La corrosión en ambientes multifases representa uno de los problemas más significativos y costosos para la industria del petróleo y gas. Los sistemas multifásicos o emulsiones (solución/hidrocarburo) es la causa principal de corrosión por la diferencia de densidad que existe entre las fases de estas mezclas, además el flujo, para su trasporte, aumenta el impacto de la corrosividad, comprometiendo la integridad estructural, la seguridad y la eficiencia operativa. La naturaleza complicada de estos ambientes requiere estrategias adecuadas para mitigar la corrosión y prolongar la vida útil de los activos.
Este artículo se centra en la integración de estrategias importantes para el control de la corrosión, entre las que se incluyen los recubrimientos protectores, el desarrollo de aleaciones resistentes y la optimización de operaciones para combatir los mecanismos de corrosión. Esta combinación de tecnologías garantiza una protección integral contra los mecanismos corrosivos al abordar la prevención inicial y la resistencia estructural a largo plazo, contribuyendo así a una estrategia efectiva para controlar la corrosión en aplicaciones críticas del sector del petróleo y gas.
Comprendiendo los ambientes multifases
Los ambientes multifases en la industria del petróleo y gas comprenden sistemas complejos donde coexisten fases líquidas y gaseosas, incluyendo agua, hidrocarburos y gases ácidos como el dióxido de carbono (CO2), el sulfuro de hidrógeno (H2S) y el oxígeno (O2). Esta coexistencia de fases crea un escenario dinámico donde las interacciones entre los componentes pueden acelerar significativamente los procesos de corrosión, desafiando la integridad y la fiabilidad de la infraestructura y los equipos.
La presencia de agua, incluso en cantidades mínimas, actúa como un electrolito que facilita la transferencia de electrones necesaria para los procesos electroquímicos de la corrosión. Los hidrocarburos, por otro lado, pueden tanto servir de barrera física que protege las superficies metálicas, como transportar ácidos disueltos que, al entrar en contacto con el agua, aumentan la agresividad del medio. Los gases ácidos disueltos, especialmente el CO2 y el H2S, contribuyen directamente a la corrosión ácida, formando ácidos fuertes en contacto con el agua que atacan las superficies metálicas. El H2S, en particular, es conocido por inducir la corrosión por sulfuro, un tipo de deterioro particularmente destructivo.
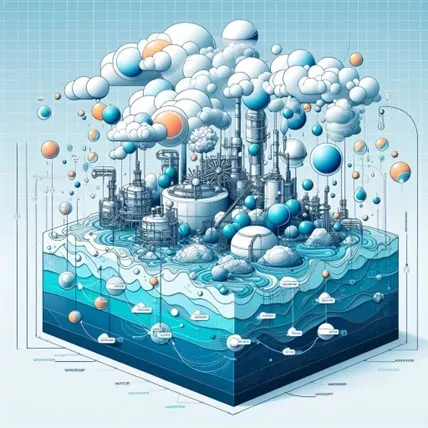
La interacción entre estas fases y componentes no es estática y varía significativamente con las condiciones operativas, como la temperatura, la presión y la composición química del medio. Estas variables alteran la solubilidad y la movilidad de los componentes corrosivos, afectando directamente la tasa y el tipo de corrosión observado. Además, la turbulencia y el flujo de los sistemas multifase pueden provocar la erosión-corrosión, donde la remoción mecánica de la película protectora por partículas en suspensión o burbujas de gas acelera el ataque corrosivo.
Entender la dinámica de los ambientes multifases y su impacto es fundamental para desarrollar estrategias efectivas de mitigación. Esto requiere un enfoque integral que considere tanto las interacciones químicas como las condiciones operativas, apuntando a minimizar la presencia y el efecto corrosivo de los componentes dañinos, al tiempo que se maximiza la eficacia de los sistemas de protección.
Estrategias de control de la corrosión en ambientes multifases
Recubrimientos avanzados y su eficacia
Los recubrimientos avanzados son la primera línea de defensa contra la corrosión en la industria del petróleo y gas. Están diseñados para crear una barrera física que impida el contacto entre los materiales corrosivos y la superficie del metal. La innovación en este campo ha llevado al desarrollo de recubrimientos con composiciones químicas específicas capaces de ofrecer protección en ambientes extremadamente corrosivos.
La eficacia de estos recubrimientos se fundamenta en su capacidad para adherirse firmemente a las superficies metálicas, formar películas protectoras densas y homogéneas, y resistir los efectos químicos y mecánicos del entorno operativo. Las innovaciones recientes incluyen recubrimientos nanoestructurados que mejoran la resistencia a la corrosión y la durabilidad, y recubrimientos inteligentes capaces de repararse a sí mismos o cambiar sus propiedades en respuesta a estímulos externos, como variaciones en el pH o la temperatura.
