Table of Contents
- Introduction
- What is a hydrocarbon charging hose?
- How is a charging hose structured?
- Types of loading hoses in the railway industry and their applications
- Inspections and tests of hydrocarbon loading hoses
- Hose storage
- Regulations and Standards for charging hoses
- Challenges and solutions
- Conclusion
- References
Introduction
The refining processes are very complex, so excellent coordination is necessary to be able to place the processed products on the world market. To achieve this product placement, a very well-developed chain of services and operations is required, within which is a vital link in the supply chain of cargo from docks to ships and vice versa. That link is a vital but often overlooked component, as are the charging hoses.
These not only facilitate the transfer of products, but play an essential role in the efficiency and security of the supply chain, especially in monobuoy operations, dock-to-ship and ship-to-ship loading. This article will explore the importance and operation of loading hoses in refineries, highlighting their vital role in the safe and efficient delivery of petroleum products.
What is a hydrocarbon charging hose?
They are flexible elastomeric components designed to transfer products to and from ships, tanks and other loading points. In a refinery, these hoses play a crucial role in moving crude oil, gasoline, liquefied gases, chemicals and other refined products. Its design and material must meet rigorous standards to ensure the integrity and safety of operations.
How is a charging hose structured?
These devices are manufactured with different types of materials that give them the characteristics of mechanical resistance and adequate flexibility, allowing safe loading and assembly for the loading of products. The assembly of a hose is carried out in a semi-artisanal way, placing overlapping steel parts with different types of elastomer, polyester and nylon layers as shown in figure 1.
The parts of a hose are the following:
- Fluid tube: It is the one that is in contact with the fluid and its function is to transport it to the load. This element is usually manufactured with flexible nitrile butadiene rubber (NBR) with high adhesion to steel, very resistant to abrasion, aromatic products, oils and fuels.
- Boundary: Typically, layers of boundary fabric are incorporated within the cover matrix between the reinforcement and the outer rubber cover. This layer serves as a manufacturing aid and both promotes adhesion and increases the robustness of the matrix.
- Reinforcement: It is what gives resistance to the hose. The reinforcements are made of fabric. (typically polyester or rayon) encapsulated in rubber to provide adhesion and prevent abrasion. They are of high tenacity and resistant to traction and fatigue.
- Filler: It is a high compression modulus rubber compound that improves the bending and traction of the hose.
- Cover: The final outer layer exposed to the elements that protects the hose reinforcement from damage. It is manufactured from rubber compounds with high resilience and resistance to wear, UV rays, cutting, fatigue and traction.
- End fittings: These are an integral part of the hose construction. They consist of a flange welded to a nipple placed at each end of the hose. The hose components are assembled over the nipple, using wire to narrow the reinforcing material between the ribs and a spirally wound wire is installed between the two flanges that resists deformation of the hose and is conductive of current. static.
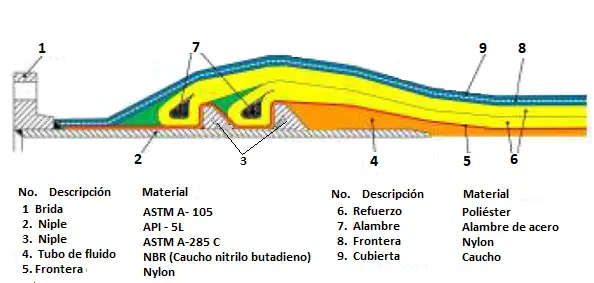
Types of loading hoses in the railway industry and their applications
There are various types of loading hoses on docks, ships and monobuoys, adapted for different products and operating conditions. These hoses made of textile-reinforced elastomers for flammable, corrosive and high-temperature products are common in refineries. Each type of hose is carefully selected according to the nature of the product being handled, the pressures and the location from which loading is carried out. They can be ordered as follows:
According to its construction
- Single shell or casing : The outer shell is the only layer that provides containment. This means that there is a single layer of material between the internal fluid and the surrounding environment. These hoses are less expensive, but also less robust in terms of protection against possible damage or leaks. In figure 2 you can see a diagram of the design of this type of hoses.

