Table of Contents
- What are industrial gases?
- What is a thermal oxidizer and how does it work?
- Regulatory framework and applicable regulations
- Types of thermal oxidizers and their differences
- Factors in choosing the type of thermal oxidizer
- Design and integration in industrial processes
- Advantages of advanced emission treatment
- Practical applications in industrial sectors
- Technical challenges and new solutions in thermal oxidation
- Efficient maintenance and operation
- Success story: RTO implementation in biogas plant
- Visual supplement: How an RTO works
- Conclusions
- References
Thermal oxidizer or thermal incinerator is a key technology in modern industry to address emission treatments. In a context where regulations for environmental risks are increasingly strict and industrial sustainability is positioned as a strategic value, the use of advanced solutions for the control of gaseous pollutants has reached an important interest.
Among these technologies, thermal oxidizers have established themselves as an effective tool for removing volatile organic compounds (VOCs) and treating various gaseous streams. This article discusses the types of thermal oxidizers, their thermal efficiency, selection criteria and their impact on key industrial sectors.
What are industrial gases?
Industrial gases are mixtures of gaseous compounds generated during manufacturing, chemical or energy activities. They may contain volatile organic compounds (VOCs), hydrocarbons, solvents, particulates or acid gases, depending on the type of process involved.
Their composition and volume vary widely depending on the industry, which conditions the treatment strategies and requires the implementation of adapted solutions. This is where the use of a thermal oxidizer is significant in the advanced treatment of these gases before their release into the environment.
What is a thermal oxidizer and how does it work?
Thermal oxidizers are pollution control units designed to prevent volatile compounds generated in industrial processes from reaching the environment. Their main function is to decompose hazardous gases through high temperatures, transforming them into carbon dioxide (CO₂) and water vapor (H₂O), which are less harmful to the environment.
This process is known as thermal oxidation and can achieve contaminant destruction levels in excess of 98%.
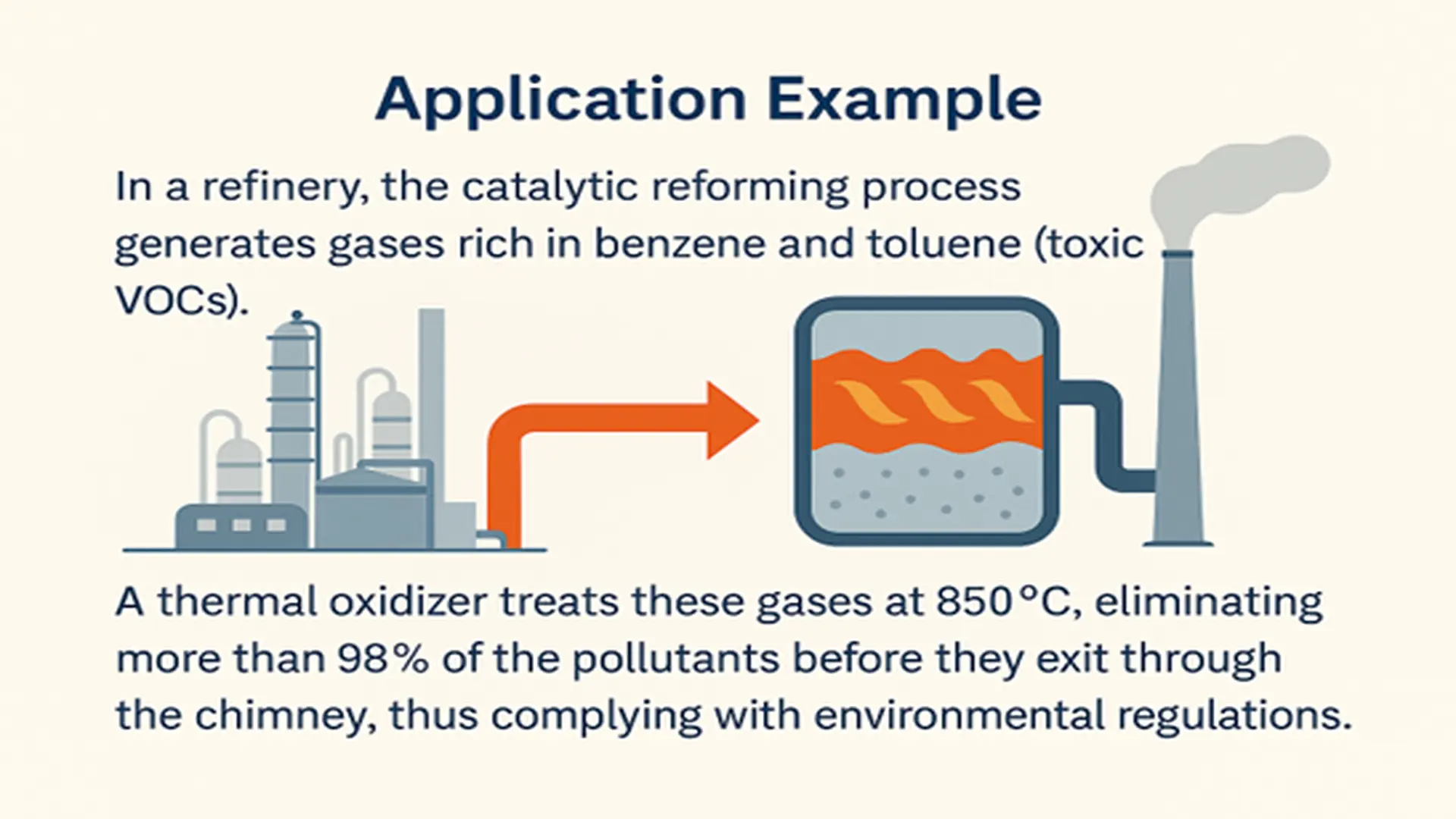
How does it work?
