Table of Contents
Introduction
Do you know what turnkey construction is? This type of contracting has positioned itself as one of the most efficient and safe options for the development of construction projects. In this model, a single contractor assumes full responsibility for the delivery of the project, from initial planning to commissioning. This allows for more efficient management and ensures that the client receives the work completely finished and ready for use.
In this article, the characteristics, phases, and strategies required to manage risk in this model are presented. It also discusses quality assurance at each stage of the project and what tools are necessary for its success.
What is turnkey construction?
A turnkey construction is a contracting model in which a single contractor or developer is in charge of the entire project, from conception to final delivery. The client delegates to a single entity all the tasks: design, planning, procurement of materials, execution of the work, testing, and commissioning of the facilities.
The main benefit of this model is simplicity. The client only needs to provide the initial requirements, while the contractor manages all the activities necessary for execution. This type of project is one of the most attractive contract modalities for large-scale projects, such as commercial, industrial, highway, or airport facilities, as it minimizes management complexity.
Characteristics of a turnkey project
Turnkey construction projects are characterized by integrated management, where a single supplier assumes all responsibility. Among its main advantages are having a single point of contact, which facilitates communication, and coordination. In addition, fixed prices and defined deadlines ensure that the client knows the total cost and delivery dates, reducing the risk of cost overruns and delays.
The turnkey contracting model allows for customization according to the client’s requirements, ensuring that the end result is aligned with their needs. It also includes a quality guarantee, both at the end of the project and in the post-delivery phase. Finally, the delivery of complete technical documentation guarantees the construction process.
When to choose a turnkey project?
This type of project is chosen when multiple disciplines (such as engineering, architecture, and construction) need to be coordinated in an efficient manner. It is particularly beneficial in cases where deadlines are tight or fast turnaround is required. This contracting model is also suitable for those who wish to maintain a fixed and predictable budget, controlling costs from the outset and avoiding over-financing.
Additionally, it is an excellent option for clients with no experience in construction project management, because the responsibility for technical supervision rests with the contractor, who guarantees delivery of the project according to the agreed specifications.
The following video explains what turnkey projects are, their pros and cons for a client.
Phases of a turnkey construction project
Turnkey projects consist of several interconnected phases, each critical to success, which require detailed planning and execution. The most common phases are listed below:
- Pre-planning and conceptualization: In this phase, the technical, economic, and legal feasibility of the project is evaluated, the terrain and associated risks are analyzed. Subsequently, a conceptual design is developed to define the scope of the project, followed by the selection of the appropriate site.
- Detailed design and planning: The contractor, in collaboration with the client, defines the project requirements. In this phase, engineering drawings and specifications are developed and all necessary permits and approvals are obtained.
- Procurement and contracting: After design, the contractor procures the materials and hires the necessary subcontractors or specialized personnel to execute the work. This phase includes the negotiation of delivery dates and costs, guaranteeing the quality of the inputs.
- Execution of the work: In this phase the project is materialized. The contractor coordinates and supervises the construction, ensuring that the activities are carried out within the established budget and time. Quality controls and continuous inspections are carried out.
- Testing and start-up: Upon completion of construction, functional tests are performed to verify that the facilities, systems, and equipment are operating correctly.
- Handover and closeout: The project is formally handed over to the client, ready for use. The contractor provides complete technical documentation (as-built drawings, operating manuals) for future maintenance.
- Post-contract phase: After handover, the contractor follows up to ensure that everything is working properly. Warranties on the work are usually provided to address any issues that arise after delivery.