- Double casing: They have two casings and are designed so that if the main casing fails, the first casing continues as a fluid conduit and the secondary casing contains space to retain the fluid and protects the environment. Double shell hose can handle higher flow rates compared to single shell ones. These hoses have the ability to contain a leak if it occurs and can be designed to include an alert device in the event of failure. Figure 3 shows a diagram of a hose of this type.
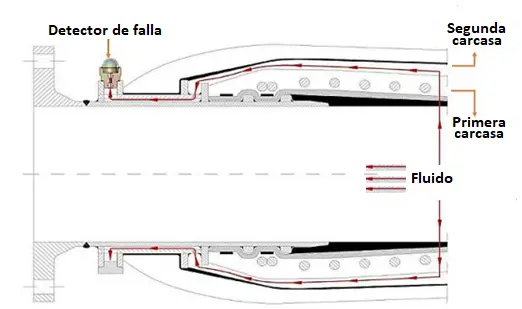
According to loading site
- Floating Hoses: Their particular characteristic is that they float in water. Typically used on the high seas for ship-to-ship and single-buoy-to-ship loading. Figure 4 shows a diagram of this type of hoses.

- Underwater hoses: Typically used offshore in monobuoys . With characteristics similar to the floating one, but without floating material. Figure 5 shows a diagram of this type of hoses.
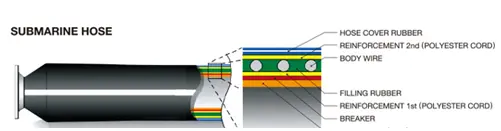
- Spring hoses: These hoses, with structural similarity to the different types of hose, have the particularity that they are installed in the discharge of the pumps or in the articulated arms of the docks, where they remain frequently exposed to the weather and UV rays as shown in the figure. 6.
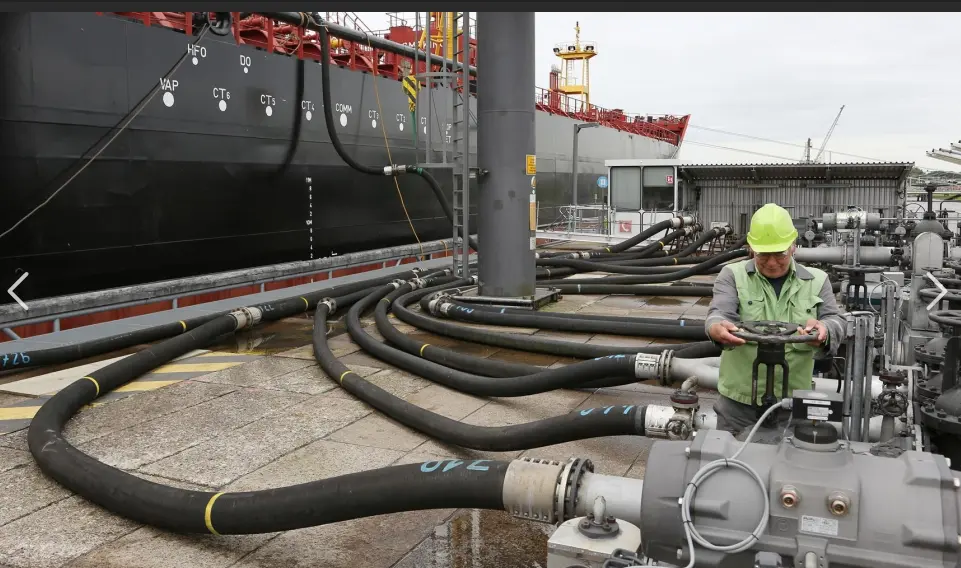
Depending on the product
The hoses used to load ships with hydrocarbons and gases are designed and classified according to the type of product to be transported. Classification is based on several factors, including product chemical composition, loading temperature, pressure and other specific requirements to ensure safe and efficient product transfer. Here is a general classification of charging hoses according to the charging product:
- Hoses for crude oil and its liquid derivatives: Designed for oils, gasoline, diesel, kerosene, etc. Resistant to abrasion and oil.