The operation of the thermal oxidizer is based on three key design factors that ensure effective oxidation:
- Temperature: The system must reach at least 800 °C to 1000 °C, depending on the type of contaminants to be destroyed.
- Residence time: It is the time that the contaminated gas remains inside the combustion chamber, the longer the residence time, the higher the destruction efficiency.
- Turbulence: Ensures adequate mixing between the pollutant gases and oxygen, facilitating complete oxidation.
These three elements: temperature, time and turbulence, are the basis of advanced emission treatment technologies, especially when dealing with gases that are difficult to remove by mechanical or chemical methods.
Regulatory framework and applicable regulations
The implementation of a thermal emission control solution in industry is driven by environmental regulations that require the control and reduction of pollutant emissions. In the United States, the Environmental Protection Agency (EPA) sets strict limits for emissions of volatile organic compounds (VOCs) and other pollutants through regulations such as the Clean Air Act (epa.gov): Clean Air Act (epa.gov). In Europe, the Industrial Emissions Directive (IED) imposes similar requirements, obliging industries to adopt efficient industrial exhaust gas treatment technologies.
Thermal oxidizers, especially regenerative oxidizers (RTOs), are recognized for their high thermal efficiency and ability to destroy up to 99% of VOCs, meeting regulatory standards and contributing to the environmental sustainability of industrial operations.
Types of thermal oxidizers and their differences
The different types of thermal oxidizers allow to adapt to multiple process configurations, flow rates and pollutant loadings. This flexibility is crucial to accurately address diverse industrial emission profiles. Below is a useful comparison table:
Type of oxidizer | Operating temp. | Thermal efficiency | Energy consumption | Recommended application |
Direct (TO) | High (800-1000°C) | Medium | High | Flows with high VOC load |
Recuperative | Medium (600-800°C) | Good | Medium | Medium flow processes |
Regenerative (RTO) | 700–850°C | Very high (95%) | Low | Large volumes, variable composition |
Catalytic | Low (300-500°C) | High | Very low | Gases with solvents and lower temperature |
Factors in choosing the type of thermal oxidizer
Correctly selecting among the different types of thermal oxidizers depends on specific technical factors related to the treated gases:
- Chemical composition: The presence of VOCs, particulates, silicones or halogens influences the choice.
- Flow volume: Large flows are best treated with systems such as the regenerative thermal oxidizer.
- Efficiency goals: Applications where high thermal performance is required, prioritize designs with energy recovery or regeneration.
- Environmental compliance: Specific regulations require minimum pollutant destruction levels and low residual emission levels.
Design and integration in industrial processes
The selection and design of a thermal oxidation unit must consider the specific characteristics of the industrial process, including the type and volume of gases generated, the concentration of contaminants and the operating conditions.
Regenerative thermal oxidizers (RTOs) are ideal for processes with large air flows and low VOC concentrations, due to their ability to recover heat and reduce energy consumption. On the other hand, catalytic thermal oxidizers are suitable for flows with higher VOC concentrations and lower operating temperatures.
The integration of these systems into the production line must ensure continuous and efficient operation, minimizing interruptions and optimizing energy recovery. In addition, it is necessary to consider available space, ease of maintenance and compatibility with other existing emission control systems.
Advantages of advanced emission treatment
Implementing an advanced treatment with a thermal oxidizer brings significant benefits:
- Rigorous control of gaseous effluents prior to release.
- Reduced risk of environmental sanctions
- Improved ESG profile of the organization.
- Energy optimization, reducing consumption and operating costs.
Practical applications in industrial sectors
- Petrochemical industry: Generates large volumes of gases with variable organic loads. The regenerative thermal oxidizer is the most widely used due to its high durability and efficiency.
- Pharmaceutical industry: Emits gases with solvents and active compounds. Solutions such as catalytic thermal oxidizers, which operate at lower temperatures, are favored.
- Coatings and paint plants: High VOC emitters, these facilities require continuous advanced treatment. RTO allows effective control at low energy cost.
Technical challenges and new solutions in thermal oxidation
The need to treat complex industrial emissions has driven the development of hybrid technologies and smart systems:
- Temperature and flow control automation (see figure 1).
- Modular and compact design for reduced spaces.
- Increased durability of ceramic materials in RTOs.
- Integration with waste heat recovery technologies.
