Scientists from Seoul National University teamed up to develop a functional robotic hand using a 3D printer. The prosthesis, known as the ST3P hand and which barely weighs 255 grams, was designed with the premise of being light and economical, with an estimated cost of $500 , according to a recent article published by the research team.
ST3P: the lightweight and functional robotic hand
With nine joints in the fingers, this prosthesis was manufactured using a single-step 3D printing process, allowing for astonishingly fast assembly of less than 10 minutes , compared to other 3D printed prosthetics.
In addition to its efficiency in assembly, the ST3P hand proves to be fully functional , capable of performing basic tasks with a pulling force of 48 N and a gripping force of 20 N. The researchers, when talking about this innovative product, express having high expectations regarding its creation and its possible applications.
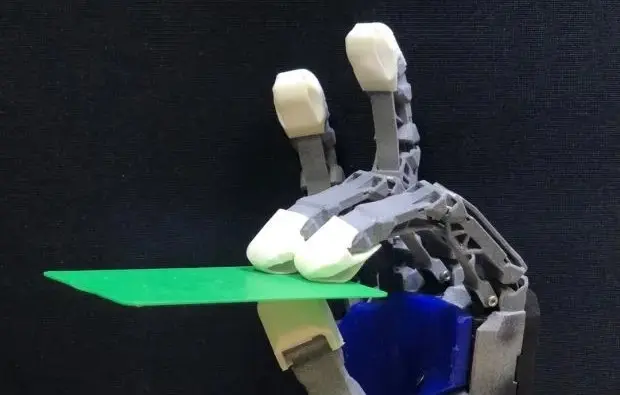
” The simple fabrication of the ST3P hand could help us take another step towards the realization of fully personalized robotic hand prostheses at low cost and effort ,” he says. they explained.
The research group opted for single-step 3D printing due to its ability to generate complex designs without the need for further assembly. The use of this printing technology has simplified the creation of mobile mechanisms ready for immediate use.
Despite the challenges encountered in terms of precision limits when employing 3D printing, as well as the inability to produce a tightly coupled moving surface, the team has addressed these issues by designing joints that feature a gap between the parts. This strategy contributes to allowing the hand to make independent movements, overcoming the limitations mentioned above.
” We simulated the anatomical structure of the human finger joint and implemented a cam effect that changes the distance between the contact surfaces by elastic flexing of the ligaments as the joint flexes, ” they explained.
Don’t miss any of our posts and follow us on social media!
Inspenet.com YouTube LinkedIn Facebook Instagram
Source: the-sun.com