- Chemical Hoses: Hoses designed for particular chemicals with special properties. Resistant to acids and alkalis.
- Gas hoses: Hoses for flammable gases such as natural gas or liquefied petroleum gas (LPG).
- Low Temperature Liquefied Gases: Designed to withstand extremely low temperatures for cryogenic products such as liquefied natural gas (LNG) or liquefied petroleum gas (LPG).
- Hoses for viscous products: Designed to facilitate the flow of viscous products such as asphalt or tar.
Inspections and tests of hydrocarbon loading hoses
Hose inspection and testing is regulated by OCIMF (Oil Companies International Maritime Forum). These must be carried out by trained personnel before connecting to the ship’s manifolds to check their suitability so that servicing can be carried out if the damage is considered critical. The inspections and tests that must be carried out are the following according to the OCIMF:
- External/Internal Visual Inspection: External surfaces and any accessible internal surfaces should be visually inspected for signs of damage or deterioration.
- Flange Integrity: Flanges should be inspected for damage, excessive corrosion, and missing screws.
- Periodic Hose Testing: Tests and inspections should be performed at least every twelve months. Inspection frequency should take into account the types of products handled through the hose, the age of the hose, and the severity of the service conditions.
- Hydrostatic tests: Internal hydrostatic pressure is carried out at 1.5 times the working pressure of the hose, and elongation is measured, during and after the test. Temporary and permanent elongations must be recorded. The test should be carried out at room temperature.
- Electrical continuity test: They must be performed with the hose empty before, during and after hydrostatic tests.
Electrically discontinuous hoses must have a resistance of no less than 25,000 Ω, electrically continuous hoses must have a resistance no greater than 100 Ω, and electrically conductive hoses must have a resistance between 25,000 and 1,000,000Ω measured flange to flange.
Hose storage
The life of stored hoses can be affected by temperature, humidity, ozone, UV rays, direct sunlight, oils, solvents, corrosive liquids and vapors, insects and rodents. It is advisable to store them in containers where they are on the ground so that they are additionally protected against insects and rodents.
In case of extreme temperatures, additional measures may be needed, such as storing the hoses in a climate-controlled warehouse and if storage is not possible, the hoses should be covered to protect them from sunlight.
Regulations and Standards for charging hoses
Charging hoses must comply with specifications and other international regulations that establish requirements for design, manufacturing, testing and maintenance. The most important are the following:
- Oil Companies International Maritime Forum (OCIMF): Guidelines for the handling, storage, use, maintenance and testing of STS hoses
- OCIMF: Specification Guide for Spring Hoses
- ISO 1823: Wire-reinforced rubber hose assemblies for transferring crude oil and non-gaseous hydrocarbons.
- BS EN 1765: For spring hoses in petroleum suction and discharge services Specification for assembly
- BS EN 13765: Multi-layer thermoplastic hoses (non-vulcanised) for the transfer of hydrocarbons, solvents and chemicals.
- BS EN 1762: Rubber hoses for liquefied petroleum gas (LPG) (liquid or gaseous phase) and natural gas up to 25 bar
- BS EN 13482: Rubber hoses for asphalt and bitumen
Challenges and solutions
Exposing charging hoses to harsh conditions and constant wear can create challenges. Regular inspections, preventive maintenance and the use of advanced technologies, such as smart hoses with monitoring sensors, are key solutions to mitigate risks and ensure operational efficiency.
Conclusion
In a complex refinery network, refinery loading hoses are the link that connects each phase of the supply chain. From the receipt of raw materials to the delivery of refined products, these hoses play a very important role in the efficiency, safety and quality of operations. As the industry evolves, attention to technology, regulations and best practices in loading hose management becomes increasingly essential to maintaining the integrity of the refinery supply chain.
References
- https://www.y-yokohama.com/global/product/mb/pdf/resource/seaflex.pdf
- https://noesis.uis.edu.co/server/api/core/bitstreams/802e6834-bf10-4155-8811-8459054ac330/content