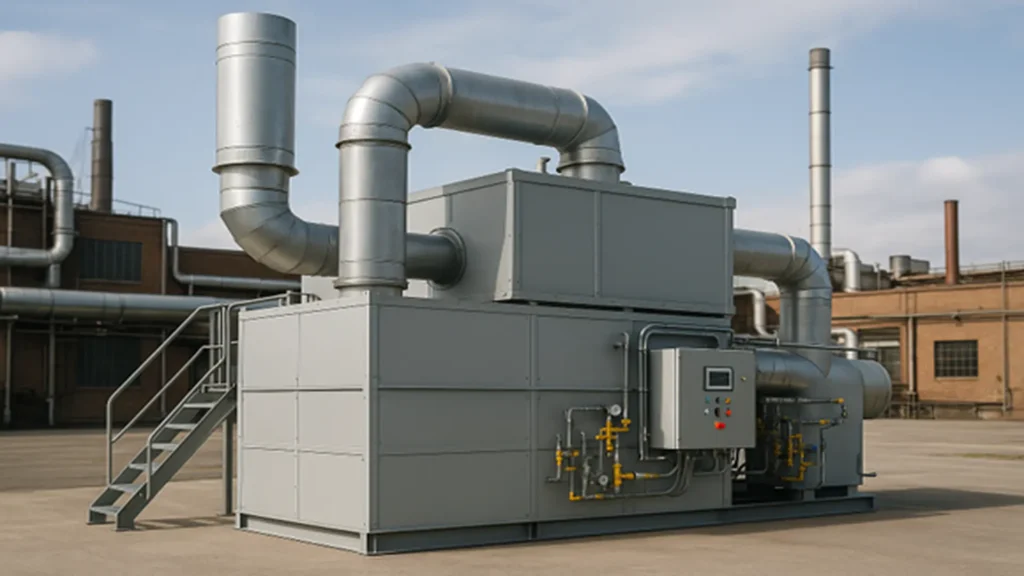
Efficient maintenance and operation
To ensure optimal performance and longevity of thermal oxidizers, it is essential to implement preventive maintenance and continuous monitoring programs. This includes regular inspection of equipment such as heat exchangers, combustion chambers and control systems.
Debris accumulation and material wear can affect thermal performance and contaminant destruction capability. Therefore, it is advisable to establish cleaning and parts replacement routines according to the manufacturer’s specifications and operating conditions.
In addition, the training of personnel in the operation and maintenance of these systems is important to detect and solve problems in a timely manner, ensuring compliance with environmental regulations and the continuity of the production process.
Success story: RTO implementation in biogas plant
An outstanding example of the successful application of an RTO can be found at a biogas plant dedicated to the conversion of biogas to renewable natural gas (RNG). Ship & Shore Environmental designed and installed a custom RTO with a capacity of 15,000 SCFM to treat waste gases from the biogas upgrading process.
The application of this oxidation technology was able to increase the efficiency of pollutant destruction up to 98%, complying with environmental regulations and improving air quality in the area. The implementation of the RTO enabled regulatory compliance and contributed to the plant’s energy sustainability by recovering and reusing the heat generated during the oxidation process.
This case demonstrates how the adoption of advanced industrial emissions treatment technologies can be an effective and cost-efficient solution for industries seeking to reduce their environmental impact and improve their operational efficiency.
Visual supplement: How an RTO works
Additionally, below is an audiovisual material courtesy of Kono Kogs, Inc. that explains in technical detail how regenerative thermal oxidizers (RTOs) work to effectively destroy VOCs and hazardous air pollutants (HAPs) present in industrial process exhaust. Source: Kono Kogs, Inc

How regenerative thermal oxidizers (RTOs) work.
This resource complements the practical understanding of the principles and benefits described in this article.
Conclusions
Far from being an unavoidable by-product, industrial gases represent an environmental challenge that can be efficiently managed through the use of thermal oxidizers. Integrated into waste and emissions treatment schemes, these systems enable compliance with increasingly stringent environmental regulations, improve corporate ESG profile and optimize the energy efficiency of industrial operations.
Choosing the type of system, whether regenerative thermal oxidizer (RTO), catalytic, recuperative or direct, must be based on a thorough technical analysis that considers the composition of the pollutants, the volume of gaseous flow and the specific thermal efficiency objectives of each plant or process. In addition, the implementation of advanced remote and satellite monitoring programs reinforces the effective management of these technologies, ensuring continuous control, traceability of emissions and sustained compliance with regulatory and environmental standards.
Act now and optimize your industrial processes with clean technology!
References
- Catalytic Products International. (n. d.). Thermal oxidizer. Retrieved from https://www.cpilink.com/thermal-oxidizer
- Wikipedia contributors. (n. d.). Thermal oxidizer. Wikipedia. Retrieved from https://en.wikipedia.org/wiki/Thermal_oxidizer
- United States Environmental Protection Agency. (n.d.). Monitoring and control technique: Thermal oxidizer. Retrieved from https://www.epa.gov/air-emissions-monitoring-knowledge-base/monitoring-control-technique-thermal-oxidizer