Table of Contents
- Introduction
- Corrosion by hydrogen sulfide or hydrogen sulfide (H2S) in aqueous media
- Environmental and operational variables
- Susceptibility of materials and areas to damage by wet H2S
- Types of wet H2S damage
- Prevention and mitigation strategies
- Implications for safety and maintenance in the industry.
- Conclusions
- References
Introduction
In the vast world of industrial materials science, particularly in the oil and gas industry, the mechanism of wet H2S1 represents a significant challenge. This industry, with its extensive use of materials such as steel in piping and storage facilities, often faces challenges due to this type of damage.
The wet H2S damage mechanism occurs when hydrogen sulfide (H2S), a colorless, toxic and flammable gas naturally present in crude oil and natural gas, comes into contact with water, dissolving and forming a weak acid hydrogen sulfide (H2S) that accelerates corrosive processes, particularly in iron and steel-based materials.
This article discusses in detail the corrosion caused by wet H2S, the mechanism of formation, as well as the conditions that cause it, the most susceptible materials, prevention strategies and its broad impact on industrial safety and maintenance.
Corrosion by hydrogen sulfide or hydrogen sulfide (H2S) in aqueous media
Hydrogen sulfide is an acidic compound and when dissolved in water generates protons (H+) and this cathodic species is easily reduced if it encounters a compound that can be oxidized, as is the case of iron contained in steels (corrosion process).
Mechanism of Wet H2S Damage Mechanism
The H2S corrosion mechanism can be described in four stages:
- H2S + H2O ⇔ H+ + HS– (1)
- HS– + H2O ⇔ H+ + S= (2)
- Fe → Fe+2 + 2e– (3)
- Fe+2 + 2H+ + S= + 2e– → FeS + H2 (4)
- Stage (1): Cathodic zone. Iron sulfide (H2S) in aqueous media (H2O) dissociates into positive hydronium ions (H+) and negative bisulfide ions (HS–).
- Stage (2): Cathodic zone. The bisulfide ion (HS–) in aqueous media produces hydronium ions (H+) and sulfide ions (S–).
- Stage (3): Anodic zone. In turn, the Fe present in the metal oxidizes and produces ferrous ions (Fe+2) at the anode.
- Stage (4): The cathodic species (2H+) produced in stages (1) and (2) react with the ferrous ion (Fe+2) and are reduced to their atomic (H) form generating iron sulfide oxides (FeS), as corrosion products [FeSx], and molecular hydrogen (H2).
This mechanism can cause confined space corrosion (crevice and pitting) and hydrogen embrittlement.
Confined space corrosion
Hydrogen sulfide H2S is an aggressive gas, which in contact with an aqueous medium forms a weak acid hydrogen sulfide (H2S) causing hydrogen sulfide acid corrosion, accelerating corrosion processes particularly in iron and steel based materials.
H2S reacts with different iron oxides to form iron sulfides, which precipitate, forming deposits of corrosion products, generating localized corrosion, such as pitting or crevices. A schematic of this mechanism is shown in Figure 1.
It is important to mention that corrosion deposits, under certain pressure and temperature conditions, can act as a barrier or protective layer that isolates the metal from the aggressive medium, slowing down the corrosion process.
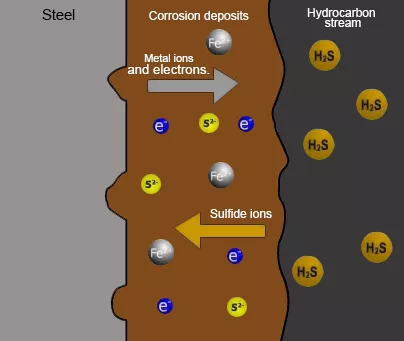
Hydrogen embrittlement
Hydrogen atoms generated in the corrosion process permeate through the metal surface and accumulate in metallurgical defects in the pipe, which can lead to embrittlement of the steel and crack initiation2 ( Figure 2).
Hydrogens in their ionic form (H+) are reduced on the metal surface to their atomic form (H) and permeate into the interior of the metal, combining to form molecular hydrogen (H2), causing blisters and generating high pressure. These blisters usually form on impurities at grain boundaries, reducing the ductility of the material.
Hydrogen embrittlement, a type of deterioration that can be linked to corrosion processes, involves the permeation of hydrogen into a component, an event that can reduce ductility and load carrying capacity, cause cracks and catastrophic brittle failure at stresses below the yield strength of susceptible materials.
