Table of Contents
- Understanding corrosion in long distance pipelines
- What is In-line Inspection (ILI)?
- Importance in the application of In-Line Inspection (ILI)
- Advantages of In-Line Inspection (ILI) using Smart PIG
- Corrosion integrity assessment: A detailed analysis
- Magnetic Flux Leakage (MFL) Vs Ultrasound (UT) on In-line Inspection
- Conclusions
- References
In-Line inspection (ILI) is one of the most effective and direct techniques, highly demanded today, for determining the actual condition of a pipeline along its entire length. It represents a valuable tool in the maintenance and safety operations of pipelines, which are crucial for transporting oil, gas, and other substances.
Ensuring the integrity of these components is important to prevent environmental disasters, guarantee supply chain consistency, and maintain public safety.
This article delves into the importance of In-Line Inspection (ILI), focusing on integrity assessments for corrosion, which are significant for the long-term sustainability of pipeline infrastructure, emphasizing the use of Pipeline Inspection Gauge (PIG) technology or instrumented tools and describing the same.
Understanding corrosion in long distance pipelines
Corrosion is a natural process that deteriorates materials over time due to environmental interactions. In the context of long-distance pipelines, corrosion can lead to leaks, ruptures, and ultimately failure of the pipeline system. Several factors contribute to pipeline corrosion:
- External corrosion: Occurs due to the interaction of the pipeline with the surrounding environment, such as soil or water.
- Internal corrosion: Caused by the substances transported within the pipeline, particularly if they are corrosive.
- Stress Corrosion Cracking (SCC): Result of the combined influence of tensile stress and a corrosive environment.
- Microbiologically Influenced Corrosion (MIC): It occurs due to the presence and activities of microorganisms.
What is In-line Inspection (ILI)?
ILI is an asset integrity management program that aims to determine the condition of a pipeline and the maintenance required to avoid a critical failure. ILI involves the use of diagnostic tools or pipeline inspection devices, the latter known by its acronym as PIG (Pipeline Inspection Gauge). “Smart PIGs” are embedded devices that travel through the pipeline collecting valuable data on the condition of the pipeline without interrupting operation. Types of ILI tools and their purposes include:
- Magnetic Flux Leakage (MFL) Technology: Detects metal loss and corrosion.
- Ultrasonic Testing Technology (UT):Measures wall thickness and identify cracks, incorporating advanced techniques such as Phased Array Ultrasound for corrosion mapping.
- Gauging instruments: Detects geometric anomalies such as dents and bends.
- Positioning System: This instrument records anomalies during the internal movement of the pipeline using odometers, gyroscope-assisted tilt sensors, and other technologies. The PIG itself cannot utilize GPS due to the metal tube blocking satellite signals1.
The acronym “PIG”, which refers to “Pipeline Inspection Gauge”, should not be translated as “pig” in Spanish or another language, as it would lose its technical meaning and could cause confusion.
There are different types of instrumented tools or smart PIGs used in ILI activities, each with its own set of advantages and disadvantages. Some are more sensitive to detect certain types of corrosion or damage in different types of pipes2, according to their NDT capabilities, others with more efficiency in the production of the service, among other characteristics of interest.
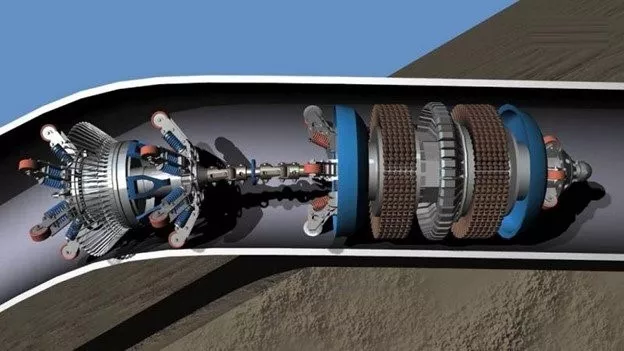
Importance in the application of In-Line Inspection (ILI)
In pipelines, corrosion is primarily caused by factors such as moisture, soil, and the materials transported internally within the pipelines. Corrosion can lead to leaks or catastrophic failures, posing environmental risks and threatening human safety. Periodic assessments of corrosion integrity help mitigate these risks by enabling detection and control.
