Introduction
In the oil and gas industry, the optimization of steam systems is essential to reduce costs, maximize energy efficiency and contribute to environmental sustainability. These systems are used to ensure energy efficiency in refining processes for hydrocarbon transformation. A thorough understanding of the steam line care required to maintain steam line thermal efficiency is significant to achieving sustainable and economically viable production goals.
Energy efficiency in the oil industry depends to a large extent on the implementation of preventive controls in steam lines. This practice not only ensures the reliability and safety of operations, but also optimizes energy consumption and minimizes CO2 emissions, in line with global environmental standards.
In this context, we will learn about the main energy sources used in industrial processes where steam is included, the importance of steam lines in refining processes and the best practices to obtain a better performance of steam systems, which guarantee an efficient heat transfer, with the purpose of maintaining an adequate management of these systems, resulting in tangible improvements for the best energy performance of the oil environment.
Steam as an energy source in refining processes
There are three main forms of energy used in industrial processes: electricity, direct combustion heat and steam. Electricity is applied in various forms, including mechanical actuation, heating and electrochemical reactions. Direct combustion energy directly transfers heat from fuel combustion to a process. The third form is steam, which is used to heat processes, control pressures, separate components and perform mechanical drives, and is also used for many process reactions1.
Steam is an indispensable source of energy in refining processes, its performance over other energy sources is outstanding and it has advantages such as ease of transport, low toxicity, high calorific value, high efficiency and low cost compared to other options.
Steam systems are mainly made up of four processes: generation, which occurs in a boiler or steam generator with heat recovery; distribution, which uses lines to transport the steam; end use, where it reaches equipment such as exchangers, turbines, fractionating towers, separators and chemical reaction vessels; and then the recovery process through condensate return systems to the boilers. Figure 1 shows the schematic of a steam system.
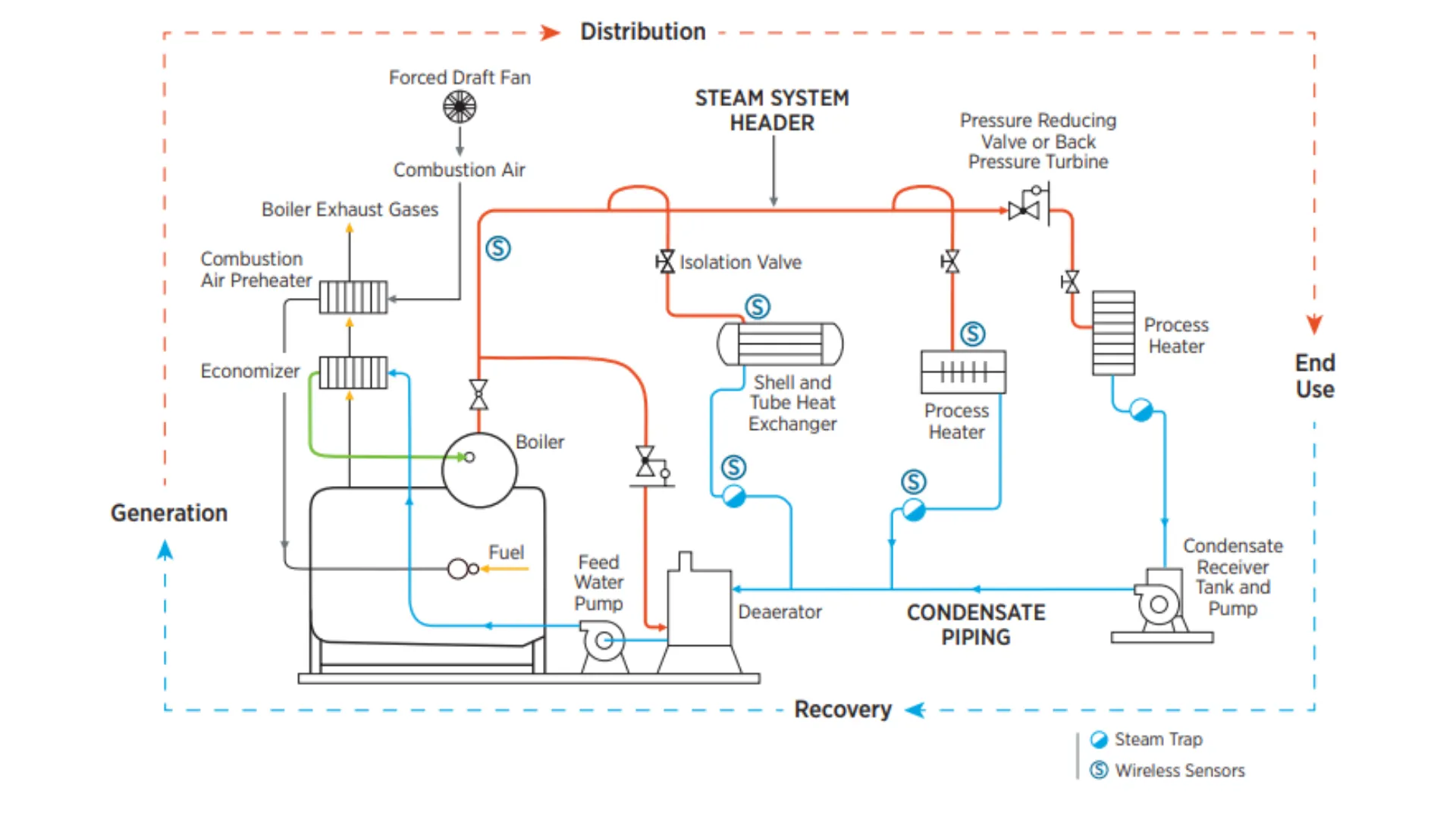
Importance of steam lines in the refining process
Although steam lines are usually quite reliable, they must be properly maintained because their efficiency directly influences energy consumption, operating costs, process safety and environmental impact. Utilizing the full capacity of steam as it is distributed to the various refining processes contributes greatly to energy efficiency and the reduction of greenhouse gas emissions, both of which are currently key to achieving decarbonization goals.
These considerations underline the importance of optimal operation of steam lines, not only in terms of optimizing energy consumption but also to maintain excellence and maximum capacity in the refining processes. Efficient steam systems minimize the risk of operational downtime and ensure constant process temperatures, which are critical to the quality and safety of refined products.