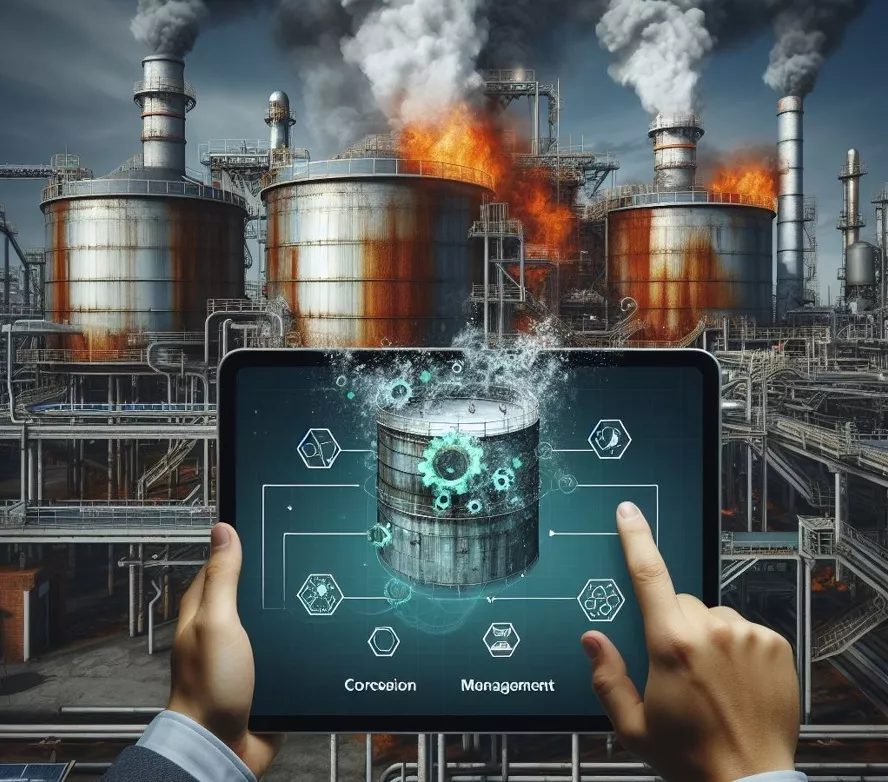
Understanding the chemistry behind the interaction between H2S and water is critical to implementing effective prevention and mitigation strategies. This knowledge enables engineers and industry professionals to identify areas of risk, select appropriate materials and apply protective treatments to extend the life of infrastructure and equipment.
Environmental and operational variables
In the oil and gas industry, environmental and operational conditions play a crucial role in determining the intensity and rate of wet H2S corrosion. High temperature and pressure, typical in oil and gas extraction and processing, significantly exacerbate this type of corrosion. Factors such as temperature, pressure, pH and turbulence can significantly aggravate corrosion, especially in industrial installations such as those in the oil and gas industry. Effective process control is vital to mitigate the intensity and rate of wet H2S corrosion by adjusting factors such as temperature and pressure in oil and gas operations.
High pressure and temperature conditions
The solubility of H2S in water increases with temperature and pressure. In deep drilling operations and high-pressure industrial processes, such as oil refining and natural gas processing, high-temperature and high-pressure conditions are common. These conditions increase the ability of H2S to dissolve in water, forming hydrosulfuric acid. This acid is a more concentrated and aggressive corrosive agent, which means that it can accelerate the corrosion process in exposed materials such as pipes and storage tanks. In addition, high temperatures can alter the mechanical properties of materials, making them more susceptible to corrosion and stress cracking.
2. Low pH values
Low pH environments, i.e. more acidic conditions, exacerbate corrosion caused by wet H2S. Hydrosulfuric acid contributes to the acidification of the environment, which can lead to an increased rate of corrosion of metals such as steel. This situation is aggravated in the presence of other acids, such as sulfuric acid or hydrochloric acid, commonly present in industrial wastewater or drilling fluids. Metallic materials under these conditions wear more rapidly, leading to a reduction in their service life and increasing the risk of structural failure.
3. High flow velocities in turbulent regime.
Turbulence and high flow rates in systems such as pipelines and processing equipment also influence erosion-corrosion mechanisms. Turbulence can cause particles and sediment in the fluid to strike and erode metal surfaces, removing protective layers and exposing the material to more direct corrosion. This erosion, combined with chemical corrosion caused by H2S, accelerates the degradation of materials.