Several cases have highlighted the effectiveness of corrosion integrity assessments, for example, in long stretches of gas pipelines in a corrosive soil environment, ILI can identify critical areas, and timely interventions prevent significant failure. Conversely, lack of proper ILI assessments can lead to disasters, as seen in historical pipeline incidents. These incidents underscore the importance of consistent and accurate ILI-based assessments.
Carrying out regular cleaning runs inside a pipeline helps identify and repair defects at an early stage, before any leaks or environmental damage occur.
Advantages of In-Line Inspection (ILI) using Smart PIG
Below are several of the most important advantages in using smart PIG or Instrumented Tool in ILI:
- Non-intrusive: ILI tools perform evaluations without interrupting pipeline service.
- Comprehensive data: Provides detailed information about the integrity of the pipeline.
- Preventive maintenance: Helps in planning maintenance before problems become critical.
- Cost-effective: Reduces the need for costly repairs and downtime.
Corrosion integrity assessment: A detailed analysis
A corrosion integrity evaluation involves several steps:
- Pre-evaluation planning: A complete understanding of the pipeline’s history, environment, and operational parameters is necessary prior to ILI. Data on previous incidents, repairs and maintenance activities should be reviewed.
- Selection of the tool for In-Line Inspection: Selection of In-Line Inspection Tool: Choosing the appropriate ILI tool, whether it’s a smart PIG or an instrumented tool with integrated NDT technologies, depends on pipeline size, transported material, efficiency, and sensitivity to types of corrosion. This inspection involves using smart PIGs or instrumented tools with non-destructive examination techniques to assess pipes and conduits for damage.
- Introduction and movement of the smart PIG: The instrumented tool is introduced and collected through specially designed and adapted sections at the ends of the pipeline section to be inspected (launcher and collector), and its movement through the pipeline is taking advantage of the internal service flow. This process is described in more detail in the PIG Movement section.
- Data collection: The smart PIGs equipped with sensors travel through the pipeline, collecting data on pipe wall thickness, corrosion pits, cracks and other anomalies. The data collected provides information on the location and severity of the defect, allowing repair teams to act quickly.
- Data analysis: Advanced software is used to analyze the collected data, identifying areas with corrosion defects that may require additional investigation.
- Integrity assessment: Experts evaluate corrosion data to determine the pipeline’s remaining strength and predict its useful life. They use models that consider factors such as corrosion rate, pipeline stress, and material properties.
- Decision making: Based on the evaluation, decisions are made regarding the need for repairs, replacements or additional protective measures.
- Risk management: A risk assessment is performed to prioritize sections of the pipeline for maintenance. This process involves evaluating the probability and consequences of a failure.
- Maintenance and mitigation: Strategies are implemented to address identified risks, which may include coating repairs, cathodic protection, or replacement of pipeline segments.
- Monitoring and reevaluation: Regular monitoring and periodic reassessments using ILI ensure the continued integrity of the pipeline and adapt maintenance plans as conditions change.
Magnetic Flux Leakage (MFL) Vs Ultrasound (UT) on In-line Inspection
MFL and/or UT test methods are widely integrated into PIGs or instrumented In-Line Inspection (ILI) tools. Each one offers unique characteristics that must be considered for the correct selection of the most suitable method.
Magnetic Field Leakage (MFL)3
- Applicable in liquid and gaseous media (internal service use).
- Speeds from 0.3 m/s to 5 m/s (3 m/s maximum optimal).
- Thicknesses from 4 mm to 32 mm (depends on diameter).
- The resolution depends on the number of sensors.
