The reliability of maritime operations is strongly influenced by the different types of maintenance implemented. Various sources highlight how various maintenance approaches contribute to the reliability of maritime operations, as detailed below:
In this context, advanced reliability analysis for marine systems operations and maintenance provides information on failures and component status, contributing to the maintenance and availability of vessels. This approach improves the understanding of how maintenance impacts the reliability of marine systems.
This idea leads to the conceptualization of maintenance, in general terms, maintenance refers to the combination of different actions, whether technical, administrative or supervisory, carried out on an asset with the purpose of restoring it or keeping it in operation so that it can comply its purpose.
This definition highlights that maintenance is a broad field and establishes that a single action does not involve the complete repair of an asset. Therefore, it is subdivided into various categories with the aim of providing greater conceptual and operational clarity.
Establishing maintenance policies and procedures is necessary to ensure safe and efficient maritime operations. By taking a comprehensive approach to maintenance and reliability, vessel owners and operators can maximize profitability and meet customer needs.
Types of strategic maintenance for reliability in maritime operations
The following focuses on the most important types of maintenance carried out in port facilities: Reliability Centered Maintenance (RCM), Advanced Reliability Analysis, maintenance policies and procedures, and port infrastructure maintenance, which contribute significantly to reliability. of maritime operations such as.
Reliability Centered Maintenance (RCM), is necessary in port operations, ensures the efficient management of critical assets such as cranes and loading systems. This personalized approach allows you to identify essential elements for operational continuity and security in complex environments.
By applying the MCC, maintenance strategies are optimized, reducing costs and minimizing downtime. In addition, it contributes to extending the useful life of assets and offers a comprehensive view of system reliability. Port authorities and companies can proactively anticipate and address challenges, strengthening operational resilience.
Reliability analysis, supported by advanced technologies, allows you to anticipate possible failures and schedule precise interventions. Using sensors, data analysis and predictive algorithms, critical components are constantly monitored, identifying early signs of wear or anomalies. This anticipation drastically reduces the risk of unexpected breakdowns, minimizing downtime and optimizing operational availability 1 .
In the field of port management, the development and execution of port infrastructure maintenance policies and procedures are necessary to guarantee the logistics of operations efficiently and safely. These detailed guidelines establish a structured framework for the regular inspection, repair and improvement of docks, cranes, warehouses and other port facilities.
Maintenance policies provide strategic guidelines, outlining responsibilities and deadlines to ensure the structural and operational integrity of the facilities. Simultaneously, detailed procedures offer a step-by-step approach to the effective execution of maintenance tasks, incorporating best practices and safety regulations.
Maintenance work such as dredging, repair of bollards and fenders, maintenance of road networks and care of cranes and loading equipment play a considerable role in improving the competitiveness and reliability of a port.
Dredging consists of the removal of sediments and materials accumulated in the access channels and docks of a port, as seen in figure 1. This process is necessary to maintain adequate depths that allow safe navigation of vessels of different drafts. In addition to ensuring safety, regular dredging improves efficiency by preventing clogging of channels and facilitating the flow of maritime traffic.
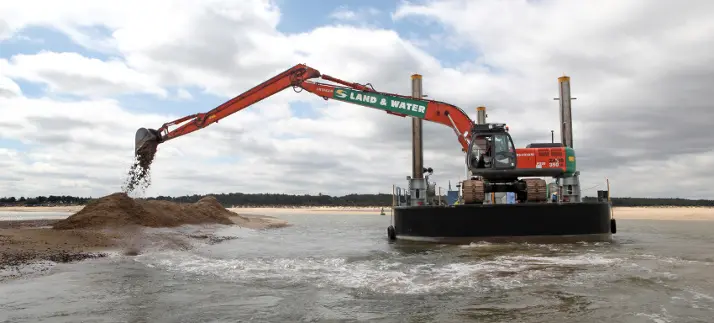
Depending on the bottom material that requires dredging, different types of dredges are used. There are several types of dredges commonly used in this type of operation: mechanical, hydraulic and mixed (mechanical/hydraulic), and each of them has different types of mechanism and operation.
Dredging operations potentially have a significant environmental impact, which must be timely and appropriately evaluated in order to take into consideration possible mitigation measures.
