Table of Contents
- Safety in the industry
- What emerging technologies are influencing industrial manufacturing operations?
- Impact of emerging technologies on the security of industrial operating environments
- Challenges of emerging technologies in industrial safety
- Cases of implementation of emerging technologies in industrial safety
- Conclusions
- References
The technological revolution has unleashed major and unprecedented changes in the industrial landscape, completely redefining the approach to the security of industrial operating environments . In this dynamic context, emerging technologies have emerged as key elements, not only to optimize the efficiency of traditional systems, but also open the door to cutting-edge techniques to address vulnerabilities in the protection of companies.
Technologies are no longer limited to boosting productivity; have crossed the line to actively support the worker, improving working conditions and preventing possible risks and accidents; therefore, they are seen as fundamental allies in the insurance of workers in the industrial environment, representing a significant evolution in the conceptualization and application of precautionary measures.
Safety in the industry
Industrial safety is defined as the set of regulations and practices aimed at reducing and managing risks in industrial environments, such as plants and factories. This systematic approach extends to all hierarchies within the company, guaranteeing the comprehensive protection of people.
Its main objective is to prevent injuries and accidents at work, acting preventively against possible damage to workers or facilities 1 . In addition to addressing proactive risk management, industrial safety includes the investigation of accidents according to current regulations, highlighting the importance of standards such as ISO 45001 for Safety and Health at Work and ISO 14001 for the environment 2 .
With the arrival of innovative concepts such as industrial automation, this sector experienced a great increase in its production processes. But at the same time, new challenges developed when it came to the safety of industrial operating environments.
In this context, sectors with high demand in security, such as mining, construction and related industries, have led the adoption of Industry 4.0 technologies and tools. These initiatives are aimed not only at enhancing operational efficiency, but also at raising workplace safety standards, paving the way for the successful integration of emerging technologies into demanding industrial operating environments.
What emerging technologies are influencing industrial manufacturing operations?
Sensors connected to the Internet of Things (IoT)
Industrial safety sensors are fundamental devices in industrial safety, thanks to their non-contact detection system that reacts exclusively to changes and inconsistencies present in critical areas. They are quick and discreet installation devices that play an essential role in risk prevention, particularly in situations where unsafe conditions are difficult to identify with the naked eye.
Its usefulness stands out in scenarios such as toxic gas leaks, where early detection is crucial to avoid serious consequences such as explosions or poisoning. Sensors can monitor a variety of conditions, from hazardous atmospheres to extreme temperatures, voltage, current, frequency, weather conditions, pressures, liquid levels and more. And thanks to IoT connectivity, this important data can be transferred and received immediately from different locations.
In industry, these devices not only provide real-time information, but also overcome human limitations by detecting elements undetectable to human senses, ensuring a safe and efficient work environment.
Virtual reality (VR)
By focusing on risk management in industrial operating environments, virtual reality allows employees to immerse themselves in realistic simulations of dangerous situations, improving decision-making and emergency response. This technology offers an engaging and immersive training experience 3 , providing accurate simulations of various industrial environments (see Figure 1). In addition, it enables the personalized creation of scenarios, adapting to the specific needs of each company.
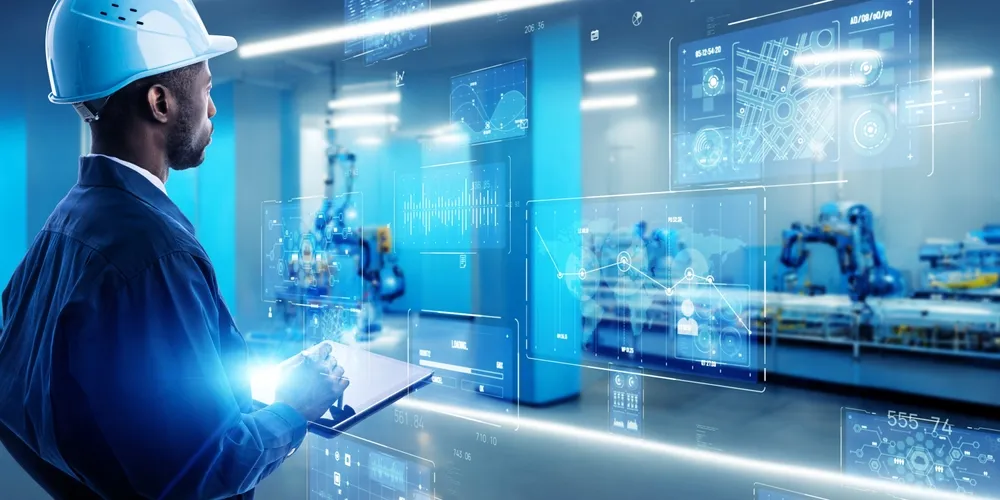
Knowledge retention is enhanced with VR, outperforming traditional training methods. This approach not only improves workplace safety, but also contributes to cost reduction by eliminating additional materials and personnel transfers.
