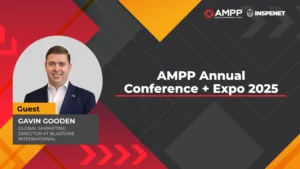
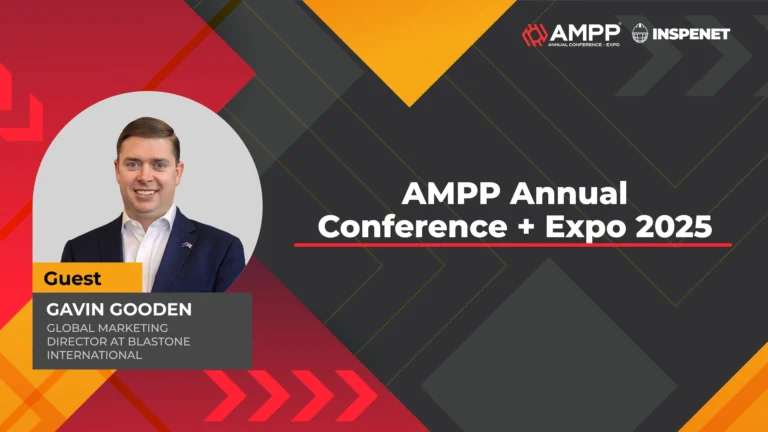
Robotics and smart data drive industrial abrasive blasting
During the AMPP 2025 event, the Inspenet team had the opportunity to interview Gavin Gooden, Global Marketing Director of BlastOne Internation, who made it clear that the future of abrasive blasting lies in automation. The company, with more than 15 years of experience in the United States and Australian roots, has developed solutions to address what it considers a dusty, dirty, and dangerous work environment, through industrial robotics at the service of safety and productivity.
The most obvious example is the VertiDrive, a robot that carries up to three high-capacity shot blasting nozzles and can climb industrial tank walls, doing the work of three to five operators. A recent case study showed that a task that normally took 14 days with eight people was completed in six days with just three operators thanks to the VertiDrive.
Sectors that benefit from abrasive blasting automation
The oil & gas sector is leading the adoption of these technologies, with applications in storage tanks and large metal structures, such as those in shipyards and railways, which directly benefit from robotics due to their scale and the constant need for surface maintenance.
In refineries, where asset owners are seeking to reduce work at height, automation has moved from being an option to a priority. By using these robots, it is possible to automate up to 95% of work at height, drastically reducing workers' exposure to risks.
Occupational safety with robotic systems
The significant impact of these systems is not only economic but also human, which is why BlastOne has designed its robots with the goal of minimizing the physical hazards of manual abrasive blasting in mind. Equipment like the Q-Layers allows tank surfaces to be painted without the need for scaffolding or baskets, encapsulating the paint to prevent overspray, while the BlastMan, used in fixed blasting rooms, can process up to 2,000 pounds of abrasive per hour, significantly reducing time and direct contact with hazardous particles.
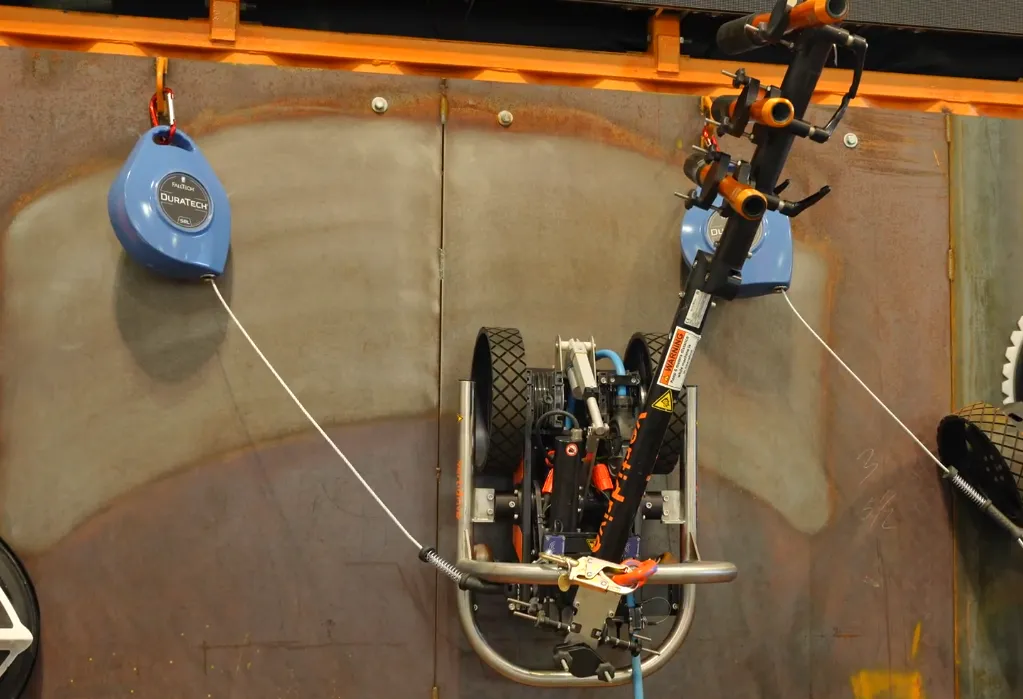
Artificial intelligence and monitoring with IntelliBlast
In addition to robotics, BlastOne has incorporated intelligent systems for remote monitoring, such as its IntelliBlast technology, which allows three key metrics to be recorded in real time: blast pressure, effective operating hours, and abrasive consumption. Supervisors can access this data from anywhere, preventing operational losses due to errors such as incorrect pressures or undetected leaks.
These types of solutions not only avoid unnecessary expenses, but also empower field teams with immediate feedback and complete control over system performance.
For more AMPP 2025 content, visit our YouTube channel and LinkedIn profile.
Source: Inspenet.