In the fast-paced world of the energy sector, job security is a critical factor that cannot be overlooked. Risk assessment, accident prevention and worker protection are key priorities in the energy industry, where risk is latent at every step and every activity. For this reason, preventive maintenance and regular inspections stand as essential pillars to guarantee safety in the work environment.
In the industrial area, it is crucial to have qualified personnel in equipment maintenance and inspection, with experience and technical knowledge, which allows them to identify and address possible failures or alterations in the equipment and machinery used in industrial processes. Likewise, it is essential to raise awareness among the personnel and highlight the need for strict compliance with the established safety regulations and procedures to minimize and control the risks present in the workplace.
Why perform preventive maintenance and regular inspections?
In the energy sector, regular maintenance and inspections are essential to ensure safety and avoid accidents that could have serious consequences for both workers and facilities.
Work accidents generate significant costs in terms of compensation and loss of production. Absence due to injuries or downtime due to incidents negatively impacts the operational efficiency of companies. For these reasons, maintenance and inspections are key tools for risk control and avoiding expenses associated with accidents.
Equipment and machinery play a crucial role in daily tasks. Adequate preventive maintenance guarantees that these work safely and reliably, avoiding failures or breakdowns that lead to accidents. Regular inspections allow the equipment to be in optimal conditions, reducing the risks associated with its use, therefore, workers are protected.
The adequate investment for preventive maintenance , monitoring and rigorous inspections of the assets in the main productive sector at a global level, not only contributes to the prevention of accidents, but also prolongs their useful life, guaranteeing a safe, productive work environment. and efficient.
The consequences of accidents can lead to losses in the form of damage to people’s health and material losses. The importance of carrying out an investigation of work accidents, with the aim of determining their causes and being able to adopt corrective measures, cannot be forgotten in any case.
Maintenance and inspections: preventive awareness for industrial safety
These actions are aimed at early detection of failures and risks, for a safe and optimal operation of machinery, equipment and facilities in general. In addition, they are linked to compliance with regulations and safety standards established to guarantee a safe work environment.
Inspections are a necessary part of preventative maintenance, and they help businesses in two ways. First, inspect the facilities and equipment, ensure that they are reliable when used. Regular assessments help prevent injuries on the job site and provide companies with greater protection from potential liability. Second, running regular inspections protects the machinery. In short, the inspections ensure that the equipment works as the manufacturer has intended.
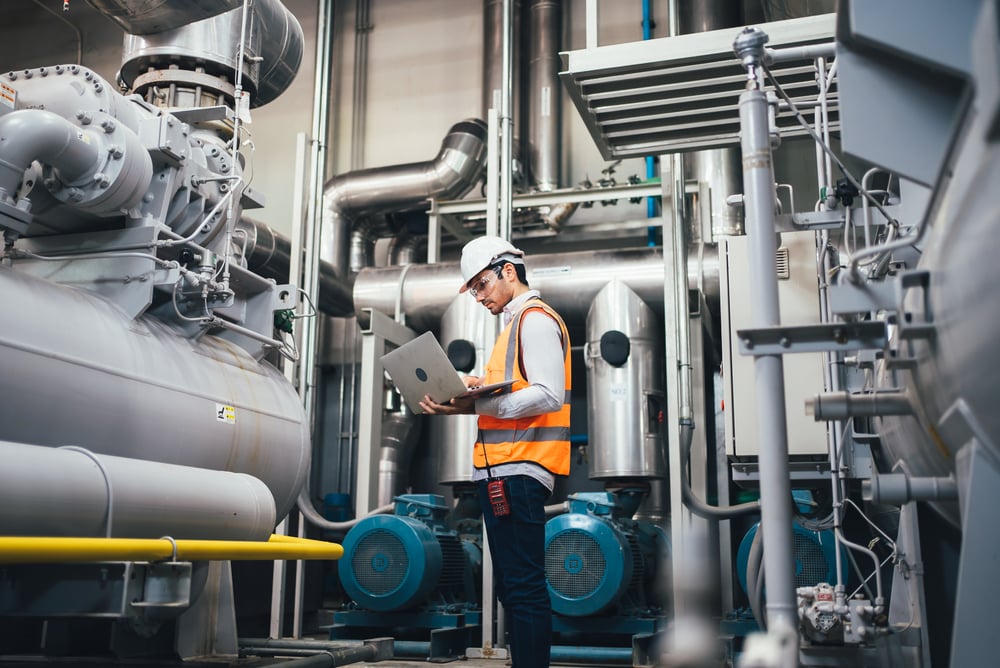
Inspecting equipment is a job of great importance and is based on visual inspections, application of methodologies and use of non-destructive testing, where today a variety of state-of-the-art equipment is available that guarantees inspections, certified personnel are also required. with the objective of evaluating and collecting important data to be analyzed and to know the condition of the assets.
