Table of Contents
- Introduction
- What is asphalt?
- How is asphalt produced?
- What is asphalt made of? Chemical composition of the binder
- Why are there different types of asphalt?
- Asphalt types: Technical classification according to composition and application technology
- Asphalt technical properties
- Environmentally friendly asphalts
- How do polymeric additives influence the mechanical properties of asphalt?
- Conclusions
- References
Introduction
Asphalt is a bituminous material with viscoelastic and thermoplastic behavior, composed of high molecular weight hydrocarbons derived from heavy petroleum residue. Its main application lies in the construction of road infrastructures due to its ability to withstand dynamic loads, thermal deformations and environmental exposure. In addition to its mechanical and waterproofing properties, asphalt adapts to different environments through specific formulations that integrate mineral aggregates, binders and modifying additives.
What is asphalt? How is asphalt produced? These questions are necessary to understand the properties of asphalt and its behavior under thermal and mechanical stresses. The engineering of asphalt mixtures makes it possible to adjust their structural, thermal and rheological performance to the technical requirements of each project. This article discusses points of interest such as technical classification, chemical composition, rheological properties and the different types of asphalt.
What is asphalt?
Asphalt is technically defined as a complex bituminous material, predominantly composed of high molecular weight hydrocarbons (asphaltenes and maltenes), originating as a residue from the fractional distillation of crude oil (ASTM D8). At room temperature, it exhibits solid or semi-solid behavior, acting as a binder matrix in the formation of asphalt mixtures that bind mineral aggregates.
Complying with standards such as AASHTO M320, asphalt confers internal cohesion, impermeability and resistance to pavements exposed to stresses induced by traffic, thermal cycles and environmental aggressiveness. Its thermoplastic nature and hydrophobicity, together with its ability to dissipate energy under dynamic loads, position it as a fundamental material in the construction of durable, high-performance road surfaces.
How is asphalt produced?
Asphalt production is articulated through refining processes:
- Atmospheric distillation: The crude oil is fractionated at ≈400 °C, separating volatile components and generating an atmospheric residue rich in heavy hydrocarbons.
- Vacuum distillation: The residue is distilled at reduced pressure to obtain the base asphalt (bitumen or bitumen), avoiding thermal degradation.
From the base asphalt, specialized products are derived through modification processes:
- Oxidized asphalt: Treated by hot air injection to increase thermal stability, mainly applied in waterproofing.
- Polymer-modified asphalt: Incorporation of polymers to improve viscoelasticity and resistance to plastic deformation, strategic in high-stress pavements.
- Asphalt emulsions: Asphalt dispersions in water stabilized with surfactants, allowing for cold applications, such as bonding and recycling irrigation.
- Liquid asphalts (cutbacks): Asphalts diluted in volatile solvents to reduce viscosity and facilitate application at low temperatures (use limited by environmental regulations).
The following video “History of Simple Things” illustrates what asphalt is, its production process, from obtaining aggregates and bitumen to mixing (with possible polymeric additives), transportation and placement in road construction. It also addresses sustainability aspects such as recycling and future innovations in the sector.

What is asphalt made of? Chemical composition of the binder
At the molecular level, base asphalt is a complex colloidal system of high molecular weight hydrocarbons, organized in two main phases that determine its macroscopic properties:
- Asphaltenes (5-25%): High molecular weight polar fraction, insoluble in aliphatic solvents, responsible for the rigidity, viscosity and colloidal stability of asphalt. Its condensed polyaromatic structure confers deformation resistance characteristics.
- Maltenes (75-95%): Continuous apolar phase that disperses the asphaltenes, subdivided into:
- Resins: Polar molecules that contribute to the adhesiveness (binder-aggregate interaction), internal cohesion and stability of the colloidal system.
- Aromatic Oils: Lower polarity components that act as internal solvents for asphaltenes, essential for binder compatibility and flexibility.
- Saturated Oils: Aliphatic hydrocarbons that influence the fluidity, workability at mixing temperatures and thermal behavior of the asphalt.
The interrelationship and proportion of these fractions define the rheological (viscoelasticity), thermal (temperature susceptibility) and mechanical (resistance to deformation and fracture) properties of the binder, as well as its ability to be modified or emulsified for specific applications.
Why are there different types of asphalt?
The diversity of asphalt types is a direct consequence of the need to optimize material performance based on the specific demands of each engineering application. Critical factors driving this diversification include:
- Climatic conditions: The viscoelastic response of asphalt must adapt to extreme operating temperature ranges. In cold climates, flexibility is prioritized to mitigate thermal cracking, while in hot climates, high flow resistance is required to prevent plastic deformation.
- Traffic loads: The volume and magnitude of vehicular loads impose different requirements in terms of resistance to permanent deformation (rutting) and fatigue damage (repetitive cracking).
- Operational constraints: Mixing and placement temperature, transportation and storage logistics, and energy efficiency considerations influence asphalt type selection.
