Table of Contents
- Possible defect locations according to API RP 577
- Commonly used non-destructive testing
- NDT method capability for different types of solder joints according to API RP 577
- Applicable NDT Method Capability vs. Discontinuity
- Discontinuities commonly found in welding processes
- Conclusions
- Bibliographic references
Structural integrity is a critical aspect in various industries, especially those where safety and reliability are imperative. In this context, the American Petroleum Institute (API) establishes rigorous standards to guarantee quality and safety in welded joints.
API RP 577 Recommended Practice provides specific guidelines for the selection of Non-Destructive Testing (NDT) in weld inspections, addressing possible defect locations, commonly used non-destructive testing, the capability of these methods depending on the type of weld joint, discontinuities and welding processes.
The essential parameters to make the most suitable choice of NDTs are discussed below according to point 8 of the recommended practice API RP 577.
Possible defect locations according to API RP 577
Before addressing the selection of non-destructive testing, it is necessary to know the possible locations of defects in welded joints. Imperfections can arise in various areas, including the weld metal zone (WMZ), weld interface (WI), base metal zone (BMZ), and heat affected zone (HAZ). Table 2 of API RP 577 lists the common types and locations of discontinuities and illustrates in Figure 13 their positions within a butt weld.
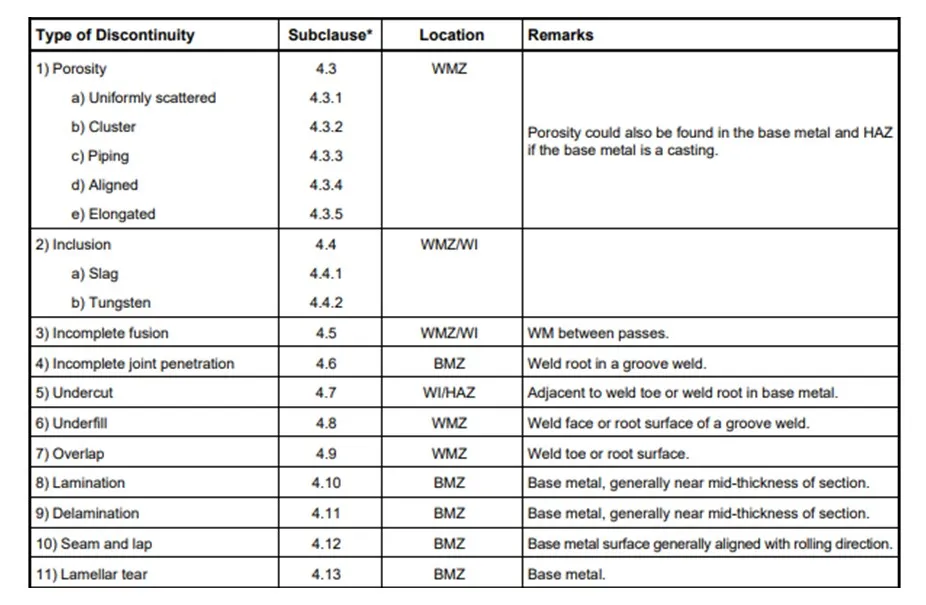
Commonly used non-destructive testing
The proper selection of non-destructive tests is essential to evaluate the quality of welds. Among the most commonly used methods in weld inspection and suggested by API RP 577 recommended practice are:
- Visual inspection (VT): This method provides a superficial evaluation of the weld, identifying visible defects such as undercuts, lack of filler material, porosities open to the surface, among others.
- Magnetic Particles (MT): Effective for detecting surface and subsurface defects in ferromagnetic materials.
- Fluorescent Wet Magnetic Particles (WFMT): Effective when high sensitivity is required for the detection of surface and subsurface defects in ferromagnetic materials.
- Penetrating liquids (LP): Ideal for detecting surface cracks, LP involves the application of a penetrating and revealing liquid, evidencing discontinuities on the surface of the weld.
- Leak test (LT): Test in which the component (pipe, pressure vessel, among others), are subjected to a certain pressure to demonstrate the tightness or integrity of the system.
- Eddy current testing (ECT): Inspection method that is mainly applied to non-ferromagnetic materials for the detection of surface and subsurface defects.
- Ultrasound (UT): Using ultrasonic waves, the UT detects internal imperfections and evaluates their depth, allowing a detailed inspection of the internal structure of the weld.
- Radiography (RT): Using ionizing radiation, radiography provides images of welds, allowing the identification of internal defects such as cracks, lack of fusion or inclusions.
- Alternating Current Field Measurement (ACFM): Electromagnetic inspection technique that can be used to detect and size surface breaks (or in some cases near-surface defects) in magnetic and non-magnetic materials.
