AWS Standards (American Welding Society) is a global organization that focuses on the different types of welding. It is, therefore, a very important resource that allows welding professionals and industries to better understand and standardize on this subject.
Welding is a significant process in the fabrication and construction of various structures and machinery in different industries, such as aerospace, automotive, and construction. The integrity of a weld is critical to the safety and service life of structures. Nondestructive testing (NDT) provides a way to evaluate the properties of a material or structure without causing damage, making it an indispensable part of welding quality assurance.
The American Welding Society (AWS) sets standards for NDT to ensure that welds meet the highest standards of safety and quality, and has created several certification programs to support the demands of the welding industry. These programs provide individuals and organizations with the credentials necessary to demonstrate their competence and knowledge in specific or related welding fields.
This article discusses AWS Standards in NDT and their role in maintaining weld integrity.
What is Non-Destructive Testing (NDT)?
Non-Destructive Testing are highly effective inspection methods and techniques used to detect and evaluate discontinuities and determine various properties of materials and structures without impairing their future usefulness. The main NDT methods include Visual Testing (VT), Ultrasonic Testing (UT), Magnetic Particle Testing (MT), Radiographic Testing (RT) and Dye Penetrant Testing (PT), Electromagnetic Testing (ET) and Leak Testing (LT)1. Each technique has its specific applications, advantages, and limitations that are chosen based on the type of material, the nature of the weld and the criticality of the component function.
AWS and its role in NDT
The American Welding Society (AWS) is a key player in formulating standards for welding and allied processes, including NDT. AWS provides guidelines, specifications, and certifications that help standardize practices and ensure quality in the welding industry. AWS Standards, are recognized and adopted globally, which speaks to their relevance and rigor in addressing safety and quality issues.
For more on this topic, see this video courtesy of the American Society for Non-Destructive Testing (ASNT).
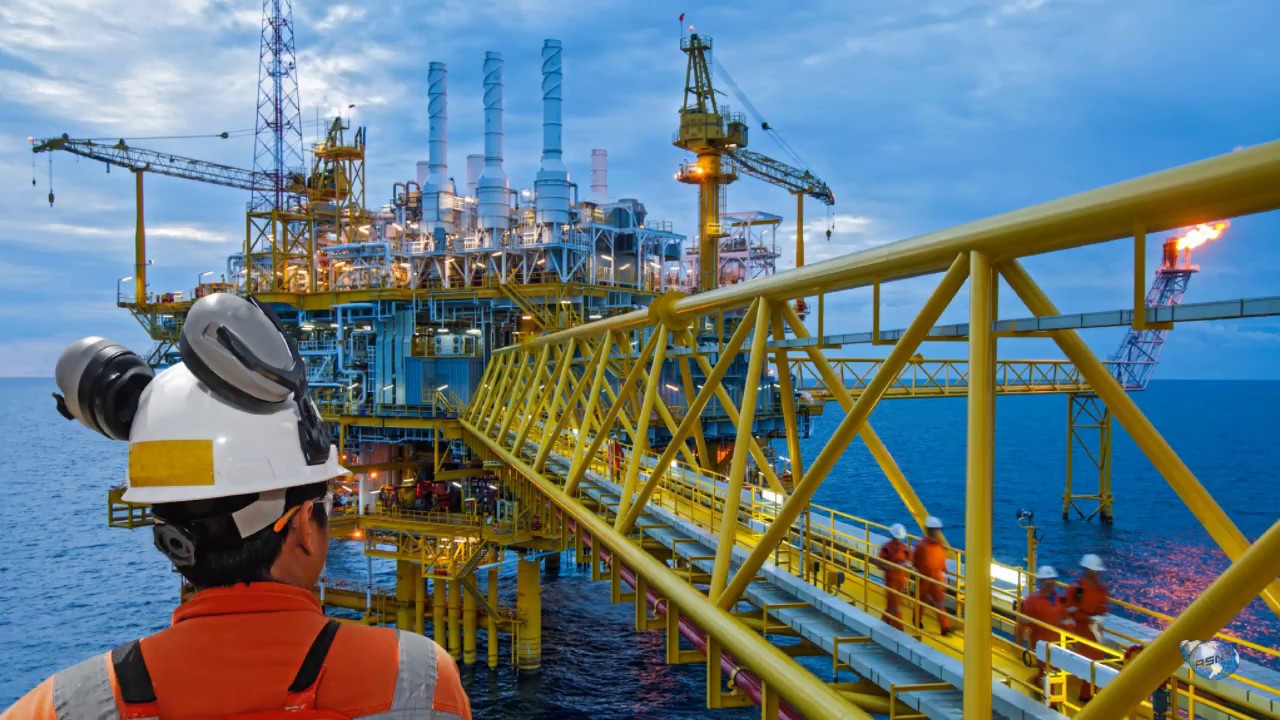
Non-destructive testing is part of AWS’s welding expertise.
AWS Standards for Nondestructive Testing
Below are the standards provided by the American Welding Society (AWS) to ensure weld quality.
AWS D1.1/D1.1M: This is one of the most comprehensive standards provided by AWS, detailing the requirements for welding steel structures. It includes extensive sections on inspection and NDT, specifying when different test methods should be used.
AWS B1.10: This guide offers best practices for examining welds and provides information on how to choose the appropriate NDT method based on the type of weld and the defects likely to occur.
AWS D1.5M/D1.5: This standard applies to bridge welding, highlighting specific NDT methods to ensure the safety and durability of welded bridges.
AWS B1.10M/B1.10: The purpose of this guide is to provide the reader with an overview of the most common examination methods available without unnecessary detail. It also provides assistance in deciding which method is generally best for the examination of a given weld.
