Corrosion and wear represent the main challenges to the integrity of industrial infrastructure; for this reason, the coating process is the most effective technical protection strategy for metal assets. This procedure is not just ‘painting’, but rather the controlled application of materials that create a robust barrier, ensuring the durability and performance of assets in different industrial sectors.
Proper surface preparation is essential to ensure coating adhesion and extend the life of the substrate. The key stages of the process, some of the latest technologies, and the main coatings used in industry are described below.
What is the coating process?
It is defined as a set of operations that allows a protective barrier to be applied uniformly to metal surfaces. Its main function is to prevent premature deterioration of the metal due to agents such as moisture, salinity, chemicals, or mechanical friction. Its guarantee depends on a sequence of four key stages, each of which serves a specific purpose to ensure high quality: substrate preparation, application, curing, and final quality control.
Stages of the coating process on metal surfaces
Metal surface preparation
This is the most critical stage of the process, as the adhesion of the coating depends directly on the cleanliness and roughness of the substrate. The selection of the preparation method is governed by international standards (such as those of the SSPC, NACE, and ISO 8501) and takes into account the type of metal and the coating to be used.
- Chemical or solvent cleaning: Uses degreasers and solvents, in accordance with SSPC-SP 1, to remove contaminants such as oils, greases, and dirt prior to mechanical preparation.
- Mechanical cleaning: Uses hand tools (SSPC-SP 2) or power tools (SSPC-SP 3) to remove rust and old coatings in hard-to-reach areas.
- Abrasive blasting (shot blasting): Projects abrasive particles at high speed (steel shot, sand, slag). This is the most effective method for thorough cleaning and creating an ideal anchor profile for adhesion. Among the most commonly used are SSPC-SP 10 (Near-Blast Clean) and SSPC-SP 5 (Blast Clean). Modern variants include wet blasting to reduce dust and automated shot blasting systems.
- Ultra-high pressure water cleaning (UHP Waterjetting): Uses water at over 30,000 psi to remove soluble contaminants and old coatings without generating dust. SSPC-SP WJ standards define degrees of cleanliness according to the pressure applied.
One company that has modernized some of these processes is RAM-100, which uses mobile units, automated shot blasting, and advanced systems for surface cleaning and industrial coating application under standards such as ISO 8501 or NACE.
Coating application
Once the surface has been prepared, the coating is applied using the most appropriate technique for the material and geometry of the part.
- Brush and roller: Used for touch-ups, small areas, or complex geometries where spraying is not feasible.
- Spray coating: This is the most common method in the industry, with several technologies available:
- High-volume airless: Uses a high-pressure pump to apply uniform coats to large surfaces quickly and efficiently; ideal for field work.
- Plural component equipment: Mixes resin and hardener just before application, the best option for epoxies or polyurea with a very short shelf life.
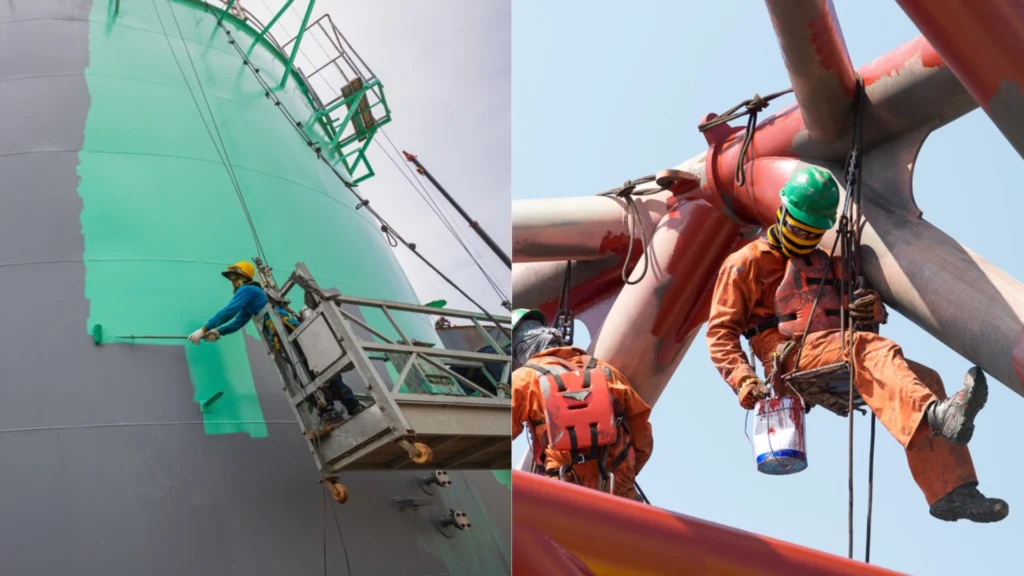
Curing or polymerization
Curing is the process by which the liquid coating transforms into a solid, resistant film. Methods vary depending on the application environment.