NDT method capability for different types of solder joints according to API RP 577
The effectiveness of non-destructive testing varies depending on the type of welded joint and the position of the defects. For example. Visual inspection, liquid penetrant and magnetic particle tests are useful for identifying surface defects, while techniques such as ultrasound and radiography are essential for evaluating the internal or volumetric integrity of the weld.
Table 4 of API RP 577 shows the suitability of the non-destructive test according to the type of welded joint (butt, corner, T, among others) and the type of discontinuity according to its location (superficial or volumetric), indicating whether the test is applicable with the letter “A” or with marginal applicability indicated with the letter “M”, the latter depending on certain factors such as the thickness of the material, size, orientation and location of the discontinuity.
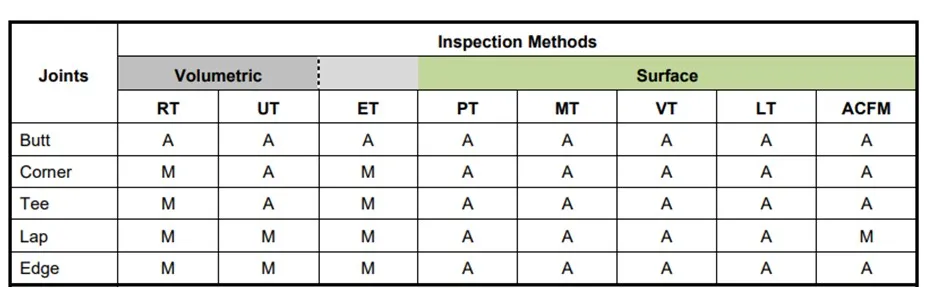
Applicable NDT Method Capability vs. Discontinuity
The selection of the NDT method has a large dependence on the nature of the expected discontinuities. For example, ultrasound testing is more appropriate for the detection and evaluation of planar defects with uncertain orientation through the component thickness, such as cracks and lack of fusion, while radiographic testing is more suitable in the detection of volumetric defects such as pores and slag inclusions.
Table 5 of API RP 577 shows the applicability of the different tests depending on the types of discontinuities, indicating with an “A” the applicable tests, “O” with marginal applicability, and with a “U” those usually not applicable.
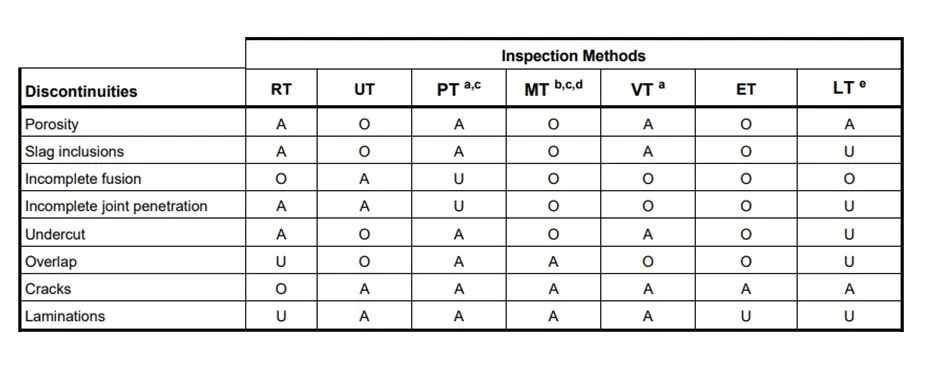
Discontinuities commonly found in welding processes
The inspector should know the basic arc welding processes most frequently used in the manufacture and repair of refinery and chemical process equipment, and the types of discontinuities that may arise for certain welding processes and that compromise structural integrity.
This is why the inspector, before considering the most appropriate Non-Destructive Tests depending on the discontinuity and configuration of the welded joint, must also keep in mind the probable discontinuities to be found depending on the welding procedure used. Some of the most common include:
- Cracks: Cracks in the weld, whether longitudinal, transverse or cold cracking.
- Porosities: Small cavities caused by the inclusion of gases during the solidification of molten metal.
- Lack of fusion: Areas where complete union between the materials is not achieved, compromising the strength of the weld.
- Inclusions: Presence of non-metallic materials in the weld, such as slag or unwanted particles.
- Incomplete Penetration: Joint root condition in a groove weld in which the weld metal does not extend through the thickness of the joint.
Early identification of these discontinuities is essential to address potential problems before they affect structural integrity. Table 6 of API RP 577 shows typical discontinuities associated with welding processes.
