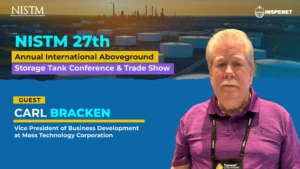
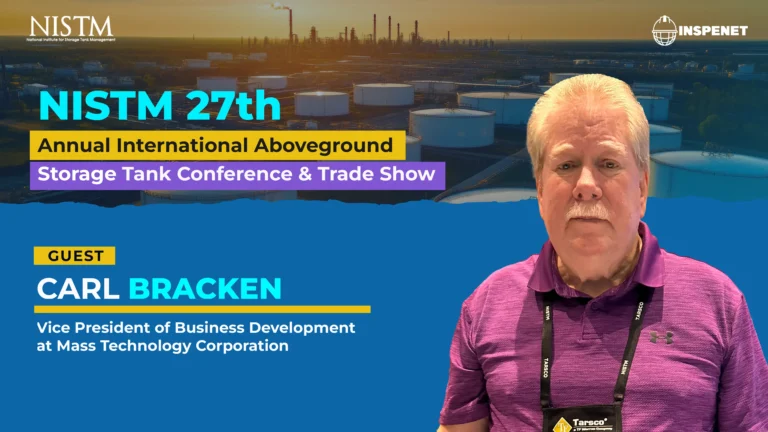
Waterjet cutting: a safe technique to open storage tanks
Maintenance of storage tanks in the energy industry carries inherent risks, especially when cutting structural metal parts is required. Carl Bracken, Vice President of Business Development at Mass Technology Corporation, explained how the method known as Safe Cut has become a reliable option through the use of pressurized waterjet cutting.
Why avoiding sparks is key?
During cutting or repair work, any spark could be enough to cause an explosion in an environment with flammable vapors. Hence, the need for methods that eliminate that risk. According to Bracken, Safe Cut is based on the use of water at pressures up to 60,000 PSI, with consumption of less than a gallon per minute, which represents a significant advantage over hydroblasting which uses large volumes of water and generates greater operational risks.
Accuracy, efficiency and collaboration
Mass Technology's team does not perform internal repairs, but specializes exclusively in the cutting process. Once the tank is opened by means of a door sheet (usually 8x10 or 10x10 feet), specialized contractors such as HMT or Matrix are in charge of removing the bottom and making the necessary repairs. The cut sheet is then welded back together to seal the tank.
This collaborative scheme improves the efficiency of the overall process, as the tank does not need to be out of service for a long time. In addition, the environmental impact is reduced by avoiding internal pre-cleaning and the structural integrity of the tank is protected.
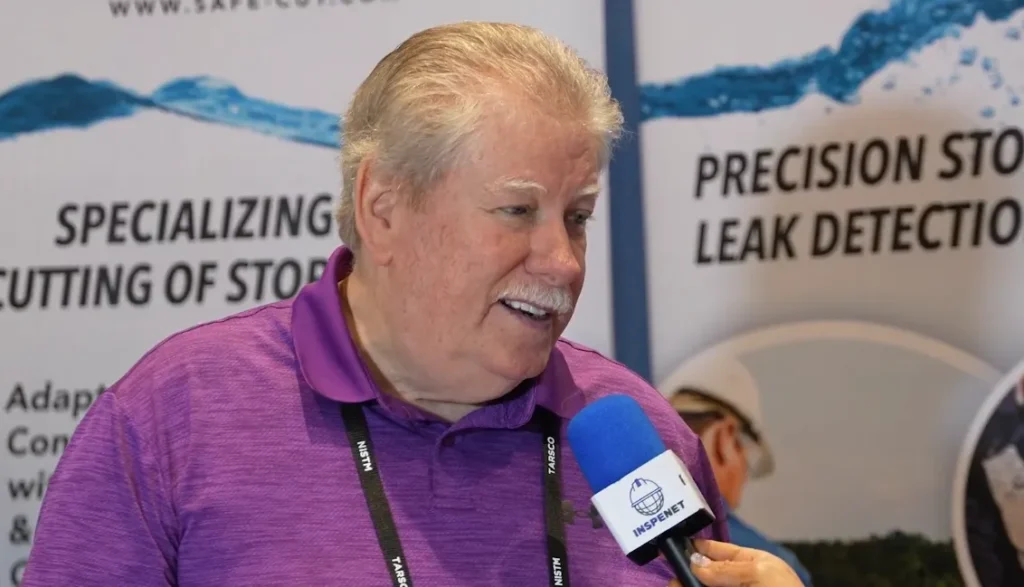
Safe Cut, more than a trade name
The name Safe Cut reflects the company's commitment to industrial safety, not only from a technical but also from an operational point of view. By eliminating the need for friction or spark cutting tools, and by working with controlled pressures and low flow rates, the method presents itself as a practical, accurate and cost-effective solution for the hydrocarbon and other hazardous fluid storage industry.
For more NISTM 2025 content, visit our YouTube channel and LinkedIn profile.
Source: Inspenet.