Table of Contents
- Introduction
- Conventional and unconventional drilling wells
- Categories of different types of unconventional oil and gas
- Advanced remote monitoring technologies in unconventional gas reservoirs
- Objectives of remote monitoring for unconventional gas wells
- The importance of advanced technologies used in the exploration and exploitation of unconventional gas
- Conclusions
- References
Introduction
Unconventional gas wells are reservoirs where oil and gas phases are tightly adhered to the rock matrix due to significant capillary forces, requiring specialized approaches for their evaluation, exploration, and exploitation. In the context of natural gas, a well is considered unconventional when it is trapped in low-permeability rock formations or uncommon crystalline structures, making extraction difficult using conventional methods.
The exploitation of this type of gas requires specific drilling and stimulation technologies, which entail additional costs and strong dependence on gas prices in the market.
Conventional and unconventional drilling wells
Oil and gas are naturally generated at depths of around 4 or 5 km beneath the Earth’s surface. Due to their lower density than water saturated in rocks below the water table, these substances tend to migrate to the surface through aquifers by buoyancy effect.
Conventional reservoirs: In these wells, hydrocarbons are formed in source rock composed of organic material and sedimented over long periods. Some oil and gas can naturally escape to the surface, either on land or under the seabed, while the rest becomes trapped underground due to geological barriers, accumulating in porous rocks, displacing water, and forming conventional reservoirs if permeability allows.
Over time, pressure, and temperature transform organic matter into hydrocarbons, which then migrate through geological formations until they encounter an impermeable rock called a seal. If conditions prevent leakage, a geological trap is formed, with oil, gas, and water housed in a reservoir rock with good permeability and porosity for commercial exploitation using conventional techniques (Figure 1, a).
Unconventional wells: In unconventional reservoirs, hydrocarbons are formed similarly to conventional ones. In unconventional ones, the hydrocarbon usually remains in the same rock where it was formed, which acts as both the source and reservoir due to its low permeability. This low permeability prevents primary migration of hydrocarbons through the rock, related to the fluid’s capacity to move in the reservoir (Figure 1, b).
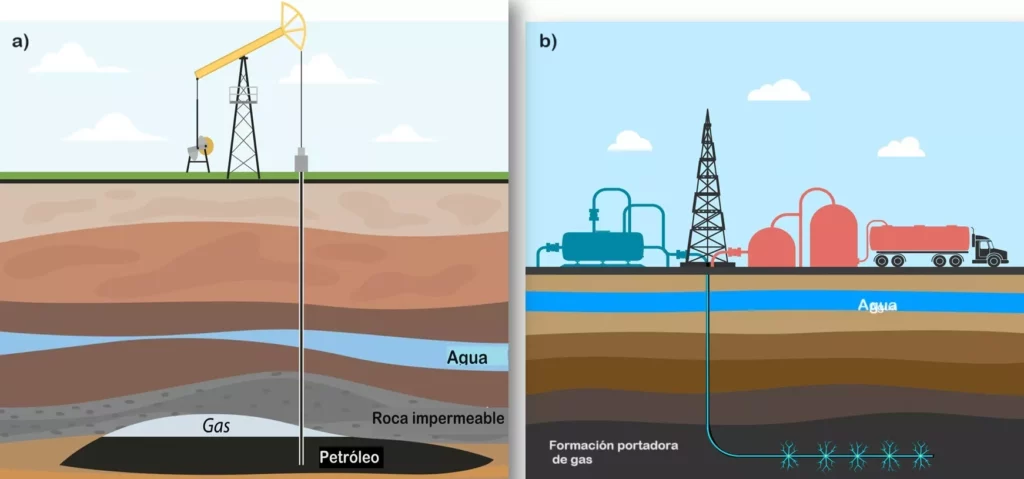
b) Unconventional (Source: Shutter Stock).
