Ammonia, a chemical compound with the formula NH3, is a molecule composed of one nitrogen atom and three hydrogen atoms. This colorless gas, with a characteristic pungent odor, is fundamental in various industries due to its versatility and unique properties. In the oil and gas industry, ammonia plays a crucial role in several processes and applications, from fertilizer production to refrigeration and the manufacture of chemicals.
This article aims to explore in depth what ammonia is, its physical and chemical characteristics, its functions and uses, its environmental impact, and its specific relevance in the oil and gas industry. By the end, you will better understand the importance of this chemical compound and how its handling and application affect various industrial sectors.
What is ammonia?
It is a chemical compound with the formula NH3, where one nitrogen atom is covalently bonded to three hydrogen atoms. This molecule is notable for being a colorless gas with a strong characteristic odor and highly soluble in water. Among its physical properties, its boiling point at -33.34 °C and melting point at -77.73 °C stand out. Chemically, ammonia is a weak base that can react with acids to form ammonium salts.
Ammonia is naturally found in the atmosphere as a result of the decomposition of organic matter and biological processes in the soil. However, most of the ammonia used industrially is produced synthetically. The Haber-bosch process is the predominant method for industrial ammonia production, combining nitrogen from the air with hydrogen derived mainly from natural gas under high pressures and temperatures in the presence of a catalyst. This process has enabled large-scale production of ammonia, which is essential for the agricultural industry and numerous industrial applications.
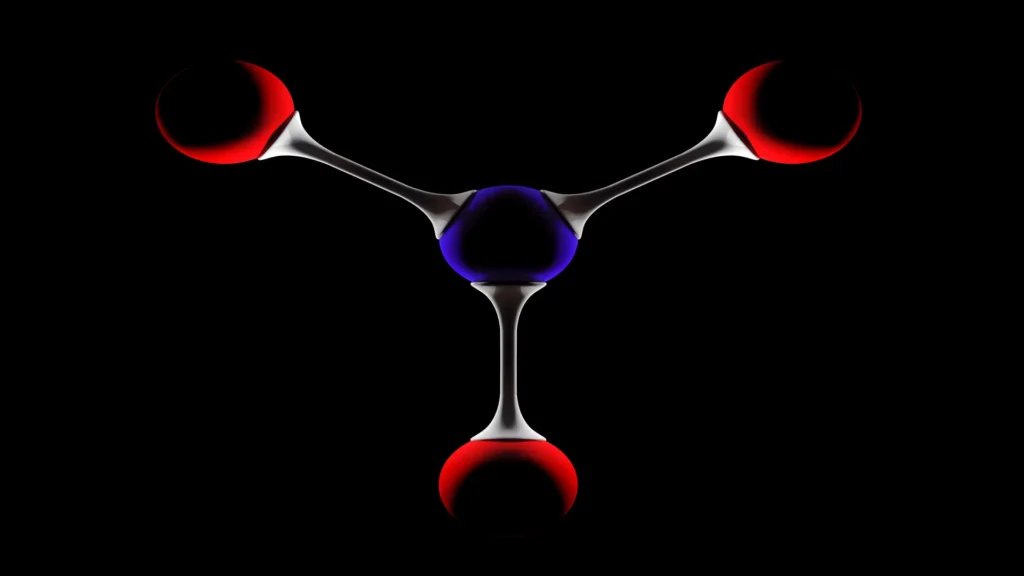
The Haber-Bosch process
The Haber-Bosch process is a chemical synthesis reaction that combines nitrogen from the air with hydrogen, generally derived from natural gas, to produce ammonia (NH3). This process is one of the pillars of the modern chemical industry and is fundamental for the large-scale production of nitrogen fertilizers. The technical process is detailed below:
Chemical reaction:

This reaction is exothermic, releasing energy in the form of heat.
Raw materials:
- Nitrogen (N2): Obtained from the air, which contains approximately 78% nitrogen.
- Hydrogen (H2): Generally produced from natural gas (methane, CH4) through a steam reforming process.
Haber-Bosch process stages
Natural gas reforming
- Methane is mixed with steam and passed over a nickel catalyst at high temperatures (700-1,000 °C).

This step produces carbon monoxide and hydrogen gas.
Carbon monoxide conversion
The resulting carbon monoxide is mixed with more steam and passed over a second catalyst at a lower temperature (200-450 °C).

This produces more hydrogen and carbon dioxide.
Hydrogen purification
- The carbon dioxide is removed from the synthesis gas (a mixture of H2, CO, and CO2) through a water wash or by using amines.
Ammonia synthesis
- Pure hydrogen gas is combined with nitrogen in a 3:1 ratio.
- The gas mixture is introduced into a reactor at high pressure (150-300 atmospheres) and high temperature (400-500 °C) in the presence of an iron catalyst.

