Introduction
The oil industry , the backbone of the global economy and energy, plays a crucial role in sustaining modern infrastructure and contemporary lifestyles. This industry not only drives the engine of the global economy through the production, refining, distribution and marketing of oil and its derivatives, but is also fundamental for the development and maintenance of critical sectors such as transportation, manufacturing and generation. of energy. However, the efficient and safe operation of this gigantic industry intrinsically depends on the mechanical integrity of its facilities.
Mechanical integrity refers to the ability of systems, components and structures to maintain their functionality and resistance to operational and environmental pressures throughout their useful life. In the context of the oil industry , this means ensuring that, from drilling rigs to refineries, every component operates reliably and safely, minimizing the risk of failures that can result in catastrophic incidents, for both workers and the customer. environment.
The central thesis of this analysis is that mechanical integrity is not just another technical component within oil operations; It is the fundamental pillar on which the operational safety and optimal performance of the facilities is supported. Effective mechanical integrity management not only prevents accidents and operational failures, but also ensures production continuity, energy efficiency and, ultimately, the economic viability and sustainability of the entire oil industry . In the following sections, how mechanical integrity directly affects safety and performance will be explored in detail, and strategies for its maintenance and continuous improvement will be discussed.
Understanding mechanical integrity
In the petroleum industry , mechanical integrity is defined as the ability of systems, components and structures to perform their required functions effectively and safely throughout their useful life, under their intended operating conditions. This definition covers a wide range of elements, from pipes and valves to storage tanks and drilling platforms, all of which must operate without failure to ensure safety and efficiency. Mechanical integrity is a multifaceted concept that involves several key components: materials, design, construction, operation and maintenance.
- Materials: The proper selection of materials is essential. They must resist the extreme conditions, such as pressure, temperature and corrosion, typical of the oil industry . Incorrect or low-quality materials can lead to premature degradation and catastrophic failure.
- Design: A robust design ensures that facilities can withstand the expected operational and environmental loads. You must incorporate safety margins and consider potential failure scenarios.
- Construction: Construction quality directly affects mechanical integrity . Accurate construction to design specifications is crucial to ensuring facilities operate as intended.
- Operation: Operations must be performed within defined safe limits. Operational overload or inadequate operating conditions can induce stress and fatigue, compromising mechanical integrity .
- Maintenance: Regular and proactive maintenance is essential to preserve mechanical integrity . Includes timely inspections, repairs and replacements to ensure all components are working properly.
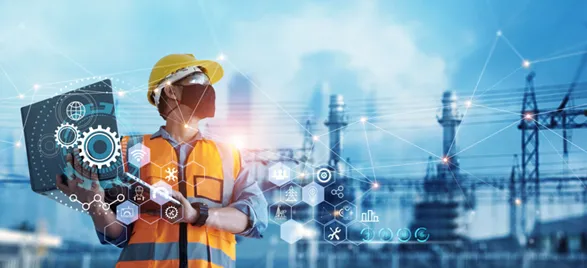
Mechanical failures in the oil industry can have devastating consequences. For example, material fatigue in a pipeline can lead to a rupture, resulting in oil spills with serious environmental and economic impacts. Similarly, a failure in the control system of a drilling platform could cause an explosion, putting human lives at risk and causing significant property damage. These incidents not only result in direct economic losses due to damage and outages, but can also lead to regulatory sanctions, reputational damage and, most importantly, loss of human life.
Understanding and maintaining mechanical integrity is therefore an important aspect of risk management in the oil industry . It requires an integrated and systematic approach ranging from materials selection and design to operation and maintenance, thus ensuring the safety and efficiency of oil operations.
Security Impact
Mechanical integrity is a fundamental pillar for safety in the oil industry . Their commitment can have catastrophic consequences for both workers and the environment. A mechanical failure can trigger a chain of dangerous events, such as explosions, fires and oil spills, that put human life at risk and cause irreparable damage to ecosystems.
For example, lack of integrity in critical components such as safety valves, pipelines and storage tanks can lead to leaks of hydrocarbons, which are highly flammable and toxic. These leaks not only expose workers to immediate fire and explosion risks, but can also result in prolonged exposure to harmful substances, affecting long-term health. Furthermore, when these hydrocarbons are released into the environment, they can contaminate water, soil and air, affecting biodiversity and natural resources.
Historical cases clearly illustrate the devastating consequences of ignoring mechanical integrity . The Deepwater Horizon disaster in 2010 is a tragic example. A series of mechanical and human failures led to the platform explosion, causing 11 deaths and the spill of millions of barrels of oil into the Gulf of Mexico. Another case is the Piper Alpha disaster in 1988, where a series of maintenance and safety failures resulted in the deaths of 167 workers and the total loss of the platform.
These events underscore the importance of adhering to rigorous regulations and safety standards. Organizations such as the American Petroleum Institute (API) and the Occupational Safety and Health Administration (OSHA) in the United States establish guidelines and regulations designed to maintain mechanical integrity and ensure operational safety . These regulations range from design and material selection to operation and maintenance procedures, and compliance is essential to prevent accidents.