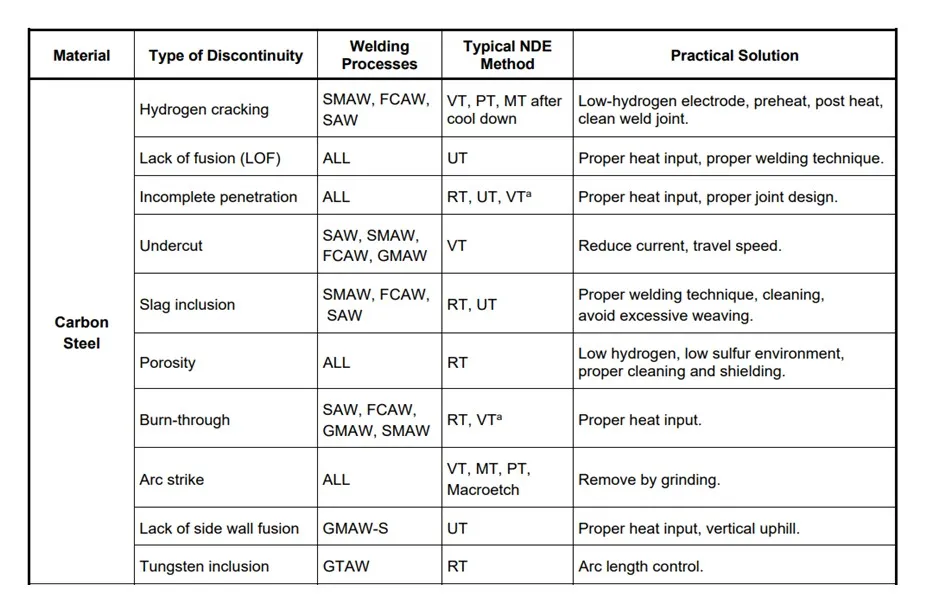
Conclusions
In summary, the selection of non-destructive testing according to API RP 577 recommended practice plays a crucial role in ensuring structural integrity in welded joints. Understanding potential defect locations, the ability of the methods to evaluate weld joints, and the identification of common discontinuities are key elements in this process.
By taking an approach that takes all of these factors into account, industries can strengthen their inspection practices and ensure the safety and reliability of their welded structures. Investment in the proper selection and application of non-destructive testing is essential to prevent catastrophic failures and maintain quality standards at the forefront of structural engineering. API RP 577 provides excellent guidance for making the best choice of NDT to optimize weld integrity.
Bibliographic references
- API RP 577: Welding Processes, Inspection, and Metallurgy ; Consulted on December 1, 2023.
About the Author:
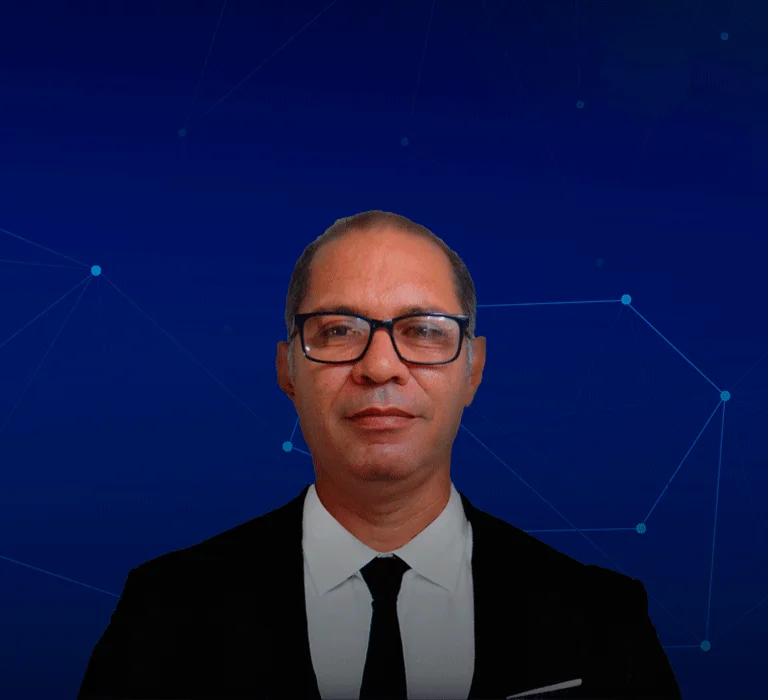
Carlos Álvarez, Mechanical Engineer (1994), with extensive training in the area of inspection and mechanical integrity, being Certified Level III by the American Society of Non-Destructive Testing (ASNT), in the Ultrasonic testing method. He has worked in the Oil and Gas area, starting as an Inspector of static equipment at the Paraguaná Refining Center (CRP), belonging to the state oil company Petróleos de Venezuela (PDVSA). Likewise, he has conducted a significant number of trainings, especially for the Education and Training Center (CEF), an institution dependent on PDVSA developing level I and II courses in the Ultrasound testing method.