Bollards and fenders are key elements in port facilities, providing safe mooring points and impact protection during vessel docking and undocking maneuvers. Proper repair and maintenance of these elements ensures structural integrity and prevents damage to both vessels and port infrastructure, minimizing risks and ensuring smooth port operations.
Cranes and stevedoring equipment are essential for the efficient handling of cargo in the port. Periodic maintenance of this equipment guarantees its operational availability, reduces downtime and improves productivity in loading and unloading operations. Furthermore, proper maintenance (figure 2), It contributes to workplace safety by preventing failures or accidents during cargo handling maneuvers.
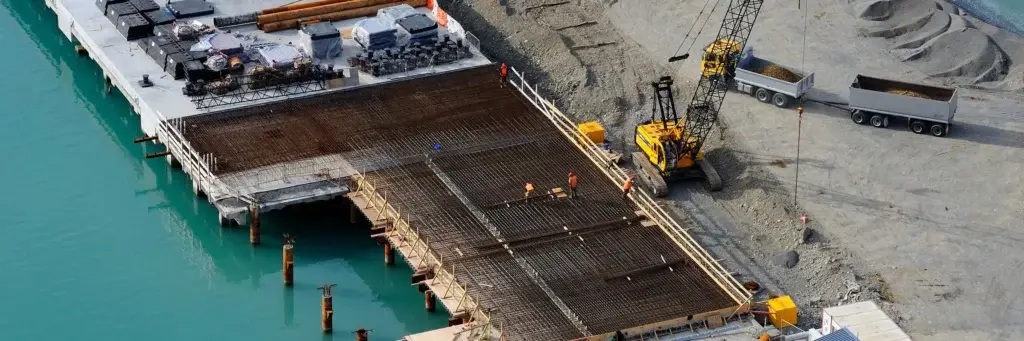
By focusing on these maintenance tasks, a port can significantly improve its operational efficiency, reliability and competitiveness in the maritime industry . These actions are important to ensure smooth vessel operations, efficient cargo handling and maintaining strong relationships with shipping companies and other stakeholders.
Predictive and preventive maintenance: Pillars of trust in maritime operations
Predictive and preventive maintenance emerge as fundamental pillars in the confidence and efficiency of maritime operations. In the dynamic maritime environment, where adverse conditions and constant wear and tear challenge the integrity of vessels, these strategies become the very essence of operational management.
In parallel, preventive maintenance establishes a structured routine of inspections and planned repairs. By following a meticulous schedule based on manufacturer specifications and industry standards, potential challenges are addressed before they become problems. This proactive approach not only extends equipment life and reduces long-term costs, but also contributes to the overall safety of maritime operations.
The strategic combination of these two maintenance methodologies not only strengthens the reliability of the vessels, but also positively impacts the safety of the crew and the protection of the marine environment. Confidence in maritime operations is built on the certainty that each critical component is in its best operational condition, ensuring safe and efficient voyages in marine environments.
How to implement a predictive maintenance plan?
The successful implementation of a predictive maintenance plan requires not only prior technological knowledge, but also deep experience and understanding of this methodology. When activating a predictive maintenance program, it is necessary to support a detailed history of the time and labor required, with the purpose of progressively optimizing it during its execution. The application of advanced technologies in ports such as the Internet of Things, the cloud and artificial intelligence allows continuous operation to be monitored in real time.
For example Evergreen Line. It has started using artificial intelligence in its predictive maintenance system. The system uses sensors and machine learning algorithms to monitor the status of equipment on ships and predict when maintenance tasks need to be performed 2 .