In conventional gas fields, extraction is facilitated by natural pressure that drives oil and gas to the surface through drilled wells. However, in unconventional gas fields, advanced stimulation techniques like hydraulic fracturing are required to release trapped oil and gas from the rock matrix.
Gas fields tend to have lower porosity and permeability but higher pressure and compressibility, meaning the gas can expand and contract more with changes in temperature and pressure. These differences impact drilling objectives, risks, and challenges, as well as the selection of optimal well location, trajectory, and depth.
Categories of different types of unconventional oil and gas
According to the International Energy Agency (IEA), unconventional gas encompasses various categories, each with particular characteristics1:
- Tight gas: Refers to natural gas trapped in sedimentary rocks like sandstones and limestones with very low permeability (usually less than 0.1 millidarcys) and low porosity. This type of gas cannot be economically extracted through conventional vertical wells.
- Shale gas: This gas is contained in fine-grained sedimentary rocks, mainly clays or silts, known as shales. These rocks have very low permeability and porosity, making commercial extraction challenging. They are considered hydrocarbon source rocks, generating gas after appropriate thermal maturation.
- Coal-Bed Methane (CBM): This type of gas is adsorbed in coal beds and is inaccessible through conventional mining due to depth or coal reserve quality.
- Gas Hydrates: These natural solid substances, resembling icy snow, consist of a crystalline structure of water molecules trapping gaseous hydrocarbons, primarily methane.
Advanced remote monitoring technologies in unconventional gas reservoirs
Today, various remote monitoring technologies are employed in unconventional gas reservoirs to enhance operational efficiency and ensure facility safety. Exploiting unconventional wells, where hydrocarbons are trapped in low-permeability rock formations at great depths and high temperatures, demands reliable technology.
In this context, field automation technology is rapidly advancing, thanks to the development of more sophisticated sensors for diverse measurements. Additionally, there is a new set of data linked to all “smart” equipment (pumps, valves, motors, etc.) equipped with integrated sensors to gather performance and status information.
Measurement solutions are ideal for acquiring critical real-time data during drilling and exploration. Below are some of the most advanced technologies in use:
- Automated drilling systems: One of the most significant advancements in drilling technology is the development of automated systems. These systems utilize algorithms and real-time data to optimize drilling parameters, such as bit weight, rotation speed, and mud flow rate. Continuous adjustment of these parameters through these systems improves drilling performance by reducing time, minimizing vibrations, and enhancing well quality.
- Deepwater well cementing technologies: These technologies enable monitoring and control from the surface, ensuring proper well operability.
- Downhole Sensors and Measurement While Drilling (MWD) Tools: These tools provide real-time data on parameters such as temperature, pressure, torque, and vibration to enhance efficiency and reduce equipment wear.
- Advanced drill bits and drilling fluids: Innovations in a bit design, such as PDC (Polycrystalline Diamond Compact) and matrix bits, offer greater efficiency and durability, higher penetration rates, and better directional capabilities, speeding up precise drilling. Synthetic-based drilling fluids also enhance well stability and cuttings removal, reducing risks and optimizing overall operation performance.
- Intelligent completion systems: Integration of remote monitoring and control technologies, like surface-controlled safety valves, to optimize production and validate reservoir models. Below are some examples of these technologies.
Examples of advanced technologies in the drilling industry
Fiber optic monitoring system
Remote monitoring technologies utilizing fiber optics2 offer an innovative and continuous solution for obtaining real-time pressure and temperature data in various reservoir applications (Figure 2). This system enables monitoring multiple points at the well bore bottom, whether vertical or horizontal, regardless of casing size.
The fiber optic cables used are suitable for any well bore environment, with additional protection to ensure their integrity. These technologies employ a variety of surface data acquisition systems, both temporary and permanent, to provide real-time data, enabling effective and precise reservoir monitoring. This facilitates informed and strategic decision-making to optimize production and operational efficiency.