The implementation of these regulations is not only a legal responsibility, but also an ethical obligation of companies towards their employees and the environment. Investing in mechanical integrity and safety is not only a preventative measure, but also a smart economic strategy, as the costs associated with accidents, both in human and financial terms, can be enormous. Therefore, maintaining high standards of mechanical integrity is essential to protect lives, preserve the environment and ensure the long-term viability of the oil industry .
Impact on performance and efficiency
Mechanical integrity is a determining factor in the operational efficiency of oil facilities. A well-maintained and operationally sound infrastructure not only ensures safety, but also maximizes efficiency and productivity. Mechanically fault-free operating systems ensure a continuous, controlled flow of oil and gas, minimizing losses and optimizing production. Conversely, mechanical failures can cause significant disruptions, reducing operational efficiency and increasing costs.
Mechanical failures can lead to unscheduled shutdowns, which are periods during which operations must stop for emergency repairs or maintenance. These interruptions not only result in immediate loss of production, but can also cause damage to other system components, increasing the time and cost of repairs. Additionally, unscheduled shutdowns require rapid mobilization of resources and personnel, further increasing operating costs. In a market where profit margins can be tight, these inefficiencies can have a significant economic impact.
A notable example of how mechanical failures affect performance is the case of extraction pumps. If a pump fails due to corrosion or wear, not only does production from the affected well stop, but a significant investment in time and resources is also required to replace or repair the pump. These types of incidents highlight the importance of mechanical integrity to maintain a smooth and efficient operation.
Proactive maintenance and monitoring are essential to improve performance and efficiency. Regular inspections, real-time monitoring and non-destructive testing are key tools for detecting potential problems before they become failures. For example, techniques such as vibration analysis can identify problems in rotating equipment before they fail, allowing for planned maintenance rather than reactions to emergencies. Additionally, implementing risk-based mechanical integrity management systems can help prioritize maintenance actions based on equipment criticality and probability of failure.
In summary, maintaining mechanical integrity is essential not only for the safety but also for the operational efficiency of oil facilities. Proactive maintenance and monitoring strategies not only prevent costly and dangerous accidents, but also ensure that operations run smoothly and efficiently, maximizing production and minimizing costs.
Strategies to maintain mechanical integrity
Maintaining mechanical integrity in the petroleum industry is a complex challenge that requires a combination of best practices, advanced technologies, and a strong organizational culture. Strategies to ensure mechanical integrity include regular inspections, nondestructive testing, real-time monitoring, ongoing training, and the adoption of emerging technologies.
- Regular inspections and non-destructive testing: Regular inspections are essential to detect potential problems before they become failures. Non-destructive testing (NDT), such as ultrasonography, radiography and thermography, allows the condition of equipment and structures to be assessed without causing damage. These techniques can identify cracks, corrosion, and other defects that could compromise mechanical integrity .
- Real-time monitoring: These sensors enable timely detection of anomalies and facilitate rapid interventions before catastrophic failures occur. For example, vibration monitoring systems can alert you to imbalances or misalignments in rotating equipment, indicating the need for maintenance or adjustments.
- Safety training and culture: Well-trained workers can not only perform their tasks more safely and efficiently, but they are also better able to identify and report potential problems. A strong safety culture promotes open communication, continuous learning, and shared responsibility in maintaining mechanical integrity .
- Emerging technologies: Artificial intelligence (AI) and Big Data are revolutionizing the maintenance of mechanical integrity. AI can analyze large volumes of monitoring data in real time to predict failures before they occur. Advanced algorithms can identify subtle patterns that indicate the onset of degradation, enabling predictive and proactive maintenance. Additionally, augmented reality (AR) and virtual reality (VR) are providing new ways to train workers and conduct remote inspections.
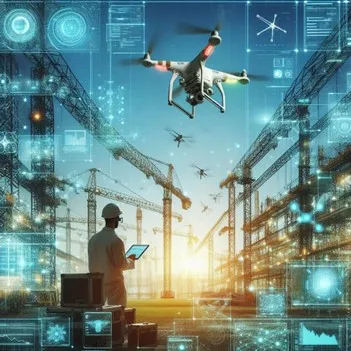
Mechanical integrity requires a combination of best practices, advanced technologies, and a strong organizational culture.
Conclusions
Mechanical integrity emerges as a critical pillar in the oil industry , essential to safeguard human life, protect the environment and ensure operational efficiency. Through this article, we have unraveled its definition and relevance, highlighting how its compromise can trigger catastrophic consequences. We have examined historical cases that illustrate the devastating repercussions of mechanical failures and emphasized the importance of adhering to rigorous regulations and safety standards.
The intrinsic connection between mechanical integrity and operational efficiency predicts how failures can induce unscheduled shutdowns and significant economic losses. Proactive maintenance and supervision strategies, along with the adoption of emerging technologies such as artificial intelligence and Big Data, are presented as indispensable solutions to prevent failures and maximize performance.
The petroleum industry must maintain an unwavering commitment to mechanical integrity . Investing in advanced technologies, continuous training and rigorous practices is not only a preventive measure, but an essential strategy to ensure a sustainable future. Mechanical integrity is not just a technical responsibility; It is an ethical commitment to global safety and efficiency that benefits everyone, from individual workers to society as a whole.
References
Own source