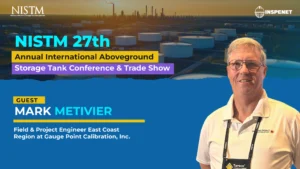
Tank gauging: Accuracy and efficiency with 3D scanning and cloud technologies
Tank calibration has evolved over the years thanks to high-definition 3D scanning technology. During an interview with Mark Metivier, Field and Project Engineer for Gauge Point Calibration's East Coast Region, it became clear that the industry is taking a decisive turn toward more accurate and efficient processes.
Thanks to 3D scanning, a complete model of the tank is generated, making it possible to identify details such as deformations, plumb deviations and roof defects, all without physical contact. This ensures that each calibration table obtained accurately reflects the actual condition of the structure.
Optimizing data recording and processing
In addition to scanning, cloud technologies play a key role in the modernization of this service. Although Gauge Point Calibration does not base its operations on artificial intelligence centrally, they use cloud support to manage 3D scan logs.
This capability facilitates the secure storage of large volumes of data and allows them to be processed quickly, even months or years after the initial inspection. In addition, this methodology reduces the need for future travel, generating significant savings for clients.
Farewell to traditional methods: calibration without liquids
Just a few years ago, tank calibration required complex water draw tests, but today, thanks to high-definition 3D scanning, this step has become unnecessary. A "virtual survey" of the tank volume is achieved, measuring every foot or even every inch of the tank structure. This transition eliminates logistical and environmental risks, speeds turnaround times and provides much more detailed results. Terminals and operators now have an accurate x-ray of the structural health of their assets.
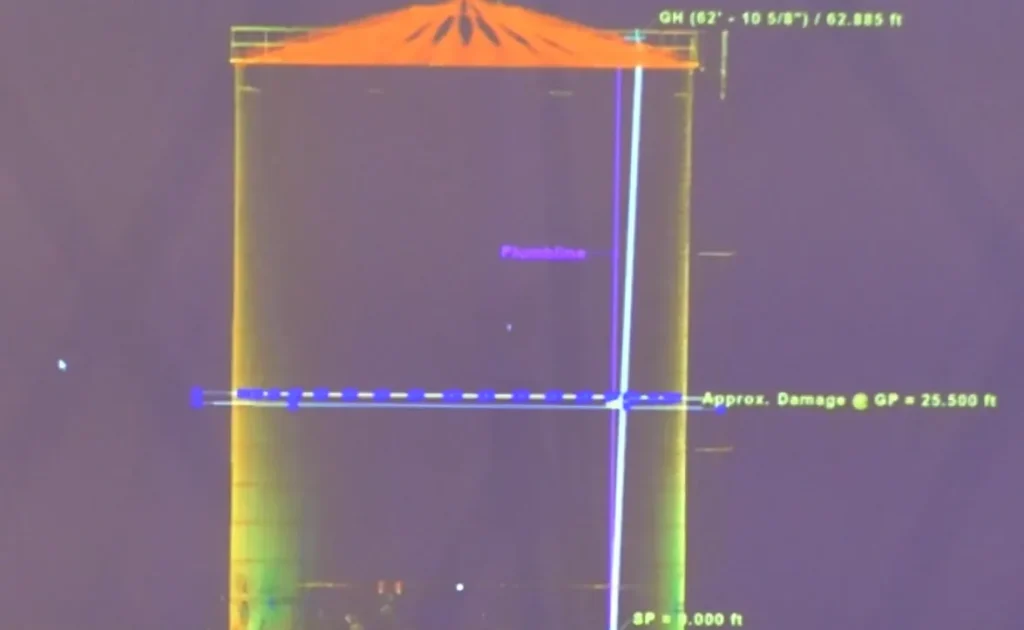
Complementary support
Although artificial intelligence does not drive the core processes at Gauge Point Calibration, its integration appears in a complementary way, especially in cloud logging and scanned data organization. This selective approach ensures that technology supports technical work without replacing human supervision. In an industry where accuracy is non-negotiable, this balance is essential to maintain the high standards demanded by industrial inspections.
Innovating in tank calibration
Tank calibration through 3D scanning and cloud processing represents a profound change in the industry. It is not just about adopting new tools, but transforming the way companies ensure the safety, efficiency and quality of their operations.
Gauge Point Calibration is at the forefront of this evolution, combining technology, experience and a clear vision of current market needs.
For more NISTM 2025 content, visit our YouTube channel and LinkedIn profile.
Source: Inspenet.