- Sensitive to the direction of the magnetizing field. In its normal configuration (longitudinal magnetization field) it would only detect circumferential linear discontinuities; for the detection of longitudinal faults, an extra arrangement of magnetic field and sensors is required.
Below is a video courtesy of Rosen Group, demonstrating the Launching & Receiving an In-Line Inspection of an intelligent device through a pipeline.
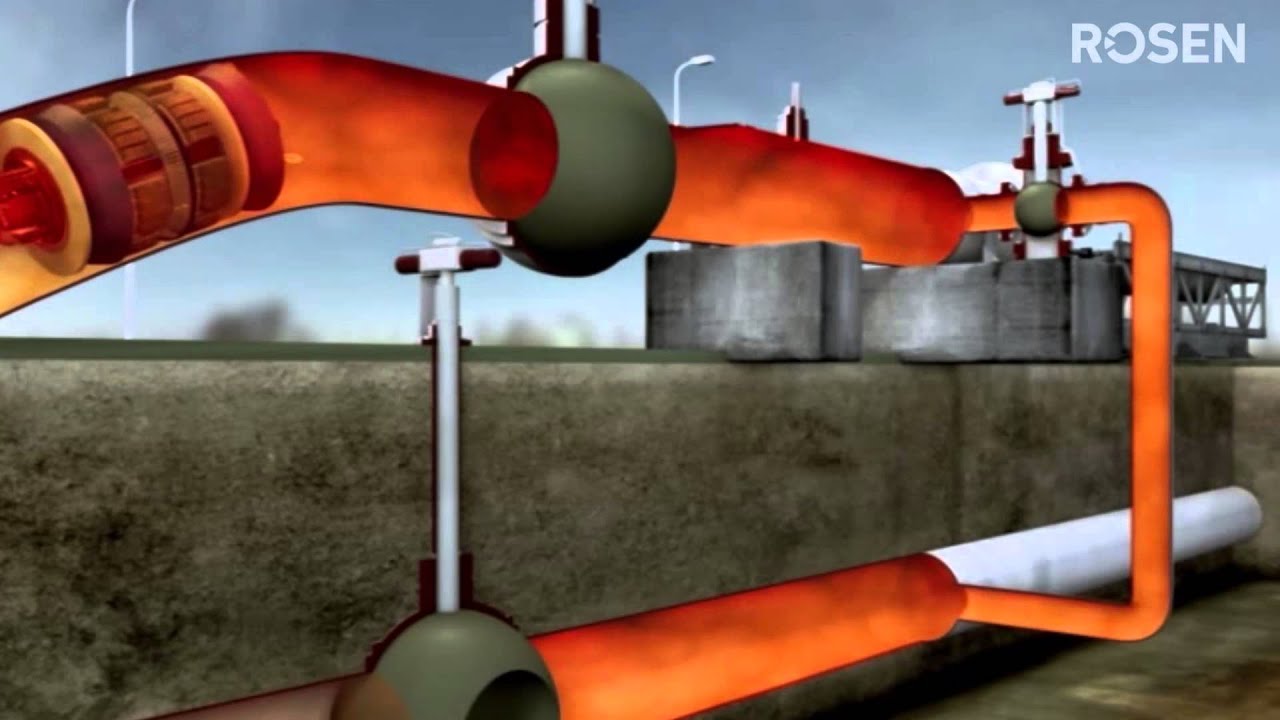
Launching & Receiving an In-Line Inspection Tool.
Ultrasound (UT)3
- Applicable only in homogeneous liquid media (use of the fluid).
- Deep external pits require a minimum thickness for detection.
- Speeds up to 2.5 m/s (1 m/s optimal).
- Thickness from 5 to 45 mm.
- Requires a higher degree of cleaning.
- Well-defined C-Scan images which meet the requirements of API 579 (Fitness For Service) for level calculations when applied.