Artificial intelligence (AI)
Traditionally, inspectors played a key role in assessing risks and implementing preventative measures. With the entry of artificial intelligence, the automation of routine tasks and the generation of valuable insights from large amounts of data has been achieved.
AI systems can analyze patterns, identify trends and detect failures in real time, providing inspectors with detailed and up-to-date information about the risks present at client facilities. This advance contributes to more efficient risk management, highlighting the integration of emerging technologies in industrial safety.
Drones/unmanned vehicles
They are autonomous tools that have benefited monitoring practices of large areas with efficiency and the use of minimal resources. They can be programmed to follow predefined routes, providing real-time updates and detailed coverage (see figure 2), identifying threats such as structural problems or spills 4 . The data collected enables decisions, identifies risks and refines safety protocols, improving monitoring of dangerous sites and ensuring regulatory compliance.
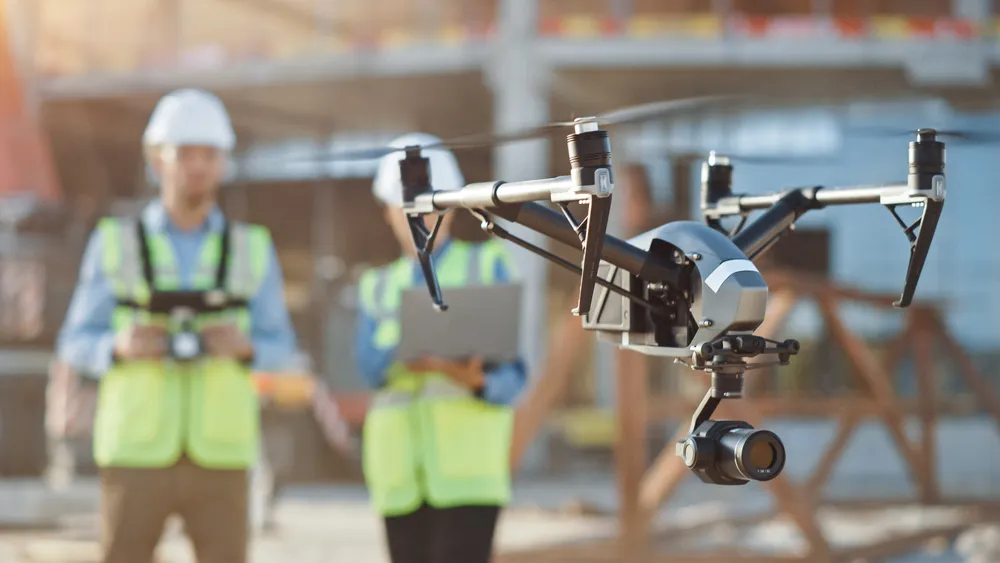
The implementation of these tools provides security to monitoring, with rapid responses to emergencies, minimizing the need for manpower and optimizing business profitability. With continued advancements, drones are projected to further strengthen industrial inspection operations.
big data
This concept refers to the analysis and management of large data sets generated by various sources in industrial environments. This data, coming from sensors, logs, monitoring systems and external sources, offers a detailed view of an organization’s working conditions and the possible risks it may be running.
It is a tool characterized by the “3Vs”: Volume, due to the large amount of data generated and handled; speed, since the information must be analyzed in real time; and variety, by including structured and unstructured data from various sources 5 . Its application involves the identification of patterns and estimates that can be helpful for decision making, as well as for the management of predictive and preventive maintenance .
Impact of emerging technologies on the security of industrial operating environments
The development of computer programs and new technologies has improved the management and maintenance of facilities (see figure 3), guaranteeing the safety of employees. The use of digital tools and industrial automation has reduced the need for workers to be directly exposed to dangerous situations. Therefore, the impact of emerging technologies on industrial safety, particularly in the oil and gas sector, is notable.