Implementing AWS Standards in NDT for welding quality assurance
- Training and Certification: Ensure that NDT personnel are properly trained and certified to AWS Standards. The American Welding Society, offers several certification programs, including Certified Welding Inspector (CWI) and Certified Radiographic Interpreter (CRI)1, in accordance with ASW B5.15:2003, ensures the ability to interpret and evaluate welding indications using radiographs (Figure 1).
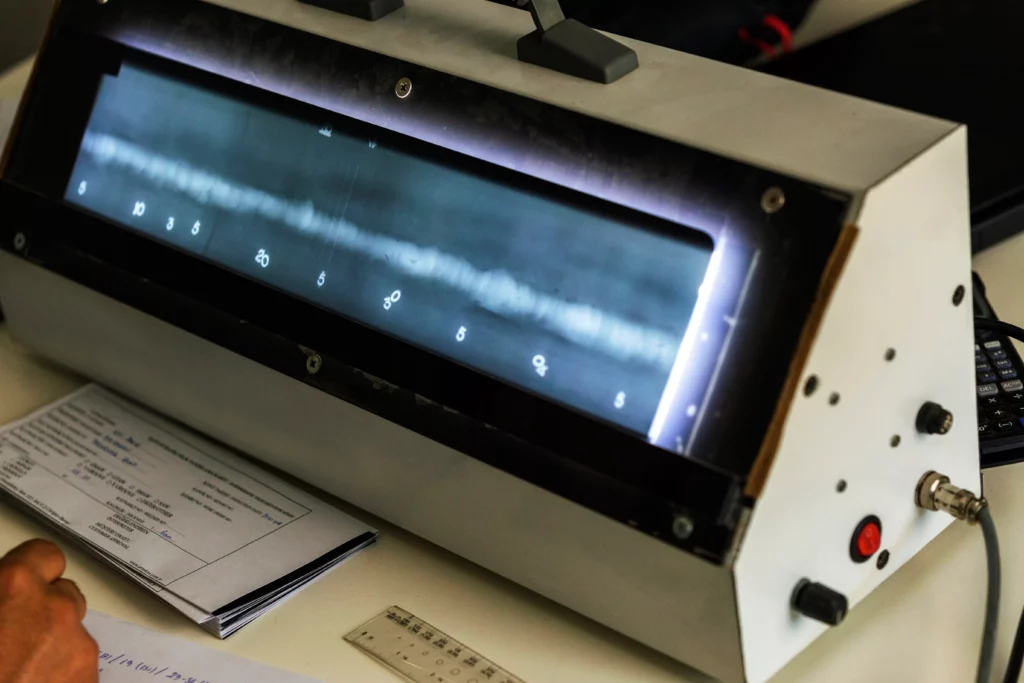
- Selection of suitable NDT methods: Depending on the material, type of construction and the critical nature of the component, selecting the correct NDT method is vital. For example, ultrasonic testing may be preferred for thick sections, while magnetic particle testing may be better suited for detecting surface cracks in ferromagnetic materials.
- Regular inspections and evaluations: Regularly scheduled inspections using AWS-recommended NDT methods aid in the early detection of defects that could develop over time due to operational stresses or environmental factors.
- Compliance and documentation: Maintaining complete records of inspections and NDT results according to AWS Standards aids in regulatory compliance and provides a traceable history of component integrity throughout its life cycle.
Challenges in the application of NDT standards
Although NDT ensures quality and safety, there are challenges in its implementation, the following are the most significant:
- Technological changes: As new welding technologies and materials emerge, updating and adapting NDT methods can be challenging.
- Skills shortage: There is always a need for trained professionals who can perform these specialized tests.
- Cost implications: High-quality NDT can be expensive, especially for small-scale projects or in developing regions.
The future of NDT in welding
The application of these tests in welding looks promising with advances in technology such as automated and real-time NDT systems, which offer more detailed and faster assessments. In addition, the integration of digital technologies with traditional NDT techniques, known as NDT 4.0, is set to improve the accuracy and efficiency of inspections.
Advances in new technologies, such as automated and real-time Non-Destructive Testing (NDT) systems, allow for more detailed and faster evaluations in welding. In addition, the integration of digital technologies with traditional NDT techniques means a significant improvement in the accuracy and efficiency of inspections in the future.
Emerging technologies such as Artificial Intelligence (AI) and machine learning are revolutionizing the way PND is performed. These technologies enable automatic defect recognition, significantly improving the accuracy and speed of inspections.
In addition, the integration of Internet of Things (IoT) devices into NDT systems enables real-time monitoring and data collection. IoT technology helps predict maintenance needs and prevents catastrophic failures by alerting to potential problems before they become critical.
The solution presented in the video below demonstrates weld defect detection using Artificial Intelligence (AI), showing how asset owners can reduce delays, increase productivity and operations by providing asset integrity assurance for operations. This video is courtesy of: TREx Technology Research Excellence.

Weld defect detection using Artificial Intelligence (AI).
Conclusion
AWS Standards in nondestructive testing are significant in ensuring the quality and safety of welded structures. By adhering to these standards, industries can mitigate risks, prevent failures and maintain compliance with safety regulations. As technology advances, NDT methods will evolve, but the core objective will remain the same: to ensure weld integrity for safe and reliable operations. AWS’s commitment to continually refine and adapt these standards ensures that industry practices keep pace with technological advances, ensuring a safer future for all involved in welding-related activities.
References
1.AMERICAN WELDING SOCIETY. Guide for the Nondestructive Examination of Welds; Accessed May 6, 2024.