- High penetration depth: Capable of inspecting thick sections.
- Accuracy: Provides accurate measurements of internal features.
- Safety: Non-hazardous and suitable for a wide range of materials.
Limitations
- Surface preparation: Requires good surface contact for accurate results.
- Skill dependency: Requires skilled operators to correctly interpret results.
- Scattered noise: The coarse-grained structure present in some molten metals causes noise scattering internally before the bottom echo. The scattering/parasite noise causes the instrument to generate incorrect measurements, especially when standard rather than custom settings are applied3.
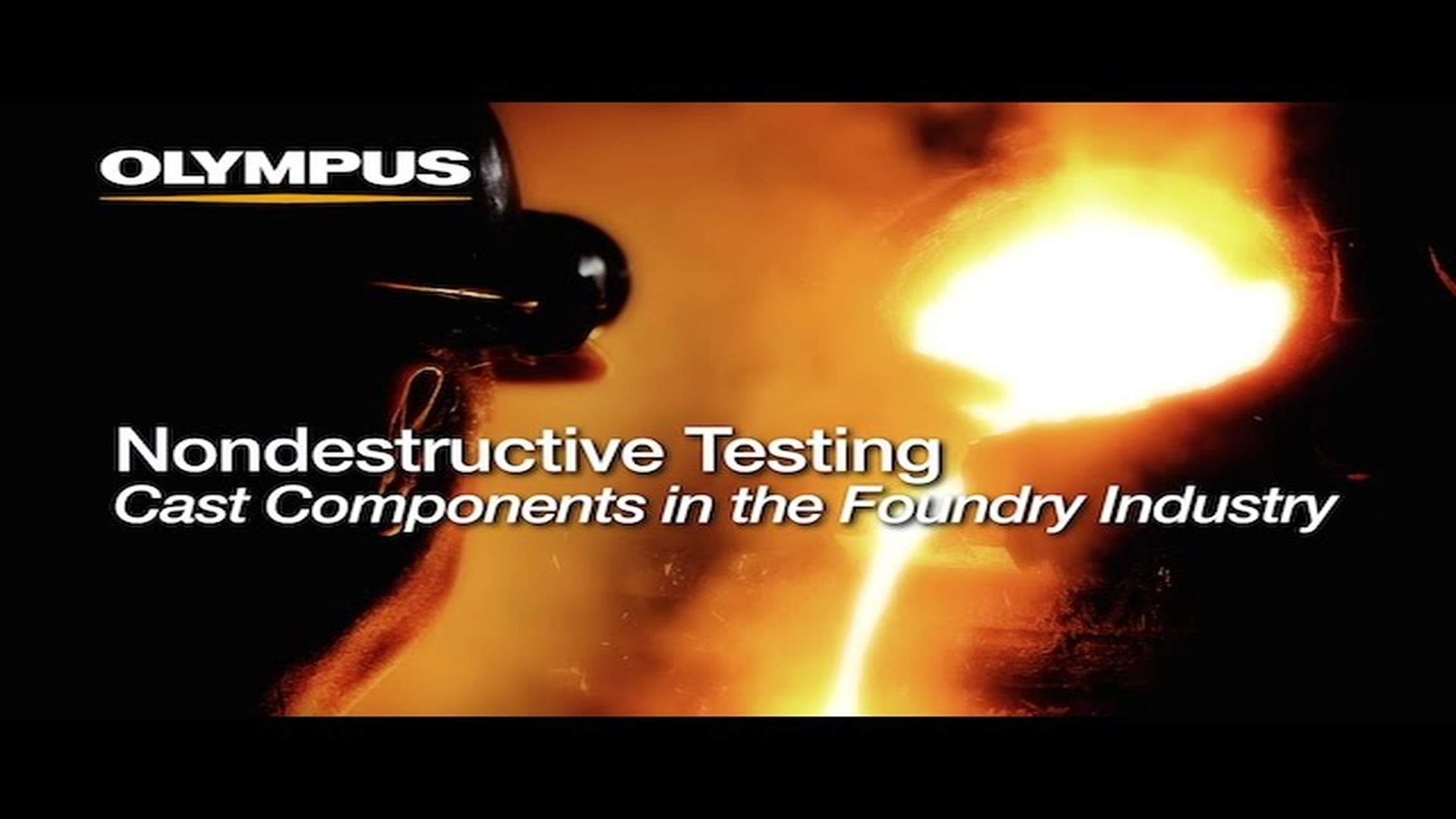
Radiographic Testing (RT) in foundries
Principle of the test
Radiographic inspections use X-rays or gamma rays to create images of the internal structure of a component. In foundries, RT is used to inspect the integrity of castings, castings and other critical parts.
Applications
- Defect detection: Identifies internal defects such as cracks, porosities and inclusions.
- Quality control: Used extensively in quality control processes to ensure that cast components meet stringent standards.
Benefits
- Detailed images: Provides a permanent record of internal structure and easy interpretation.
- Versatility: Suitable for a variety of materials and thicknesses.
Limitations
- Safety concerns: Requires strict safety measures due to the health risks of radiation exposure to both occupationally exposed workers and non-radiation personnel.
- Cost: Equipment, consumables and operating costs can be high.
- Licenses to operate ionizing radiation emitting equipment: Due to the risks involved in operations with ionizing radiation generating equipment, the necessary permits and registrations are required for industrial radiography activities.
Magnetic particle testing (MT) in foundries
Principle of the test
Magnetic particle inspections are used to detect surface and near-surface discontinuities in ferromagnetic materials. The process involves magnetizing the component and applying ferrous particles to the surface. The defects disrupt the magnetic field, creating poles around them that attract the particles and form visible indications.