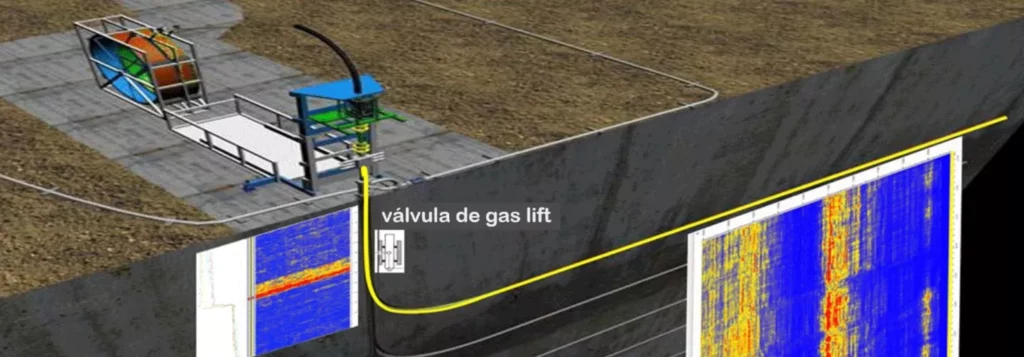
Drilling technologies with intelligent completion systems
Success in unconventional well drilling has been driven by innovations and technologies that enhance the process. Tools like downhole sensors, mandrels, and surface-controlled safety valves have enabled the development of smart wells in the hydrocarbon industry3. These advancements in remote monitoring technologies facilitate real-time control of production zones without the need for physical intervention, representing a significant evolution in operational efficiency and safety.
For more information, we invite you to watch the following video showcasing innovative technologies in unconventional gas well drilling from Weatherford, which recently launched the Rotary Steerable System (RSS).

RSS directional rotary system for directional drilling applications.
Smart completions gather and process a large amount of data from various downhole nodes and surface installations, incorporating sensors and surface-controlled flow control valves. This allows real-time monitoring, evaluation, and active management of production or injection, facilitating continuous optimization of production processes.
Information is transmitted to the surface via a local or remote digital monitor installed on the well platform, demonstrating significant improvements in production. The system has three applications: vertical control, horizontal control, and tangential control. Adopting advanced techniques and remote drilling monitoring technologies requires companies to have trained personnel to prevent accidents and equipment failures.
Digitalization in oil extraction (Artificial Intelligence (AI) and IIoT)
Currently, integrating digitalization into remote monitoring technologies represents comprehensive solutions to address current automation issues in well drilling.
The application of Artificial Intelligence (AI) is radically transforming the oil industry, enabling more efficient, safe, and profitable oil extraction. Thanks to its advanced capabilities in data analysis and predictive maintenance, AI can anticipate equipment failures, optimize drilling operations, and improve strategic decision-making. Machine learning algorithms can accurately analyze seismic data, identifying potential drilling sites more precisely, minimizing financial risk, and reducing the environmental impact associated with oil exploration.
The Internet of Things (IoT) enables remote and real-time monitoring of extraction operations; however, for effective implementation, owners and operators must adopt IIoT-enabled enterprise architectures, allowing data to securely flow from connected field sensors and equipment, bypassing traditional process control networks. This ensures the security and accuracy of critical data while facilitating access for asset management, inventory control, and other enterprise systems. Implementations in onshore oil and gas applications focus on areas such as equipment status, corrosion monitoring, and production chemical management.
Objectives of remote monitoring for unconventional gas wells
Remote monitoring of unconventional gas wells aims to achieve the following primary objectives:
- Production optimization and reservoir model validation:
- Utilization of intelligent completion systems integrating remote control and monitoring technologies to optimize production.
- Real-time monitoring of well conditions to validate and efficiently adjust reservoir models.
- Problem prevention and well integrity preservation:
- Deployment of downhole sensors such as optical cables and inductive coupling devices for real-time monitoring of critical parameters like pressure and temperature.
