Introduction
It is the responsibility of the equipment inspector and his employer to guarantee the results of an inspection carried out, since these may or may not affect the production process of any company. Human reliability plays a leading role in any manufacturing and repair activity that is carried out.
This article describes in a very general way, the important interrelation that exists between the equipment inspector and its reliability, before the client’s asset. Therefore, the issue of human reliability is presented as an engineering tool and its controls to make the equipment inspector a person aware of their results; although it is only through his professional self-development that he will make his mark as an equipment inspector in the future.
The main factor that drives an organization is its human talent and the conviction to carry out its tasks efficiently. In this sense, its workforce requires the study of human reliability to evaluate and analyze the influence of the human factor, in the fulfillment of the assigned goals within organizations and corporations worldwide. As shown in Figure 1, it is a duty of every equipment inspection organization to plan, prepare the Training Plan and execute it. All this according to the responsibilities of the position held by the professional, also taking into account their vision within the organization.
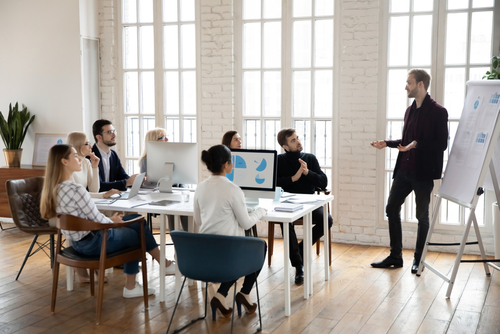
Definitions
To understand this article it is necessary to know some definitions of what is described below:
Reliability: It is defined as “The ability of a system (human beings, facilities, equipment and processes) to perform the function within its design limits, in a specific environment, during a determined interval of time”.
Equipment inspector: “Is a representative of the organization’s mechanical integrity department, who is responsible for quality assurance and control functions, such as: welding processes, contract execution, among others” (1).
Asset management: “It is the discipline that seeks to manage the entire life cycle of a company’s physical assets in order to maximize their value. It covers processes such as the design, construction, operation, maintenance, inspection and replacement of assets and infrastructure”.
Based on the aforementioned concepts, it is significant to establish the close relationship that exists between them; which will serve to develop the importance of the role of the equipment inspector as an essential variable of reliability in the handling/management of assets in the process of mechanical integrity.
Human reliability as an inspection discipline
The human reliability of the equipment inspector as a discipline must be measured by the effects of the deviations caused in safety, quality and effectiveness, on the production processes; this in order to identify their root causes and establish actions to eliminate them or mitigate their consequences.
In this context, in an operational reliability system it is necessary to analyze its four operational dimensions: human reliability, process reliability, equipment reliability and design reliability; on which action must be taken and a systematic development of activities must be carried out, in order to promote continuous and long-term improvement within the organization. Any isolated fact of improvement can bring benefits, but by not taking other factors into account, its advantages are limited or diluted in the organization and become only the result of a project and not of an organizational change. (2)
A professional equipment inspector (engineer or technician), with vast experience in asset inspections, qualified and certified in Non-Destructive Testing, management of international standards and codes such as: API, ASTM, ASME, NACE and others, technical support courses, diplomas, specializations, knowledge of oil and gas processes, corrosion mechanisms, metallurgy of materials, handling of work procedures under ISO 9001 and excellent writing of technical reports; They would make up the integral inspector desired for any contracting entity that is responsible for the operational reliability of its company.
Conclusion
The Equipment Inspector must be a professional with comprehensive training in technical knowledge and handling of inspection equipment; capable of providing fast, safe and quality solutions; that guarantee any client the reliability of their assets and make their operations a safe supplier of their products.
References
- The inspector according to API.
- Human reliability in maintenance management. Oliver Garcia (2006).