Susceptibility of materials and areas to damage by wet H2S
In the oil and gas industry, certain materials and areas are disproportionately affected by wet H2S corrosion. This is particularly evident in infrastructure components such as pipelines and storage tanks commonly used in this industry, especially in the oil and gas industry. Understanding the susceptibility of different materials and areas is essential to prevent and mitigate associated risks.
Materials
In wet H2S corrosion control, the selection of materials varies depending on the susceptibility to wet H2S damage:
– Carbon steels: Commonly used in industry due to their strength and cost-effectiveness. However, they are particularly vulnerable to corrosion in the presence of H2S, especially when water is involved. The combination of H2S and water can cause loss of structural integrity due to accelerated corrosion and sulfide-induced cracking.
– Low alloy steels: Although they offer higher corrosion resistance than carbon steels, these steels are not immune to wet H2S damage. Under high stress conditions, they can suffer from sulfide cracking, a form of corrosion that severely compromises the structural integrity of the material.
– High alloy steels (such as stainless steel): These steels contain high amounts of chromium, nickel and other alloying elements that improve their corrosion resistance. Although they are more resistant to wet H2S damage, they are not completely immune to it, especially in environments with high H2S concentrations and severe corrosive conditions.
– Non-metallic materials: Advanced polymers and composites offer significant resistance to wet H2S corrosion and are increasingly used in applications where corrosion risk is high. However, their selection should be carefully based on the specific operating environment and the chemical properties of the H2S.
Susceptible areas
Deterioration caused by wet hydrogen sulfide (H2S) poses a significant challenge in carbon and low alloy steels, being a major concern in the oil and gas industry. This problem is not limited to this sector; H2S is a common compound also in mining, the food industry, paper and pulp manufacturing, wastewater treatment and power generation. Specifically, equipment exposed to more than 50 ppm H2S and temperatures below 180°F in acidic aqueous environments are highly susceptible to this type of corrosion.
Vulnerability to H2S damage is aggravated in older or lower quality steels. These materials often have a high number of inclusions, laminations and manufacturing defects, both in the base metal and in the weld zones. It has been observed that steel plates, in particular, are more prone to these defects compared to other forms of steel products. This implies that items such as pressure vessel bodies, tanks and large diameter welded pipe sections are more prone to wet H2S damage compared to standard seamless pipes, tubes or forgings.
In the context of specifically susceptible areas, pipelines carrying crude oil or natural gas stand out for their vulnerability. Their constant exposure to H2S and water mixtures makes them prone to internal corrosion, which can result in leaks or even catastrophic ruptures. Similarly, storage tanks, essential for handling crude oil and refined products, face risks of material degradation and contamination of stored contents due to wet H2S damage.
This type of corrosion compromises the structural integrity of the tanks, highlighting the importance of proper maintenance and design. Likewise, valves and control equipment, essential for the safe operation of the facilities, are also at risk. These components, being at points where the interaction between gas and water is more frequent, become critical areas of concern. Preventing damage in these areas is vital to ensure continuity and safety in operations, underlining the need for careful design and rigorous preventive maintenance.
Types of wet H2S damage
There are several types of damage associated with the presence of wet hydrogen sulfide (H2S) in metals, especially in steels. Among these types of deterioration, the following stand out:
Formation of hydrogen blisters or bubbles
This phenomenon manifests itself as internal cavities or protrusions in the steel, caused by the accumulation of molecular hydrogen (H2)3. These blisters generally form in areas where the steel has imperfections such as non-metallic inclusions, laminations or discontinuities in its structure, causing visible deformation and metal fragility3 (Figure 3), on the internal or external surface of equipment operating under pressure, and can sometimes lead to cracks extending from its perimeter, especially in areas near welds.
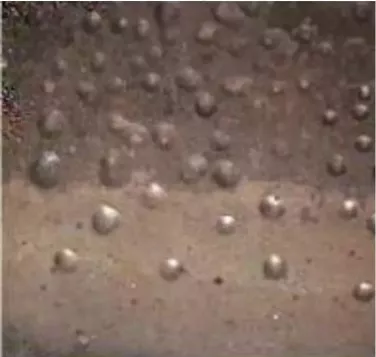
Cracking Induced Cracking (HIC)
Hydrogen Induced Cracking, this type of internal damage is characterized by the appearance and expansion of small cracks or cavities inside the steel, which generally have an orientation parallel to the internal and external surfaces of the material. These cracks may coalesce over time, driven by internal pressure and stresses in the affected areas, and may extend through the thickness of the material, resulting in a sudden fracture, as shown in Figure 4.