Aleaciones resistentes a la corrosión
Las aleaciones resistentes a la corrosión representan una solución material avanzada, donde la composición química y la microestructura están optimizadas para resistir los ambientes corrosivos específicos del sector petrolero y gasífero. Estas aleaciones suelen incorporar elementos como el cromo, níquel, molibdeno, y titanio, los cuales mejoran la resistencia a la corrosión mediante la formación de películas pasivas o la mejora de la estabilidad estructural.
Los desarrollos recientes se centran en aleaciones de alta entropía, las cuales ofrecen propiedades excepcionales gracias a su estructura cristalina única y la distribución homogénea de múltiples elementos principales. Estas aleaciones no solo demuestran una resistencia superior a la corrosión, sino también una notable resistencia mecánica y a la fatiga, haciéndolas idóneas para aplicaciones bajo condiciones operativas severas.
Optimización de procesos y manejo de operaciones
La gestión eficaz de las operaciones y los procesos es vital para minimizar el riesgo de corrosión. Esto incluye el diseño adecuado de sistemas para evitar zonas de estancamiento donde se depositan productos de corrosion, el mantenimiento preventivo para asegurar la integridad de recubrimientos y aleaciones, y la monitorización constante de las condiciones operativas para detectar tempranamente signos de corrosión.
Las prácticas recomendadas incluyen el uso de sistemas de detección de corrosión en tiempo real que permiten ajustes operativos proactivos, la implementación de procedimientos de limpieza para eliminar depósitos corrosivos, y la adopción de estrategias de control de flujo para minimizar la erosión-corrosión. Además, la selección cuidadosa de materiales y la aplicación de tratamientos superficiales adecuados pueden mejorar significativamente la resistencia a la corrosión de los componentes críticos.
La optimización de estos procesos reduce los mecanismos de corrosión, y por ende la vida útil de los activos, mejora la seguridad y la eficiencia operativa, y reduce los costos asociados con el mantenimiento y la sustitución de equipos. La clave está en una estrategia integrada que combine tecnologías avanzadas de materiales con una gestión y mantenimiento eficaces.
Estas estrategias representan un enfoque comprensivo y multidisciplinario para combatir la corrosión en la industria del petróleo y gas, destacando la importancia de la innovación tecnológica y la gestión operativa inteligente en la preservación de la integridad y la funcionalidad de los sistemas contra la corrosión en ambientes multifases.
Innovación y futuro en el control de la corrosion
En el futuro, la mitigación de la corrosión en el sector petrolero y gasífero se enfoca en integrar innovaciones tecnológicas. Específicamente, avances en materiales inteligentes y sistemas de monitorización avanzados están prometiendo transformar la protección contra la corrosión. Estos avances permiten la auto-reparación de los materiales o la adaptación de sus propiedades en respuesta a cambios ambientales, ofreciendo así soluciones dinámicas y altamente efectivas contra la corrosión.
Paralelamente, los sistemas de monitorización en tiempo real, potenciados por el análisis de datos y la inteligencia artificial, ofrecen una ventana sin precedentes para la detección y gestión proactiva de la corrosión, permitiendo intervenciones precisas y oportunas. Estas innovaciones tecnológicas mejoran la detección y prevención de la corrosión, marcando el inicio de una era de mantenimiento predictivo. Decisiones estratégicas se basan en análisis detallados y en tiempo real, lo que mejora significativamente la sostenibilidad y la eficiencia operativa.
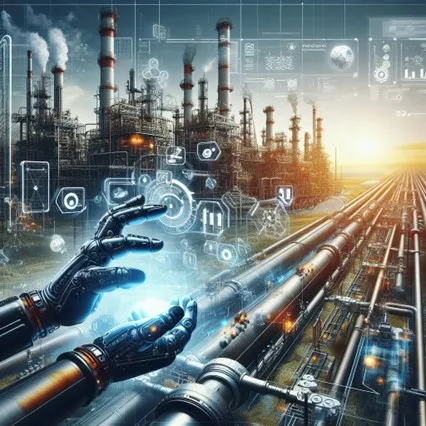
Materiales inteligentes
Los materiales inteligentes, también conocidos como materiales activos o adaptables, son aquellos que tienen la capacidad de cambiar sus propiedades en respuesta a estímulos externos del medio ambiente. Estos estímulos pueden ser variaciones de temperatura, presión, humedad, pH, campos eléctricos o magnéticos, entre otros. La respuesta de los materiales inteligentes a estos estímulos les permite adaptarse a nuevas condiciones, haciéndolos extremadamente útiles en una amplia gama de aplicaciones tecnológicas y científicas. Algunos ejemplos de materiales inteligentes incluyen:
- Aleaciones con memoria de forma: Estos materiales pueden volver a su forma original después de ser deformados, simplemente con un cambio de temperatura. Se utilizan en aplicaciones médicas como stents coronarios, en elementos de actuación en la industria aeroespacial y en el sector Oil & Gas con materiales como el Nitinol (una aleación de níquel-titanio), valoradas por su durabilidad, resistencia a la corrosión y, sobre todo, por sus propiedades de memoria de forma y superelasticidad.
