Artificial Intelligence (AI) unites with human intelligence, to fight against corrosion. The way forward is the use of new technologies, here is where it arises AI in corrosion management as, necessary for the implementation of computational techniques such as machine learning algorithms and state-of-the-art technologies, capable of providing a deeper and more precise vision to stop this phenomenon.
The resistance and useful life of industrial structures is affected by frequent exposure to aggressive environments that accelerate deterioration processes, where the main enemy is corrosion. This occurs predominantly in steel structures, which are essential for the daily operations of the different industrial sectors; and it is here, where this phenomenon is hidden in unpredictable areas and is one of the main causes of failures.
Having innovative tools and technologies, capable of predicting failures due to corrosion, is essential to safeguard assets, guarantee safety and optimize resources during operational processes. Control of all these factors leads to better corrosion management .
Corrosion: A persistent challenge in the industry
Corrosion is a constant threat, it is established as a persistent challenge that significantly affects the industrial sector. The use of metals in industry in general is very high and this type of material commonly corrodes due to its exposure conditions.
This phenomenon represents a great economic expense, since it affects steel structures and causes their physical properties to decrease, completely damaging the structure, its stability and, therefore, causing numerous risks. Understanding the magnitude of this problem is necessary to address it effectively and take appropriate preventive measures.
It should be noted that corrosion is a common and costly problem in many industrial sectors and affects it in more ways than we realize. This unwanted chemical reaction causes irreparable damage to structures, equipment and assets in general, which leads to considerable expenses in repairs and replacements. However, the risks associated with corrosion go beyond mere economic aspects. The safety of people and the environment are threatened by corrosive effects.
To know a little about the global impact of corrosion, it is estimated at 2.5 trillion US dollars, which is equivalent to 3.4% of the world Gross Domestic Product (GDP) (2013). By using available corrosion control practices, it is estimated that savings of between 15 and 35% of the cost of corrosion could be achieved; that is, between US$375 and $875 billion annually worldwide, an astronomical saving. Furthermore, these costs do not normally include individual safety or environmental consequences 1 .
These shocking figures are a call to action for science, researchers, companies and industries that must face this phenomenon. It is necessary to recognize the importance of implementing effective corrosion management and control strategies, as well as taking advantage of advanced technologies, such as artificial intelligence, to address this problem.
Advancing Corrosion Management: Artificial Intelligence as Alloy Technology
Artificial Intelligence covers a considerable space in different fields to solve complex problems for human beings, such as the detection and control of corrosion in the industrial sector. The digital technical field is increasing day by day in the world and is part of our life, although sometimes we do not realize it.
Early detection of corrosion is a key factor in the effective management of this persistent problem in the industry. Fortunately, AI has opened up a range of possibilities by offering advanced techniques/tools for efficient and accurate corrosion identification and monitoring.
Automatic detection of corrosion by images: With the use of special cameras and scanners, multiple images of the areas to be inspected are taken, these are processed by automated algorithms with corrosion detection patterns, which locate and classify corrosion in all facilities according to its criticality. By associating the captured images and the corresponding laser data, it is possible to calculate the physical area, dimensions and location of the detected corrosion.
By providing the measurements of the affected areas, a better estimate of the damage is allowed. From the automatic detection of corrosion and the state of the coating in the inspection images by AI-based systems, actions are prioritized and inspection work strategies are created to facilitate NDTs, maintenance or repair of the failures.
In this case, we mention Computer Vision 2 algorithms, which are used to detect corrosion, allowing high-risk equipment to be remediated. The algorithm was used for the industry’s first application of an artificial intelligence-based system to improve corrosion control and inspection processes. The system is deployed on a large offshore oil and gas platform in the Gulf of Mexico, demonstrating a vast improvement in inspection and maintenance processes while reducing operating costs and risks associated with O&G platforms. in high sea.
The results obtained from the inspection of the AI-based corrosion detection and management system were the following:
- 83 nominations for “urgent equipment replacement”, where the equipment has an estimated time to failure of 6 to 12 months
- 217 high-priority paint nominations, where if the equipment is not painted, the equipment will degrade to the point of requiring urgent equipment replacement within 12-24 months
- The implementation of this process also generated comparative results with the application of corrosion detection with traditional methods, generating the following results 2 . “A direct comparison is provided between the inspection coverage of the AI-based corrosion detection/management system and the inspection results of traditional inspections. Approximately 75% of all computers are covered by platform-level scans. Coverage is improved to approximately 97% by capturing scans in positions that consider corner cases, such as tight spaces, complex piping, and overhead equipment. In contrast, only 20% of teams were covered in the GVI 2019 campaign. The AI system provided approximately 77% more coverage. In addition, the full platform health assessment provided by the AI system was $0.5 million less than the proposed annual budget for traditional manned GVI. Direct recurring savings for each subsequent year would be approximately $1 million annually for the example platform.”
Artificial Intelligence Assisted Thermography to Detect CUI Corrosion Under Insulation: This type of corrosion is a critical challenge affecting the integrity of assets where the oil and gas industry is not immune. Its seriousness arises due to its hidden nature, since it can often go unnoticed. CUI is stimulated, in principle, by the ingress of moisture through the insulation layers to the pipe surface. This AI-powered detection technology arose from an urgent need to detect the presence of these types of corrosion.
A cyberphysicist has been developed that meets the demands of inspection units in the oil and gas industry, providing a real-time system and online assessment tool to monitor the presence of CUI by improving the outcome of inspection technologies. thermography. This system uses AI and machine learning technology 3 .