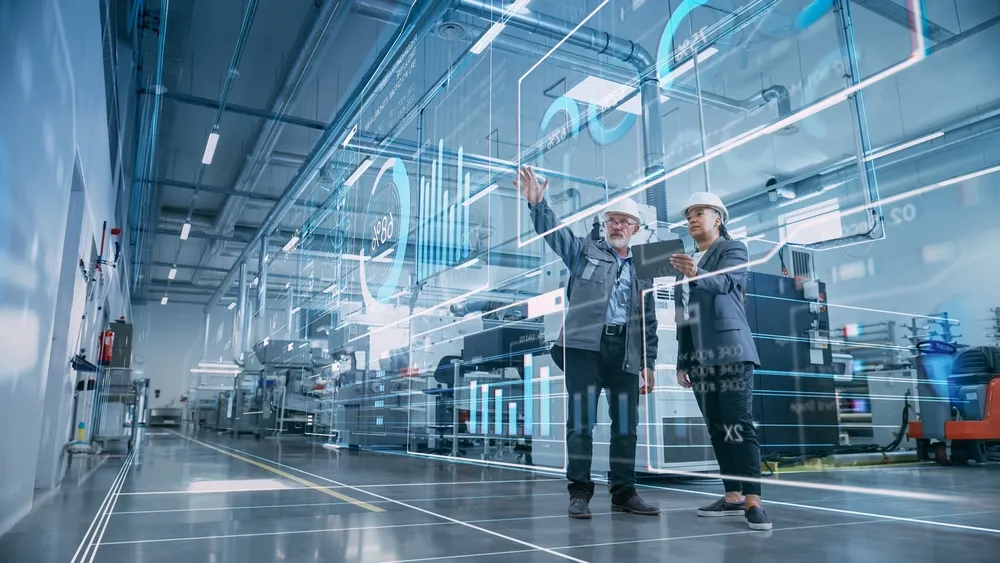
These innovative technologies play an important role in protecting against sensitive variables such as chemicals, extreme temperatures and pressures. Thanks to this, risk management in industrial operating environments is part of a transformation for a future where security represents the main pillars in the development of business operations.
As these are industries whose environments are constantly evolving, the implementation of technologies in industrial safety results in an incredible option for adapting to regulatory changes and fluctuating requirements. As a result, they improve operational efficiency in areas such as exploration, extraction, transportation and distribution, and also raise industry safety standards to unprecedented levels.
Challenges of emerging technologies in industrial safety
More and more industries are adopting digitalization; This increasing connectivity increases the risk of cyberattacks, with potential consequences ranging from loss of customer trust to financial fines, unscheduled production shutdowns, and legal risks. For this reason, the implementation and continuous improvement of cybersecurity measures are essential to guarantee effectiveness against these threats and safeguard the integrity of industrial operating environments.
Implementation in globalized industries
Decentralization is the main characteristic of many companies, considering this, the integration of new technologies in organizations that operate in this way can be a difficult process. The reason for this is that, depending on the location, environmental conditions may vary, affecting the state and performance of the equipment differently as a consequence 6 . Furthermore, its large-scale implementation can represent economic and logistical challenges.
Lack of technological skills of new technologies
To achieve the safety of industrial operating environments, it is necessary that these technologies be used ideally, therefore, it is essential that work teams have the necessary skills to use equipment and tools that will allow the assurance of the procedures carried out in the facilities 6 . The lack of knowledge will not only hinder the digital transformation process, but can also lead to malfunctions, production stops and even workplace accidents.
Digital immaturity
Digital transformation is a process that depends mainly on the naturalness with which an organization can adopt a technological scheme to its infrastructure. Unfortunately, many industries have an immature definition of the importance of technology and its impact on the safety of their facilities and processes.
As a consequence, resistance may arise to the proposed changes to certain work practices 6 , as well as to the implementation of risk management equipment, technologies and software in industrial operating environments.
Cases of implementation of emerging technologies in industrial safety
Chevron
Chevron, a leader in the oil and gas sector, has collaborated with Wyld Networks to implement the Wyld Connect system, an innovative satellite IoT solution. This system aims to improve safety in Chevron’s industrial operating environments by connecting remote sensors in distant locations.
“Sensor-to-satellite” technology allows data collection in areas without coverage. This innovative model would facilitate the evaluation of the system’s effectiveness in managing sensor data, supporting Chevron’s global operations in challenging environments that could pose some type of danger to workers.
shell
The Shell Rheinland energy and chemical park, in order to improve the security of its facilities, has implemented Energy Robotics drones as one of the steps in Shell’s digitalization.
