Vibration analysis in gas turbines is used to determine the operating and mechanical conditions of the equipment. A big advantage is that vibration analysis can identify developing problems before they become too serious and cause unscheduled downtime.
This can be achieved by regularly monitoring machine vibrations, either continuously or at scheduled intervals. Regular vibration monitoring can detect damaged or defective bearings, mechanical play, and worn or broken gears. These analyzes can also detect misalignment and imbalance before these conditions cause bearing or shaft deterioration.
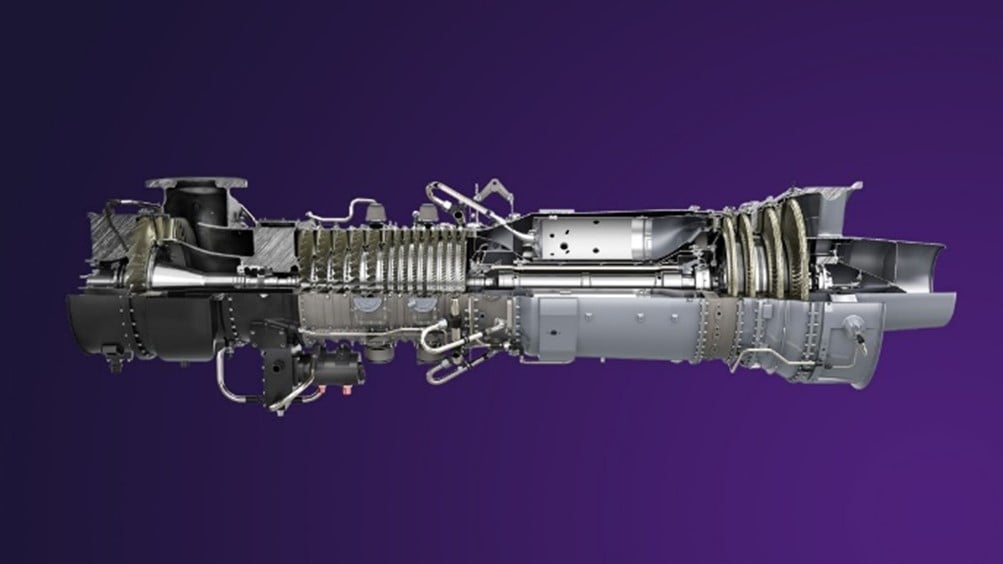
Importance of vibration analysis in gas turbines.
Vibration analysis allows monitoring the dynamic behavior of gas turbines and detecting possible failures or wear in components. By anticipating problems, costly repairs can be avoided and unplanned downtime can be reduced, as well as helping to optimize performance by identifying poor operating conditions that could affect efficiency and fuel consumption.
Instrumentation and measurement techniques.
Vibration analysis requires the use of suitable instrumentation, such as accelerometers and speed sensors, to measure vibrations at different points in the turbine. Measurement techniques may include time-domain and frequency-domain analysis, as well as the use of waveform analysis and spectrograms.
Instrumentation and measurement techniques must be carefully selected to ensure accurate and representative measurements.
Analysis and diagnosis of vibrations.
The analysis of the vibration signals is carried out using specialized software that allows the visualization, processing and analysis of the data. Different types of vibrations, such as axial, radial or high-frequency vibrations, can be identified and their root cause determined.
Accurate vibration diagnosis may involve comparing data to alarm thresholds, analyzing trends over time, and comparing to known vibration patterns.
Improvements in availability and useful life.
By implementing a gas turbine vibration analysis program, several significant improvements can be achieved. First, a predictive maintenance plan must be established based on the early detection of problems, which reduces downtime and associated costs.
New techniques for gas turbines are being developed to improve their performance and efficiency. Growth is led by growth in materials technology, new coatings, new cooling schemes, and the growth of combined cycle power plants.
One approach is to introduce advanced technologies into gas turbine design and manufacturing, such as single-crystalline turbine blades and thermal barrier coatings that can withstand high inlet temperatures.
Single crystal blades are single crystal alloy castings based on Nickel (Ni) and many other metals such as Chromium (Cr) and Cobalt (Co).
The development of these new techniques improves the performance and efficiency of gas turbines. Growth in this field is driven by advances in materials technology, new coatings, innovative cooling schemes, and the growth of combined cycle power plants.
One approach is to incorporate advanced technologies into gas turbine design and manufacturing, such as single-crystalline turbine blades and thermal barrier coatings capable of withstanding high inlet temperatures.
