Table of Contents
- Introduction
- Zinc plating fundamentals and applications
- Galvanized fundamentals and applications
- Five key differences between zinc plating and galvanized
- Metallic coatings and their importance
- Surface treatments: Techniques and benefits
- Corrosion Protection
- Coating service life
- Recommendations for maximizing the durability of the coatings
- Zinc plating vs. galvanized: Which is more effective?
- Conclusions
- References
Introduction
In the metallurgical industry, the choice between zinc plating vs. galvanized makes all the difference in terms of corrosion protection. Both methods apply zinc to the base metal to protect against corrosion and extend the life of metal structures, but the techniques and applications are very different. Understanding the difference between the two processes is critical to optimizing protection and ensuring the longevity of metal structures.
Zinc plating, usually performed by an electrolytic process, is ideal for small parts and high-precision components, as it provides a uniform zinc layer of controlled thickness. galvanized, on the other hand, usually performed by hot-dip galvanized, provides a strong and durable protection suitable for structures exposed to aggressive environments. Understanding the differences between these methods and their applications is significant in corrosion protection.
Zinc plating fundamentals and applications
Zinc plating is a process by which a layer of zinc is electroplated onto a base metal, typically steel, to protect it from corrosion. This process is commonly carried out through electrolytic zinc plating, also known as electro galvanized In this method, the part to be coated acts as a cathode in an electrolytic solution containing zinc salts. When an electric current is applied, zinc ions are uniformly deposited on the surface of the metal. Common zinc plating applications include fasteners, automotive parts, electrical equipment and machinery components.
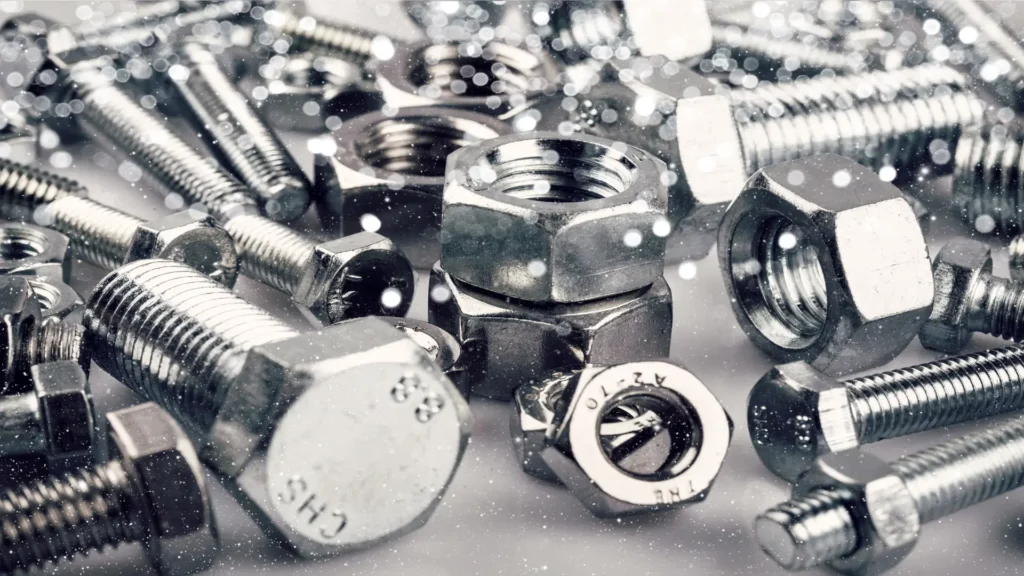
Electrolytic zinc plating is characterised by its ability to produce a zinc layer of controlled and uniform thickness, which is ideal for high-precision components and small parts. This method allows the thickness of the coating to be adjusted according to the specific protection and usage needs of the component. In addition, zinc plating provides an aesthetically pleasing finish and can improve the adhesion of paints and other coatings.
This method is especially valuable in industries where precision and surface quality are essential, as well as in applications where components are exposed to moderate corrosion conditions. The choice of zinc plating ensures effective and economical protection, prolonging the life of metal components and improving their performance in a variety of industrial applications.
Here is a short video about this process. Source: Physical Metallurgy

Metal plating process | A complete guide to its types and technique.
Galvanized fundamentals and applications
Galvanized is a process of protecting metals, mainly steel, by applying a layer of zinc to prevent corrosion. This method is noted for its ability to provide a physical and cathodic barrier against corrosive agents, significantly extending the service life of metal structures.
Hot-dip galvanizing is the most common and effective method of galvanizing. This process involves immersing the steel part in a bath of molten zinc at temperatures around 450°C (842°F). During immersion, the zinc reacts with the surface of the steel to form a series of zinc-iron alloy layers, topped by an outer layer of pure zinc. These layers provide exceptional corrosion protection. The outer zinc layer acts as a physical barrier, while the zinc-iron alloy layers provide cathodic protection that sacrifices the zinc in place of the steel if the surface layer is damaged.