- Polímeros sensibles a estímulos: Varian sus propiedades físicas o químicas en respuesta a cambios en el medio ambiente como el pH, la temperatura o la luz. Se aplican en sistemas de liberación controlada de fármacos y como sensores.
- Piezoelectricidad en materiales cerámicos y polímeros: Estos materiales generan un voltaje cuando se les aplica una presión mecánica y viceversa, lo cual es útil en la creación de sensores, actuadores y generadores de energía.
- Materiales magnetostrictivos: Cambian de forma o dimensiones en presencia de un campo magnético. Se utilizan en aplicaciones industriales para la creación de dispositivos de precisión como sensores y actuadores.
- Materiales fotocrómicos: Al ser expuestos a la luz, varian su color, tienen aplicaciones en lentes de sol que se oscurecen automáticamente bajo la luz solar intensa.
- Materiales hidrogélicos: Absorben grandes cantidades de agua y cambiar sus propiedades mecánicas en respuesta a variaciones en la humedad, la temperatura o el pH. Son utilizados en aplicaciones biomédicas y como actuadores suaves.
- Cristales líquidos: Sustancias que pueden cambiar sus propiedades ópticas en respuesta a un cambio en temperatura, voltaje eléctrico, etc., lo que los hace útiles en pantallas de dispositivos electrónicos.
- Nanomateriales: A escala nanométrica, muchos materiales exhiben propiedades únicas que pueden ser controladas para aplicaciones específicas, incluyendo la liberación dirigida de medicamentos y sensores de alta sensibilidad.
Sistemas de monitorización en tiempo real, análisis de datos y la inteligencia artificial
La implementación de sistemas de monitorización en tiempo real para combatir la corrosión representa una innovación significativa en el mantenimiento y protección de infraestructuras críticas en sectores como el petróleo y gas, la industria química, y la ingeniería civil. Estos sistemas utilizan una combinación de sensores avanzados y plataformas de análisis de datos para proporcionar una comprensión detallada y continua del estado de corrosión de los materiales y estructuras.
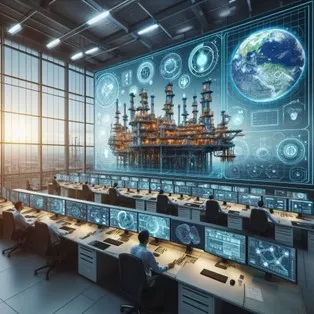
Funcionamiento y componentes
Los sistemas de monitorización en tiempo real se basan en la instalación de sensores en puntos críticos de las estructuras o tuberías susceptibles a la corrosión. Estos sensores pueden medir una variedad de parámetros, como la acidez (pH) del entorno, la presencia de iones cloruro, la temperatura, la humedad, y la concentración de gases corrosivos como el CO2 y el H2S. La información recabada se transmite a un sistema centralizado donde se analiza en tiempo real, permitiendo la detección temprana, de condiciones que favorezcan la corrosión.
La inteligencia artificial en la monitorización
La incorporación de la inteligencia artificial (IA) y el aprendizaje automático (Machine Learning, ML) en estos sistemas amplifica su capacidad de predicción y diagnóstico. A través del análisis de grandes volúmenes de datos históricos y en tiempo real, los algoritmos de IA pueden identificar patrones y tendencias que indican el inicio de la corrosión mucho antes de que se vuelva detectable por métodos tradicionales. Esto permite no solo una intervención temprana sino también la predicción de futuros sitios de corrosión basándose en el comportamiento pasado y presente de la estructura.
Conclusiones
La corrosión en ambientes multifases es una amenaza la integridad estructural de los activos, y representa un riesgo significativo para la seguridad operativa y la eficiencia económica. Sin embargo, a través de innovaciones y estrategias se presenta una nueva era en la lucha contra la corrosión.
Para resistir la agresividad de ambientes severos, a través de la ciencia y la ingeniería se ha logrado la integración de recubrimientos avanzados y aleaciones resistentes para crear soluciones robustas. Más allá de la materia, la optimización de procesos y el manejo inteligente de operaciones surgen alternativas clave, asegurando la aplicación efectiva de estas innovaciones y sustentando un régimen de mantenimiento proactivo.
El sector del petróleo y gas se encuentra en una encrucijada de desafíos y oportunidades. Armados con el conocimiento y las herramientas correctas, estamos preparados para avanzar hacia un futuro donde la corrosión, aunque inevitable, puede ser gestionada de manera eficaz, asegurando la sostenibilidad y la resiliencia de nuestra industria frente a los desafíos del mañana.
Referencias
Fuente propia.