- Ambient or room temperature curing: The most common method for field-applied coatings, where the coating cures through solvent evaporation or a chemical reaction that occurs at room temperature. The curing speed can vary depending on temperature, humidity, and coating type.
- Thermal curing: Typically used in factory settings to polymerize powder or thermoset coatings. The part is placed in an oven to accelerate the process.
- UV or LED curing: Uses ultraviolet light or high-intensity LEDs to polymerize specialized coatings; useful in the manufacture of small parts or for quick repairs.
Final inspection
Inspection is the final step in ensuring that the coating meets technical specifications. Some of the inspection methods include:
- Dry film thickness (DFT) measurement: Magnetic induction gauges or advanced X-ray fluorescence (XRF) technology are used. ASTM D1186 and ISO 2808 are common references.
- Adhesion tests: These evaluate the strength of the bond between the coating and the substrate. The most common are cross-hatch cutting tests under standard (ASTM D3359) or pull-off tests under standard (ASTM D4541).
- Holiday test: Identifies porosity or pinholes and other discontinuities with high- and low-voltage equipment.
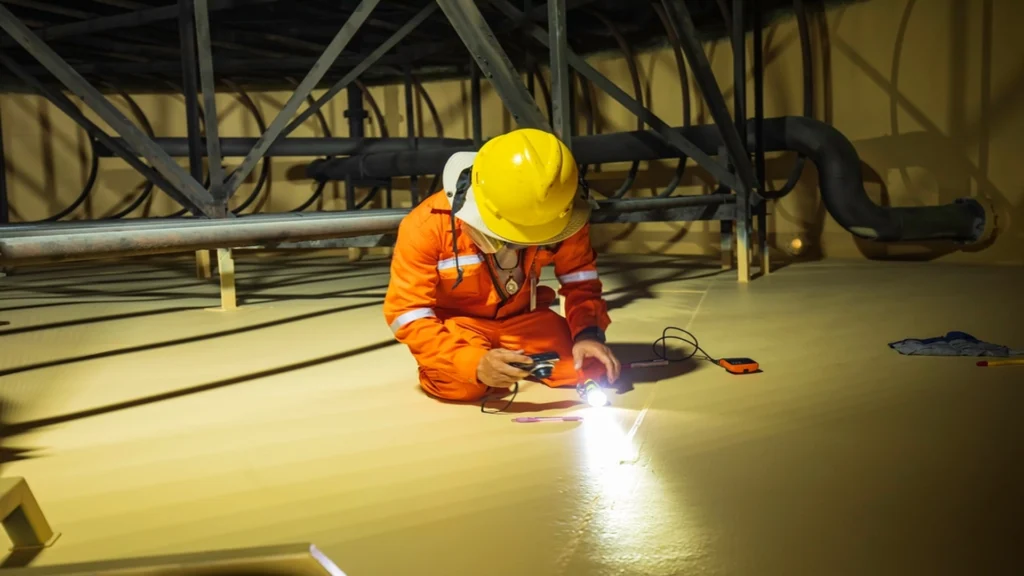
Post-coating maintenance
Maintenance is an important and proactive phase, following application and curing, designed to preserve the integrity of the coating system. Through periodic inspections and timely repairs, small defects such as cracks, blisters, or localized wear are identified and corrected before they progress and compromise the protection of the substrate.
Establishing a preventive maintenance plan based on the operating conditions of the asset and the nature of the coating is the most effective strategy for maximizing its efficiency and extending its useful life, significantly reducing long-term costs and avoiding catastrophic failures.
Types of industrial coatings and their technical applications
Coatings are classified according to their chemical composition, protective properties, and application conditions. The correct selection of the system depends on the operating environment, the substrate, and the performance requirements.
- Epoxy coatings: High chemical resistance, good adhesion, and durability; commonly used indoors, in tanks, chemical plants, and offshore platforms.