The following video shows NDT Global’s in-line ultrasonic pipe inspection process to determine and detect the loss of metal wall thickness due to corrosion. Courtesy of NDT Global.
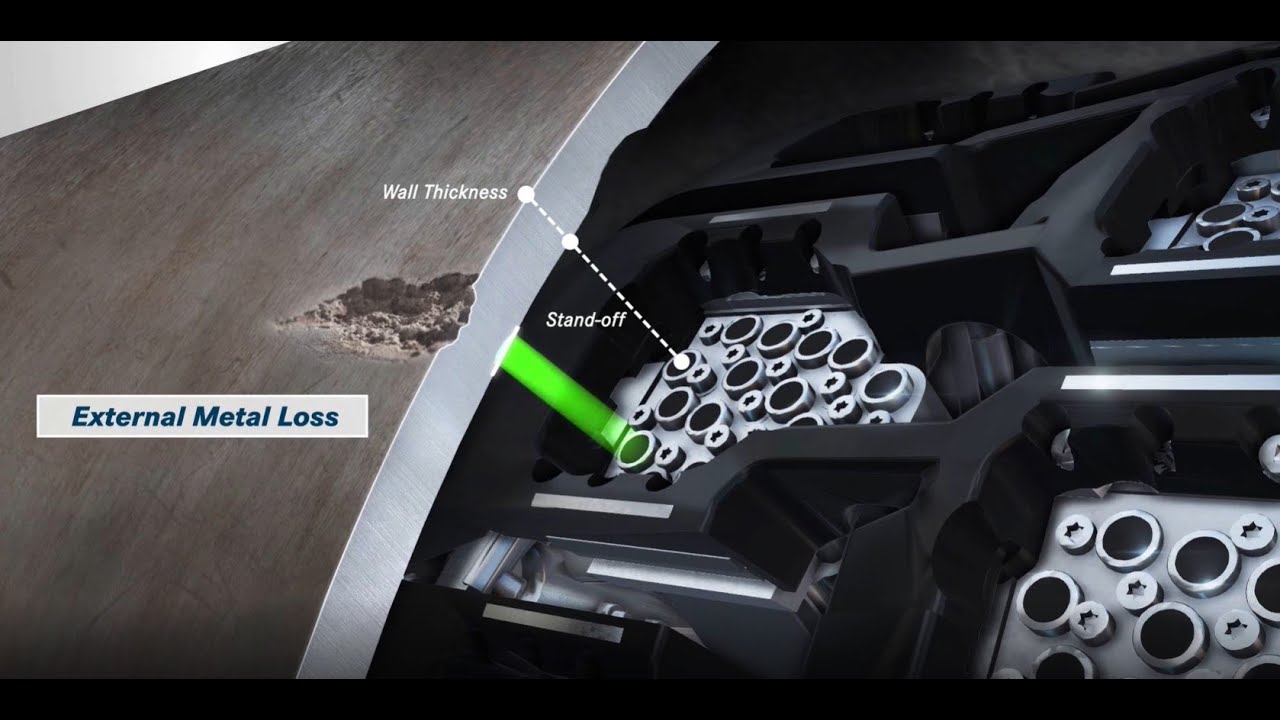
In-line ultrasonic inspection of a pipeline.
In recent years, some manufacturers are combining the various functions of these separate tools into one. In this way, a single tool can now be used to detect several different types of damage, making it more efficient and effective.
The smart PIG in motion
Passing PIGs through pipes works a little differently in liquid and gas pipes. Both pipelines have launchers and receivers installed, like a T outside the main pipeline. These sections are slightly larger than the pipe size, which can range from 4” to 48” in diameter4.
This allows inspection teams to safely load or remove PIGs. Once the PIG is in the barrel of the launcher, the cup on the front of the tool is fitted against the diameter of the pipe and the flow of oil or gas is controlled to move the PIG along the pipe and provide Accurate readings during the ride.