- Sustainability objectives: The growing importance of reducing environmental impact is driving the development of asphalts with a lower carbon footprint through recycling, reduced production temperatures and the use of alternative materials.
For this reason, the industry has developed variants that can be grouped into conventional asphalts, modified asphalts, asphalts by mixing technology or in the form of emulsions and dilutions. As well as ecological asphalts. A detailed classification of these types is presented below.
Asphalt types: Technical classification according to composition and application technology
The technical classification of asphalt is based on its origin, the level of processing to which it is subjected and the method of application on site. This segmentation allows a precise selection of the material according to the requirements of the project.
Base asphalts
- Asphalt cements (conventional asphalts): Obtained directly from petroleum distillation, they are the basis for most asphalt mixtures. Their classification is based on standardized physical properties:
- Penetration Degree: (ASTM D5) Measure of consistency at 25 °C (0.1 mm). Higher values indicate lower viscosity.
- Viscosity: (ASTM D88, D2171, D2170) Flow resistance at specific temperatures (e.g., 60 °C for dynamic viscosity, 135 °C for kinematic viscosity). Designations such as AC-5, AC-10, AC-30 reflect viscosity ranges.
- Performance Grade (PG): (AASHTO M320) Superpave system that specifies asphalt performance as a function of expected maximum and minimum service temperatures (e.g., PG 64-22, PG 70-28).
- Oxidized (or blown) asphalts: (ASTM D312) Produced by hot air insufflation, resulting in a higher softening point and lower penetration. Their lower ductility orients them to waterproofing and sealing applications.
- Natural asphalt: High viscosity mineralized bitumen extracted from geological deposits. Its use, although limited, provides high resistance to aging and thermal stiffness in specialized mixes.
Modified asphalts
- Polymer modified asphalt (PMA): (ASTM D5976) The addition of synthetic polymers (elastomers or plastomers) significantly alters the rheological properties of the base asphalt, improving its elastic response, resistance to plastic deformation and cracking.
- Elastomer modified (EMA): (e.g., SBS) Increases elastic recovery, rutting resistance and low temperature flexibility, crucial in high load pavements and braking zones.
- Plastomer modified (EMP): (e.g., EVA, PE) Improve high temperature stiffness, dimensional stability and fatigue crack resistance.
Asphalt mix application technologies
- Hot-mix asphalt (HMA): (AASHTO M323) In hot-mix asphalt, aggregates and binder are mixed at high temperatures (140-190 °C) to ensure adequate workability and compaction. It offers high durability and structural stability, being the predominant technology for wearing courses and bases. Varieties such as SMA (Stone Mastic Asphalt) and discontinuous mixes are designed for specific rutting and noise resistance requirements. The high mixing and placing temperature ensures optimum interparticle and interlayer adhesion.
- Warm mix (WMA): (FHWA Technical Brief) Produced at lower temperatures (110-140 °C) by additives or foaming of the asphalt, reducing energy consumption and emissions. Optimization of viscosity and wetting of aggregates at reduced temperatures are key to its performance.
- Cold mix (CMA): (ASTM D4867) Uses asphalt emulsions or diluted asphalts mixed with aggregates at room temperature. Suitable for non-structural repairs and low volume roads, its curing depends on the evaporation of water or solvents. Its initial mechanical resistance is lower than hot mixed asphalt.
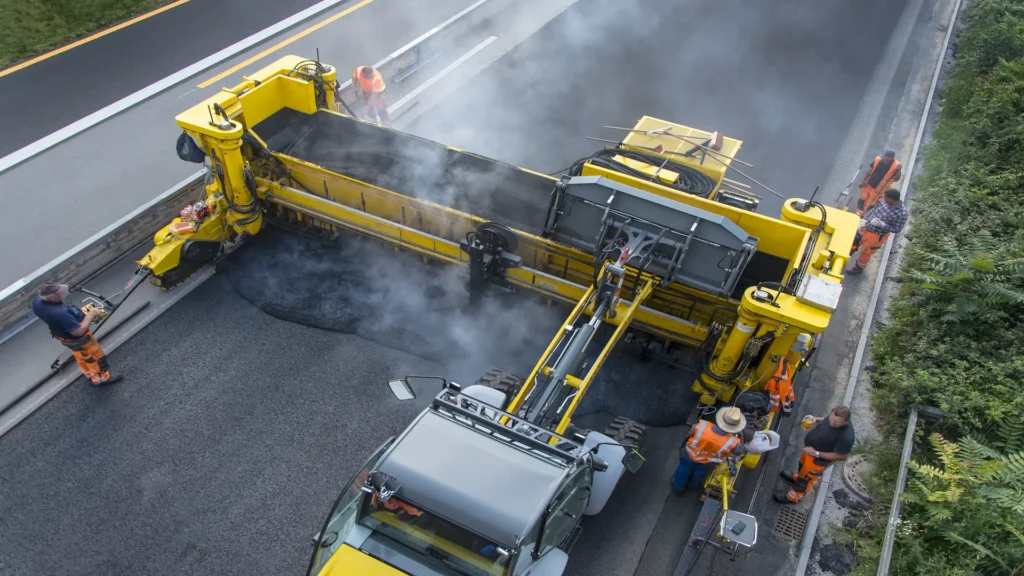
Sparse systems and solutions
- Asphalt emulsions: (ASTM D977, D2397) Colloidal dispersions of asphalt in water stabilized by surfactants. Their classification by ionic charge (cationic/anionic) and breaking speed (fast/medium/slow) determines their applicability in surface treatments, cold recycling and as a binder in thin layers. The selection of the type of emulsion depends on the reactivity with the aggregates and the required workability time.