Its use in “beyond visual range of the pilot” (BVLOS) operations allows automated inspections from control rooms, optimizing the efficiency and safety of asset management processes in comparison to manual inspection rounds, contributing to the objective of Shell to completely eliminate workplace accidents.
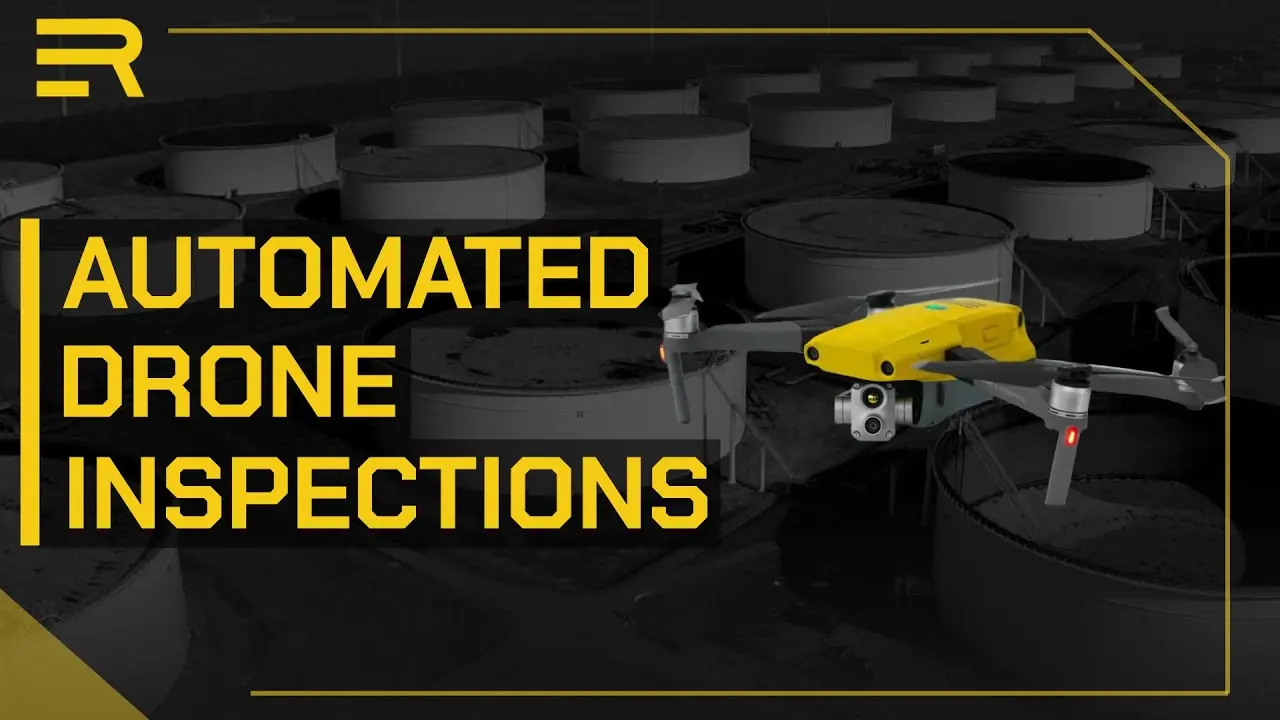
Exxonmobil
Focused on predictive maintenance and increasing production, Exxonmobil has implemented systems based on artificial intelligence and Big Data, with the aim of analyzing large loads of data at a global level.
By creating these “data lakes” on a global scale, this company empowers its operators to process them, allowing a comprehensive view that improves the security of each of its facilities, operations and promotes a more efficient and sustainable energy future throughout the world. world.