Process conditions
- Pressure: 150-300 atmospheres.
- Temperature: 400-500 °C.
- Catalyst: Commonly iron with promoters such as potassium and aluminum.
Separation and recycling
- The produced ammonia is cooled and separated from the unreacted gas.
- The unreacted gases (mainly N2 and H2) are recycled back to the reactor to maximize process efficiency.
Watch video of the Haber-Bosch process for producing ammonia

What is the Haber-Bosch process?
Importance of the Haber-Bosch process
The Haber-bosch process revolutionized ammonia production, enabling the large-scale synthesis of nitrogen fertilizers, which has been crucial for modern agriculture and global food supply. Additionally, the produced ammonia is used in a wide variety of industrial applications, from the manufacture of explosives to the production of plastics and textiles. This process is a key example of the importance of industrial chemistry in the global economy and human well-being.
What ammonia is used for and its use in different industries
Applications in agriculture (fertilizers)
It is essential in the production of nitrogen fertilizers, which are vital for modern agriculture. Through the Haber-Bosch process, ammonia is synthesized and then converted into ammonium nitrate, ammonium sulfate, and urea. These fertilizers provide nitrogen to the soil, a crucial nutrient that promotes plant growth and increases agricultural yields.
Uses in the industrial refrigeration
It is an efficient and economical refrigerant used in industrial refrigeration systems, such as food processing plants and cold storage. Due to its high coefficient of performance (COP), ammonia is preferred in applications that require a large refrigeration capacity. However, its toxicity requires rigorous safety measures for handling and storage.
Applications in cleaning products
It is used in domestic and industrial cleaning products due to its ability to break down fats and oils. It is commonly found in window cleaners, degreasers, and detergents. Its effectiveness in removing stains and residues makes it a valuable component for various cleaning formulations.
Use of ammonia in the oil and gas industry
In the oil and gas industry it is employed in several key processes. One of the most important applications is in the reduction of nitrogen oxides (NOx) through Selective catalytic reduction (SCR) technology. This process involves injecting ammonia into the exhaust gases, where it reacts with NOx in the presence of a catalyst to produce nitrogen and water, significantly reducing pollutant emissions.
Ammonia is also used in the production of hydrogen through steam reforming of natural gas, a fundamental process for petroleum refining. The generated hydrogen is used in hydrotreating and cracking, which are critical processes for producing clean and high-quality fuels. Additionally, ammonia is a precursor in the synthesis of numerous chemical products used in the oil and gas industry.
Characteristics of ammonia
Physical and chemical properties
It is a colorless gas at standard atmospheric temperature and pressure. It liquefies easily at moderately high temperatures and pressures, with a boiling point of -33.34 °C and a melting point of -77.73 °C. Its liquid density is approximately 682 kg/m³ at its boiling point.
Solubility and reactivity
It is highly soluble in water, forming a solution known as ammonium hydroxide (NH4OH). This solution is a weak base, allowing it to react with acids to form ammonium salts. Additionally, ammonia can react with certain metals and halogenated compounds, exhibiting significant reactivity under various industrial conditions.
Toxicity and safety measures
It is toxic and can cause severe irritation to the eyes, skin, and respiratory system. Exposure to high concentrations can result in severe and potentially fatal lung damage. Due to these risks, the handling of ammonia requires strict safety measures, including adequate ventilation systems, personal protective equipment (PPE), and emergency procedures for leaks and spills. Facilities that use ammonia must comply with specific safety and environmental regulations to minimize the risks associated with its use and storage.
Function of ammonia
It is essential in various industrial processes due to its versatility and chemical properties. In the synthesis of other compounds, it acts as a raw material in the production of fertilizers, explosives, pharmaceuticals, and textiles. Its ability to react with acids forms ammonium salts, vital for multiple applications.
In reducing pollutant emissions, ammonia plays a crucial role in Selective catalytic reduction (SCR) technology. This process converts nitrogen oxides (NOx), harmful to the environment, into harmless nitrogen and water, significantly decreasing air pollution.
The importance of ammonia in hydrogen production and its derivatives is notable. Hydrogen produced from ammonia is used in petroleum refining and methanol synthesis. Additionally, as an energy carrier, ammonia facilitates the storage and transport of hydrogen, a key component in clean energy technologies.
Impact of ammonia
The environmental impact of ammonia is significant. In high concentrations, it can cause acidification of soil and water bodies, affecting local flora and fauna. Additionally, its accidental release into the atmosphere can contribute to smog formation and the eutrophication of aquatic ecosystems.
The risks associated with the handling and storage of ammonia are considerable due to its high toxicity and ability to form explosive mixtures with air. Direct exposure can cause respiratory and ocular irritation, and in severe cases, lung damage.
Mitigation and regulatory measures are essential to control these risks. They include the implementation of leak detection and containment systems, rigorous training for personnel, and strict compliance with environmental and safety regulations. The adoption of safe practices and advanced technologies ensures the minimization of the negative impact of ammonia on the environment and human health.
Conclusions
Ammonia, with its formula NH3, is essential in many industries, from agriculture to energy production. Its ability to form fertilizers through the Haber-bosch process has been crucial for the development of modern agriculture, significantly increasing food production. Additionally, in the oil and gas industry, ammonia is used to reduce pollutant emissions and produce hydrogen, both vital for the creation of cleaner fuels.
However, its handling presents risks due to its toxicity and potential danger to health and the environment. Exposure to ammonia can cause irritation and, at high concentrations, severe damage. Therefore, it is essential to follow strict safety measures and regulations to minimize these risks.
In summary, although ammonia is invaluable in many industrial processes, it is crucial to handle it with care and responsibility to take advantage of its benefits without compromising safety and the environment.
References
Own source