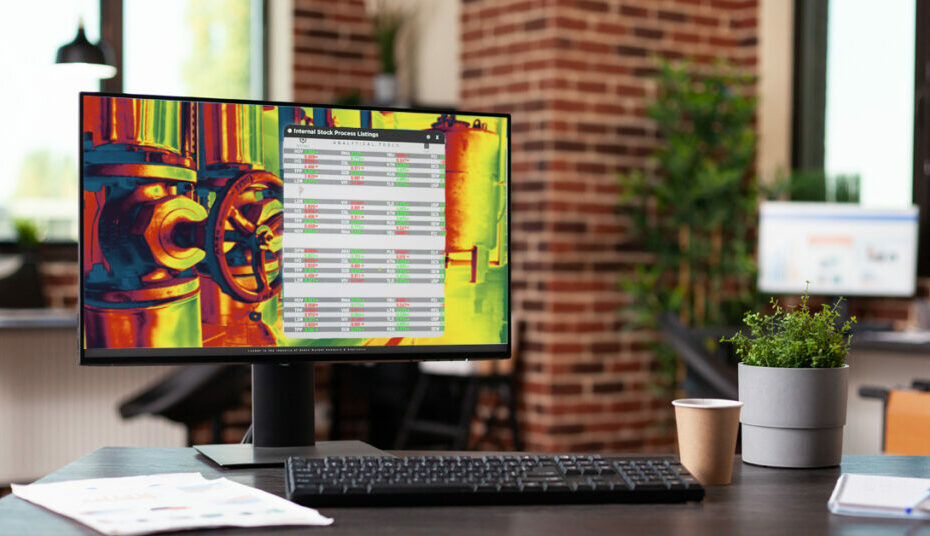
Digitization of corrosion management: Solutions have been created to identify corrosion through Machine Learning (ML) and monitor the asset in almost real time. The systems help identify corrosion through images using the Google Cloud ML service, as well as the Google Cloud tagging service for annotation.
Machine Learning is mainly used for corrosion detection, while a management tool is used to get an overview of the structure, allowing technicians to navigate the 3D environment by scanning exact coordinates, where they identify corrosion and automatically generate a report for planning corrosion management strategies.4.
Integrated monitoring sensors: These are AI-backed tools to manage the monitoring of structures affected by corrosion and thus identify high-risk areas. These devices perform decision-making based on AI, where the data on the evaluated structures is received and the Machine Learning algorithms will generate reports of high-risk areas to program maintenance strategies. They also create a continuous stream of data that must be collected, processed, and interpreted by specialized personnel to deliver useful results. The main interest is to be informed about the current state of the structure in terms of corrosive degradation, and whether to know when a failure may exist.
It should be noted that the constant developments in Big Data, machine learning algorithms , machine-to-machine communication, and cloud technology have opened up new possibilities to investigate information derived from industrial assets. Real-time monitoring of corrosion is feasible, thanks to sensors, actuators and other control parameters.
Benefits of Corrosion Management with Artificial Intelligence
The implementation of artificial intelligence tools in corrosion management entails a series of advantages that impact both the economic aspect and the safety of industrial operations. These benefits are necessary for companies to continue seeking to optimize their resources and safeguard their assets.
Several benefits are shown that are obtained with the use of techniques based on artificial intelligence compared to traditional approaches to corrosion management:
- A significant cost reduction is obtained in continuous inspection programs
- Provides greater coverage of the inspected area with less human intervention time
- It is possible to obtain more information and results in real time, requiring fewer personnel in the operational area, which reduces the risks associated with manual activities.
- Automatically generate preliminary reports
- Allows prioritizing and optimizing inspection strategies and predictive and preventive maintenance in the facilities evaluated
- By early identification of areas affected by corrosion, costly repairs and replacements of damaged structures or equipment are avoided.
- Guarantees a safer work environment for employees and prevents incidents
- The improvement in safety is notable, when corrosion is detected in difficult areas, failures of critical structures and components are prevented
- By preventing the spread of corrosion, the useful life of the assets is extended and the available resources are optimized.
- All the information is digitally saved for future evaluations, leaving comparative patterns
These factors drive the contribution of anti-corrosion technologies through the research, development and implementation of new effective solutions.
Conclusions
With the effective application of corrosion management programs based on artificial intelligence , applied to steel structures in the industrial sector, positive results are achieved. Detecting areas with corrosion early and accurately in order to prioritize non-destructive evaluations (NDT) and predictive or preventive maintenance in high-impact systems, allows effective planning, risk reduction and efficient operational continuity.
AI science is increasingly developing techniques to detect, classify, quantify and report the actual state of structures in reference to corrosion failures. By analyzing multiple variables and patterns, you gain deep insight into corrosion, significantly improving your ability to prevent and control it.
Corrosion management in synergy with AI is giving tangible highlights to combat the ravages of rust and preserve the integrity of assets in general, with greater preponderance in the most corrosive environments, such as marine ones.
From the economic point of view and optimization of available resources, the objective of each industry is to minimize operating costs and maximize profits; in this sense, the use of artificial intelligence and machine learning models is a desirable development to avoid future industrial risks and economic losses.
It is important that the operations carried out by systems dependent on artificial intelligence for the detection of corrosion ensure reliable, understandable and coherent results, supported by the objectives, experiences and human knowledge.
References
- http://impact.nace.org/executive-summary.aspx
- Eric L. Ferguson, Steve Potiris, Marco Castillo, Toby F. Dunne, and Suchet Bargoti; “Detection and Management of Atmospheric Corrosion with Artificial Intelligence; Energy, May 8, 2023.
- https://onepetro.org/SPEMEOS/proceedings-abstract/21MEOS/4-21MEOS/474505
- https://trifork.com/?portfolio=automatic-corrosion-detection