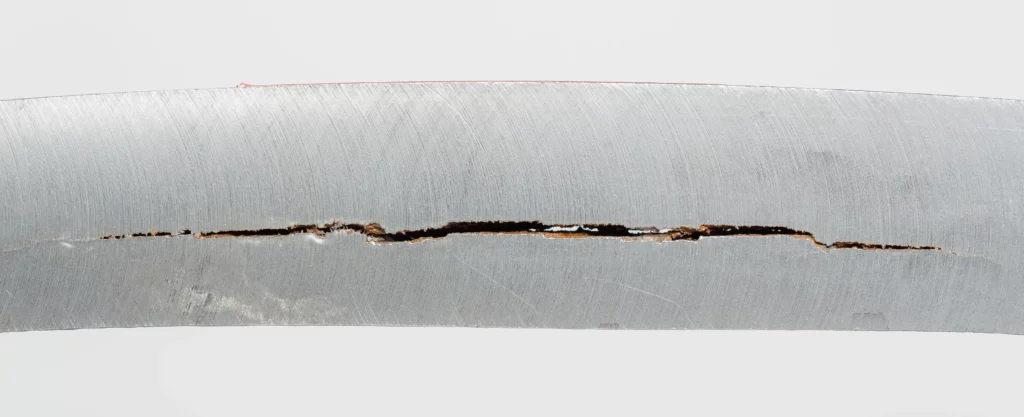
In the case of high strength hard steels, the combination of lack of ductility and internal stress coupled with tensile stress causes cracking and subsequent rupture of the metal, resulting in cracks in the zone of maximum stress and when a critical concentration is reached, a crack is formed, the process continues until the remaining metal cannot withstand the applied load.
Sulfide Stress Cracking (SSC)
This type of cracking, known as Sulfide Stress Cracking4 ( Figure 5), occurs when hydrogen infiltrates high-strength steels or alloys in areas of high internal stress, such as at grain boundaries or in areas of triaxial stress, such as notches. The combination of these stresses with the presence of hydrogen can lead to embrittlement of the material and initiation of brittle fractures.
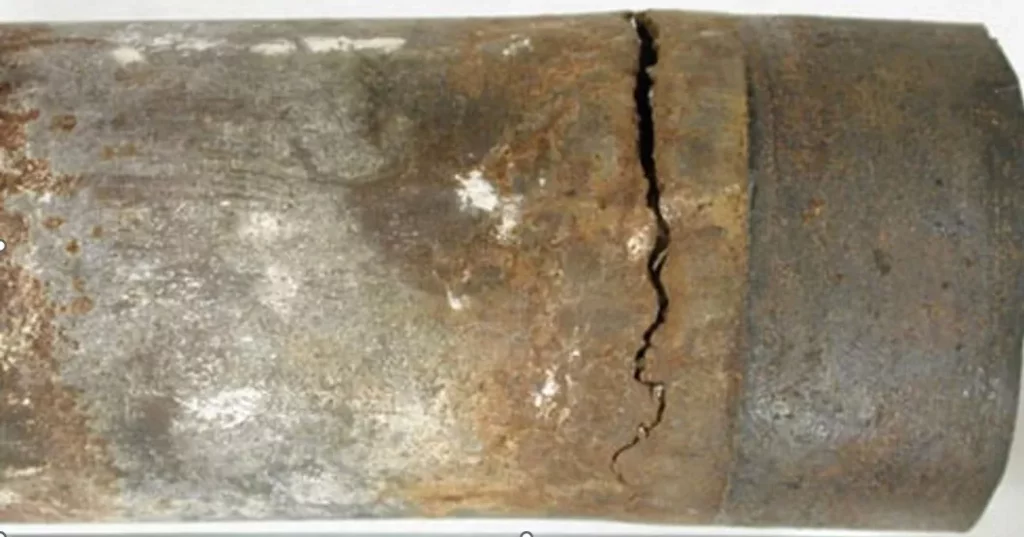
These types of damage are critical in the industry and require specialized attention for prevention and treatment, given their potential to significantly affect the structural integrity and safety of the equipment and structures involved. Pipelines and equipment in oil and sour gas fields containing H₂S have appeared many times with brittle fractures, weld zone cracking and other accidents, which are mainly caused by Hydrogen Induced Cracking (HIC) and Sulfide Stress Cracking (SSC).