In this technological era, continuous inspections allow early detection of breakdowns, possible failures, wear or deterioration in the equipment and machinery used in the energy sector, the devices used for evaluation and monitoring in systems, mainly those of high risk, have been become characteristic in large industries, providing ample opportunities for security control in work areas.
Develop optimal inspection plans, with the purpose of defining the activities necessary to detect the deterioration in service of components or assets that can cause failures and identify maintenance activities or other risk mitigation actions that can be applied before it becomes a problem. unsafe situation preventing the equipment from reaching a critical state and an exponential failure from occurring, putting safety in general at risk.
The correct application of the inspection programs in progress, optimize the determination, the minimum inspection points required, mainly in the critical components or equipment, based on the deterioration mechanisms, risk levels and corrosion speeds, which may cause some unforeseen failure and compromise the safety of personnel at the facilities.
Regarding maintenance management, preventive maintenance is essential to increase the useful life of assets, reduce corrective maintenance costs and maintain a safe working environment. This is why the companies that carry out their maintenance up to date, have the obligation to carry out increasingly exhaustive verification tasks of their facilities, infrastructures and machinery.
Preventive maintenance helps department managers to detect problems at an early stage, when it is still relatively easy, safe and economical to fix them. In this technological age, there is a need to move from corrective maintenance to a model of anticipating failures.
In practice, many machines can be dangerous when operating normally, but even more so when they malfunction. Therefore, it is essential to adequately train the personnel involved on the operation of each asset, what to do and what not to do in terms of safety and protocols for emergency situations.
Nowadays, maintenance occupies a fundamental place in any industrial activity and is an important challenge for the productivity, competitiveness and safety of companies. Maintain in good condition, machinery and tools, work equipment, which allows a better performance and safety, partly avoiding risks in the work area.
Previously, corrective maintenance was carried out, which was adjusted to repair operations or problem solving on an occasional basis or when the failure has already occurred. But currently, maintenance is a fairly broad field of action whose result considerably influences the appearance, productivity and safety of industrial plants.
Have you ever come across a plant that runs without a maintenance department? Although many managements find it difficult to invest in this department, they will never leave the maintenance team aside. That’s because, it’s an essential service for the smooth running of operations.
Carrying out appropriate maintenance and at the precise times guarantees that the equipment is in good operational condition, minimizing the chances of accidents arising from failures or malfunctions, maintaining a safe work environment by preventing dangerous situations, such as leaks of flammable substances or exposure to toxic substances.
The execution of continuous inspections and preventive maintenance is a requirement in many regulations and standards in the energy sector. Complying with safety regulations is essential to avoid legal penalties, damage to reputation and, most importantly, protect the life and health of workers. Additionally, following these regulations demonstrates a strong commitment to safety and corporate responsibility.
Final Considerations
In the energy sector, maintenance and regular inspections are essential in accident prevention and ensure a safe working environment. Compliance with security rules and procedures, as well as awareness of the importance of these practices, are essential. Investment in proper maintenance and the adoption of good practices are crucial to improve safety, prolong the useful life of the equipment and offer greater security to the people who use the facilities and machines.