Corrosion in multiphase environments represents one of the most significant and costly challenges for the oil and gas industry. Multiphase systems or emulsions (water/hydrocarbon) are the primary cause of corrosion due to the density difference between phases, and transportation flow increases corrosiveness, compromising structural integrity, safety, and operational efficiency. The complex nature of these environments demands suitable strategies to mitigate corrosion and prolong asset life.
This article focuses on integrating key strategies for corrosion control, including protective coatings, development of resistant alloys, and operational optimization to combat corrosion mechanisms. This combination of technologies ensures comprehensive protection against corrosive mechanisms by addressing initial prevention and long-term structural resilience, contributing to an effective corrosion control strategy in critical oil and gas applications.
Understanding multiphase environments
Multiphase environments in the oil and gas industry comprise complex systems where liquid and gas phases coexist, including water, hydrocarbons, and acidic gases such as carbon dioxide (CO2), hydrogen sulfide (H2S), and oxygen (O2). This coexistence of phases creates a dynamic scenario where interactions between components can significantly accelerate corrosion processes, challenging the integrity and reliability of infrastructure and equipment.
The presence of water, even in minimal amounts, acts as an electrolyte facilitating the electron transfer necessary for electrochemical corrosion processes. Hydrocarbons, on the other hand, can serve as a physical barrier protecting metal surfaces, or they can transport dissolved acids that, upon contact with water, increase the medium’s aggressiveness. Dissolved acidic gases, especially CO2 and H2S, directly contribute to acidic corrosion by forming strong acids upon contact with water that attack metal surfaces. H2S, in particular, is known to induce sulfide stress corrosion, a particularly destructive type of degradation.
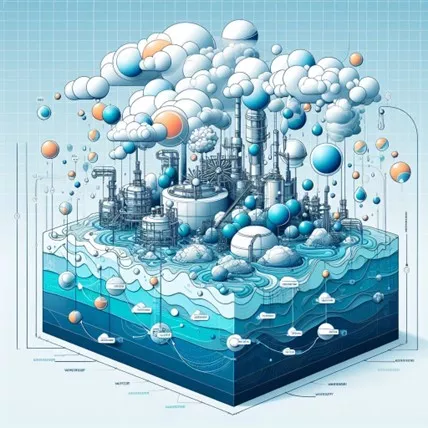
The interaction between these phases and components is not static and varies significantly with operational conditions such as temperature, pressure, and chemical composition of the medium. These variables alter the solubility and mobility of corrosive components, directly affecting the rate and type of corrosion observed. Furthermore, turbulence and flow within multiphase systems can lead to erosion-corrosion, where mechanical removal of the protective film by suspended particles or gas bubbles accelerates the corrosive attack.
Understanding the dynamics of multiphase environments and their impact is fundamental to developing effective mitigation strategies. This requires a comprehensive approach that considers both chemical interactions and operational conditions, aiming to minimize the presence and corrosive effect of harmful components while maximizing the effectiveness of protection systems.
Corrosion in multiphase environments control strategies
Advanced coatings and their effectiveness
Advanced coatings represent the first line of defense against corrosion in the oil and gas industry. They are designed to create a physical barrier that prevents contact between corrosive materials and the metal surface. Innovation in this field has led to the development of coatings with specific chemical compositions capable of providing protection in extremely corrosive environments.
The effectiveness of these coatings is grounded in their ability to adhere firmly to metal surfaces, form dense and homogeneous protective films, and withstand the chemical and mechanical effects of the operating environment. Recent innovations include nanostructured coatings that enhance corrosion resistance and durability, as well as smart coatings capable of self-repair or changing their properties in response to external stimuli such as variations in pH or temperature.
Corrosion resistant alloys
Corrosion-resistant alloys represent an advanced material solution where chemical composition and microstructure are optimized to withstand the specific corrosive environments of the oil and gas sector. These alloys often incorporate elements such as chromium, nickel, molybdenum, and titanium, which enhance corrosion resistance by forming passive films or improving structural stability.
Recent developments focus on high-entropy alloys, which offer exceptional properties due to their unique crystalline structure and homogeneous distribution of multiple principal elements. These alloys not only demonstrate superior corrosion resistance but also notable mechanical strength and fatigue resistance, making them suitable for applications under severe operating conditions.
Process optimization and operations management
Effective management of operations and processes is crucial for minimizing the risk of corrosion. This includes the proper design of systems to avoid stagnant zones where corrosion products accumulate, preventive maintenance to ensure the integrity of coatings and alloys, and continuous monitoring of operating conditions to detect early signs of corrosion.
Recommended practices involve the use of real-time corrosion detection systems that enable proactive operational adjustments, implementation of cleaning procedures to remove corrosive deposits, and adoption of flow control strategies to minimize erosion-corrosion. Furthermore, careful selection of materials and application of appropriate surface treatments can significantly enhance corrosion resistance of critical components.
Optimizing these processes reduces corrosion mechanisms and extends asset life, improves safety and operational efficiency, and reduces costs associated with maintenance and equipment replacement. The key lies in an integrated strategy that combines advanced material technologies with effective management and maintenance.
These strategies represent a comprehensive and multidisciplinary approach to combating corrosion in the oil and gas industry, highlighting the importance of technological innovation and smart operational management in preserving the integrity and functionality of control systems corrosion in multiphase environments.