Common galvanizing applications
Hot-dip galvanizing is widely used in industries where durability and corrosion resistance are critical. Common applications include steel building structures (bridges, buildings, transmission towers), infrastructure components (guardrails, light poles, guard rails), agricultural equipment and machinery, as well as pipelines and ducts exposed to aggressive environments. The robustness and longevity of galvanized coating make it a preferred choice for projects requiring long-term protection from the elements. Furthermore, its cost-effectiveness and ease of maintenance additionally favour its use in a wide range of industrial and construction applications.
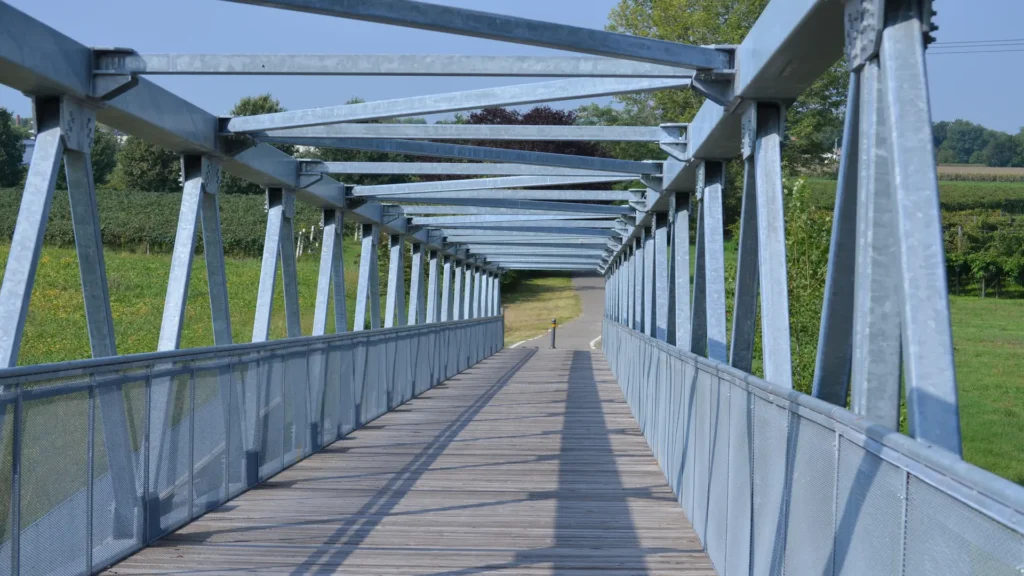
Five key differences between zinc plating and galvanized
- Differences in the application process: Zinc plating and galvanized are different methods in their application. Zinc plating, especially electrolytic zinc plating, involves dipping the part in an electrolytic solution of zinc salts and applying an electric current to deposit a uniform layer of zinc. In contrast, hot-dip galvanizing immerses the part in molten zinc, creating a protective coating by reacting the zinc with the steel.
- Differences in coating thickness: Electrolytic zinc plating produces thinner zinc layers, generally between 5 and 25 microns, suitable for precise parts and small components. Hot-dip galvanized produces thicker coatings, typically between 50 and 150 microns, offering greater protection for structures exposed to harsh environments.
- Differences in coating life: Due to its greater thickness, hot-dip galvanized coatings have a longer life, resisting corrosion better in aggressive environments. Electrolytic zinc plating, while providing good protection, is more suitable for less demanding conditions and requires more frequent maintenance.
- Differences in corrosion resistance: Hot-dip galvanized provides a robust physical barrier and cathodic protection that prevents corrosion even if the coating is damaged. Electrolytic zinc plating, while effective, does not provide the same level of cathodic protection and is more susceptible to mechanical damage.
- Differences in applications and costs: Electrolytic zinc plating is preferred for small, high-precision parts in applications such as automotive and electronics, where surface finish is critical. Hot-dip galvanized, due to its durability, is ideal for large structures such as bridges and transmission towers. In terms of cost, electrolytic zinc plating tends to be more economical for small parts, while hot-dip galvanized, although more expensive, offers a favorable cost-benefit ratio for large industrial applications.
Metallic coatings and their importance
Metallic coatings are layers applied on the surface of a base metal to protect it against corrosion, improve its appearance and increase its durability. These coatings can be of different types, including zinc, nickel, chromium, and other metals that offer various protective and decorative properties.
Surface treatment is crucial in engineering and manufacturing, as it directly affects the corrosion resistance, wear and performance of components. Proper treatment can significantly extend the service life of materials and reduce maintenance and replacement costs. In addition, surface treatments improve the adhesion of paints and other coatings, optimizing the aesthetics and functionality of products.
Compared to other coatings, such as organic coatings (paints and resins) and ceramic coatings, metallic coatings offer a unique combination of durability and cathodic protection. Organic coatings can be more flexible and decorative, but generally do not offer the same resistance to severe corrosion as metallic coatings. Ceramic coatings, while extremely hard and heat-resistant, can be more brittle and costly to apply. In this context, zinc plating and galvanized stand out for their balance between protection, cost, and ease of application and are preferred methods in many industrial and construction applications.