Applications
- Surface crack detection: Effective in detecting surface cracks and discontinuities in cast iron and steel components.
Benefits
- Simplicity: Simple to perform and interpret.
- Cost-effective: Relatively low cost compared to other NDT methods.
Limitations
- Material limitation: Only applicable to ferromagnetic materials.
- Surface sensitivity: Detects mainly surface and near-surface defects.
Liquid Penetrant Testing (PT) in foundries
Principle of the test
Liquid penetrant testing involves applying a liquid with a primary characteristic of high capillarity that allows it to penetrate into tight, open imperfections on the surface of a component and provided with a dye for easy detection. The penetrant infiltrates surface defects and, after applying a colored developer which contrasts with the dye of the penetrant liquid, these defects become visible under ultraviolet or white light.
Applications
- Surface defect detection: Suitable for detecting surface cracks, cold seals, porosities and other surface-breaking defects in non-porous materials.
- Complex geometries: Effective on components with complex shapes and geometries.
Benefits
- Versatility: Can be used on a variety of materials, including metals, plastics and ceramics.
- Simplicity: Simple to perform and requires minimal equipment.
Limitations
- Surface cleanliness: Requires thorough cleaning before and after testing.
- Application on non-porous materials: Not applicable on porous materials due to the difficulty of subsequent cleaning for application.
- Size of defects: Less effective for very fine or shallow defects.
Eddy Current Testing (ECT) in foundries
Principle of the test
Eddy Current Testing uses electromagnetic induction to detect surface and near-surface defects in conductive materials. The process involves inducing eddy currents in the component and monitoring changes in the resulting circuit impedance caused by the presence of defects or changes in the electrical properties of the material.
Applications
- Surface crack detection: Effective in detecting surface cracks and discontinuities in non-ferrous and ferrous metals.
- Conductivity measurements: Can be used to measure conductivity and material thickness.
Benefits
- High sensitivity: Sensitive to small surface and near-surface defects and accurate in measurement.
Limitations
- Material limitation: Only applicable to conductive materials.
- Complex interpretation: Requires skilled operators for accurate interpretation.
- Lift Off Effects: Alternating movements of the probe away from the surface of the component cause variations in the signal affecting its interpretation.
Selection of appropriate NDT techniques in the foundry industry
Selecting the appropriate NDT technique in the evaluation of components or castings depends on several factors, including the type of material, the nature of the defects, and the specific inspection requirements. Key considerations include:
- Material type: Different materials respond better to different NDT methods. For example, magnetic particle testing is suitable for ferromagnetic materials, while liquid penetrant testing is versatile on a variety of materials.
- Type of defect: Surface defects can best be detected using magnetic particle testing or liquid penetrant testing, while internal defects are more suitable for ultrasonic or radiographic testing.
- Component geometry: Complex geometries may require techniques such as liquid penetrant testing or eddy current testing for effective inspection.
Training and certification of NDT personnel
The effectiveness of NDT methods depends largely on the skill and experience of the personnel performing the tests. Proper training and certification are essential to ensure accurate and reliable results.
Training programs
Training programs for NDT staff generally cover:
- Basic principles: Understanding of the fundamental principles of various NDT methods.
- Equipment use: Hands-on training in the use of NDT equipment.
- Defect Recognition: Learning to identify and interpret different types of defects.
- Safety procedures: Ensure safe handling and operation of NDT equipment, particularly for radiographic testing.
Certification levels
NDT personnel are certified at various levels, indicating their competence and experience:
- Level I: Basic level, capable of performing specific calibrations and tests under supervision.
- Level II: Intermediate level, capable of configuring and calibrating equipment, performing tests, and interpreting results independently.
- Level III: Advanced level, able to develop NDT procedures, train personnel and perform high-level analysis.
Impact of NDT on quality assurance and production efficiency
The application of NDT in the foundry industry significantly improves quality assurance and production efficiency. By identifying defects early in the production process, foundries can:
- Reduce scrap rates: Early detection of defects minimizes scrap and reduces costs associated with discarding defective components.
- Ensure compliance: NDT helps ensure that cast components meet industry standards and specifications, thereby maintaining compliance with regulatory requirements.
- Improve safety: By verifying the integrity of critical components, NDT helps prevent failures that could lead to accidents or downtime.
- Increase customer satisfaction: Delivering high-quality, defect-free components improves customer satisfaction and builds a reputation for reliability.
Conclusion
Non Destructive Testing is indispensable in the foundry industry, representing a reliable means to ensure the integrity and quality of the casting. The use of these methods in the evaluation of these materials allows to detect defects, reduce waste and improve overall production efficiency. The continued advancement of NDT technologies promises greater accuracy and reliability in the future, further consolidating its role in the foundry industry.
References
- ERMAK. metal casting defects; Accessed June 17, 2024. https://ermak.com/common-metal-casting-defects/#:~:text=Core%20Shift%20%E2%80%93%20A%20core%20shift,cast%20at%20the%20parting%20line.
- NIAGARA INCESTMENT CASTING LTD. Casting shrinkage, why it happens and how to avoid it?; Accessed June 17, 2024. https://niagarainvestmentcastings.com/casting-shrinkage-why-it-happens-and-how-to-avoid-it/
- EVIDENT. Ultrasonic Testing in the Foundry Industry; Accessed June 18, 2024. https://www.olympus-ims.com/en/applications/ultrasonic-testing-foundry-industry/