Innovation and future in corrosion control
In the future, corrosion mitigation in the oil and gas sector is focusing on integrating technological innovations. Specifically, advancements in smart materials and advanced monitoring systems are promising to transform corrosion protection. These advancements enable materials to self-repair or adapt their properties in response to environmental changes, offering dynamic and highly effective corrosion solutions.
Simultaneously, real-time monitoring systems, powered by data analysis and artificial intelligence, provide an unprecedented window for proactive corrosion detection and management, enabling precise and timely interventions. These technological innovations enhance corrosion detection and prevention, ushering in an era of predictive maintenance. Strategic decisions are based on detailed and real-time analysis, significantly improving sustainability and operational efficiency.
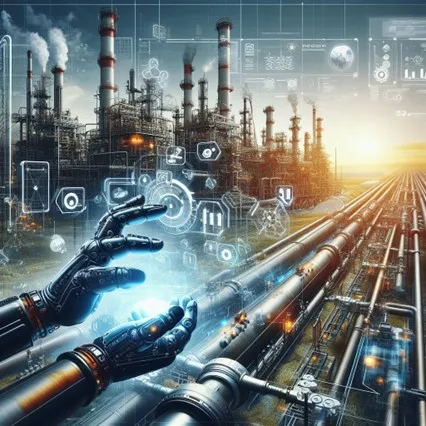
monitoring systems.
Smart materials
Smart materials, also known as active or adaptive materials, are those capable of changing their properties in response to external environmental stimuli. These stimuli can include variations in temperature, pressure, humidity, pH, electric fields, or magnetic fields, among others. The response of smart materials to these stimuli allows them to adapt to new conditions, making them extremely useful in a wide range of technological and scientific applications. Examples of smart materials include:
- Shape Memory Alloys: These materials can return to their original shape after deformation simply by a change in temperature. They are used in medical applications such as coronary stents, in actuation elements in the aerospace industry, and in the Oil & Gas sector with materials like Nitinol (a nickel-titanium alloy), valued for their durability, corrosion resistance, and especially for their shape memory properties and superelasticity.
- Stimuli-Responsive Polymers: These materials change their physical or chemical properties in response to changes in the environment such as pH, temperature, or light. They are applied in controlled drug release systems and as sensors.
- Piezoelectricity in Ceramic and Polymer Materials: These materials generate a voltage when subjected to mechanical pressure and vice versa, which is useful in creating sensors, actuators, and energy harvesters.
- Magnetostrictive Materials: They change shape or dimensions in the presence of a magnetic field. They are used in industrial applications for precision devices such as sensors and actuators.
- Photochromic Materials: These materials change color when exposed to light, with applications in sunglasses that automatically darken under intense sunlight.
- Hydrogels: Capable of absorbing large amounts of water and changing their mechanical properties in response to variations in humidity, temperature, or pH. They are used in biomedical applications and as soft actuators.
- Liquid Crystals: Substances that can change their optical properties in response to a change in temperature, electrical voltage, etc., making them useful in electronic device displays.
- Nanomaterials: At the nanoscale, many materials exhibit unique properties that can be controlled for specific applications, including targeted drug delivery and high-sensitivity sensors.
Real-Time Monitoring Systems, Data Analysis, and Artificial Intelligence
The implementation of real-time monitoring systems to combat corrosion represents a significant innovation in the maintenance and protection of critical infrastructure in sectors such as oil and gas, chemical industry, and civil engineering. These systems utilize a combination of advanced sensors and data analytics platforms to provide detailed and continuous insight into the corrosion status of materials and structures.
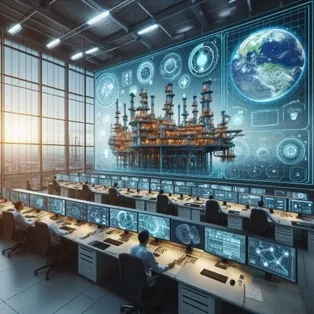
Operation and components
Real-time monitoring systems are based on the installation of sensors at critical points of structures or pipelines susceptible to corrosion. These sensors can measure a variety of parameters, such as environmental acidity (pH), presence of chloride ions, temperature, humidity, and concentration of corrosive gases like CO2 and H2S. The collected information is transmitted to a centralized system where it is analyzed in real-time, allowing for early detection of conditions conducive to corrosion.
Artificial iintelligence in monitoring
The incorporation of artificial intelligence (AI) and machine learning (ML) into these systems enhances their predictive and diagnostic capabilities. Through the analysis of large volumes of historical and real-time data, AI algorithms can identify patterns and trends indicating the onset of corrosion long before it becomes detectable by traditional methods. This enables not only early intervention but also the prediction of future corrosion sites based on the past and present behavior of the structure.
Conclusions
Corrosion in multiphase environments poses a threat to asset structural integrity and represents a significant risk to operational safety and economic efficiency. However, through innovations and strategies, a new era in corrosion control is emerging.
To withstand the aggressiveness of severe environments, the integration of advanced coatings and corrosion-resistant alloys has been achieved through science and engineering, creating robust solutions. Beyond material considerations, process optimization and intelligent operations management are key alternatives, ensuring the effective implementation of these innovations and supporting a regime of proactive maintenance.
The oil and gas sector faces a crossroads of challenges and opportunities. Armed with the right knowledge and tools, we are poised to move towards a future where corrosion, though inevitable, can be effectively managed, ensuring the sustainability and resilience of our industry against tomorrow’s challenges.
References
Own source.