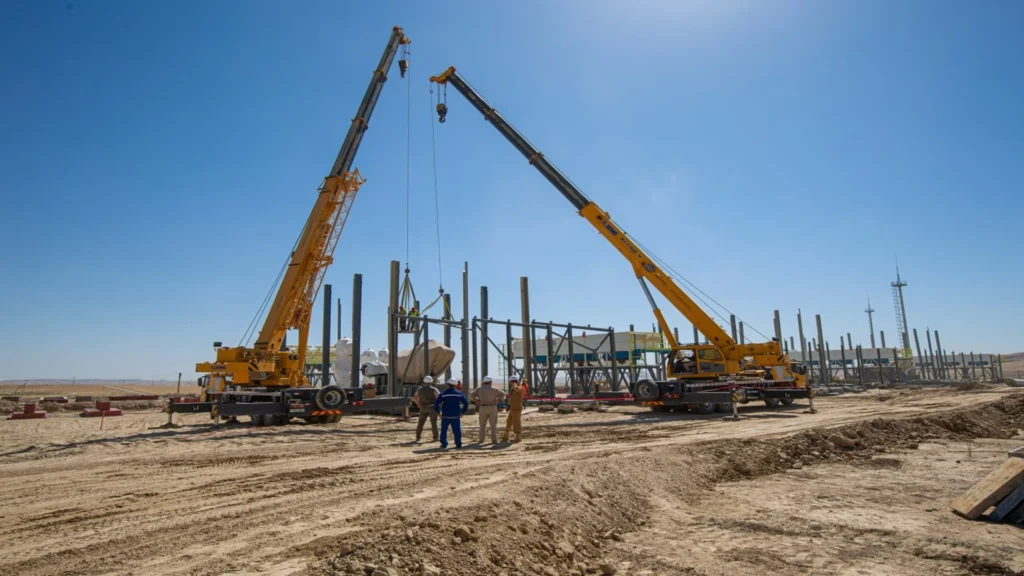
Comparison of turnkey construction vs. other contracting models
Turnkey construction vs. separate contracting
In separate contracting, the client assumes responsibility for managing different suppliers and contractors for each stage of the project, such as design, construction, and installation. This requires a high level of coordination and increases the risk of delays and cost overruns, in which case the client must oversee multiple contracts and ensure that each supplier meets established deadlines and standards.
In contrast, in the turnkey construction model, responsibility is centralized in a single contractor. This simplifies management by avoiding the need to coordinate multiple players, which minimizes risks and reduces the possibility of conflicts between different suppliers. In addition, the client has greater control over costs and deadlines, establishing a fixed price and defined delivery dates from the beginning of the project.
Turnkey construction vs. EPC model (Engineering, Procurement, Construction)
The EPC (Engineering, Procurement, Construction) model is similar to the turnkey model in that the contractor assumes responsibility for engineering, materials procurement, and construction. However, in the EPC, the client can have a greater say in project decisions, especially in the design and supplier selection phase, which is useful in projects where the client desires greater technical control or a more customized approach in certain areas.
On the other hand, the turnkey model is more suitable for projects where the client is looking for less involvement in the day-to-day management, where the contractor is in charge of execution and takes responsibility for delivering a fully completed and ready-to-use project. In terms of schedule and cost control, this model tends to offer greater flexibility.
Although both models transfer much of the risk to the contractor, the turnkey approach is more efficient in schedule and budget management, as the client does not need to be actively involved during project development, making it a preferred option for those who want a simplified process with financial certainty.
How to manage risks in turnkey construction projects
To manage risks in these turnkey construction projects, it is necessary:
- Early identification of risks: Assess all potential risks and create a matrix to rank them by likelihood and impact.
- Risk mitigation: Develop a risk management plan and have adequate insurance in place. Hiring an experienced contractor is key, as is establishing a contingency reserve.
- Monitoring and control: Define performance indicators (KPIs) and periodically review the risk plan, maintaining transparent communication with all parties involved.
- Mitigation strategies: Transfer some risks to the contractor through contractual clauses and mitigate others to reduce their impact.
How to ensure the quality of a turnkey project
Quality assurance is critical at every stage of the project:
- Detailed planning: Ensure accurate design and feasibility studies from the outset.
- Materials selection: Work with reliable suppliers and regularly audit materials.
- Construction controls: Conduct regular inspections and employ advanced real-time monitoring technologies.
- Testing and commissioning: Verify proper operation of all systems prior to delivery.
- Documentation and reporting: Provide comprehensive reporting, ensuring transparency and compliance with agreed standards.
These processes are based on quality management systems, such as ISO 9001, which allow standardizing processes, detecting and correcting deviations, auditing, and promoting continuous improvement.
Recent trends in turnkey projects
New trends, such as the use of Building Information Modeling (BIM) and modular manufacturing, are reshaping the way these types of projects are managed. New technologies improve efficiency, reduce costs, and facilitate coordination between teams. In addition, the use of advanced software such as Primavera P6 and Microsoft Project, and collaborative platforms such as Asana and Trello optimize planning and deadline control, reducing the risk of delays.
In addition, the integration of these systems allows for improved decision-making, as real-time data facilitates early identification of problems and their rapid resolution, improving productivity and efficiency in all phases.
Conclusions
The turnkey construction model is an efficient and safe solution for large construction projects. By using this contracting model, the client delegates full responsibility to a single contractor, allowing for more effective control over costs and schedules, while reducing the risks associated with coordinating multiple players.
This approach, characteristic of this type of construction, facilitates a controlled, efficient, and high-quality execution, which makes it an ideal option for those projects that require comprehensive and personalized management.
References
- https://www.propertypistol.com/blog/what-is-turnkey-project-and-meaning/
- https://www.investopedia.com/terms/t/turnkey_solution.asp