Inadequate management and maintenance of steam lines can result in considerable energy losses and increased operational risks, highlighting the need to implement preventive maintenance and adopt constant care measures.
Practices to improve the performance of steam systems
The care of steam lines, mainly high-pressure lines, goes beyond energy efficiency and includes improving process reliability and safety. Efficient use of steam and process control optimizes line operation. There are several factors that must be monitored and controlled to achieve maximum performance from these systems. The following highlights several practices that improve steam line performance and in many cases reduce operating costs.
Steam system analysis
The integral analysis of the steam network in a refining plant allows to achieve a complete efficiency of the thermal cycle and therefore a better energetic and operational performance. This analysis is the most effective way to know the general conditions of the system; that is, the operational variables and the mechanical conditions of the elements; and it must be performed in the four phases of the system: steam generation, distribution, final use and condensate recovery system.
When a steam network analysis is performed, it ensures that the end use of steam is adequate, i.e. the processes that consume steam obtain the correct amount of energy at the required pressure, temperature and quality. Systems that achieve optimum steam have no energy losses unless there are steam line leaks, excessive low-pressure steam blowdowns or flash steam blowdowns, and condensate loss. Steam system analysis is the first step towards obtaining a balance of steam variables for maximum thermal efficiency.
Regular maintenance
Implementing preventive maintenance programs ensures the optimal performance of system components such as lines, traps, valves and other devices. These actions prevent leaks in steam lines and the consequent loss of energy. Maintenance activities include cleaning of steam fleas and valves, replacement of elements, as well as inspection of steam lines for leaks, insulation damage, corrosion under insulation or any other problem that compromises the energy performance of the system.
By avoiding or minimizing energy leakage and waste, operating costs and environmental impact are reduced. In a maintenance program, it is advisable to comply with the guidelines indicated by the equipment manufacturers, establishing periods for revisions and preventive care. It is also advisable to use modern technologies with innovative tools to detect problems early and take preventive actions in a timely manner.
Optimal insulation of steam lines
The correct use of thermal insulation of steam lines minimizes heat losses and maintains the steam temperature during transport. Use insulation materials recommended by the manufacturer to provide good thermal performance, durability and reduce energy losses. Thermal insulation should cover all piping as shown in figure 2, fittings and accessories properly and uniformly, all joints and seams should be properly sealed to avoid leaks in steam lines.