- Implementation of real-time leak detection and localization systems to prevent issues and ensure well integrity.
- Remote monitoring of rectifiers and cathodic protection stations to prevent corrosion in facilities.
- Operations optimization and cost reduction:
- Remote control of operations such as well cementing to optimize processes and decrease costs.
- Integration of monitoring and control systems into a centralized “digital brain,” such as the one used by YPF in Vaca Muerta, to enhance operational efficiency.
The importance of advanced technologies used in the exploration and exploitation of unconventional gas
The following will discuss the importance of advanced technologies in drilling unconventional gas wells:
In recent years, the oil and gas industry has witnessed a significant shift towards the exploration and exploitation of unconventional gas reservoirs. Unconventional wells gas, which include shale gas formations and gas trapped in tight rock formations, require innovative approaches and advanced technologies for efficient exploration and production.
A key aspect driving success in unconventional gas resource development is the utilization of remote monitoring technologies. These technologies play a crucial role in optimizing drilling operations, enhancing safety, and reducing operational costs associated with unconventional wells development.
Exploration and exploitation of unconventional gas reservoirs present unique challenges compared to conventional reservoirs. These reservoirs often have low permeability and require specialized drilling techniques to extract gas trapped in tight rock formations. Traditional drilling methods often struggle to achieve economic viability in these challenging environments.
However, with the advent of advanced monitoring technologies such as real-time data analytics, automated drilling systems, and remote sensing tools, the industry has experienced a paradigm shift. These technologies enable operators to monitor drilling parameters and well performance remotely, allowing for precise adjustments and operational optimization without constant onsite presence.
Remote monitoring technologies provide continuous surveillance of drilling processes, well integrity, and reservoir behavior. This capability enhances safety by quickly identifying potential issues and mitigating risks associated with complex drilling operations in unconventional wells.
The pursuit of new technologies has driven significant advancements in research. Currently, institutions like Texas A&M University are developing new viscosifiers called “dynamic binary complexes” designed to enhance viscosities in hydraulic fracturing fluids, even under extreme conditions of temperature, pressure, and salinity4. This advancement would increase productivity in the hydrocarbon industry, especially in drilling unconventional wells.
Furthermore, these advanced technologies contribute to better reservoir characterization, enabling more informed decision-making during exploration and production phases. Enhanced data analytics helps identify optimal drilling locations within unconventional reservoirs, leading to higher success rates and lower exploration costs.
The adoption of advanced technologies in drilling unconventional gas wells is crucial for the success of modern oil and gas operations. Remote monitoring technologies offer significant advantages in terms of operational efficiency, safety, and profitability, thereby supporting the sustainable development of unconventional gas resources in the current energy landscape.
Conclusions
Remote monitoring technologies applied to unconventional gas wells are designed to optimize production, prevent issues, maintain well integrity, and reduce costs through more efficient operational management. This approach directly contributes to the success of operations in unconventional reservoirs.
The ongoing development of advanced technologies primarily aims to maximize energy production from unconventional oil and gas resources. Simultaneously, these innovations seek to enhance safety and minimize the environmental impact of operations, especially within the context of petroleum refineries.
References
- Mariano Marzo; “Unconventional Gas: Resources, Production Forecasts, and Geopolitical Impact of Development”; Fusean (Foundation for Energy and Environmental Sustainability), 2014; Universitat de Barcelona.
- Morken Group; “Real-Time Well Instrumentation and Monitoring.”
- World Energy Trade; “Smart Drilling: Increasing Well Productivity by Up to 30%; Research, Development, and Innovation.”
- Bhat, Bhargavi Sripathi (2020). “pH-SWITCHABLE DYNAMIC BINARY COMPLEXES AS VISCOSITY MODIFYING AGENTS.” Master’s thesis, Texas A&M University. Available electronically from https://hdl.handle.net/1969.1/192951.