In a gas pipeline, the cups act like the sail of a sailboat that traps the wind in its sails. Natural gas flows through the pipeline, gets trapped in the cup, and pushes against the PIG. The speed of the instrument can be managed by controlling the gas flow rate in the pipe or by opening the cup in the middle to allow some of the gas to flow. Since oil is not compressible like gas, the tool must operate at the velocity of the liquid in the line. The cup is sealed against the sides of the pipe and is pushed, as if riding an underwater current.
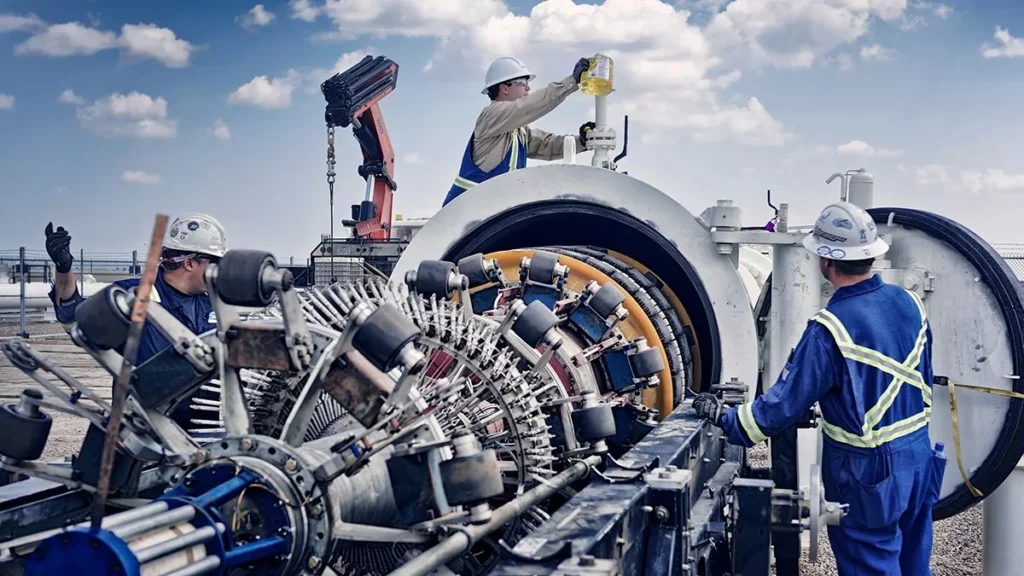
Conclusions
In-Line Inspection (ILI) involves assessing pipes and pipelines using smart PIGs integrating non-destructive testing techniques to detect and size internal damage, record irregularities, corrosion, deformations, or other defects. It is a process that requires advanced technology, expert analysis, and strategic planning.
The role of pipelines is significant in the global economy and energy supply, underscoring the importance of these assessments. Through continuous innovation and adherence to best practices in ILI, the industry can ensure the safe and efficient operation of long-distance pipelines in the years ahead.
References
- CLAIRE MARCHAND. Smart pigs essential for detecting pipeline problems; Accessed on April 22, 2024; https://etech.iec.ch/issue/2020-04/smart-pigs-essential-to-the-detection-of-pipeline-problems
- ASSET INTEGRITY ENGINEERING. Unpiggable pipelines – the industry-wide challenge; Accessed on April 22, 2024; https://www.assetintegrityengineering.com/unpiggable-pipelines-the-industry-wide-challenge/
- DELFÍN RODRÍGUEZ. MFL vs UT for pipeline inspection (video); Accessed on April 23, 2024; https://www.youtube.com/watch?v=pkEd_iU_pts
- TC ENERGY. How we see inside our pipes with intelligent machines; Accessed on April 23, 2024; https://www.tcenergy.com/about/explore-energy/understanding-how-it-works/how-we-see-inside-our-pipes-with-intelligent-machines/#:~:text=Smart%2Dpigs%20are%20data%20capturing,a%20clear%20and%20accurate%20reading.