Surface treatments: Techniques and benefits
Metal surface treatment includes a variety of techniques designed to improve the physical and chemical properties of materials. Among the most common techniques are galvanized, zinc plating, anodizing, phosphatizing, and powder coating. These techniques involve processes such as immersion in chemical solutions, the application of electrical currents, and the use of heat to deposit protective or decorative layers on the base metal.
Benefits of metal surface treatments
Metal surface treatments offer multiple benefits essential to the durability and functionality of products. These benefits include increased corrosion resistance, improving component life; increased wear resistance, reducing the need for frequent maintenance; and improved aesthetic appearance, enhancing the commercial value of products. In addition, some treatments can improve electrical and thermal properties, as well as the adhesion of paints and other additional coatings.
Industrial applications
In the automotive industry, surface treatments are used to protect components such as chassis and engine parts against corrosion and wear. In the construction industry, galvanized steel structures provide durability and strength in bridges and buildings. In the electronics industry, the coating of components improves conductivity and protects against oxidation. These examples highlight the versatility and importance of surface treatments in various industrial applications.
Corrosion Protection
Corrosion protection is critical to the integrity and longevity of metal structures and components. Corrosion can compromise the safety, functionality and economic value of products, making it crucial to implement preventive measures. Proper corrosion protection ensures long-term reliability and operational efficiency.
Both zinc plating and galvanized are effective in preventing corrosion, but differ in their effectiveness depending on the context. Hot-dip galvanized, with its thick layer of zinc and zinc-iron alloys, provides robust and durable protection, ideal for aggressive and outdoor environments. On the other hand, electrolytic zinc plating, with its thinner and more uniform layer, is suitable for applications where precision and aesthetic finish are crucial, although it offers less resistance in highly corrosive environments.
The choice between zinc plating and galvanized depends on several factors, including operating environment, exposure conditions, maintenance requirements and costs. In harsh industrial environments, hot-dip galvanized is preferred for its superior durability. In applications where high precision and aesthetics are required, electrolytic zinc plating is more suitable. Other factors include the size and shape of the parts, as well as the expected life and performance of the coating. Evaluating these factors helps to select the most appropriate protection method for each specific application.
Coating service life
The service life of a coating depends on several key factors:
- Coating thickness: Thicker coatings provide a greater barrier against corrosion, extending the service life of the protected metal. Hot-dip galvanized, for example, offers significantly greater thickness compared to electrolytic zinc plating.
- Quality of the application process: Proper surface preparation and uniformity in coating application are crucial. Poorly prepared surfaces or unevenly applied coatings can have weak points that accelerate corrosion. Environmental conditions: Factors such as humidity, air salinity, and exposure to chemicals influence the corrosion rate. More aggressive environments demand more robust coatings.
- Maintenance: Regular inspections and preventive maintenance, such as cleaning and touching up damaged areas, can extend coating life.
- Type of exposure: Constant exposure to abrasion or mechanical impact can wear the coating, reducing its effectiveness and service life.
Recommendations for maximizing the durability of the coatings
- Proper surface preparation: Make sure to properly clean and prepare the surface before applying the coating to improve adhesion.
- Uniform application: Ensure uniform application of the coating to avoid areas vulnerable to corrosion.
- Selection of the right method: Choose the coating method that best suits the environmental conditions and the intended use of the component.
- Regular inspection and maintenance: Perform periodic inspections and preventive maintenance, such as cleaning and touching up damaged areas.
- Additional protection: Consider using additional coatings or sealants to provide an extra layer of protection in particularly aggressive environments.
Zinc plating vs. galvanized: Which is more effective?
Hot-dip galvanized offers greater durability and corrosion resistance, especially in aggressive environments, due to its thicker zinc coating. However, it can be more expensive and less suitable for small or high-precision parts. Electrolytic zinc plating provides a thinner, more uniform layer of zinc, is more economical and is ideal for applications requiring high precision and a superior aesthetic finish.
galvanized is preferred for large structures exposed to severe conditions, such as bridges, towers and infrastructure components. Zinc plating is more suitable for small parts, automotive components, electronic equipment and applications where surface finish is crucial.
There is no single answer as to which is best; it depends on the context and the specific needs of the application. For robust and durable protection in harsh environments, galvanized is the best choice. For precision and aesthetic finish in less severe conditions, zinc plating is more suitable.
Conclusions
In conclusion, both zinc plating vs. galvanized are effective methods of protecting metals against corrosion, each with its own advantages and disadvantages. Electrolytic zinc plating provides a uniform and aesthetically pleasing coating, ideal for small and high-precision parts, although its protection is less robust in aggressive environments.
Hot-dip galvanized provides superior, long-lasting protection, especially suitable for large structures exposed to harsh conditions. The choice between zinc plating and galvanized depends on multiple factors, such as operating environment, exposure conditions, maintenance requirements and costs.
For applications demanding high durability and outdoor corrosion resistance, galvanized is the preferred choice. However, for components that require precision and an aesthetic finish, zinc plating is more suitable. Understanding the differences between these methods allows engineers to make informed decisions and optimize the protection of their projects, ensuring greater longevity and performance of metallic materials.
References
Own source