- Cutbacks: (ASTM D2028, D2027, D2026) Asphalts fluidized by volatile solvents (naphtha, kerosene). Classified by curing speed (fast/medium/slow), they are mainly used in primers and tack coatings, although their use is restricted by VOC emissions.
The selection of asphalt type and application technology should be based on a thorough technical analysis of service conditions, required pavement properties, and the environmental and economic considerations of the project.
Asphalt technical properties
The properties of asphalt are determinant in predicting its behavior in asphalt mixtures and long-term performance:
- Penetration: Indicates relative consistency by the depth that a standard needle reaches at 25 °C under standard conditions. Asphalts with higher penetration are softer, suitable for cold climates, while lower values correspond to harder asphalts.
- Viscosity: (ASTM D88, D2171, D2170) It is the resistance to flow at specific temperatures, influencing workability and rutting resistance.
- Softening point (Ring and Ball): (ASTM D36) Temperature at which asphalt flows under load, indicator of resistance to plastic deformation at high temperatures.
- Ductility: (ASTM D113) Deformation capacity without fracture at 25 °C, relevant to resistance to fatigue cracking and thermal shrinkage.
- Elastic recovery: (ASTM D5976) Percentage of deformation recovered after elimination of load, fundamental in modified asphalts for resistance to permanent deformation.
- Thermal susceptibility: Viscosity variation with temperature, ideally low for stable behavior in different climates.
- Adhesiveness: Interfacial interaction between asphalt and aggregates, critical for resistance to moisture damage and durability of the mix.
- Resistance to aging: (ASTM D2872, D6521) Evaluation of asphalt degradation by oxidation and volatilization in the long term, using tests such as RTFOT (Rolling Thin Film Oven Test) and PAV (Pressure Aging Vessel).
Environmentally friendly asphalts
Mitigation of GHG emissions in the asphalt industry drives the development of solutions with a lower carbon footprint:
- Warm-mix asphalt (WMA): Requires less thermal energy, thereby reducing energy consumption and emissions during production and placement.
- Cold asphalt (CMA): Eliminates the need for heating, minimizing energy impact.
- Recycled asphalt (RAP): Reuse of existing pavements, conserving natural resources and reducing waste.
- Asphalts with ecological additives: Recycled materials (plastics, rubber) or bio-based materials are incorporated to improve performance and reduce environmental impact.
- Self-repairing asphalt: Technologies that extend the useful life of the pavement, reducing the frequency of maintenance and the demand for new materials.
- Asphalt with graphene: Nanometric additive that improves mechanical properties and durability, allowing the reduction of the conventional binder.
- Porous asphalt: It is a specialized asphalt mix for permeable pavements. Its open granulometry, with a predominance of uniform coarse aggregates and less binder, creates a high volume of interconnected voids (15-25%) that allow water infiltration.
How do polymeric additives influence the mechanical properties of asphalt?
The incorporation of polymers in the asphalt matrix generates significant modifications in its mechanical behavior:
- Increased elasticity: Elastomers form a three-dimensional network within the asphalt, allowing greater elastic recovery after deformation, which improves resistance to fatigue cracking.
- Improved rutting resistance: Polymers increase asphalt stiffness at high service temperatures, reducing susceptibility to plastic deformation under repeated loading.
- Thermal crack resistance optimization: Flexibility at low temperatures is maintained or even increased, preventing the formation of thermal shrinkage-induced cracks.
- Prolonged service life: Comprehensive improvement of mechanical properties leads to increased pavement durability and reduced long-term maintenance costs.
Conclusions
The technical classification of asphalt types, its modification with polymers and the use of mixtures with low environmental impact allow the selection of suitable formulations for each service condition. This choice should be based on quantifiable variables such as viscosity, softening point, penetration and elastic recovery, all of which are directly linked to asphalt properties.
The use of hot-mix asphalt continues to be indispensable in road infrastructure projects that demand efficient compaction and high structural performance. Binder characterization and strict in-plant quality control are key aspects to ensure that the asphalt mix responds adequately to service conditions and meets the functional requirements of the pavement.
References
Own source