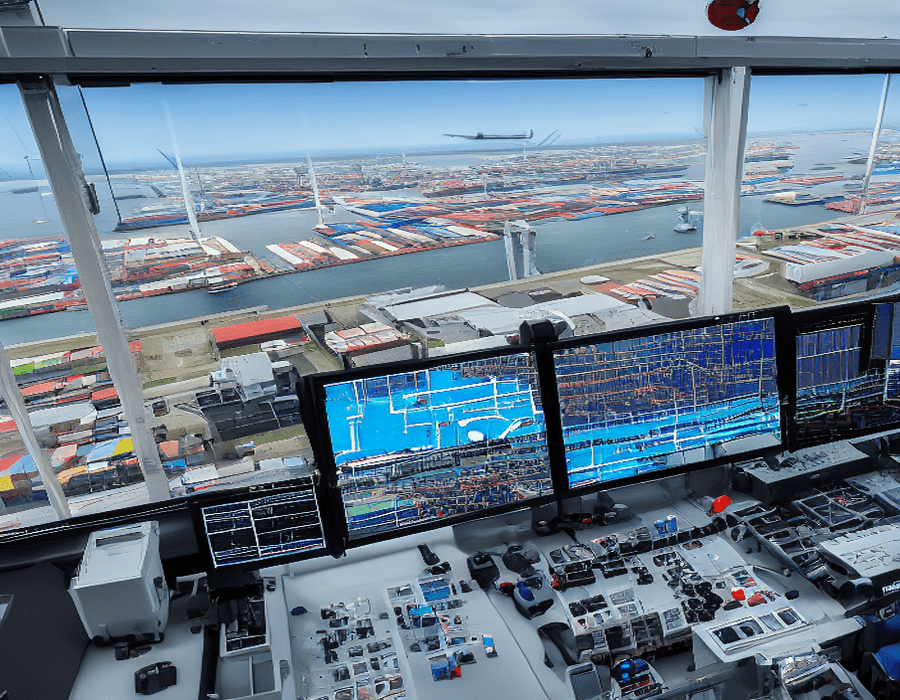
If there is no background in predictive maintenance, it is imperative to develop a reliable study model for future improvements. This methodology involves taking regular readings of selected variables from the equipment and measuring instruments, software or even manufacturers can provide estimates of values indicative of an imminent failure.
This allows operators to make preventive component replacements, thereby maximizing operational efficiency and equipment reliability.
An alternative is to implement a more autonomous data collection system, where the analyzed parameters, such as vibrations, tribology and thermography, are transmitted to a center on land. There, experts specialized in the subject can process the information and send detailed reports, providing an updated view of the status of the monitored equipment. This automated system collects data such as vibrations and ultrasound to detect serious faults that require immediate intervention, providing early warnings of abnormal conditions.
In the event that the onboard team develops its own model, careful consideration must be given to which variables to analyze to determine what instruments and software are required.
In this sense, numerous companies specialized in predictive maintenance are entering the sector, offering cutting-edge computer solutions and advanced devices for data collection.
Finally, once the model identifies the critical moments and points of a part, alarms are incorporated into the system to signal the need for future replacement, thus facilitating proactive and preventive maintenance management.
Predictive maintenance allows greater control over the spare parts necessary for a machine, since it is not based on scheduled changes as in preventive maintenance. This translates into long-term savings on spare parts.
Essential maintenance for confidence in maritime operations
The implementation of predictive techniques in the maintenance cycle of a ship provides the shipowner company with greater availability of its fleet, a more efficient operating environment and a reduction in long-term maintenance costs.
However, there is currently no completely reliable technology that allows the useful life of maritime assets to be determined with certainty. It is clear that carrying out continuous surveillance across all systems would not be feasible for any entity.
The resolution of these limitations involves constant monitoring of the critical components that govern the optimal operation of the vessel, overcoming specific technological challenges:
- Obtain continuous control and monitoring during the operation of the vessel.
- Improve the ability to predict the remaining useful life of equipment.
- Develop intelligent systems with learning capacity so that predictive systems identify failures with greater precision.
Once these challenges are overcome, the key initiative falls to the shipping companies. Without their commitment, predictive maintenance becomes a mere proposition. It is evident that the initial investment is considerable, along with other identified disadvantages, but it is the only way to compete with low-cost labor, encouraging the adoption of such methods.
Conclusions
The port is a multifunctional location that encompasses loading and unloading activities, ship repair and manufacturing of new vessels. In loading and unloading systems and new shipbuilding infrastructure, the time required to inspect tools and equipment according to the system should always be considered, whether for minor repairs or more serious damage. However, it is also crucial to take into account ergonomic aspects in the maintenance of port infrastructure.
This involves guaranteeing safety, comfort and efficiency in the maintenance process, since ergonomics is expected to play an important role in reducing incidents in the maintenance of port infrastructure.
References
- Prosertek “Innovation in port risk management”; https://prosertek.com/blog/innovation-in-port-risk-management/
- PierNext; Will AI take control of port management?; https://piernext.portdebarcelona.cat/tecnologia/tomara-la-ia-el-control-de-la-gestion-portuaria/