Another approach is based on the use of classical and forward-looking technologies in the design of micro gas turbines.
How to determine the appropriate vibration analysis technique for a specific model of gas turbine?
Determining the appropriate vibration analysis technique requires consideration of the specific characteristics and requirements of the gas turbine.
One approach is to model the mechanical vibrations of the gas turbine system and study the system to achieve the diagnostic and decision-making function.
It is also important to identify locations to acquire vibration readings using accelerometers on the gas turbine and gearbox.
Machine learning techniques can also be used to model the vibration response of a gas turbine and diagnose failures or damage in the internal mechanical components of the different stages that make up a gas turbine.
Vibration analysis plays a crucial role in ensuring gas turbine reliability and is an important component of asset management strategies.
Why vibration analysis is important for gas turbine reliability and how it can be effectively implemented in asset management:
Early detection of failures: Gas turbines operate in adverse conditions and are subject to various mechanical stresses. Vibration analysis allows early detection of failures such as imbalance, misalignment, bearing wear, rotor cracks, and blade damage.
By identifying these issues at an early stage, maintenance and repair activities can be scheduled proactively, minimizing the risk of unexpected failures and costly downtime.
Condition Monitoring – Continuous vibration monitoring provides valuable data on the condition of gas turbines. By analyzing vibration patterns over time, deviations from normal behavior can be identified, indicating potential problems.
This proactive approach allows maintenance teams to take corrective action before failures escalate, extending the operating life of the gas turbine and maximizing its reliability.
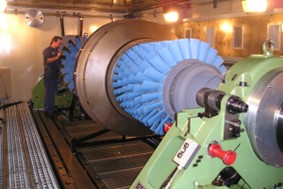
Performance Optimization – Vibration analysis not only helps detect faults, but also helps optimize the performance of gas turbines. By monitoring vibration levels during normal operation, engineers can identify opportunities to improve efficiency, reduce wear and improve overall operating performance. This can lead to energy savings, increased productivity, and longer equipment life.
To effectively implement vibration analysis in asset management for gas turbines, the following steps can be followed:
Establish Baseline Data – Collect baseline vibration data during commissioning or initial operation of the gas turbine. These data serve as a reference for future comparisons and trend analysis.
Set Vibration Limits – Set vibration limits for different gas turbine components based on manufacturer recommendations, industry standards (such as ISO 10816-4), and historical data. These limits will serve as indicators to identify abnormal vibrations.
Continuous monitoring – Use vibration sensors and monitoring systems to collect real-time data on gas turbine vibration levels. This can be done through online condition monitoring systems that provide automatic alerts and trend analysis capabilities.
Data analysis: Regularly analyze vibration data to identify any deviation from established limits. Advanced analysis techniques such as Fourier analysis and waveform analysis can be used to extract valuable information from vibration signals.
Maintenance and intervention: When vibrations outside the established normal range are detected, follow the established maintenance and intervention protocols. This may involve scheduling maintenance activities, performing root cause analysis, and implementing corrective actions to address identified failures.
Documentation and reporting – Maintain complete records of vibration data, analysis results, maintenance activities, and results. This documentation makes it easy to track performance, analyze trends, and support decision making for future asset management strategies.
Overall, effective implementation of vibration analysis in gas turbine asset management enables proactive maintenance, maximizes reliability, optimizes performance, and helps minimize costly unplanned downtime.
Now ensuring sufficient power, its reliable supply and consistent grid quality have become strategic concerns.
However, with the latest advances in highly efficient gas turbine technology, generating power on-site for mains supply to data centers has become much more attractive, solving grid challenges today and in the long term as well.
In the future, these stable, low-emission on-site power generation solutions will be able to run exclusively on carbon-free fuels such as e-hydrogen.
So, it’s time for engineers and operators to get up to speed on how gas turbine power generation can benefit the data center business. To this end, this paper will shed light on market trends and challenges for on-site power generation for data centers, provide valuable insights into gas turbine technology and power generation design.
Sources:
1. https://www.siemens-energy.com/mx/es/soluciones/power-and-heat-generation/turbinas-de-gas.htm https://www.sulzer.com/en/services/spare- partsl
2. https://www.sulzer.com/en/services/spare-parts
3. https://youtu.be/cOcu7szPKmQ
4. https://youtu.be/GF-70yncAVY
5. https://youtu.be/1eiBMqVuPA8
.