Table of Contents
- Fundamentals of corrosion in underground pipelines
- Traditional methodologies vs. recent advances
- Innovative technologies in corrosion control
- Integration of sustainability and regulatory compliance
- Cases of organizations that implement these methodologies
- Cost indicators associated with not implementing advanced technologies
- Conclusions
- References
Corrosion control management has relied on conventional approaches that, although effective to some extent, do not fully address the complexities of the underground environment. However, recent advances in technology and materials science are revolutionizing protection methodologies.
Corrosion in underground pipelines represents one of the most significant challenges in the oil & gas industry. This phenomenon not only carries enormous economic costs, but also poses serious security risks.
These new approaches not only promise greater effectiveness in corrosion prevention and control, but also offer more sustainable and economically viable solutions. This article explores these advances, highlighting how they can transform the way the oil & gas industry protects its critical assets underground.
Fundamentals of corrosion in underground pipelines
Underground corrosion affects pipes, tanks and buried metal structures, mainly due to electrochemical reactions between metal, soil and water. Factors such as soil composition, humidity, temperature and the presence of microorganisms can accelerate this process.
Corrosion can manifest itself in a variety of ways, including uniform corrosion, pitting, cracking, and stress corrosion. These forms of degradation not only reduce the useful life of assets, but can also cause catastrophic failures.
Traditional methodologies vs. recent advances
Historically, corrosion protection has relied on protective coatings, sacrificial anodes, and cathodic protection systems. Although these techniques are effective, they have limitations in durability and efficiency in complex environments. In contrast, recent advances focus on more innovative solutions.
Advanced materials, such as corrosion-resistant alloys and smart coatings that can self-heal, changing color upon detection of corrosion. Additionally, the adoption of real-time monitoring systems, powered by sensors and Internet of Things (IoT) technologies, enables earlier detection and faster response to corrosion problems.
Innovative technologies in corrosion control
Emerging technologies are redefining the fight against corrosion in underground environments. Nanotechnology, for example, is enabling the development of coatings and materials at the molecular level with improved properties.
Smart sensors and AI-based systems are facilitating constant monitoring and predictive analysis, helping to prevent corrosion before it becomes a bigger problem. These technologies not only improve protection, but also optimize maintenance management and decision making, significantly reducing downtime and repair costs.
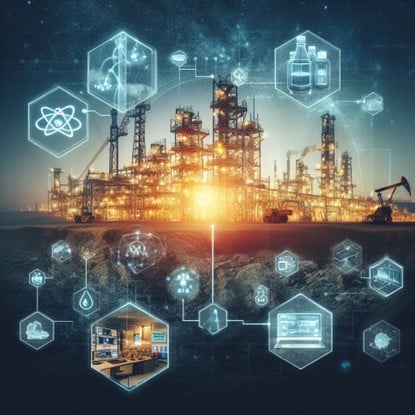
Integration of sustainability and regulatory compliance
In the area of underground pipeline corrosion protection, the integration of sustainable practices is not only an ethical choice, but also an operational and legal necessity. The advancement of protection methodologies has begun to focus strongly on solutions that minimize environmental impact, reducing the emission of harmful substances and promoting the use of safer and more durable materials.
This transition towards more sustainable practices is aligned with growing international regulations that seek to protect both the environment and public health. New corrosion protection technologies offer companies in the oil & gas sector the possibility of meeting these stricter regulatory standards.
Adopting these methodologies is not only a strategic decision for regulatory compliance, but also an important step towards a more sustainable future in the oil and gas industry, while improving its corporate image in an increasingly environmentally conscious market. atmosphere.
Cases of organizations that implement these methodologies
Various leading companies in the oil & gas sector have adopted advanced methodologies to combat corrosion in underground assets, obtaining significant results on several fronts. As notable examples we have:
- Shell: Shell is one of the world’s largest energy companies and has been at the forefront of implementing advanced corrosion protection technologies. For example, they have used advanced protective coatings and real-time corrosion monitoring systems to protect their underground buried pipelines, which has resulted in significant improvement in efficiency and reduced maintenance costs.
- BP (British Petroleum): BP has invested in advanced technologies for monitoring the integrity of its underground assets, including the use of smart sensors and AI-based systems for early detection of corrosion. These technologies have enabled BP to improve the safety and extend the life of its critical infrastructure.
- BP (British Petroleum): BP has invested in advanced technologies to monitor the integrity of its underground assets, including the use of smart sensors and AI-based systems for early detection of corrosion. These technologies have enabled BP to improve the safety and extend the life of its critical infrastructure.
- ExxonMobil: This company has implemented innovative technologies in corrosion protection, including the use of corrosion-resistant alloys and nondestructive inspection techniques to evaluate the integrity of its pipelines and underground structures.
- Chevron: Has used advanced cathodic protection techniques to combat corrosion in its underground infrastructure. These techniques, combined with a rigorous monitoring and maintenance program, have helped Chevron extend the life of its assets and reduce costs associated with corrosion.
Cost indicators associated with not implementing advanced technologies
The economic impact of untreated corrosion in the oil & gas industry is a crucial issue. According to recent studies, corrosion represents a significant economic loss, reaching up to 3-4% of the GDP of some industrialized countries. This figure underlines the importance of effective corrosion control management, particularly in critical underground assets.
When comparing costs, traditional maintenance, which often involves reactive repairs and frequent component replacements, is more expensive in the long run. For example, one study indicated that the use of advanced anti-corrosion technologies could reduce maintenance costs by up to 20-25% over the life of an asset.
Investment in new technologies, such as advanced coatings and real-time monitoring systems, although initially higher, is offset by extending the useful life of equipment, reducing the frequency of failures and decreasing operating costs. These data highlight the need to adopt more proactive and technologically advanced approaches in corrosion control.
Conclusions
This analysis reveals an inescapable reality: corrosion in underground assets is a challenge in the oil & gas industry, with far-reaching economic and safety implications. The transition towards advanced methodologies and innovative technologies is not just an option, but a prevailing necessity.
These new practices, ranging from advanced coatings to real-time monitoring systems, offer unprecedented effectiveness in corrosion prevention and management. Furthermore, its integration with principles of sustainability and regulatory compliance not only responds to current ethical and legal requirements, but also prepares companies to face the challenges of the future.
The examples of leading companies in the sector that have already implemented these methodologies confirm their viability and benefits, marking a clear path forward. The adoption of these advanced technologies not only means a significant reduction in maintenance and operation costs, but also represents a commitment to sustainability and safety, aspects increasingly valued by stakeholders and consumers.
Ultimately, the evolution and adoption of these advanced protection methodologies for corrosion control are necessary to ensure useful life, efficiency and sustainability in the oil & gas industry.
References
Own source