Prevention and mitigation strategies
Preventing and mitigating the damage caused by wet H2S is crucial in industries such as oil and gas. The implementation of effective strategies can significantly reduce the risks associated with this type of corrosion.
– Material selection: Choosing H2S resistant materials is a primary strategy. Materials such as high-alloy stainless steels, nickel-based alloys and certain types of plastics and rubbers offer superior resistance to H2S. Although these materials may be more expensive initially, they significantly reduce the need for frequent maintenance and replacement, resulting in long-term savings and increased operational safety.
– Protective Coatings: Protective coatings act as a barrier between the material and the corrosive environment. Epoxy, phenolic and polyurethane coatings are commonly used due to their corrosion resistance and durability. These coatings must be carefully selected and applied, considering the specific operating conditions and type of H2S exposure.
– Cathodic protection: Cathodic protection is a technique that protects metals from corrosion by applying an electric current. This technique can be by sacrificial anodes or by impressed current, depending on the environment and infrastructure. It is particularly effective in subway pipelines and storage tanks, where corrosion can be a significant problem.
– Regular monitoring and maintenance: A regular monitoring and maintenance program is essential to identify and address early signs of corrosion. This includes visual inspections, ultrasonic testing and other non-destructive evaluation techniques. Proactive maintenance can prevent failures and extend equipment life.
– Process control: Among the prevention strategies, process control plays a fundamental role, helping to regulate the conditions that can exacerbate wet H2S corrosion. Controlling operating processes, such as regulating temperature, pressure and pH, is essential to minimize conditions that promote wet H2S corrosion. This may include dehydrating the natural gas to reduce the amount of water present and chemical treatment to neutralize the acids formed.
Implications for safety and maintenance in the industry.
– Safety concerns: Corrosion due to wet H2S poses significant safety risks in industry, especially in the oil and gas sector. The main concern lies in the structural integrity of the equipment and piping. Corrosion can cause weakening and failure of these components, which could lead to leaks of hazardous gases or liquids, fires, explosions or structural collapse. These events not only pose a danger to workers and the environment, but also to the communities near these industrial facilities.
– Economic impact: The economic impact of wet H2S corrosion is considerable. The costs associated with maintaining, repairing or replacing corroded equipment can be enormous. In addition, equipment failures due to corrosion can cause unplanned shutdowns, resulting in lost production and operational efficiency. On the other hand, investing in preventive measures such as selecting appropriate materials, applying protective coatings and cathodic protection systems, although initially costly, can result in significant savings in the long term by reducing the frequency and severity of maintenance and repairs.
– Equipment longevity: Effective corrosion management directly impacts the useful life of infrastructure and equipment. A well-implemented maintenance program, including regular monitoring and proactive mitigation strategies, can prevent premature deterioration of critical components. This not only ensures continuous and efficient operation of the facilities, but also maximizes the investment made in equipment and structures.
Conclusions
he industry’s reliance on materials susceptible to H2S corrosion requires an understanding and strategic approach to mitigate this problem. Understanding the mechanism of wet H2S damage is critical for infrastructure safety and environmental protection. Wet H2S corrosion significantly affects materials such as carbon and low alloy steels, requiring a meticulous approach to material selection and mitigation strategies such as protective coatings and cathodic protection.
Effective management of the wet H2S damage mechanism includes rigorous process control, essential for safety and operational efficiency in the industry. Operating conditions, such as high temperature and pressure, as well as low pH levels and turbulence, intensify corrosion, underscoring the importance of careful design and management of industrial operations. Effective control of these factors can markedly reduce the severity of corrosion.
References
- Herbert H. Uhlig; Corrosion and Corrosion Control; Fourth Edition.
- Wei Zhang; “Evaluation of susceptibility to hydrogen embrittlement: an ascending step-load test method”; Materials Science and Applications, Vol.7. No.8 , August 5, 2016.
- WebCorr The Corrosion Clinic “Hydrogen Blistering”.
- http://met-tech.com/images/preheater-tube-failure-4.jpg