- Polyurethane coatings: Excellent UV resistance, gloss, and aesthetic finish; used as a top coat on structures exposed to sunlight and in architectural applications.
- Zinc-rich coatings: Provide cathodic protection to steel; recommended for exterior metal structures, bridges, transmission towers, and marine structures.
- Ceramic coatings: Have extremely high resistance to abrasion, chemicals, and temperatures. Used in the mining, paper, and steel industries.
- Powder coatings: Dry application by electrostatic spraying; these do not contain solvents, making them environmentally friendly: mostly used in the manufacture of auto parts and appliances.
- Chemical conversion coatings: Such as phosphating and anodizing, they improve the adhesion of subsequent layers or provide dielectric properties.
- Smart coatings: These coatings incorporate self-diagnostic, self-healing, or self-cleaning properties, revolutionizing protection. Currently under research for the aerospace and electronics sectors, they promise even more advanced metal integrity management.
Automation and robotics in industrial coatings
The integration of robotics is transforming the coating industry, optimizing surface preparation and coating application.
Cleaning and surface preparation robots
Automation at this stage ensures consistent results and improves workplace safety by eliminating staff exposure to risk.
- Remote abrasive blasting: These robots use magnets to adhere to vertical or horizontal surfaces, such as storage tanks or ship hulls. Equipped with abrasive blasting nozzles, they move in a programmed manner to ensure uniform cleaning and an optimal anchor profile.
- Robotic pressure washing: Similar to blasting systems, these robots clean surfaces with water jets at different pressures and are used in sensitive environments where particle containment is mandatory.
Industrial coating application robots
The application of coatings using robots is optimized for uniformity and material savings, overcoming the adversities of manual labor.
- Uniformity and repeatability: They follow programmed trajectories for each type of structure; these robots eliminate variations in film thickness that can occur with manual application, ensuring precise and durable finishes.
- High-efficiency spraying: These are systems that use technologies such as electrostatic spraying, where paint particles are electrically charged to improve transfer efficiency and reduce waste.
- Improved safety: They operate in paint booths with high concentrations of solvents and particles, protecting operators.
The following video from INSPENET shows a VertiDrive robotic system, distributed by BlastOne. By using a programmable robotic arm for shot blasting, this technology minimizes personnel exposure to hazardous environments and ensures uniform, high-quality surface treatment.

Common causes of coating process failures
Despite the technology available, industrial coatings can fail if certain variables are not properly controlled during their application and operation. Some common causes include:
- Poor surface preparation: An inadequate anchor profile, residual contaminants, or moisture can drastically affect adhesion.
- Incorrect dry film thickness (DFT): A DFT lower than specified reduces corrosion resistance; an excessive DFT can cause cracks, compromising long-term adhesion or leading to incomplete curing.
- Improper application: Temperature, relative humidity, and application speed influence proper film formation.
- Incomplete curing: Premature, incomplete, or artificially accelerated curing can prevent the polymer matrix from developing properly.
- Unforeseen severe environmental conditions: Environments with extreme salinity, intense UV exposure, or violent thermal cycles can accelerate deterioration.
- Poor chemical compatibility: Applying successive coats without checking compatibility between primers, intermediates, and finishes can lead to negative reactions.
Conclusions
The process of coating metal surfaces is a fundamental strategy for preserving the integrity of industrial assets, most of which operate in harsh environments and under strict technical specifications. It has been proven to be a science that combines meticulous preparation and precise application.
The adoption of advanced technologies, such as robotics in cleaning and application, has improved uniformity and efficiency, and has also raised safety standards. The integration of technology and precise control ensure that coatings remain the primary tool for protecting modern metal infrastructure.
FAQ (People Also Ask)
What is the coating process?
It is a series of steps to apply a protective coating to a surface, including preparation, application, curing, and inspection.
What is DFT in coatings?
It is the dry film thickness, a critical parameter to ensure adequate protection of the metal substrate.
What causes coating failure?
The most common failures include poor surface preparation, improper application, incomplete curing, and more aggressive environments than anticipated.
Which coatings resist UV exposure?
Aliphatic polyurethane and fluoropolymer coatings offer high resistance to ultraviolet radiation.
What is surface profiling in coating preparation?
It is the roughness generated on the substrate to improve coating adhesion, measured in microns.
In which industries are protective coatings applied?
Sectors such as oil u0026amp; gas, maritime, petrochemical, automotive, construction, and other industries, where specific coatings are selected according to resistance and durability requirements.