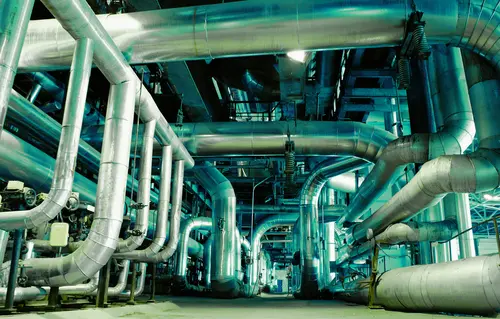
Likewise, factors such as protection against humidity and corrosion must be taken into account to prevent failures, especially in corrosive environments. The efficiency of the insulation also reduces heat losses during transport, keeping the steam temperature constant, and ensuring a reliable and stable supply to the points of use.
Safety is also another key factor because it prevents accidental contact with hot surfaces, reducing the risk of burns and injury to workers. Thermal insulation of steam lines also has an environmental sustainability benefit by reducing energy losses and fossil fuel consumption, which reduces the carbon footprint.
Control of steam pressure levels
Maintain steam pressure controls at the optimum levels required for each end use, excessive steam pressure causes unwanted energy losses and leads to piping damage. The overpressure of these systems places additional stress on the components, generating significant energy losses due to leaks in steam lines and associated connections.
On the other hand, if the steam pressure is too low, it affects the adequate supply at the end points of use, which will negatively affect the efficiency and performance of the processes. To control the steam pressure efficiently, appropriate pressure regulators are used within the systems; these devices are installed at strategic points in the steam lines in order to adjust and maintain the pressure within the ranges required for each process.
Check condition of control valves and condensate drains.
Performs periodic inspections of the control valves in the steam lines to ensure their optimal operation, thus preventing any leakage or blockage that compromises the efficiency of the system. Likewise, condensate must be drained efficiently at the appropriate times to avoid water accumulation in the bottoms of the lines or equipment and thus ensure efficient heat transfer.
Heat recovery from condensed steam
Heat recovery systems represent an efficient technique to take advantage of waste heat from condensed steam during refining processes. These systems make it possible to reuse heat to preheat boiler feedwater or other processes, reducing the need to generate new steam. The use of heat exchangers to transfer waste heat to a secondary fluid optimizes energy consumption and reduces the demand for thermal resources.
In addition, the direct utilization of condensed steam in applications requiring heat at lower temperatures contributes to energy efficiency. Proper design and sizing of heat recovery systems are necessary for efficient heat transfer and energy efficiency. Proper selection of heat exchangers, taking into account process temperatures and flows, and ensuring integration with the main system.
Optimized steam distribution network
Review the design of the steam piping distribution network and make the necessary adjustments to avoid pressure losses and incorrect steam transport to its final use. Steam distribution must be accurate and with the pressure required for each system, this avoids pressure losses and unnecessary steam transport, resulting in a significant improvement in system efficiency.
Evaluating the design of the distribution network involves analyzing the location of end points of use, the diameter and length of piping, the location of valves, fittings and accessories; controlling these factors reduces pressure losses and improves steam transport efficiency. Another technique is the use of steam traps and appropriate control valves at points of use. These devices allow precise control of steam flow and prevent excessive transport or unnecessary release of steam.
The use of modern innovative technologies that simulate steam flow and piping network design software is recommended to evaluate the variables and optimize steam distribution in the processes.
Importance of steam line care for energy efficiency
Improving efficiency in steam systems through care and maintenance not only involves reducing energy waste, but also maximizing the use of the heat generated. By optimizing the distribution through the steam and heat delivery lines to the end use of the refining processes, it can be ensured that each unit of thermal energy generated is utilized effectively and productively.
The correct use of steam under the predetermined operational variables not only increases the overall efficiency of the systems, but also improves the productivity and competitiveness of the companies due to the reduction of operating costs and improvement of the quality of the final products.
Conclusion
Optimizing energy efficiency through steam line care is critical to achieving efficiency and sustainability in hydrocarbon refining processes. This involves not only the implementation of preventive maintenance practices, but also the adoption of technical strategies for the operational and thermal integrity of steam systems.
The proper management of the lines that make up the steam systems ranges from the detailed analysis of the steam network to the optimization of its distribution and the efficient use of condensate, including the inspection of steam lines and proper maintenance of its components, the optimal condition of thermal insulation and the precise control of operational variables such as pressure and temperature.
References
- U.S. Department of Energy. (2014). Improving Steam System Performance: A Sourcebook for Industry, Second Edition. Retrieved February 26, 2024 from https://www.energy.gov/sites/prod/files/2014/05/f15/steamsourcebook.pdf.
- https://vaporparalaindustria.com/10-consejos-practicos-para-optimizar-el-rendimiento-de-las-lineas-de-vapor-y-reducir-costos/. Accessed February 28, 2024