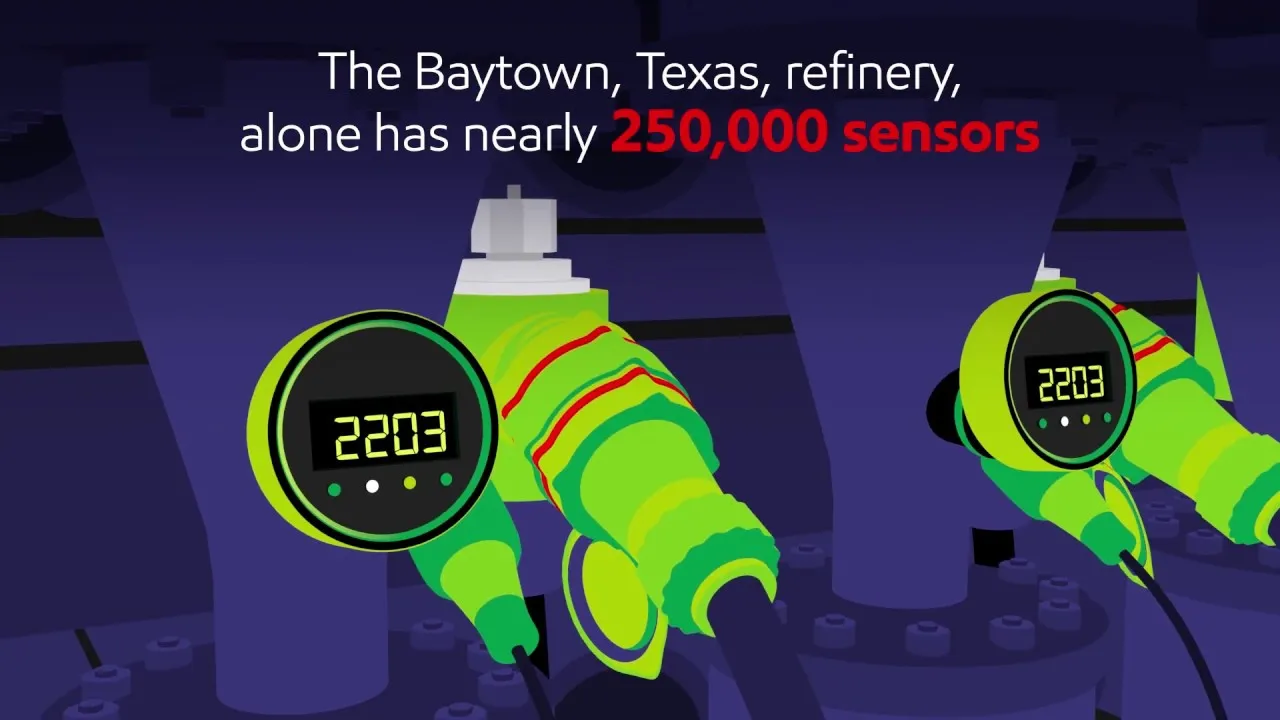
Conclusions
In a sector undergoing constant change, emerging technologies act as a determining factor for energy providers, particularly in the security of industrial operating environments. These new equipment and concepts allow for rapid and efficient adaptation to the different changes that may occur in work processes. From exploration to distribution, the widespread use of new technologies drives improvements in risk management and operational efficiency.
The application of advanced technologies together with strategic plans and a deep situational analysis of the current industrial structure allows organizations to develop a proactive approach to security. This approach not only mitigates threats and protects assets, but will also help in achieving business objectives, by guaranteeing the sustainability of production processes, as a result of the incorporation of innovations in work schemes.
References
- Burge, S. (2023, March 15). What is Industrial Security Management? Retrieved December 4, 2023, from https://internationalsecurityjournal.com/industrial-security-management/
- Prysmex. (2019, May 30). Industrial Safety: What is it and what is it for? Consulted on December 4, 2023, from https://www.prysmex.com/blog/seguro-industrial-que-es-y-para-que-sirve
- Chironprevention. (2022, November 1). Virtual reality, the best ally of the occupational risk prevention technician. Consulted on December 5, 2023, from https://www.quironprevencion.com/blogs/es/prevenidos/realidad-virtual-mejor-aliada-tecnico-prevencion-riesgos-la
- Frąckiewicz, M. (2022, November 1). The Benefits of Autonomous Drones for Industrial Safety. Consulted on December 5, 2023, from https://ts2.space/es/los-beneficios-de-los-drones-autonomos-para-la-seguro-industrial/#gsc.tab=0
- Drixit Technologies. (sf). Big data: How to use it to increase industrial security. Consulted on December 5, 2023, from https://drixit.com/es/big-data-y-seguro-industrial
- Zhang, A. (2021, September 10). 7 Digital Transformation Challenges for Oil and Gas Companies. Retrieved December 5, 2023, from https://www.linkedin.com/pulse/7-digital-transformation-challenges-oil-gas-companies-cdmc/